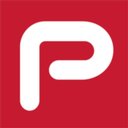
It is a method of production that involves a constant flow through the supply chains. It is an efficient, effective method to manufacture goods while avoiding overproduction.
Just in time production
Toyota Production System uses a production method called Just-in Time Production. It is a method of manufacturing that uses the Toyota Production System.
Businesses can also reduce their inventory costs and save on storage space. This can allow a company to create less product and have more cash to spend in other areas.
A good example of just in time production is the automobile industry. Many car manufacturers cannot afford to overproduce vehicles because they need to sell them within a year. They wait for customer orders and try to keep as little stock as possible.
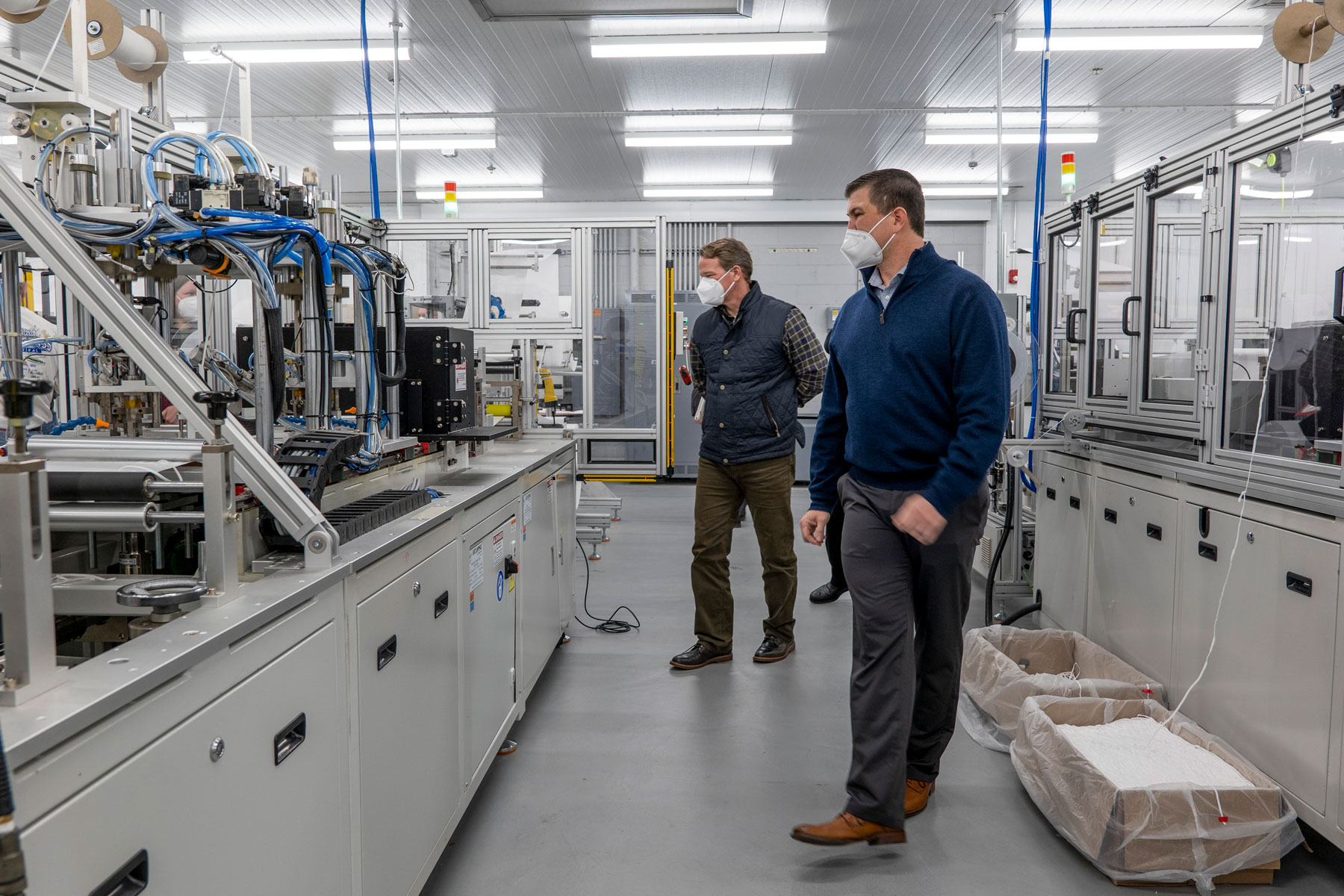
The PPS system allows them to see which parts are in stock and which have been ordered. Then, they can plan production accordingly.
It is possible to order raw materials and components from suppliers. This can help reduce costs of production, while ensuring high quality.
When a new vehicle needs to be built, they can create a purchase order that says when they want the parts to arrive at their facility. The supplier then delivers the parts to the company and they begin building the car.
The car can be completed and delivered in a timely way by the company. The company can provide a consistent and reliable product to its customers.
Just-in time production is often used by small companies who need to create products but do not have a large inventory or complex supply chains. They can build strong relationships to minimize stockouts, shortages or other risks.
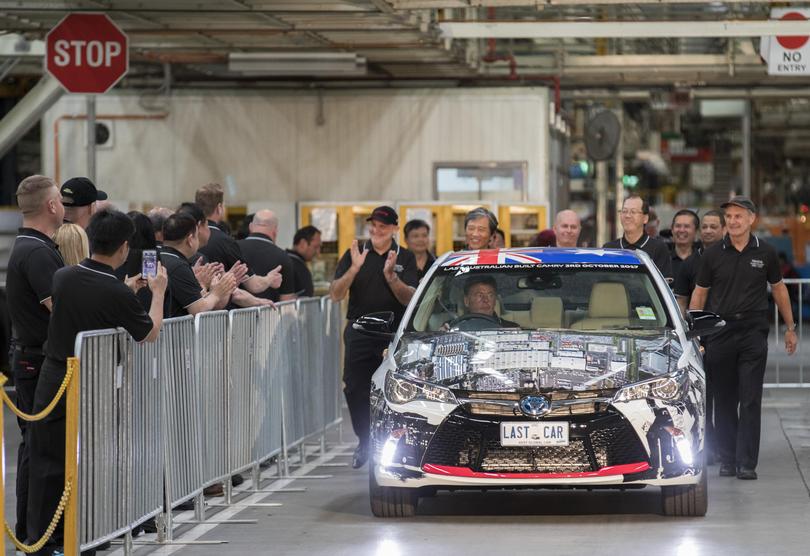
Just-in time is especially useful for manufacturers who are located close to a large city or have suppliers nearby that can deliver their parts easily and quickly. The method also helps to retain employees by allowing them to stay with the company for long periods of time.
Just-intime delivery is the method of supply management where a product is delivered to a particular location so that it can be shipped at the exact moment a customer wants it. This is a crucial delivery for businesses with an ecommerce presence as well as customers who require their products to be delivered as quickly as they can.
Just in time delivery is popular because it allows retailers and customers to choose from more convenient and quicker shipping options. Customers are able to select the most convenient and fast shipping method for their order.
Just-in time delivery can be a good way for businesses react to supply chains that fail due to unforeseeable delays or accidents. This can allow businesses to stay in business and remain competitive.
FAQ
What does manufacturing industry mean?
Manufacturing Industries are those businesses that make products for sale. The people who buy these products are called consumers. This is accomplished by using a variety of processes, including production, distribution and retailing. They manufacture goods from raw materials using machines and other equipment. This covers all types of manufactured goods including clothing, food, building supplies and furniture, as well as electronics, tools, machinery, vehicles and pharmaceuticals.
What is production management?
Production Planning refers to the development of a plan for every aspect of production. This document will ensure everything is in order and ready to go when you need it. This document should also include information on how to get the best result on set. It should include information about shooting locations, casting lists, crew details, equipment requirements, and shooting schedules.
The first step is to outline what you want to film. You may already know where you want the film to be shot, or perhaps you have specific locations and sets you wish to use. Once you've identified the locations and scenes you want to use, you can begin to plan what elements you need for each scene. You might decide you need a car, but not sure what make or model. To narrow your options, you can search online for available models.
Once you have found the right vehicle, you can think about adding accessories. Do you need people sitting in the front seats? Maybe you need someone to move around in the back. You may want to change the interior's color from black or white. These questions will help determine the look and feel you want for your car. You can also think about the type of shots you want to get. Do you want to film close-ups, or wider angles? Perhaps you want to show the engine or the steering wheel? These factors will help you determine which car style you want to film.
Once you have all the information, you are ready to create a plan. You can create a schedule that will outline when you must start and finish your shoots. Every day will have a time for you to arrive at the location, leave when you are leaving and return home when you are done. This way, everyone knows what they need to do and when. It is possible to make arrangements in advance for additional staff if you are looking to hire. You should not hire anyone who doesn't show up because of your inaction.
It is important to calculate the amount of filming days when you are creating your schedule. Some projects may only take a couple of days, while others could last for weeks. It is important to consider whether you require more than one photo per day when you create your schedule. Multiplying takes in the same area will result both in increased costs and a longer time. If you aren't sure whether you need multiple shots, it is best to take fewer photos than you would like.
Budgeting is another important aspect of production planning. You will be able to manage your resources if you have a realistic budget. You can always lower the budget if you encounter unexpected problems. But, don't underestimate how much money you'll spend. If you underestimate the cost of something, you will have less money left after paying for other items.
Production planning is a complicated process. But once you understand how everything works together, it becomes much easier to plan future project.
What is the importance of automation in manufacturing?
Not only is automation important for manufacturers, but it's also vital for service providers. Automation allows them to deliver services quicker and more efficiently. In addition, it helps them reduce costs by reducing human errors and improving productivity.
What does it take for a logistics enterprise to succeed?
To run a successful logistics company, you need a lot knowledge and skills. Good communication skills are essential to effectively communicate with your suppliers and clients. You should be able analyse data and draw inferences. You need to be able work under pressure and manage stressful situations. In order to innovate and create new ways to improve efficiency, creativity is essential. You need to have strong leadership qualities to motivate team members and direct them towards achieving organizational goals.
It is also important to be efficient and well organized in order meet deadlines.
Statistics
- Job #1 is delivering the ordered product according to specifications: color, size, brand, and quantity. (netsuite.com)
- According to a Statista study, U.S. businesses spent $1.63 trillion on logistics in 2019, moving goods from origin to end user through various supply chain network segments. (netsuite.com)
- According to the United Nations Industrial Development Organization (UNIDO), China is the top manufacturer worldwide by 2019 output, producing 28.7% of the total global manufacturing output, followed by the United States, Japan, Germany, and India.[52][53] (en.wikipedia.org)
- You can multiply the result by 100 to get the total percent of monthly overhead. (investopedia.com)
- Many factories witnessed a 30% increase in output due to the shift to electric motors. (en.wikipedia.org)
External Links
How To
Six Sigma in Manufacturing:
Six Sigma is defined as "the application of statistical process control (SPC) techniques to achieve continuous improvement." Motorola's Quality Improvement Department developed it at their Tokyo plant in Japan in 1986. Six Sigma is a method to improve quality through standardization and elimination of defects. Since there are no perfect products, or services, this approach has been adopted by many companies over the years. The main goal of Six Sigma is to reduce variation from the mean value of production. It is possible to measure the performance of your product against an average and find the percentage of time that it differs from the norm. If it is too large, it means that there are problems.
Understanding the nature of variability in your business is the first step to Six Sigma. Once you understand this, you can then identify the causes of variation. This will allow you to decide if these variations are random and systematic. Random variations happen when people make errors; systematic variations are caused externally. You could consider random variations if some widgets fall off the assembly lines. However, if you notice that every time you assemble a widget, it always falls apart at exactly the same place, then that would be a systematic problem.
Once you identify the problem areas, it is time to create solutions. It might mean changing the way you do business or redesigning it entirely. Once you have implemented the changes, it is important to test them again to ensure they work. If they don't work you need to rework them and come up a better plan.