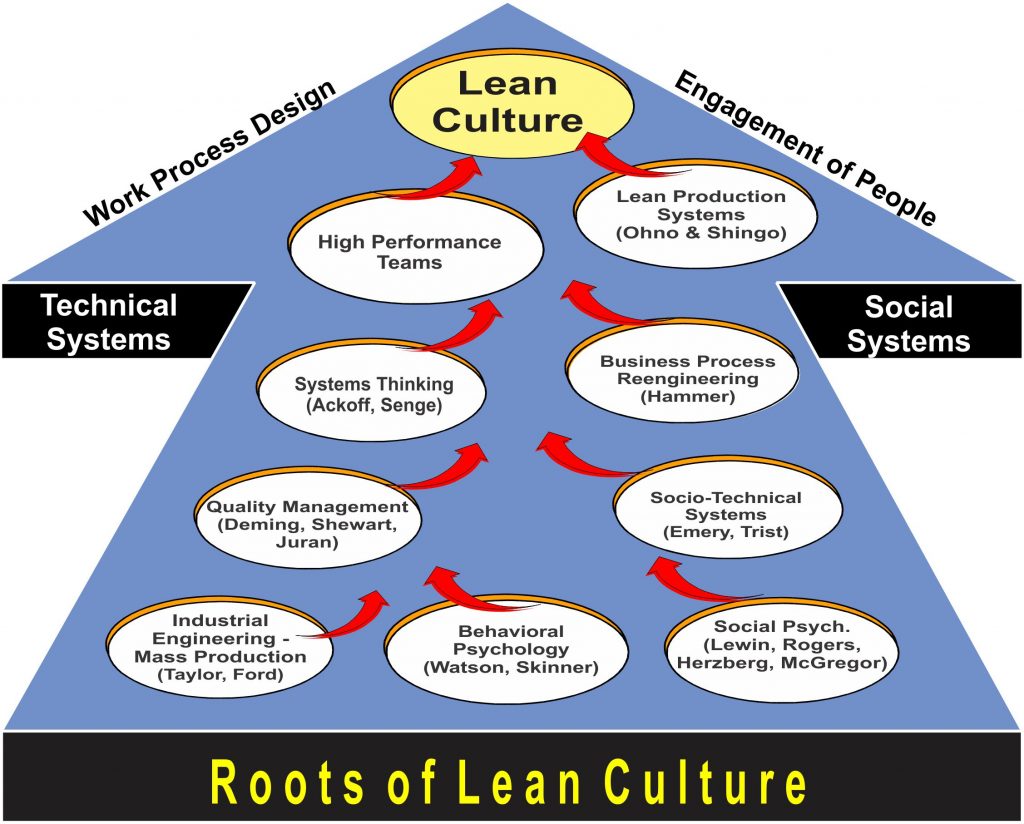
Supply Dynamics, a multi-enterprise supply channel analytics suite, was established in Loveland Ohio in 2003. It offers technology solutions for manufacturers working in distributed manufacturing environments. Supply Dynamics is a partner of the Defense Logistics Agency and the Navy. It allows organizations to monitor and control their entire supply chain. It helps manufacturers plan production and reduce the costs of raw materials. Supply Dynamics has worked with many industries, including aerospace, defense and manufacturing.
Dynamics 365 Supply Chain Management is a Microsoft Cloud solution that enables companies to improve operational efficiency as well as streamline production. It also helps them build strong supply chains. It provides flexibility, predictive analytics, and unparalleled visibility into all aspects of the supply chain. Its modules ensure that products reach their customers on-time and provide functionality for the entire product lifecycle.
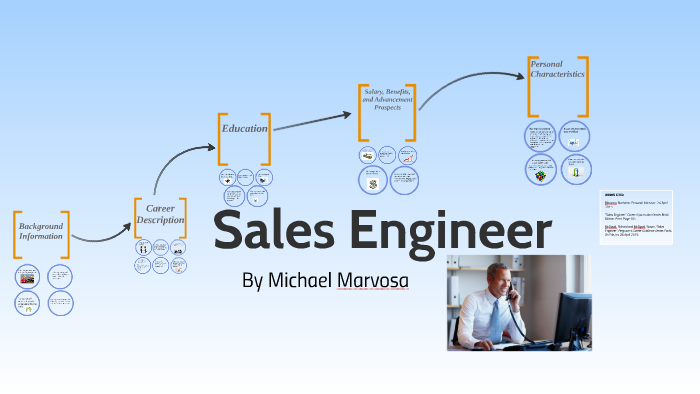
The Dynamics Supply Chain module includes features that allow users to configure items for process or discrete manufacturing, submit RFQs, test product quality, and submit purchase orders. You can also create Gantt charts that provide transparency for all operations. Visual Supply Schedule lets users see the forecast of inventory levels and anticipated demand. When supply chain problems arise, they can adjust the schedules. It provides managers with the ability track the progress and status of job functions on different production floors.
Microsoft Dynamics 365 Supply Chain Management provides organizations with a unified and predictive way to manage customer demand and ensure that the right materials are in the right place at the right time. It allows businesses to anticipate customer demands and changes in capacities. It integrates logistics and purchasing with production and can be used across multiple sites or warehouses. It also supports vendor-specific pricing, multiple inventory costing methods, and transportation management. The solution also supports the use of inventory optimization and predictive analytics, as well as AI features.
Dynamics 365 provides self-service to suppliers. Suppliers can accept or reject purchase orders and raise PO invoices. They can also enter shipment information for existing POs. It supports several inventory costing methods including item-level, vendor-specific pricing and item-group pricing. It also includes several inventory optimization features, including the ability to create an inventory allocation plan for an order.
Supply Dynamics also offers unique metals price benchmarking solutions. This technology allows manufacturers faster response to fluctuations in market conditions. They can also anticipate fluctuations in manufacturing costs and forecast them. This technology can reduce manufacturing costs and reduce waste. It provides manufacturers with a blueprint that can be used to convert bill of material data.
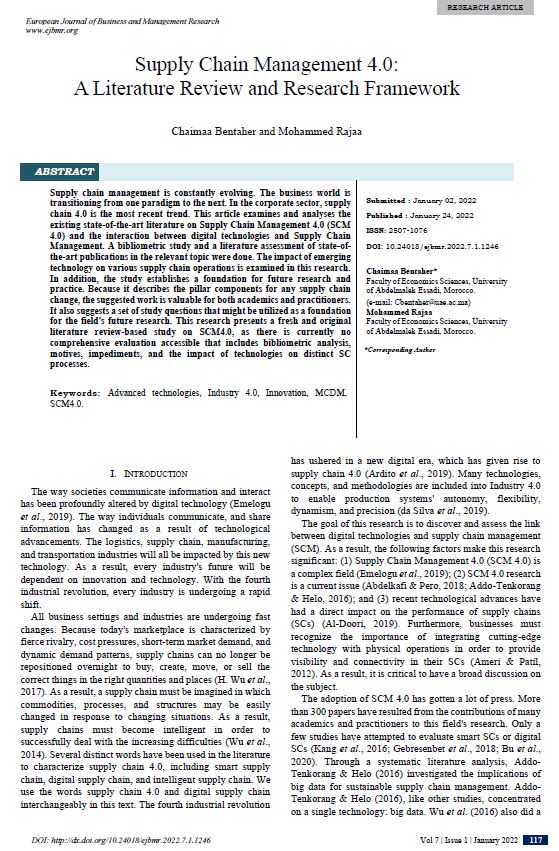
Its master-planning feature automates creating Production Orders from open Purchase Orders. The optimization add-in allows users to predict changes in customer demand. The AI capabilities of the program can help improve the flow in goods distribution. The Dynamics Supply Chain Management platform is certified by Microsoft, making it a great solution for companies seeking to build a strong supply chain.
FAQ
How can excess manufacturing production be reduced?
The key to reducing overproduction lies in developing better ways to manage inventory. This would reduce the time spent on unproductive activities like purchasing, storing and maintaining excess stock. This would allow us to use our resources for more productive tasks.
You can do this by adopting a Kanban method. A Kanbanboard is a visual tool that allows you to keep track of the work being done. A Kanban system allows work items to move through several states before reaching their final destination. Each state represents an individual priority level.
To illustrate, work can move from one stage or another when it is complete enough for it to be moved to a new stage. A task that is still in the initial stages of a process will be considered complete until it moves on to the next stage.
This allows for work to continue moving forward, while also ensuring that there is no work left behind. Managers can view the Kanban board to see how much work they have done. This data allows them adjust their workflow based upon real-time data.
Lean manufacturing, another method to control inventory levels, is also an option. Lean manufacturing emphasizes eliminating waste in all phases of production. Any product that isn't adding value can be considered waste. These are some of the most common types.
-
Overproduction
-
Inventory
-
Packaging not required
-
Material surplus
Manufacturers can increase efficiency and decrease costs by implementing these ideas.
What type of jobs is there in logistics
Logistics can offer many different jobs. These are some of the jobs available in logistics:
-
Warehouse workers - They load and unload trucks and pallets.
-
Transportation drivers – These drivers drive trucks and wagons to transport goods and pick up the goods.
-
Freight handlers are people who sort and pack freight into warehouses.
-
Inventory managers - These are responsible for overseeing the stock of goods in warehouses.
-
Sales representatives - They sell products to customers.
-
Logistics coordinators are responsible for organizing and planning logistics operations.
-
Purchasing agents - They purchase goods and services needed for company operations.
-
Customer service representatives - Answer calls and email from customers.
-
Shipping clerks - They process shipping orders and issue bills.
-
Order fillers - They fill orders based on what is ordered and shipped.
-
Quality control inspectors are responsible for inspecting incoming and outgoing products looking for defects.
-
Other - Logistics has many other job opportunities, including transportation supervisors, logistics specialists, and cargo specialists.
What are manufacturing and logistic?
Manufacturing is the process of creating goods from raw materials by using machines and processes. Logistics manages all aspects of the supply chain, including procurement, production planning and distribution, inventory control, transportation, customer service, and transport. Manufacturing and logistics can often be grouped together to describe a larger term that covers both the creation of products, and the delivery of them to customers.
What is the role of a logistics manager
Logistics managers ensure that goods arrive on time and are unharmed. This is done through his/her expertise and knowledge about the company's product range. He/she must also ensure sufficient stock to meet the demand.
What does the term manufacturing industries mean?
Manufacturing Industries refers to businesses that manufacture products. Consumers are people who purchase these goods. These companies use various processes such as production, distribution, retailing, management, etc., to fulfill this purpose. These companies produce goods using raw materials and other equipment. This includes all types if manufactured goods.
Statistics
- According to a Statista study, U.S. businesses spent $1.63 trillion on logistics in 2019, moving goods from origin to end user through various supply chain network segments. (netsuite.com)
- [54][55] These are the top 50 countries by the total value of manufacturing output in US dollars for its noted year according to World Bank.[56] (en.wikipedia.org)
- It's estimated that 10.8% of the U.S. GDP in 2020 was contributed to manufacturing. (investopedia.com)
- (2:04) MTO is a production technique wherein products are customized according to customer specifications, and production only starts after an order is received. (oracle.com)
- You can multiply the result by 100 to get the total percent of monthly overhead. (investopedia.com)
External Links
How To
How to Use Six Sigma in Manufacturing
Six Sigma is defined as "the application of statistical process control (SPC) techniques to achieve continuous improvement." Motorola's Quality Improvement Department, Tokyo, Japan, developed it in 1986. Six Sigma's main goal is to improve process quality by standardizing processes and eliminating defects. Since there are no perfect products, or services, this approach has been adopted by many companies over the years. Six Sigma aims to reduce variation in the production's mean value. It is possible to measure the performance of your product against an average and find the percentage of time that it differs from the norm. If you notice a large deviation, then it is time to fix it.
The first step toward implementing Six Sigma is understanding how variability works in your business. Once you have this understanding, you will need to identify sources and causes of variation. These variations can also be classified as random or systematic. Random variations happen when people make errors; systematic variations are caused externally. If you make widgets and some of them end up on the assembly line, then those are considered random variations. You might notice that your widgets always fall apart at the same place every time you put them together.
After identifying the problem areas, you will need to devise solutions. That solution might involve changing the way you do things or redesigning the process altogether. Test them again once you've implemented the changes. If they don't work you need to rework them and come up a better plan.