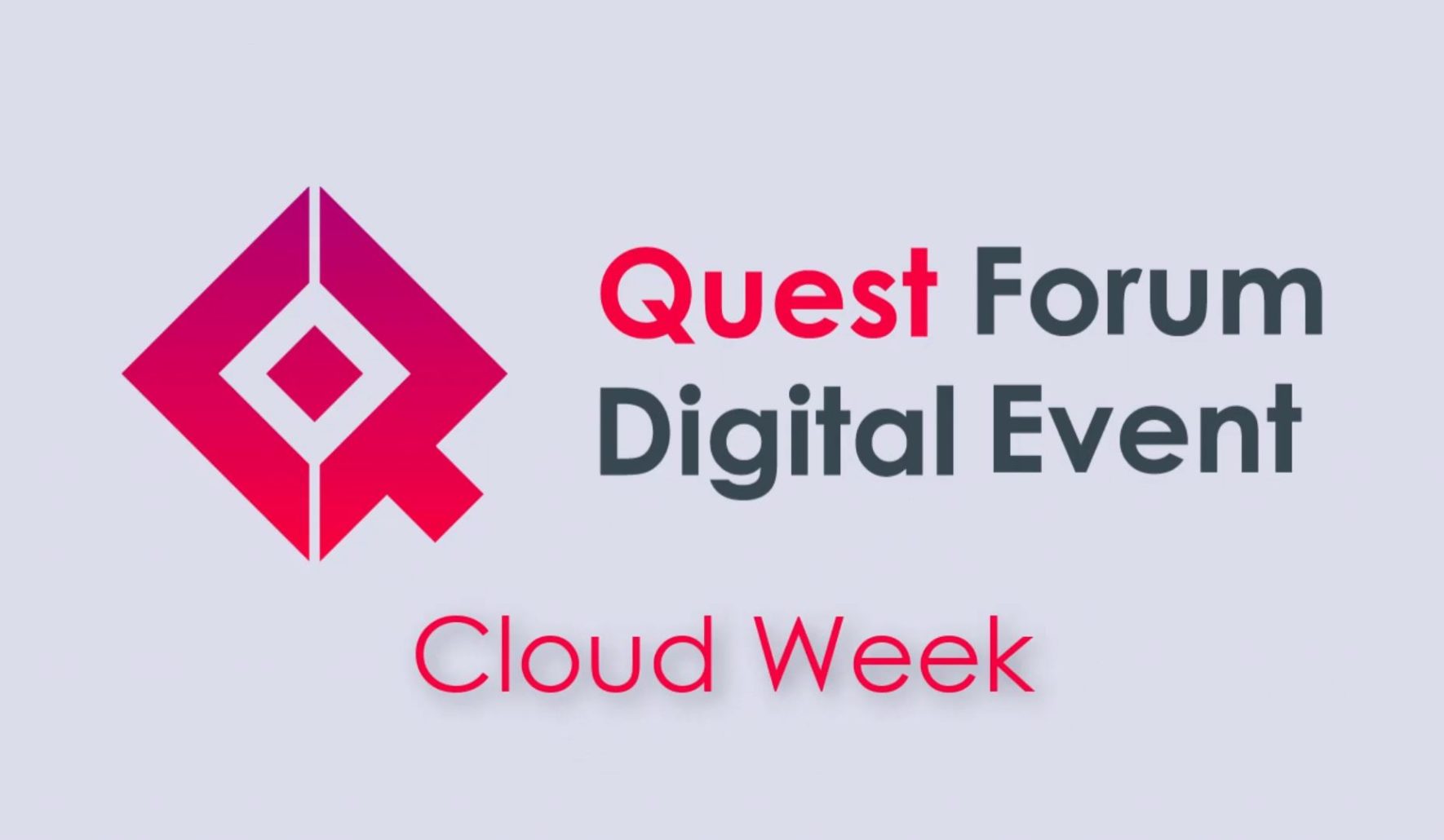
Facilities engineers (also known as maintenance engineers) are professionals who provide support in engineering and construction for buildings and operations. Their duties include implementing and planning procedures, recommending upgrades and repairs, and managing routine and emergency maintenance. They can be involved in a variety of engineering disciplines including plumbing, electrical, and mechanical. Aside from their technical expertise, they have a good understanding of construction law, safety standards and other regulatory requirements.
Facilities engineers often start in the entry level of their career and can quickly rise to more senior positions. Building a portfolio of projects, research, articles and other relevant work is the best way to be noticed in your field. Facilities engineers must continue to study their specialty. This will make them stand out when they apply for a new job.
Even though certification is not necessary for all facilities engineers it can make a difference when you apply for a new job. An engineer must have a good understanding of engineering principles and concepts. They should also be able to make compelling presentations and analyze data. Facility engineers should be familiar with asset reliability-centered maintenance strategies and predictive maintenance.
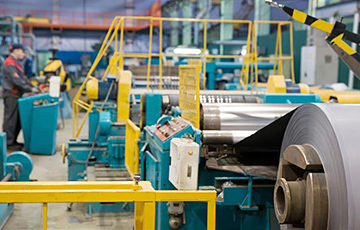
Facilities engineers can work in office, construction, manufacturing, or other settings. They oversee and implement processes to ensure the safe, efficient, and effective operation of facility utility systems. Facilities engineers work closely with managers and other engineers. This helps to make work more efficient and resolves any problems.
The specific type of facility an engineer is working in will determine the responsibilities. The job requires excellent time management, problem-solving skills, and the ability of working well with others. A facilities engineer might perform hundreds of tasks in a day. The facilities engineer can be responsible for plumbing, electrical, and mechanical equipment. He or she must also be able to diagnose and correct malfunctions.
There are many websites that provide news and information about the profession, including those of AFE (Association of Facility Engineers). These websites offer a sample resume and salary information as well as articles related to job search.
These websites are not the only way for facilities engineers to learn. They can also read articles and attend training courses. In order to be a successful facilities engineer, you should have good organizational skills, a good understanding of various engineering and construction disciplines, and a solid understanding of building and safety codes.
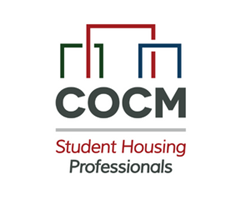
It is important to know that many of the most talented facilities engineers can perform multiple tasks at once and analyze data. For this to happen, they will need to have a working knowledge about AutoCAD as well construction techniques such the CAM. The skills of project management, critical thought, and problem-solving are also beneficial.
One of the biggest advantages of a facilities engineer job is the chance to work with a large array of people. These engineers can work with many different materials and coordinate other engineers' work.
FAQ
What is the difference between Production Planning and Scheduling?
Production Planning (PP), also known as forecasting and identifying production capacities, is the process that determines what product needs to be produced at any particular time. Forecasting demand is one way to do this.
Scheduling is the process that assigns dates to tasks so they can get completed within a given timeframe.
What are the 7 Rs of logistics?
The acronym "7R's" of Logistics stands for seven principles that underpin logistics management. It was published in 2004 by the International Association of Business Logisticians as part of their "Seven Principles of Logistics Management" series.
The following letters make up the acronym:
-
Responsible - to ensure that all actions are within the legal requirements and are not detrimental to others.
-
Reliable - have confidence in the ability to deliver on commitments made.
-
Be responsible - Use resources efficiently and avoid wasting them.
-
Realistic - Consider all aspects of operations, including environmental impact and cost effectiveness.
-
Respectful: Treat others with fairness and equity
-
Reliable - Find ways to save money and increase your productivity.
-
Recognizable is a company that provides customers with value-added solutions.
How can manufacturing efficiency improved?
First, we need to identify which factors are most critical in affecting production times. We then need to figure out how to improve these variables. If you don’t know how to start, look at which factors have the greatest impact upon production time. Once you've identified them, try to find solutions for each of those factors.
What is the responsibility for a logistics manager
A logistics manager makes sure that all goods are delivered on-time and in good condition. This is accomplished by using the experience and knowledge gained from working with company products. He/she must also ensure sufficient stock to meet the demand.
Statistics
- According to the United Nations Industrial Development Organization (UNIDO), China is the top manufacturer worldwide by 2019 output, producing 28.7% of the total global manufacturing output, followed by the United States, Japan, Germany, and India.[52][53] (en.wikipedia.org)
- According to a Statista study, U.S. businesses spent $1.63 trillion on logistics in 2019, moving goods from origin to end user through various supply chain network segments. (netsuite.com)
- You can multiply the result by 100 to get the total percent of monthly overhead. (investopedia.com)
- [54][55] These are the top 50 countries by the total value of manufacturing output in US dollars for its noted year according to World Bank.[56] (en.wikipedia.org)
- Many factories witnessed a 30% increase in output due to the shift to electric motors. (en.wikipedia.org)
External Links
How To
How to use lean manufacturing in the production of goods
Lean manufacturing refers to a method of managing that seeks to improve efficiency and decrease waste. It was developed in Japan between 1970 and 1980 by Taiichi Ohno. TPS founder Kanji Tyoda gave him the Toyota Production System, or TPS award. Michael L. Watkins published the original book on lean manufacturing, "The Machine That Changed the World," in 1990.
Lean manufacturing, often described as a set and practice of principles, is aimed at improving the quality, speed, cost, and efficiency of products, services, and other activities. It emphasizes the elimination and minimization of waste in the value stream. Lean manufacturing can be described as just-in–time (JIT), total productive maintenance, zero defect (TPM), or even 5S. Lean manufacturing focuses on eliminating non-value-added activities such as rework, inspection, and waiting.
Lean manufacturing is a way for companies to achieve their goals faster, improve product quality, and lower costs. Lean Manufacturing is one of the most efficient ways to manage the entire value chains, including suppliers and customers as well distributors and retailers. Lean manufacturing can be found in many industries. Toyota's philosophy has been a key driver of success in many industries, including automobiles and electronics.
Lean manufacturing includes five basic principles:
-
Define value - Find out what your business contributes to society, and what makes it different from other competitors.
-
Reduce waste - Stop any activity that isn't adding value to the supply chains.
-
Create Flow. Ensure that your work is uninterrupted and flows seamlessly.
-
Standardize and Simplify – Make processes as consistent, repeatable, and as simple as possible.
-
Develop Relationships: Establish personal relationships both with internal and external stakeholders.
Lean manufacturing is not a new concept, but it has been gaining popularity over the last few years due to a renewed interest in the economy following the global financial crisis of 2008. To increase their competitiveness, many businesses have turned to lean manufacturing. Some economists even believe that lean manufacturing can be a key factor in economic recovery.
With many benefits, lean manufacturing is becoming more common in the automotive industry. These benefits include increased customer satisfaction, reduced inventory levels and lower operating costs.
The principles of lean manufacturing can be applied in almost any area of an organization. Because it makes sure that all value chains are efficient and effectively managed, Lean Manufacturing is particularly helpful for organizations.
There are three main types in lean manufacturing
-
Just-in Time Manufacturing: This lean manufacturing method is commonly called "pull systems." JIT is a process in which components can be assembled at the point they are needed, instead of being made ahead of time. This approach reduces lead time, increases availability and reduces inventory.
-
Zero Defects Manufacturing: ZDM ensures that no defective units leave the manufacturing plant. Repairing a part that is damaged during assembly should be done, not scrapping. This also applies to finished products that need minor repairs before being shipped.
-
Continuous Improvement (CI): CI aims to improve the efficiency of operations by continuously identifying problems and making changes in order to eliminate or minimize waste. Continuous Improvement involves continuous improvement of processes.