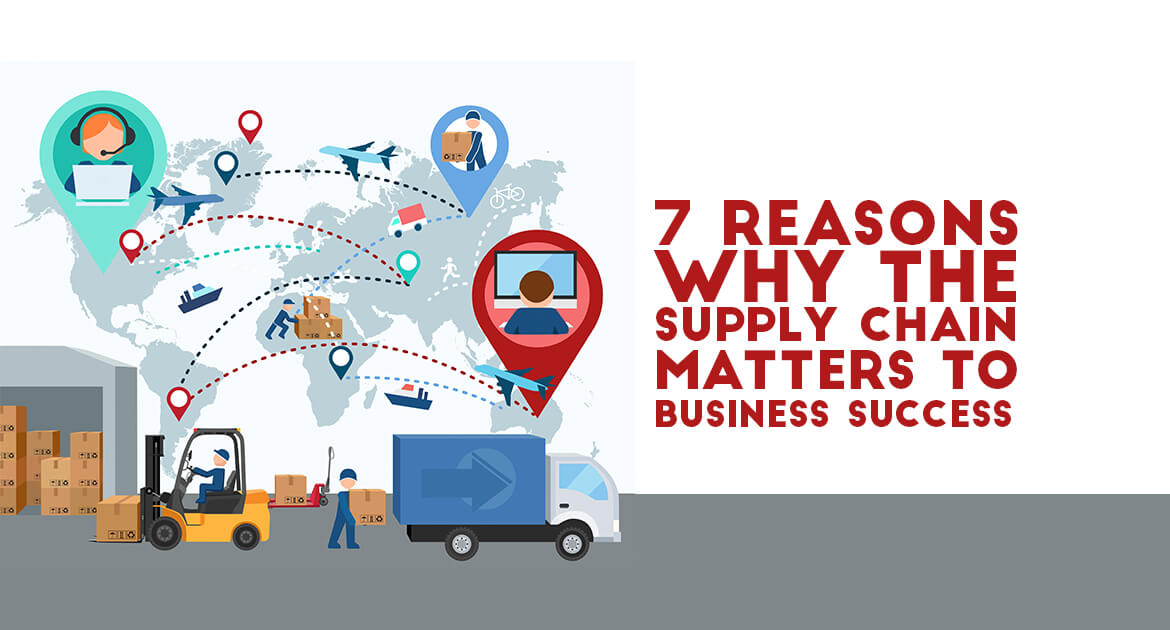
OEE stands for Overall Equipment Effectiveness. It is a measurement that measures the equipment's efficiency. This article explains the definition and calculates OEE. It is a best-practice metric that measures availability, performance, and quality. OEE helps improve manufacturing efficiency by decreasing downtime, increasing production, and reducing costs. It helps manufacturers save money.
OEE is a labor efficiency measure.
OEE measures the overall quality of production. It is based on an interaction of availability, quality, and performance. The losses in OEE are time lost due to inconsistent production. These include the time down, rate fluctuations in process, scrap, and any rework that is generated during operative modes.
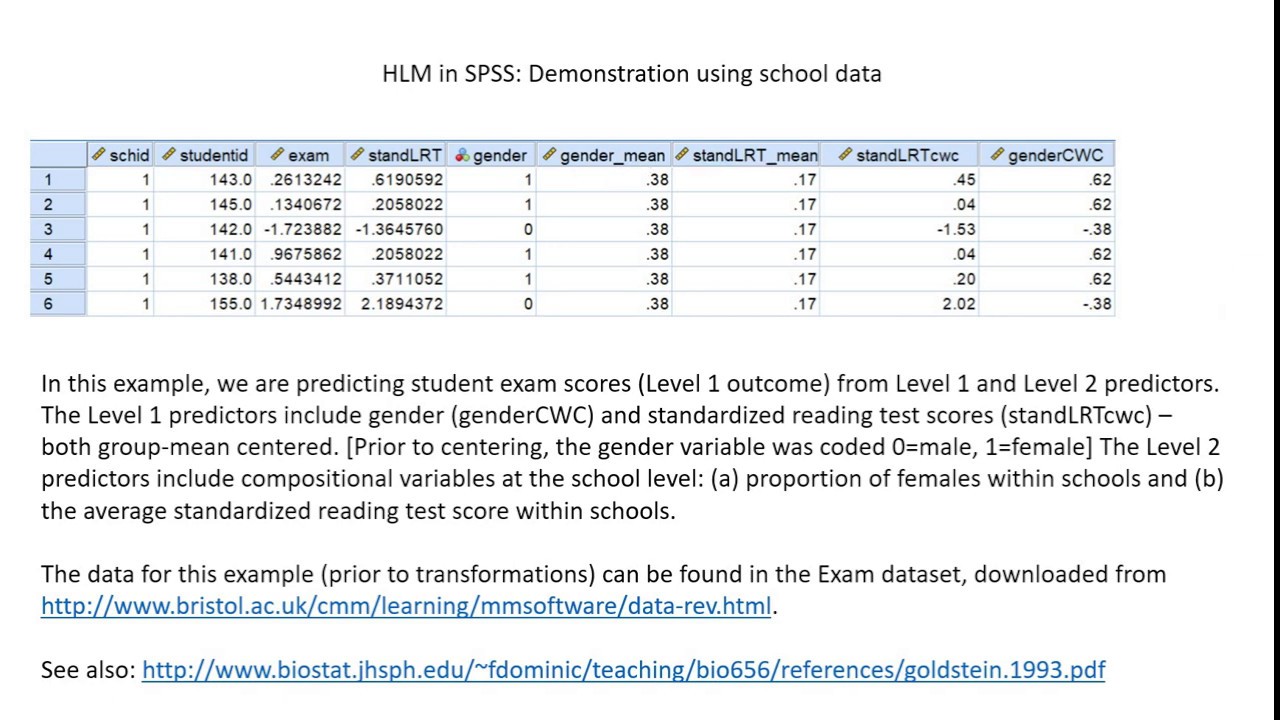
It's based on Availability and Performance as well as Quality
OEE is a production management method that stresses the importance of availability and performance. Availability refers to the time that a product, service or other item is available for purchase or use. It may also be defined as the period between the delivery of a product or service to a customer and its recovery, or the interval between scrapping and repair. The quality of a company's performance directly correlates to its success. The best way to gauge performance is to have a professional company assess your business and give you suggestions for improvement.
It is an indicator of best practices.
OEE is a powerful tool for improving and measuring your operation. This metric provides different levels of analysis that can help you improve your operations and reduce waste. However, this metric should not be considered the final metric. This means that you should not start an OEE improvement program without carefully piloting it first.
It is a directional metric
OEE is not only a directional measurement that can be used to measure the performance of similar machines in a company. Companies can determine if their machines are becoming more efficient by consistently measuring this metric across all machines.
It is called a TPM metric.
It is useful for measuring production efficiency. It measures the loss and inefficiencies in three main areas: availability (performance), quality (quality). It can also be used to track progress and identify areas where improvement is needed.
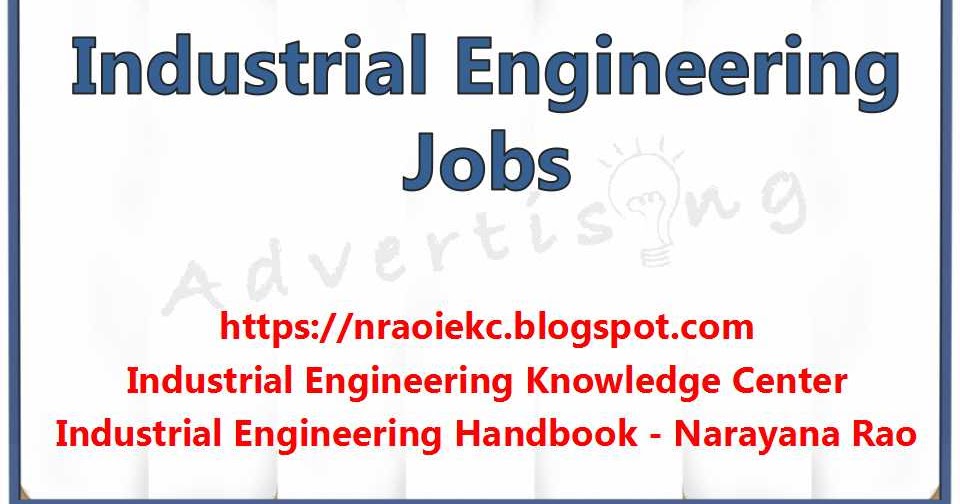
It is a best practice in manufacturing
OEE is an acronym for overall equipment effectiveness. It's the ratio between how much a machine, cell or device can produce in a specific time and how long that product takes to actually be produced. It is important to minimize downtime and maximize OEE. Manufacturing operations can increase quality and reduce costs.
FAQ
What does warehouse mean?
A warehouse is an area where goods are stored before being sold. It can be either an indoor or outdoor space. It could be one or both.
What is the difference in Production Planning and Scheduling, you ask?
Production Planning (PP), is the process of deciding what production needs to take place at any given time. This is done through forecasting demand and identifying production capacities.
Scheduling involves the assignment of dates and times to tasks in order to complete them within the timeframe.
What are manufacturing & logistics?
Manufacturing refers to the process of making goods using raw materials and machines. Logistics manages all aspects of the supply chain, including procurement, production planning and distribution, inventory control, transportation, customer service, and transport. Manufacturing and logistics can often be grouped together to describe a larger term that covers both the creation of products, and the delivery of them to customers.
Statistics
- Many factories witnessed a 30% increase in output due to the shift to electric motors. (en.wikipedia.org)
- You can multiply the result by 100 to get the total percent of monthly overhead. (investopedia.com)
- According to a Statista study, U.S. businesses spent $1.63 trillion on logistics in 2019, moving goods from origin to end user through various supply chain network segments. (netsuite.com)
- In the United States, for example, manufacturing makes up 15% of the economic output. (twi-global.com)
- (2:04) MTO is a production technique wherein products are customized according to customer specifications, and production only starts after an order is received. (oracle.com)
External Links
How To
How to use 5S in Manufacturing to Increase Productivity
5S stands to stand for "Sort", “Set In Order", “Standardize", and "Store". Toyota Motor Corporation developed the 5S method in 1954. It assists companies in improving their work environments and achieving higher efficiency.
This method has the basic goal of standardizing production processes to make them repeatable. Cleaning, sorting and packing are all done daily. These actions allow workers to perform their job more efficiently, knowing what to expect.
There are five steps that you need to follow in order to implement 5S. Each step involves a different action which leads to increased efficiency. If you sort items, it makes them easier to find later. You arrange items by placing them in an order. After you have divided your inventory into groups you can store them in easy-to-reach containers. Make sure everything is correctly labeled when you label your containers.
This requires employees to critically evaluate how they work. Employees must be able to see why they do what they do and find a way to achieve them without having to rely on their old methods. They must learn new skills and techniques in order to implement the 5S system.
The 5S method not only increases efficiency but also boosts morale and teamwork. As they begin to see improvements, they feel motivated to continue working towards the goal of achieving higher levels of efficiency.