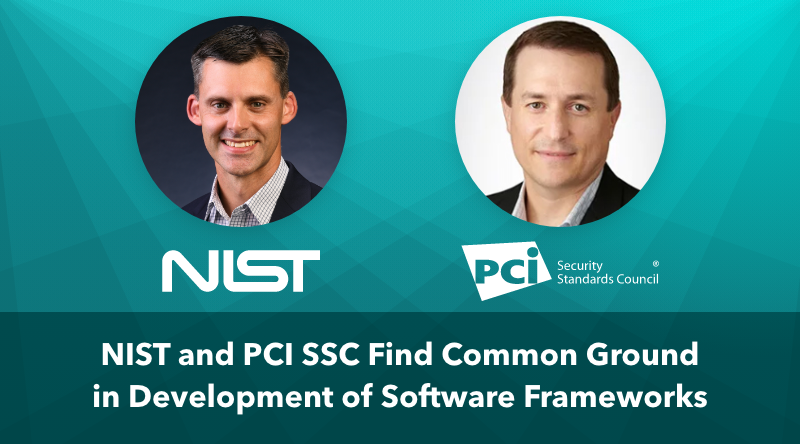
Machines are just one of the many tools that machinists use. These machines can repair metal products, such as cars. They can also create precision metal parts or new alloys. Machinists can be exposed to toxic substances. A good machinist is meticulous, can communicate well, and can interpret blueprints.
Machinists typically work full-time or part-time. Many machinists start working straight out of high school. Some machinists do an apprenticeship before moving on to a fulltime job. Others may pursue associate degrees. Some machinists may even pursue a degree in engineering or computer-aided design (CAD).
Machine operators often work in factories and specialty shops. While these jobs can be noisy and expose to hazardous materials, they also offer excellent opportunities for problem-solving. Machinists use manual and automatic machines. For those with more experience, it is possible to rise up to managerial and supervisory roles. Machine operators are in high demand as the baby boomers retire. Additionally, machine shops are being retooled for automation which increases job security.
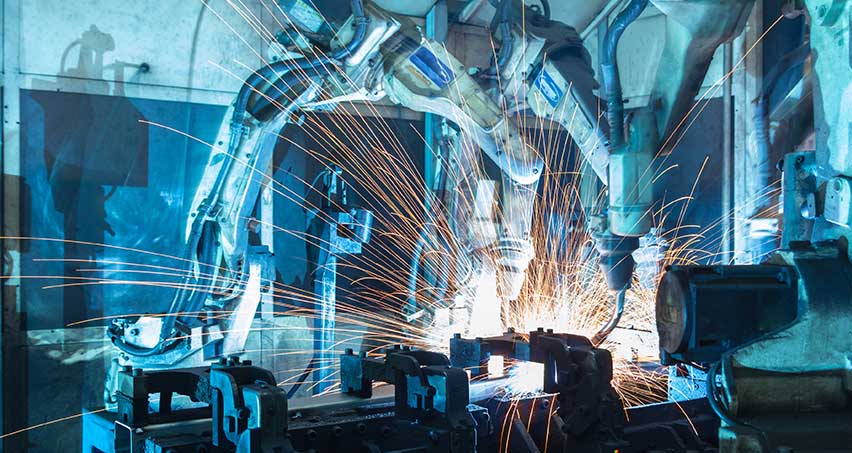
Depending on their employer, machinists could be assigned specific tasks such as setting up machines, fixing them, or making sure the parts they produce are compliant with quality standards. You can also work with assembly lines. These machines are operated by humans and robots. Other responsibilities include programming the machines and monitoring them, and reading blueprints.
Machinists have to work with many different materials like steel, aluminum (brass), copper, and other metals. Although most machinists work in machines that make metal parts they may also be required to work in other materials.
Although machinists typically have a high school diploma in most cases, some employers may require a bachelor's degree. Start your training program for machinists, which can last up to 4 years. To get more experience and learn, you can work alongside a mentor at work. Ask your mentor about any other training opportunities such as apprenticeships, or further education.
Machinists, no matter their employer, must work in a team. They can either work as part of a larger team or individually, but they must always follow safety procedures. This includes wearing proper safety equipment, such as earplugs, gloves, and masks. Machinists may also be exposed to chemicals, fumes, or other environmental hazards. Machinists aren't always under constant pressure.
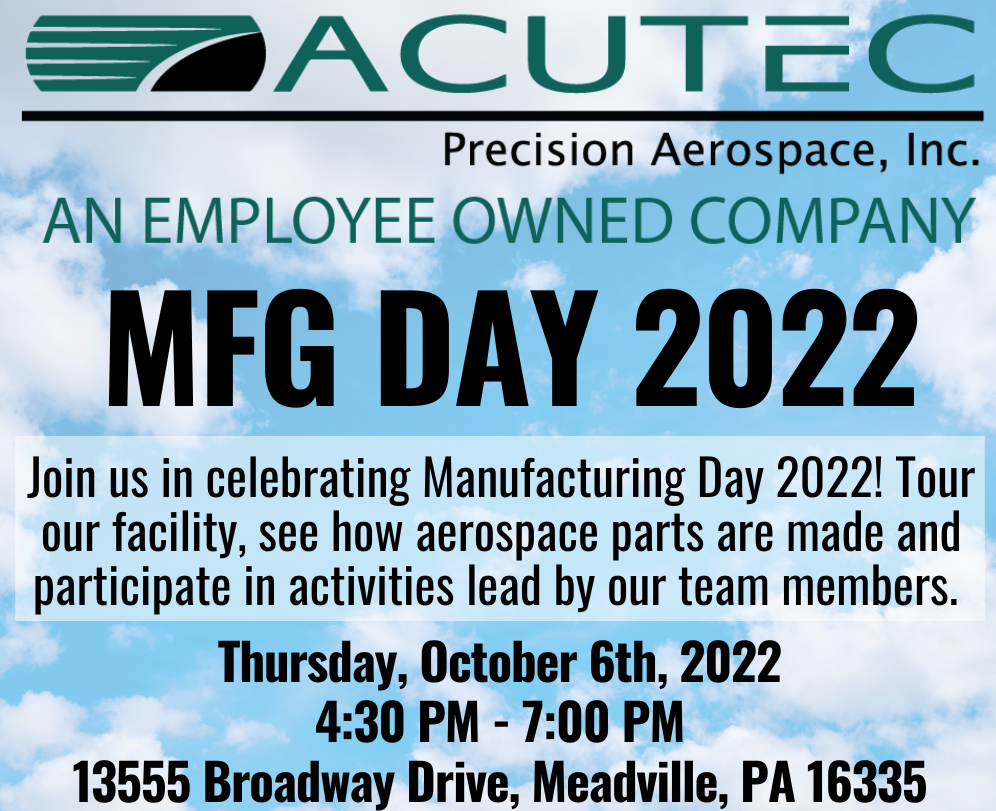
In addition to on-the job training, machinists have the option of enrolling in college courses and joining trade unions. Machinists with union membership enjoy better benefits and greater job security. Many union members have health insurance and retirement plans. Many colleges offer 2-year programs for machining associates.
You can climb up the corporate ladder with a degree as a machinist. Machinists will be more in demand as car parts become more expensive. Between 2020 and 2030, the projected job growth will be 7%. And, with increasing use of artificial intelligence and retooling for automation, machinists will be in high demand over the next two decades.
FAQ
Why automate your warehouse
Modern warehouses are increasingly dependent on automation. With the rise of ecommerce, there is a greater demand for faster delivery times as well as more efficient processes.
Warehouses should be able adapt quickly to new needs. Technology is essential for warehouses to be able to adapt quickly to changing needs. The benefits of automating warehouses are numerous. Here are some benefits of investing in automation
-
Increases throughput/productivity
-
Reduces errors
-
Improves accuracy
-
Safety enhancements
-
Eliminates bottlenecks
-
Allows companies scale more easily
-
Increases efficiency of workers
-
Provides visibility into everything that happens in the warehouse
-
Enhances customer experience
-
Improves employee satisfaction
-
Reduces downtime and improves uptime
-
You can be sure that high-quality products will arrive on time
-
Eliminates human error
-
Helps ensure compliance with regulations
Is it possible to automate certain parts of manufacturing
Yes! Yes! Automation has existed since ancient times. The Egyptians created the wheel thousands years ago. Robots are now used to assist us in assembly lines.
There are many applications for robotics in manufacturing today. These include:
-
Assembly line robots
-
Robot welding
-
Robot painting
-
Robotics inspection
-
Robots that create products
Manufacturing can also be automated in many other ways. For example, 3D printing allows us to make custom products without having to wait for weeks or months to get them manufactured.
What is the difference in Production Planning and Scheduling, you ask?
Production Planning (PP), also known as forecasting and identifying production capacities, is the process that determines what product needs to be produced at any particular time. This is accomplished by forecasting the demand and identifying production resources.
Scheduling is the process that assigns dates to tasks so they can get completed within a given timeframe.
What are the 4 types of manufacturing?
Manufacturing refers the process of turning raw materials into useful products with machines and processes. Manufacturing can include many activities such as designing and building, testing, packaging shipping, selling, servicing, and other related activities.
What does the term manufacturing industries mean?
Manufacturing Industries are businesses that produce products for sale. These products are sold to consumers. These companies use various processes such as production, distribution, retailing, management, etc., to fulfill this purpose. They create goods from raw materials, using machines and various other equipment. This includes all types and varieties of manufactured goods, such as food items, clothings, building supplies, furnitures, toys, electronics tools, machinery vehicles, pharmaceuticals medical devices, chemicals, among others.
Statistics
- Job #1 is delivering the ordered product according to specifications: color, size, brand, and quantity. (netsuite.com)
- In 2021, an estimated 12.1 million Americans work in the manufacturing sector.6 (investopedia.com)
- (2:04) MTO is a production technique wherein products are customized according to customer specifications, and production only starts after an order is received. (oracle.com)
- According to the United Nations Industrial Development Organization (UNIDO), China is the top manufacturer worldwide by 2019 output, producing 28.7% of the total global manufacturing output, followed by the United States, Japan, Germany, and India.[52][53] (en.wikipedia.org)
- You can multiply the result by 100 to get the total percent of monthly overhead. (investopedia.com)
External Links
How To
Six Sigma: How to Use it in Manufacturing
Six Sigma is defined by "the application SPC (statistical process control) techniques to achieve continuous improvements." It was developed by Motorola's Quality Improvement Department at their plant in Tokyo, Japan, in 1986. Six Sigma's core idea is to improve the quality of processes by standardizing and eliminating defects. In recent years, many companies have adopted this method because they believe there is no such thing as perfect products or services. Six Sigma aims to reduce variation in the production's mean value. If you take a sample and compare it with the average, you will be able to determine how much of the production process is different from the norm. If you notice a large deviation, then it is time to fix it.
Understanding the dynamics of variability within your business is the first step in Six Sigma. Once you have this understanding, you will need to identify sources and causes of variation. It is important to identify whether the variations are random or systemic. Random variations occur when people make mistakes; systematic ones are caused by factors outside the process itself. You could consider random variations if some widgets fall off the assembly lines. You might notice that your widgets always fall apart at the same place every time you put them together.
Once you have identified the problem, you can design solutions. That solution might involve changing the way you do things or redesigning the process altogether. After implementing the new changes, you should test them again to see if they worked. If they don’t work, you’ll need to go back and rework the plan.