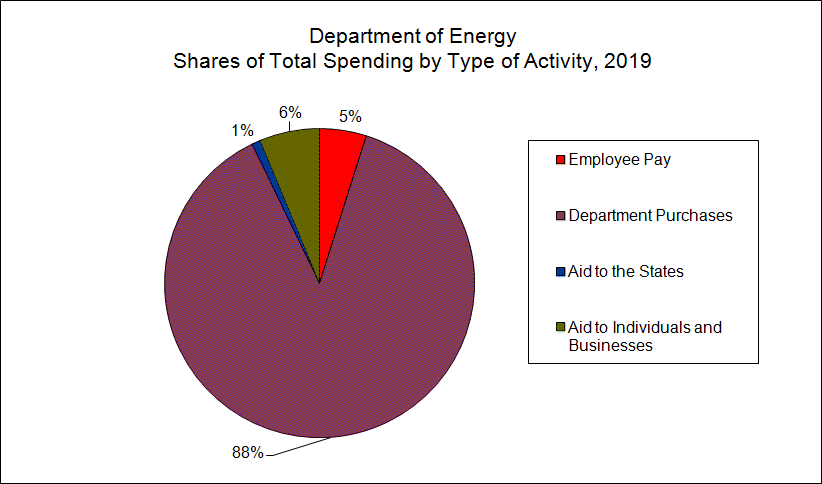
Manufacturing failures can be caused by many things. These include poor design, cost cutting initiatives, lackluster quality control, and more. There are a number of ways to avoid problems and improve product quality.
Does lean Manufacturing really work?
In many cases companies that implement lean methods are very successful. They are able, amongst other things, to eliminate waste and improve their cycle times. But they have to do it through a lot trial and errors and failure.
All lean practitioners agree that ownership and senior management are responsible for the majority of failures. The people in charge of the company are usually not aware of how to implement lean.
This can make it difficult for employees to join in and achieve the desired results. That's why it is important to begin a skill assessment well before implementing lean techniques. This will eliminate a lot ambiguity, help keep you on track and identify who is able to help you achieve your goals.
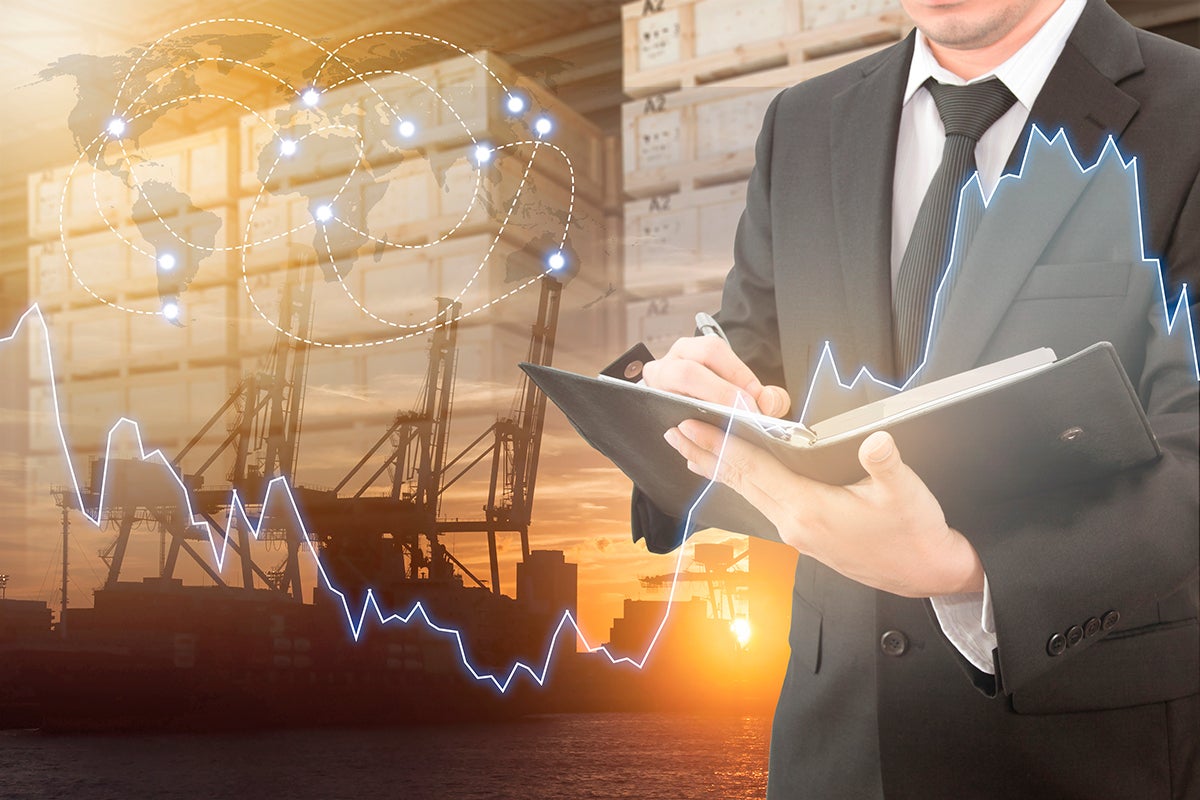
Why do manufacturers fail?
Some manufacturing faults are caused when the manufacturer fails to use the correct material or does not implement the proper quality control procedures. Manufacturing errors can also cause defects. This is when a product has been made in a manner that was not intended. It can be costly to repair these mistakes and the company may lose revenue.
It is important that the products are made correctly to avoid these problems. They can be expensive for both the manufacturer and consumer. To avoid these problems, manufacturers must be able detect failures as early as possible in the manufacturing process.
Understanding the causes of machine failures is essential to achieving this goal. This will help them improve their processes and reduce costs.
One of the most common failures is when a manufacturer does not have enough capital. There are many reasons why this can happen, but the most important thing to remember is that a business needs enough capital to continue to produce and sell in the long run.
It can be problematic for both the company and the consumer when a firm does not have enough funds to manufacture the product. This can lead a wide range of problems such as delayed delivery or lower product prices.
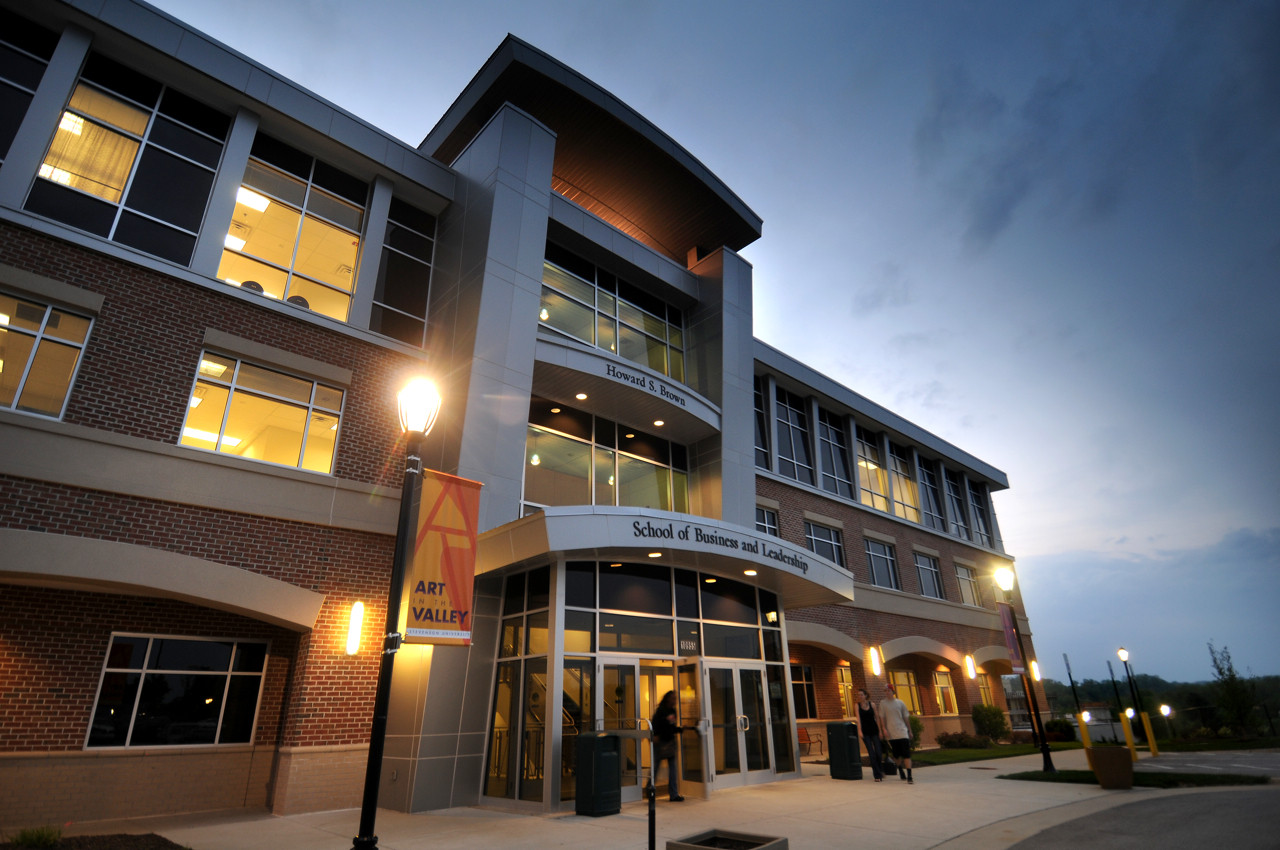
Also, the product may cause injury to a consumer who is using it in an unsafe fashion. If a person breaks their bone after playing with a lit match, the manufacturer could be held responsible for failing to warn the victim about the fire-starting risk.
This can be a very dangerous situation, especially for children who are not yet accustomed to handling hazardous materials. For the manufacturer it can be very expensive to fix this issue but is crucial for any business to survive.
FAQ
What are the four types of manufacturing?
Manufacturing refers the process of turning raw materials into useful products with machines and processes. Manufacturing involves many activities, including designing, building, testing and packaging, shipping, selling, service, and so on.
What are my options for learning more about manufacturing
You can learn the most about manufacturing by getting involved in it. You can read books, or watch instructional videos if you don't have the opportunity to do so.
How can manufacturing efficiency be improved?
First, we need to identify which factors are most critical in affecting production times. Then we need to find ways to improve these factors. If you aren't sure where to begin, think about the factors that have the greatest impact on production time. Once you've identified them, try to find solutions for each of those factors.
Why automate your warehouse
Modern warehouses have become more dependent on automation. Increased demand for efficient and faster delivery has resulted in a rise in e-commerce.
Warehouses should be able adapt quickly to new needs. To do so, they must invest heavily in technology. Automating warehouses is a great way to save money. Here are some of the reasons automation is worth your investment:
-
Increases throughput/productivity
-
Reduces errors
-
Increases accuracy
-
Safety Boosts
-
Eliminates bottlenecks
-
Companies can scale up more easily
-
Workers are more productive
-
The warehouse can be viewed from all angles.
-
Enhances customer experience
-
Improves employee satisfaction
-
This reduces downtime while increasing uptime
-
This ensures that quality products are delivered promptly
-
Removing human error
-
It ensures compliance with regulations
What is the responsibility of a production planner?
Production planners ensure that all project aspects are completed on time, within budget and within the scope. A production planner ensures that the service and product meet the client's expectations.
Statistics
- [54][55] These are the top 50 countries by the total value of manufacturing output in US dollars for its noted year according to World Bank.[56] (en.wikipedia.org)
- In the United States, for example, manufacturing makes up 15% of the economic output. (twi-global.com)
- Job #1 is delivering the ordered product according to specifications: color, size, brand, and quantity. (netsuite.com)
- According to the United Nations Industrial Development Organization (UNIDO), China is the top manufacturer worldwide by 2019 output, producing 28.7% of the total global manufacturing output, followed by the United States, Japan, Germany, and India.[52][53] (en.wikipedia.org)
- In 2021, an estimated 12.1 million Americans work in the manufacturing sector.6 (investopedia.com)
External Links
How To
How to use the Just-In Time Method in Production
Just-intime (JIT), a method used to lower costs and improve efficiency in business processes, is called just-in-time. It is a process where you get the right amount of resources at the right moment when they are needed. This means that only what you use is charged to your account. Frederick Taylor, a 1900s foreman, first coined the term. He noticed that workers were often paid overtime when they had to work late. He then concluded that if he could ensure that workers had enough time to do their job before starting to work, this would improve productivity.
JIT teaches you to plan ahead and prepare everything so you don’t waste time. It is important to look at your entire project from beginning to end and ensure that you have enough resources to handle any issues that may arise. You'll be prepared to handle any potential problems if you know in advance. This will ensure that you don't spend more money on things that aren't necessary.
There are different types of JIT methods:
-
Demand-driven: This type of JIT allows you to order the parts/materials required for your project on a regular basis. This will enable you to keep track of how much material is left after you use it. This will allow to you estimate the time it will take for more to be produced.
-
Inventory-based: This is a type where you stock the materials required for your projects in advance. This allows you predict the amount you can expect to sell.
-
Project-driven: This means that you have enough money to pay for your project. If you know the amount you require, you can buy the materials you need.
-
Resource-based JIT : This is probably the most popular type of JIT. Here you can allocate certain resources based purely on demand. You might assign more people to help with orders if there are many. If you don't have many orders, you'll assign fewer people to handle the workload.
-
Cost-based : This is similar in concept to resource-based. But here, you aren't concerned about how many people your company has but how much each individual costs.
-
Price-based: This is very similar to cost-based, except that instead of looking at how much each individual worker costs, you look at the overall price of the company.
-
Material-based: This is very similar to cost-based but instead of looking at total costs of the company you are concerned with how many raw materials you use on an average.
-
Time-based: Another variation of resource-based JIT. Instead of focusing only on how much each employee is costing, you should focus on how long it takes to complete your project.
-
Quality-based: This is yet another variation of resource-based JIT. Instead of focusing on the cost of each worker or how long it takes, think about how high quality your product is.
-
Value-based: This is one of the newest forms of JIT. In this case, you're not concerned with how well the products perform or whether they meet customer expectations. Instead, you focus on the added value that you provide to your market.
-
Stock-based: This inventory-based approach focuses on how many items are being produced at any one time. It's useful when you want maximum production and minimal inventory.
-
Just-in-time (JIT) planning: This is a combination of JIT and supply chain management. It is the process of scheduling components' delivery as soon as they have been ordered. It's important as it reduces leadtimes and increases throughput.