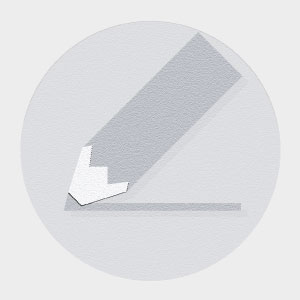
The National Association of Manufacturers (NAM), founded in 1898 is a trade union that represents approximately 14,000 member companies representing every sector of American manufacturing. NAM works to ensure the success of the 12 million American producers. It promotes new and innovative industries, as well as increasing awareness of manufacturing. NAM is represented in all 50 states.
NAM is America's most influential advocate to manufacturers. Its members include small and medium-sized manufacturing companies. It promotes new industries and advanced manufacturing. NAM also plays an important role in Washington policymaking. Its executives strive to reduce regulatory burden and promote trade and export. The headquarters of NAM is located in Washington, D.C. The company's executives have the ability to research and develop products and services that improve manufacturers' competitiveness.
Texas Association of Manufacturers congratulated the 84th Legislature on passing SB 1. The legislation will allow Texas businesses to grow through broad tax relief. Senator Bill Nelson and Representative Bill Bonnen sponsored the bill. The legislation also addresses the state’s tax code, Chapter 312 which allows temporary tax exemptions.
Texas's aerospace industry and aircraft manufacturing sector are major contributors to the state's economy. It supports nearly 49 billion in economic activity and employs 200,000 people. To maintain its strong state position, the industry must be competitive. The reform of TSCA is crucial to ensure the sector's growth and competitiveness. AMT's USMTO program offers assistance to its member companies to establish Brazil operations. Its USMTO program reported more than $400 million in manufacturing orders in May.
Texas' aerospace and aircraft industry needs to stay competitive in order to generate new revenue and jobs. The sector has made significant contributions to strengthening the state’s manufacturing sector.
The Texas Association of Manufacturers supports Chapter 312 of Texas' Tax Code renewal. The Association supports the Operating Reserve Demand Curve payments (ORDC) as well. These payments assist manufacturers in paying for dispatchable generator, which is crucial to the security and reliability of the electricity grid. The ORDC payments increased after Winter Storm Uri. This was due to changes to the "phase one” operations of Public Utility Commission.
AMT ranks among the top trade groups in the country. It has offices in more then 30 cities throughout the United States. The company's top executives are skilled in both business and policy. Its mission is promote advanced manufacturing and technology. It encourages regulatory convergence among the U.S.A. and the European Union. It promotes and protects manufacturers from every industry sector. It has developed several industry-specific committees, including one for small and medium-sized manufacturers. It also promotes technology and innovation.
AMT's video introduces "MT Ambassadors," young professionals who share their knowledge about manufacturing careers. The USMTO program is promoted by the organization, which allows member companies to visit Brazil. Its Top Shops conference and Top Shops programs help manufacturers benchmark their businesses and identify opportunities. The Association for Manufacturing Technology works together with the association to promote interoperability among manufacturing systems. The MTConnect program improves the capability of manufacturers to share and transmit data across various manufacturing technologies.
FAQ
Why automate your factory?
Modern warehousing has seen automation take center stage. The rise of e-commerce has led to increased demand for faster delivery times and more efficient processes.
Warehouses need to adapt quickly to meet changing needs. In order to do this, they need to invest in technology. Automation warehouses can bring many benefits. These are just a few reasons to invest in automation.
-
Increases throughput/productivity
-
Reduces errors
-
Increases accuracy
-
Safety Boosts
-
Eliminates bottlenecks
-
This allows companies to scale easily
-
This makes workers more productive
-
This gives you visibility into what happens in the warehouse
-
Enhances customer experience
-
Improves employee satisfaction
-
It reduces downtime, and increases uptime
-
You can be sure that high-quality products will arrive on time
-
Removes human error
-
It helps ensure compliance with regulations
Are there ways to automate parts of manufacturing?
Yes! Yes. The wheel was invented by the Egyptians thousands of years ago. We now use robots to help us with assembly lines.
Actually, robotics can be used in manufacturing for many purposes. These include:
-
Line robots
-
Robot welding
-
Robot painting
-
Robotics inspection
-
Robots that make products
There are many other examples of how manufacturing could benefit from automation. For instance, 3D printing allows us make custom products and not have to wait for months or even weeks to get them made.
What is the difference between Production Planning, Scheduling and Production Planning?
Production Planning (PP), is the process of deciding what production needs to take place at any given time. This can be done by forecasting demand and identifying production capabilities.
Scheduling refers to the process of allocating specific dates to tasks in order that they can be completed within a specified timeframe.
How can manufacturing excess production be decreased?
Better inventory management is key to reducing excess production. This would reduce the time spent on unproductive activities like purchasing, storing and maintaining excess stock. This will allow us to free up resources for more productive tasks.
One way to do this is to adopt a Kanban system. A Kanbanboard is a visual tool that allows you to keep track of the work being done. A Kanban system allows work items to move through several states before reaching their final destination. Each state represents a different priority level.
For instance, when work moves from one stage to another, the current task is complete enough to be moved to the next stage. If a task is still in its beginning stages, it will continue to be so until it reaches the end.
This keeps work moving and ensures no work is lost. Managers can view the Kanban board to see how much work they have done. This data allows them adjust their workflow based upon real-time data.
Lean manufacturing is another option to control inventory levels. Lean manufacturing seeks to eliminate waste from every step of the production cycle. Anything that doesn't add value to the product is considered waste. These are some of the most common types.
-
Overproduction
-
Inventory
-
Unnecessary packaging
-
Exceed materials
By implementing these ideas, manufacturers can improve efficiency and cut costs.
Statistics
- Job #1 is delivering the ordered product according to specifications: color, size, brand, and quantity. (netsuite.com)
- According to the United Nations Industrial Development Organization (UNIDO), China is the top manufacturer worldwide by 2019 output, producing 28.7% of the total global manufacturing output, followed by the United States, Japan, Germany, and India.[52][53] (en.wikipedia.org)
- In 2021, an estimated 12.1 million Americans work in the manufacturing sector.6 (investopedia.com)
- It's estimated that 10.8% of the U.S. GDP in 2020 was contributed to manufacturing. (investopedia.com)
- Many factories witnessed a 30% increase in output due to the shift to electric motors. (en.wikipedia.org)
External Links
How To
How to use 5S to increase Productivity in Manufacturing
5S stands as "Sort", Set In Order", Standardize", Separate" and "Store". The 5S methodology was developed at Toyota Motor Corporation in 1954. It helps companies achieve higher levels of efficiency by improving their work environment.
The basic idea behind this method is to standardize production processes, so they become repeatable, measurable, and predictable. It means tasks like cleaning, sorting or packing, labeling, and storing are done every day. Because workers know what they can expect, this helps them perform their jobs more efficiently.
Implementing 5S requires five steps. These are Sort, Set In Order, Standardize. Separate. And Store. Each step requires a different action to increase efficiency. If you sort items, it makes them easier to find later. Once you have placed items in an ordered fashion, you will put them together. After you have divided your inventory into groups you can store them in easy-to-reach containers. Labeling your containers will ensure that everything is correctly labeled.
This requires employees to critically evaluate how they work. Employees should understand why they do the tasks they do, and then decide if there are better ways to accomplish them. In order to use the 5S system effectively, they must be able to learn new skills.
The 5S method not only increases efficiency but also boosts morale and teamwork. They will feel motivated to strive for higher levels of efficiency once they start to see results.