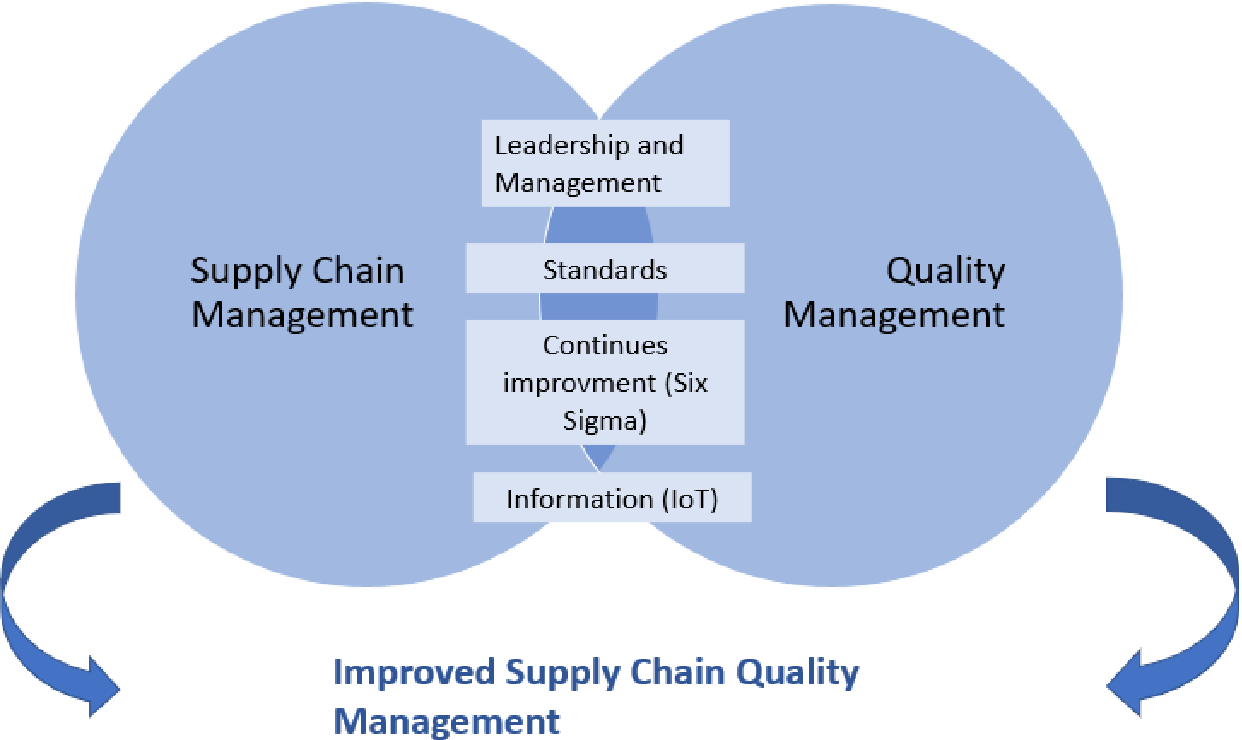
It is important to have a smooth media supply chain. Companies must invest in modern technology to ensure their content gets delivered to consumers in a timely manner. A cloud-based platform that is purpose-built for media assets can be a great way of ensuring your media assets are being used as efficiently as possible. It can also help you gain greater insights into your business by facilitating processes.
To get the most from your media supply chain workflow you must understand all components. A workflow could include quality control, which ensures that media files are properly formatted, sound mapping is done, and the codec is used. This is crucial to ensure that the content gets delivered in the correct format and that it is kept clean. Having a good metadata framework also helps you understand what content is being delivered, which can help you find content faster.
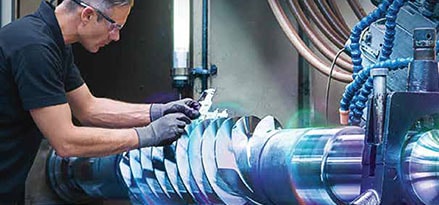
You may be able to receive content from third parties or other companies as part of your media supply chain workflow. This can present challenges as files may arrive in multiple formats. Also, you may have to modify the files in order to make them usable. This may include changing the format or transcoding the master files into smaller proxy files. This can cause your business to be disrupted and cost you a lot of money.
Media supply chain workflows have become much more complicated than in the past. Gone are the days of inserting tape onto a machine. The way content is produced has changed with the advent of streaming services and video editing technology. You can now create multiple versions and ensure the highest quality content. This is a great way to save money and still deliver high quality content.
You will need to be able to understand the process involved in order to make the most of your media supply chain workflow. Expertise in server and client operating systems, networking, as well as media terminology is essential. Experience with cloud deployments is also required. An IT Analyst with expertise in cloud environments may be able to help you if you have any questions.
The video engineer collaborates closely with the client's staff to design a media supply chains workflow. They are responsible in improving functionality, working with vendors and delivering media to the user. They are also responsible for developing requirements for new features.
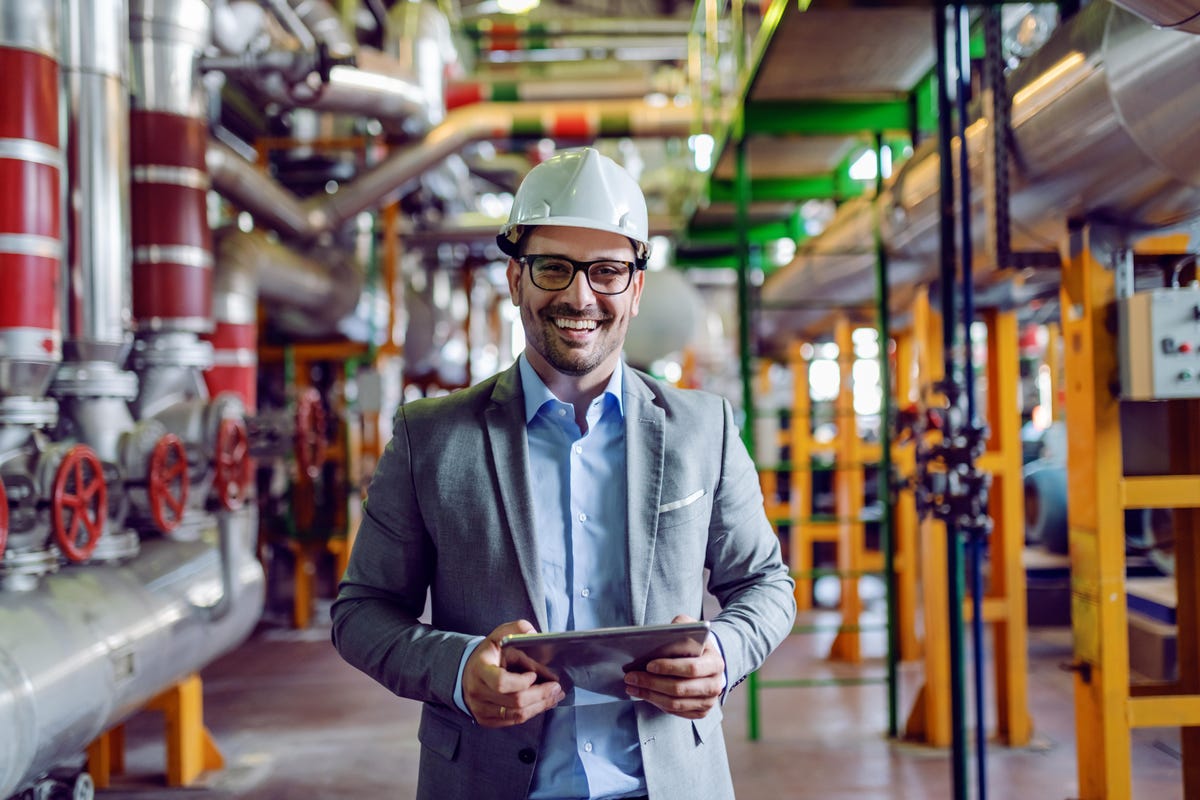
The Director, Product is the lead on Paramount Global Media Supply Chain Platforms Operations workflows. They will work with internal and external collaborators to develop and implement solutions for Paramount's customers. They will be reviewing product requirements and providing feedback on a daily basis. They will also manage product development cycles that use Agile methodology. They will also communicate product requirements to development teams and oversee the translation of these requirements into the product.
FAQ
What's the difference between Production Planning & Scheduling?
Production Planning (PP) is the process of determining what needs to be produced at any given point in time. Forecasting and identifying production capacity are two key elements to this process.
Scheduling is the process that assigns dates to tasks so they can get completed within a given timeframe.
How can we improve manufacturing efficiency?
First, we need to identify which factors are most critical in affecting production times. We must then find ways that we can improve these factors. If you don’t know how to start, look at which factors have the greatest impact upon production time. Once you have identified the factors, then try to find solutions.
Is there anything we should know about Manufacturing Processes prior to learning about Logistics.
No. You don't have to know about manufacturing processes before learning about logistics. But, being familiar with manufacturing processes will give you a better understanding about how logistics works.
What is the role of a logistics manager
A logistics manager ensures that all goods are delivered on time and without damage. This is done using his/her knowledge of the company's products. He/she also needs to ensure adequate stock to meet demand.
Statistics
- According to the United Nations Industrial Development Organization (UNIDO), China is the top manufacturer worldwide by 2019 output, producing 28.7% of the total global manufacturing output, followed by the United States, Japan, Germany, and India.[52][53] (en.wikipedia.org)
- In the United States, for example, manufacturing makes up 15% of the economic output. (twi-global.com)
- According to a Statista study, U.S. businesses spent $1.63 trillion on logistics in 2019, moving goods from origin to end user through various supply chain network segments. (netsuite.com)
- (2:04) MTO is a production technique wherein products are customized according to customer specifications, and production only starts after an order is received. (oracle.com)
- Many factories witnessed a 30% increase in output due to the shift to electric motors. (en.wikipedia.org)
External Links
How To
How to Use the Just In Time Method in Production
Just-in-time is a way to cut costs and increase efficiency in business processes. It's the process of obtaining the right amount and timing of resources when you need them. This means that you only pay the amount you actually use. Frederick Taylor developed the concept while working as foreman in early 1900s. Taylor observed that overtime was paid to workers if they were late in working. He then concluded that if he could ensure that workers had enough time to do their job before starting to work, this would improve productivity.
JIT is a way to plan ahead and make sure you don't waste any money. It is important to look at your entire project from beginning to end and ensure that you have enough resources to handle any issues that may arise. You can anticipate problems and have enough equipment and people available to fix them. This will prevent you from spending extra money on unnecessary things.
There are different types of JIT methods:
-
Demand-driven: This JIT is where you place regular orders for the parts/materials that are needed for your project. This will allow to track how much material has been used up. You'll also be able to estimate how long it will take to produce more.
-
Inventory-based: This is a type where you stock the materials required for your projects in advance. This allows one to predict how much they will sell.
-
Project-driven: This means that you have enough money to pay for your project. If you know the amount you require, you can buy the materials you need.
-
Resource-based JIT : This is probably the most popular type of JIT. Here you can allocate certain resources based purely on demand. For example, if there is a lot of work coming in, you will have more people assigned to them. If you don't have many orders, you'll assign fewer people to handle the workload.
-
Cost-based: This is similar to resource-based, except that here you're not just concerned about how many people you have but how much each person costs.
-
Price-based: This is a variant of cost-based. However, instead of focusing on the individual workers' costs, this looks at the total price of the company.
-
Material-based: This approach is similar to cost-based. However, instead of looking at the total cost for the company, you look at how much you spend on average on raw materials.
-
Time-based: This is another variation of resource-based JIT. Instead of worrying about how much each worker costs, you can focus on how long the project takes.
-
Quality-based JIT - This is another form of resource-based JIT. Instead of looking at the labor costs and time it takes to make a product, think about its quality.
-
Value-based JIT: This is the latest form of JIT. In this instance, you are not concerned about the product's performance or meeting customer expectations. Instead, you're focused on how much value you add to the market.
-
Stock-based: This is an inventory-based method that focuses on the actual number of items being produced at any given time. This method is useful when you want to increase production while decreasing inventory.
-
Just-intime planning (JIT), is a combination JIT/sales chain management. This refers to the scheduling of the delivery of components as soon after they are ordered. It is essential because it reduces lead-times and increases throughput.