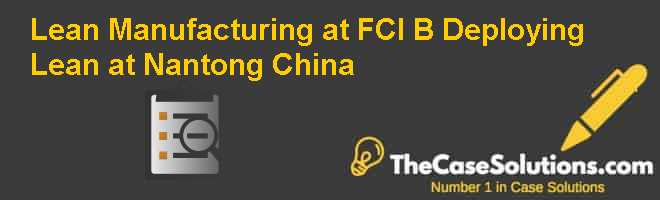
Classical economics identifies three fundamental sectors. These three basic sectors can be divided into manufacturing, financial activities, and services. Business classifications are based on the characteristics and risks of each business. Learn more about each one of the three sector groups below. Here is a quick overview of the different types of businesses within each sector. This information can be further explored if you are curious. Keep in mind, however, that these categories don't have to be mutually exclusive.
Economic activity
Factors that are used to produce, inputs, or outputs affect the country's economic activity. The demand for a particular good or service is often a key factor in determining the region's economic activity. There are two types if economic activity. Primary economic activities provide goods or services to satisfy daily human needs, while secondary economic activities add value to raw materials and combine them to make a more valuable product. Some examples of secondary economic activities include manufacturing and processing industries.
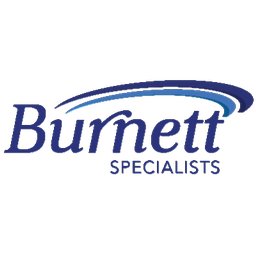
Classification of businesses
Business classification refers to the process of grouping businesses based on their activities. There are two main categories: primary and secondary. Primary businesses are those that mine and trade natural resources. The second category of businesses processes and converts raw materials to consumer-ready products. There are many differences between the two types. Below are the main differences between these two types. The information in this article will help you to decide which type is right for your business.
Characteristics
Following discussion will discuss the differences in the primary, second, and third sectors. It will also focus on how each sector impacts the economy. First, let's define sectors. Sectors can be considered unique economic entities. They respond differently depending on different factors. These conditions could be repeated, such business cycles, or they might be one-off events, such improvements in technology. These characteristics are useful in identifying the most profitable sectors and determining their relative importance within an economy.
There are risks
Industry risk is the variation of performance across industries and among companies. It is measured by the variation in return on equity and profitability. This could also reflect stock market performance, depending on which industry. For example, a company that manufactures steel is considered to be high risk because of the potential for a major earthquake in the region. An analysis of these risks can help investors identify volatile sectors.

Investments
While investors often invest in certain companies, sector investing can be a great option for the more cautious investor. Sectors are more risk-free and can be found within mutual funds and exchange traded funds. In addition, sector investing is becoming a popular investment strategy today. This article will explain how sector investing can help to find the right investments. Continue reading to find out more. For more information, don't miss our free resource section.
FAQ
Is it necessary to be familiar with Manufacturing Processes before we learn about Logistics.
No. No. Knowing about manufacturing processes will help you understand how logistics works.
What type of jobs is there in logistics
Logistics can offer many different jobs. Some of them are:
-
Warehouse workers – They load and unload pallets and trucks.
-
Transportation drivers – These drivers drive trucks and wagons to transport goods and pick up the goods.
-
Freight handlers - They sort and pack freight in warehouses.
-
Inventory managers – These people oversee inventory at warehouses.
-
Sales representatives - They sell products to customers.
-
Logistics coordinators – They plan and coordinate logistics operations.
-
Purchasing agents – They buy goods or services necessary to run a company.
-
Customer service representatives are available to answer customer calls and emails.
-
Shipping clerks – They process shipping orders, and issue bills.
-
Order fillers: They fill orders based off what has been ordered and shipped.
-
Quality control inspectors: They inspect outgoing and incoming products for any defects.
-
Others - There are many other types of jobs available in logistics, such as transportation supervisors, cargo specialists, etc.
What are the 4 types of manufacturing?
Manufacturing refers the process of turning raw materials into useful products with machines and processes. Manufacturing involves many activities, including designing, building, testing and packaging, shipping, selling, service, and so on.
What is production management?
Production Planning includes planning for all aspects related to production. This document ensures that everything is prepared and available when you are ready for shooting. This document should also include information on how to get the best result on set. This includes location information, crew details, equipment specifications, and casting lists.
The first step in filming is to define what you want. You might have an idea of where you want to film, or you may have specific locations or sets in mind. Once you have identified the scenes and locations, you can start to determine which elements are required for each scene. Perhaps you have decided that you need to buy a car but aren't sure which model. This is where you can look up car models online and narrow down your options by choosing from different makes and models.
Once you have found the right vehicle, you can think about adding accessories. Do you have people who need to be seated in the front seat? Maybe you need someone to move around in the back. Maybe you'd like to change the interior from black to a white color. These questions will help you determine the exact look and feel of your car. It is also worth considering the types of shots that you wish to take. You will be filming close-ups and wide angles. Maybe the engine or steering wheel is what you are looking to film. These details will help identify the exact car you wish to film.
Once you have all the information, you are ready to create a plan. You will know when you should start and when you should finish shooting. Every day will have a time for you to arrive at the location, leave when you are leaving and return home when you are done. This way, everyone knows what they need to do and when. If you need to hire extra staff, you can make sure you book them in advance. There is no point in hiring someone who won't turn up because you didn't let him know.
Your schedule will also have to be adjusted to reflect the number of days required to film. Some projects can be completed in a matter of days or weeks. Others may take several days. While creating your schedule, it is important to remember whether you will require more than one shot per day. Multiple takes of the same location will lead to higher costs and take more time. If you are unsure if you need multiple takes, it is better to err on the side of caution and shoot fewer takes rather than risk wasting money.
Budgeting is another important aspect of production planning. It is important to set a realistic budget so you can work within your budget. Remember that you can always reduce the budget later on if you run into unforeseen problems. However, you shouldn't overestimate the amount of money you will spend. You'll end up with less money after paying for other things if the cost is underestimated.
Planning production is a tedious process. Once you have a good understanding of how everything works together, planning future projects becomes easy.
How can we reduce manufacturing overproduction?
Better inventory management is key to reducing excess production. This would decrease the time that is spent on inefficient activities like purchasing, storing, or maintaining excess stock. This will allow us to free up resources for more productive tasks.
A Kanban system is one way to achieve this. A Kanban board can be used to monitor work progress. Work items are moved through various states to reach their destination in a Kanban system. Each state represents a different priority level.
When work is completed, it can be transferred to the next stage. If a task is still in its beginning stages, it will continue to be so until it reaches the end.
This allows work to move forward and ensures that no work is missed. Managers can see how much work has been done and the status of each task at any time with a Kanban Board. This allows them to adjust their workflows based on real-time information.
Another way to control inventory levels is to implement lean manufacturing. Lean manufacturing seeks to eliminate waste from every step of the production cycle. Anything that doesn't add value to the product is considered waste. There are several types of waste that you might encounter:
-
Overproduction
-
Inventory
-
Packaging not required
-
Excess materials
These ideas will help manufacturers increase efficiency and lower costs.
Statistics
- Many factories witnessed a 30% increase in output due to the shift to electric motors. (en.wikipedia.org)
- Job #1 is delivering the ordered product according to specifications: color, size, brand, and quantity. (netsuite.com)
- You can multiply the result by 100 to get the total percent of monthly overhead. (investopedia.com)
- In the United States, for example, manufacturing makes up 15% of the economic output. (twi-global.com)
- In 2021, an estimated 12.1 million Americans work in the manufacturing sector.6 (investopedia.com)
External Links
How To
How to use the Just In-Time Production Method
Just-intime (JIT), a method used to lower costs and improve efficiency in business processes, is called just-in-time. It's the process of obtaining the right amount and timing of resources when you need them. This means that you only pay for what you actually use. Frederick Taylor, a 1900s foreman, first coined the term. He saw how overtime was paid to workers for work that was delayed. He concluded that if workers were given enough time before they start work, productivity would increase.
The idea behind JIT is that you should plan ahead and have everything ready so you don't waste money. Also, you should look at the whole project from start-to-finish and make sure you have the resources necessary to address any issues. If you expect problems to arise, you will be able to provide the necessary equipment and personnel to address them. This will ensure that you don't spend more money on things that aren't necessary.
There are many types of JIT methods.
-
Demand-driven: This type of JIT allows you to order the parts/materials required for your project on a regular basis. This will let you track the amount of material left over after you've used it. You'll also be able to estimate how long it will take to produce more.
-
Inventory-based: This type allows you to stock the materials needed for your projects ahead of time. This allows you to predict how much you can expect to sell.
-
Project-driven : This is a method where you make sure that enough money is set aside to pay the project's cost. If you know the amount you require, you can buy the materials you need.
-
Resource-based JIT is the most widespread form. You assign certain resources based off demand. You might assign more people to help with orders if there are many. If you don't receive many orders, then you'll assign fewer employees to handle the load.
-
Cost-based: This is a similar approach to resource-based but you are not only concerned with how many people you have, but also how much each one costs.
-
Price-based: This is very similar to cost-based, except that instead of looking at how much each individual worker costs, you look at the overall price of the company.
-
Material-based is an alternative to cost-based. Instead of looking at the total cost in the company, this method focuses on the average amount of raw materials that you consume.
-
Time-based: This is another variation of resource-based JIT. Instead of focusing on the cost of each employee, you will focus on the time it takes to complete a project.
-
Quality-based JIT: This is another variation of resource based JIT. Instead of thinking about the cost of each employee or the time it takes to produce something, you focus on how good your product quality.
-
Value-based JIT: One of the most recent forms of JIT. In this instance, you are not concerned about the product's performance or meeting customer expectations. Instead, your focus is on the value you bring to the market.
-
Stock-based: This is an inventory-based method that focuses on the actual number of items being produced at any given time. It's useful when you want maximum production and minimal inventory.
-
Just-intime (JIT), planning is a combination JIT management and supply chain management. This refers to the scheduling of the delivery of components as soon after they are ordered. It's important because it reduces lead times and increases throughput.