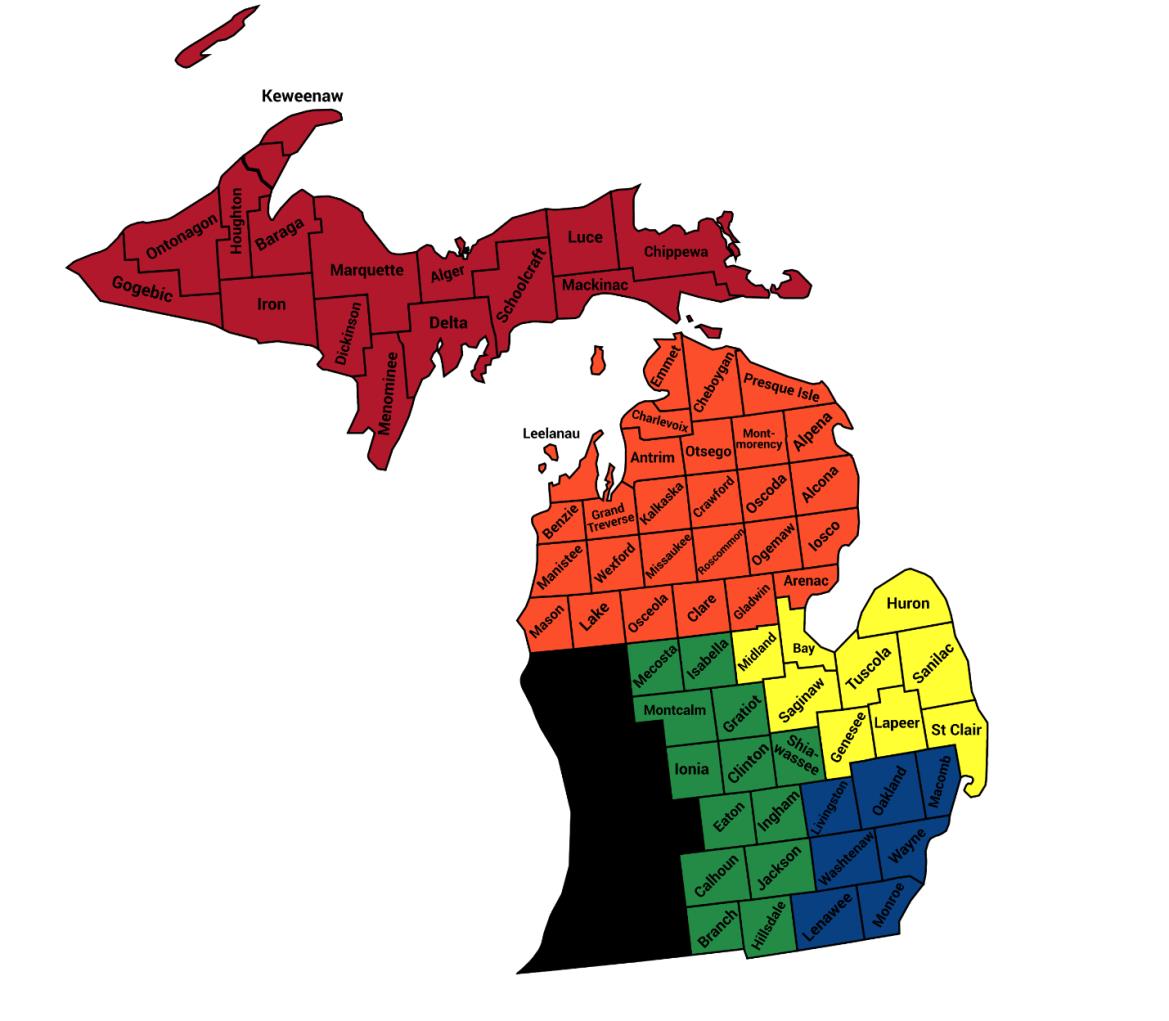
Industrial engineering (wvu) is the study that people, machines, equipment, information and energy work together to create products or services. It is concerned with maximizing productivity by minimizing costs, increasing quality, and maintaining a safe environment.
West Virginia engineers have a high demand in many industries. They use their knowledge of production, design, and operation in order to solve problems for businesses of all kinds.
Industrial engineering is different from other engineering types. It focuses on the bigger picture, the relationship between people and systems, as well as the "right" combination to produce products or service that meets or exceeds customer expectations. Industrial engineering is a broad area that requires technical and interpersonal abilities.
These professionals are responsible for bridging the gap between management (and operations), motivating staff and determining how to best use tools and systems. They use sophisticated software and computers to ensure the proper functioning of all systems, as well as productivity, reliability, schedule compliance, and cost management.
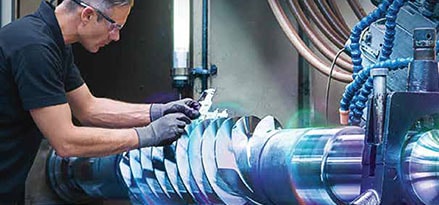
Students in this program apply the skills they learn from mathematics, physics statisitics, engineering, and managerial disciplines to analyze processes and create plans. They also design equipment and processes which produce products or service. You can choose to work on projects that involve electrical, computer, mechanical and electronic equipment.
Many college graduates with industrial engineering experiences find that they have an advantage in the job market. These graduates can enjoy higher salaries, increased responsibilities, and better work/life integration.
Co-op employment is an excellent opportunity for students to gain practical experience in the workplace while still in school. They are usually with local manufacturers but they can also be found at banks, insurance companies, construction firms, and public utilities.
The University of West Virginia's co-op programme provides students with real-world engineering experience. This includes calculating materials, inspecting sites and participating in field review.
There are also numerous internships for undergraduates that give them valuable experience working on real-world industrial projects. It is a great way to get a first-hand look at the engineering profession, and to make valuable connections with employers.
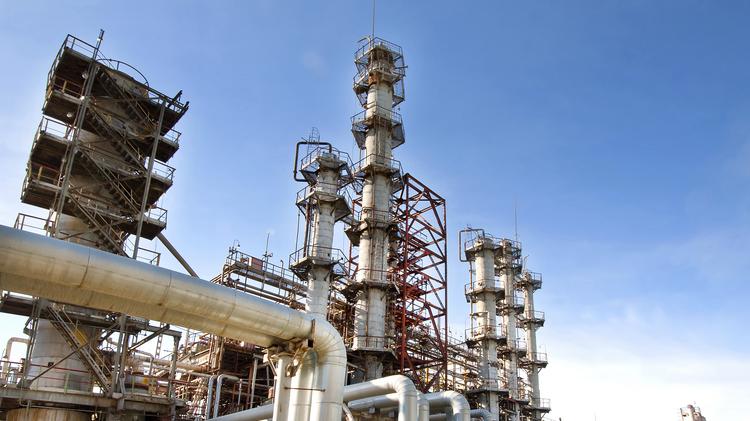
Graduates can sit for the exam to become an engineer in WV. This is an excellent way to boost your resume and make you application stand out.
To be successful in the industrial engineering industry, you must choose a program that suits your interests and career objectives. The University of West Virginia offers a variety of industrial engineering programs to suit your needs.
A bachelor's is the standard requirement for industrial engineering careers, but some colleges or universities offer graduate-level degrees. These programs, which can last several years, are designed to help students prepare for further study or a career as industrial engineers.
The University of West Virginia has a bachelor degree in industrial technology, along with several master's programs. These programs aim to prepare students in industrial engineering careers and help them develop their leadership skills in the business world, in education, or in government. These programs are accredited and approved by the Accreditation Council for Engineering Technology (ABET), Inc.
FAQ
What are the 7 Rs of logistics management?
The 7R's of Logistics is an acronym for the seven basic principles of logistics management. It was developed by International Association of Business Logisticians (IABL), and published as part of their "Seven Principles of Logistics Management Series" in 2004.
The acronym is made up of the following letters:
-
Responsible - ensure that all actions taken are within legal requirements and are not harmful to others.
-
Reliable - You can have confidence that you will fulfill your promises.
-
Reasonable - make sure you use your resources well and don't waste them.
-
Realistic - Consider all aspects of operations, including environmental impact and cost effectiveness.
-
Respectful – Treat others fairly and equitably.
-
Be resourceful: Look for opportunities to save money or increase productivity.
-
Recognizable: Provide customers with value-added service
What is the job of a production plan?
A production planner makes sure all project elements are delivered on schedule, within budget, as well as within the agreed scope. A production planner ensures that the service and product meet the client's expectations.
What is production planning?
Production planning is the process of creating a plan that covers all aspects of production. This includes scheduling, budgeting and crew, location, equipment, props, and more. This document will ensure everything is in order and ready to go when you need it. It should also contain information on achieving the best results on set. It should include information about shooting locations, casting lists, crew details, equipment requirements, and shooting schedules.
The first step is to outline what you want to film. You may have already decided where you would like to shoot, or maybe there are specific locations or sets that you want to use. Once you have identified your locations and scenes it's time to begin figuring out what elements you will need for each one. For example, you might decide that you need a car but don't know exactly what model you want. If this is the case, you might start searching online for car models and then narrow your options by selecting from different makes.
After you have chosen the right car, you will be able to begin thinking about accessories. Do you have people who need to be seated in the front seat? Or perhaps you need someone walking around the back of the car? You might want to change your interior color from black and white. These questions will help you determine the exact look and feel of your car. Also, think about what kind of shots you would like to capture. Are you going to be shooting close-ups? Or wide angles? Maybe you want the engine or the steering wheels to be shown. These factors will help you determine which car style you want to film.
Once you've determined the above, it is time to start creating a calendar. You can use a schedule to determine when and where you need it to be shot. You will need to know when you have to be there, what time you have to leave and when your return home. Everyone will know what they need and when. Hire extra staff by booking them ahead of time. There is no point in hiring someone who won't turn up because you didn't let him know.
Also, consider how many days you will be filming your schedule. Some projects are quick and easy, while others take weeks. When creating your schedule, be aware of whether you need more shots per day. Multiplying takes in the same area will result both in increased costs and a longer time. It is better to be cautious and take fewer shots than you risk losing money if you are not sure if multiple takes are necessary.
Budget setting is an important part of production planning. As it will allow you and your team to work within your financial means, setting a realistic budget is crucial. It is possible to reduce the budget at any time if you experience unexpected problems. However, it is important not to overestimate the amount that you will spend. If you underestimate how much something costs, you'll have less money to pay for other items.
Production planning is a detailed process. But, once you understand the workings of everything, it becomes easier for future projects to be planned.
What do you mean by warehouse?
A warehouse is an area where goods are stored before being sold. It can be indoors or out. In some cases it could be both indoors and outdoors.
Why automate your warehouse?
Modern warehouses have become more dependent on automation. The rise of e-commerce has led to increased demand for faster delivery times and more efficient processes.
Warehouses must adapt quickly to meet changing customer needs. Technology investment is necessary to enable warehouses to respond quickly to changing demands. Automating warehouses has many benefits. Here are some benefits of investing in automation
-
Increases throughput/productivity
-
Reduces errors
-
Accuracy is improved
-
Safety Boosts
-
Eliminates bottlenecks
-
Companies can scale up more easily
-
Makes workers more efficient
-
The warehouse can be viewed from all angles.
-
Enhances customer experience
-
Improves employee satisfaction
-
Reduces downtime and improves uptime
-
You can be sure that high-quality products will arrive on time
-
Removing human error
-
It ensures compliance with regulations
What is the difference between manufacturing and logistics
Manufacturing refers the process of producing goods from raw materials through machines and processes. Logistics manages all aspects of the supply chain, including procurement, production planning and distribution, inventory control, transportation, customer service, and transport. Logistics and manufacturing are often referred to as one thing. It encompasses both the creation of products and their delivery to customers.
Statistics
- According to a Statista study, U.S. businesses spent $1.63 trillion on logistics in 2019, moving goods from origin to end user through various supply chain network segments. (netsuite.com)
- You can multiply the result by 100 to get the total percent of monthly overhead. (investopedia.com)
- Job #1 is delivering the ordered product according to specifications: color, size, brand, and quantity. (netsuite.com)
- In 2021, an estimated 12.1 million Americans work in the manufacturing sector.6 (investopedia.com)
- In the United States, for example, manufacturing makes up 15% of the economic output. (twi-global.com)
External Links
How To
How to Use Just-In-Time Production
Just-in-time (JIT) is a method that is used to reduce costs and maximize efficiency in business processes. It allows you to get the right amount resources at the right time. This means you only pay what you use. Frederick Taylor was the first to coin this term. He developed it while working as a foreman during the early 1900s. Taylor observed that overtime was paid to workers if they were late in working. He decided that workers would be more productive if they had enough time to complete their work before they started to work.
JIT is a way to plan ahead and make sure you don't waste any money. Also, you should look at the whole project from start-to-finish and make sure you have the resources necessary to address any issues. If you anticipate that there might be problems, you'll have enough people and equipment to fix them. This will ensure that you don't spend more money on things that aren't necessary.
There are several types of JIT techniques:
-
Demand-driven: This is a type of JIT where you order the parts/materials needed for your project regularly. This will allow for you to track the material that you have left after using it. You'll also be able to estimate how long it will take to produce more.
-
Inventory-based: This type allows you to stock the materials needed for your projects ahead of time. This allows for you to anticipate how much you can sell.
-
Project-driven: This is an approach where you set aside enough funds to cover the cost of your project. Knowing how much money you have available will help you purchase the correct amount of materials.
-
Resource-based JIT: This is the most popular form of JIT. Here, you allocate certain resources based on demand. You will, for example, assign more staff to deal with large orders. If you don’t have many orders you will assign less people to the work.
-
Cost-based: This is similar to resource-based, except that here you're not just concerned about how many people you have but how much each person costs.
-
Price-based: This approach is very similar to the cost-based method except that you don't look at individual workers costs but the total cost of the company.
-
Material-based: This is very similar to cost-based but instead of looking at total costs of the company you are concerned with how many raw materials you use on an average.
-
Time-based JIT: A variation on resource-based JIT. Instead of focusing on the cost of each employee, you will focus on the time it takes to complete a project.
-
Quality-based JIT: Another variation on resource-based JIT. Instead of thinking about how much each employee costs or how long it takes to manufacture something, you think about how good the quality of your product is.
-
Value-based JIT is the newest form of JIT. This is where you don't care about how the products perform or whether they meet customers' expectations. Instead, you are focused on adding value to the marketplace.
-
Stock-based: This stock-based method focuses on the actual quantity of products being made at any given time. This is used to increase production and minimize inventory.
-
Just-intime (JIT), planning is a combination JIT management and supply chain management. It is the process that schedules the delivery of components within a short time of their order. It's important because it reduces lead times and increases throughput.