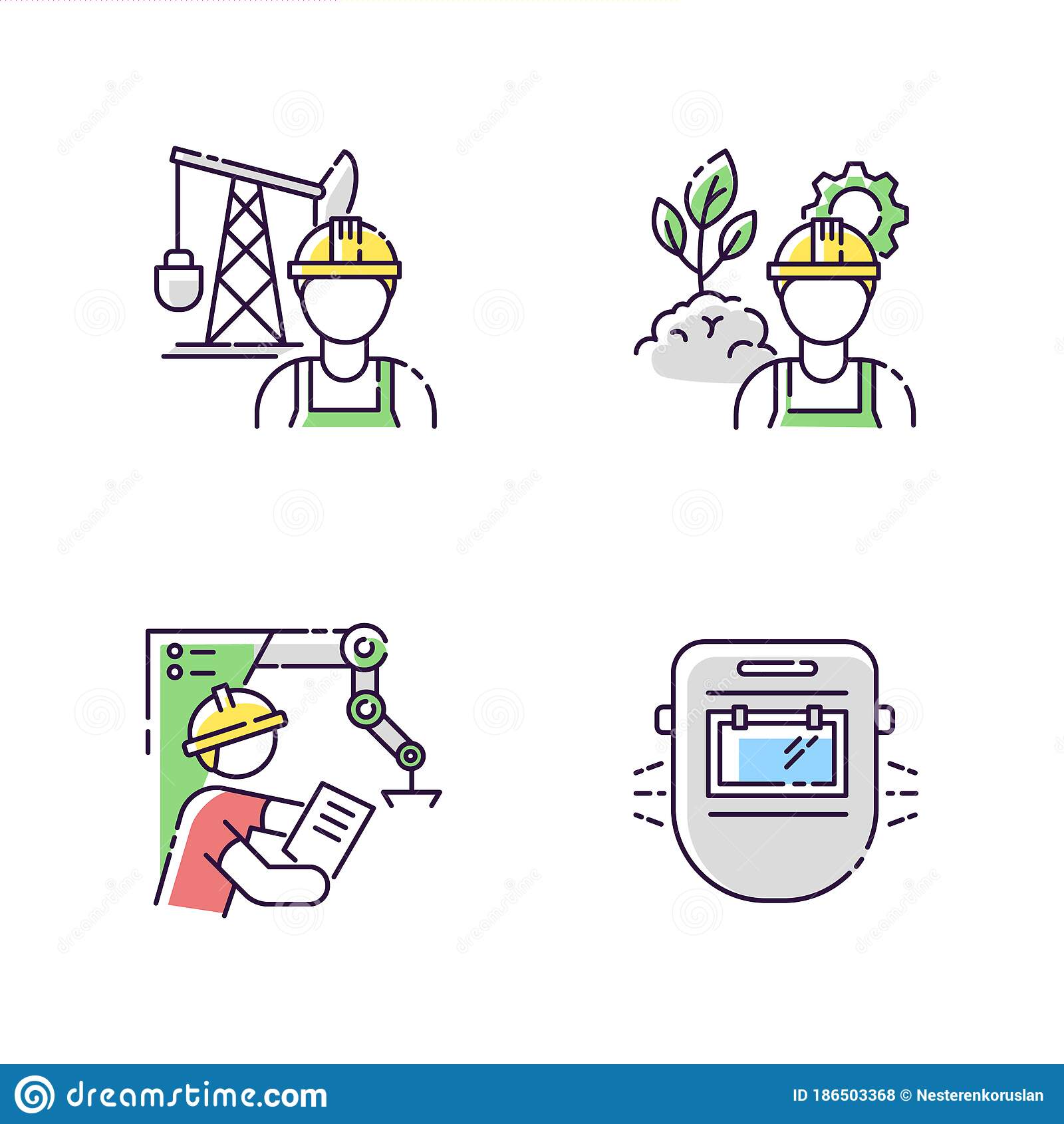
Civil engineers design and build infrastructure such a roads, railways, airports, bridges, harbours, dams, etc. They also manage and design water and sewerage systems and irrigation projects.
In order to become a civil engineer, you will need several skills as well as an unwavering commitment to your education. Students wishing to enter the civil engineering field are required to have a bachelor’s degree, either in civil or related fields such as construction and business administration. Around one-fifth hold a Master's Degree. This increases the chances that you will get a position as a junior engineer. Senior engineers may need a license from ABET.
Most entry-level jobs require a bachelor’s degree in civil or closely related disciplines, such as construction management. Most civil engineer degrees require four or five year to complete. Many schools offer programs that make it possible to earn a degree more affordable.
Graduates in civil engineering can hold a wide range of positions, including design engineer and project manager. They usually start in a graduate training scheme, where they work under an experienced professional to develop their skills. After gaining more experience, engineers can progress to full-time roles and eventually become lead engineers.
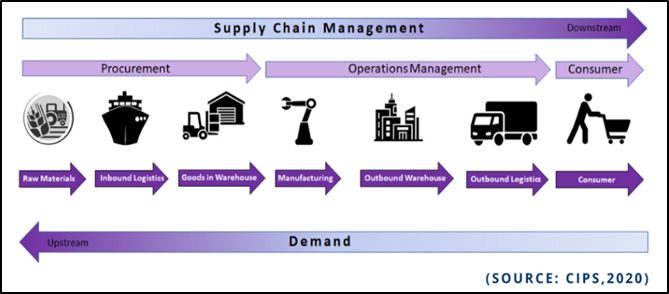
Civil engineers have a rewarding career that is both challenging and exciting. There are many opportunities for advancement. You'll find these careers in a wide range of industries, such as transportation, energy, manufacturing and building construction.
Employers prefer candidates who are creative, have a good sense of communication and can think critically. These skills will help you solve engineering problems and improve technical processes for your employer.
Leadership and teamwork skills are also important, as you often oversee the construction of your projects. You'll also need to have the ability to communicate with other team members or vendors in order to resolve any problems that may arise.
Staying current with trends and regulations is crucial for a career in civil engineering, as this profession evolves with the needs of industry. If you want to stay on top of the latest trends, consider joining a professional organisation or pursuing continuing education.
This job requires excellent decision-making skills. You'll need to make decisions on budgeting and safety concerns, balancing your own expertise with the advice of other professionals.
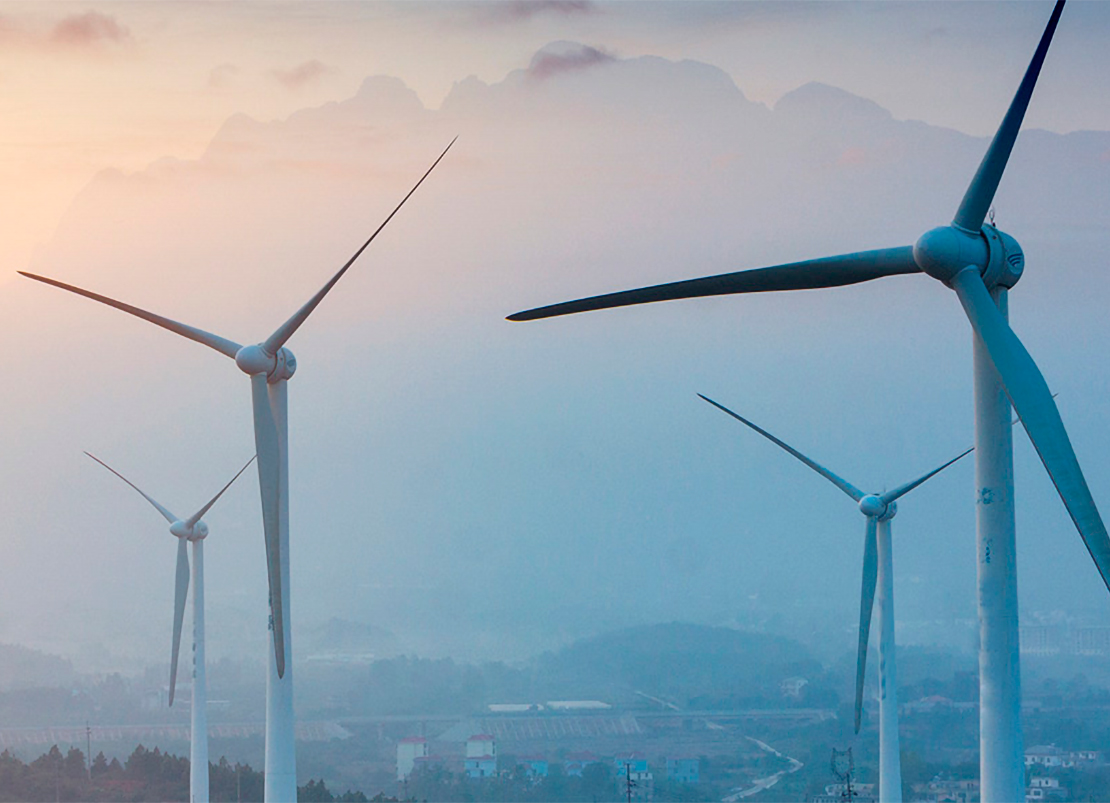
It is essential that you have the right education and training to be a successful civil engineer. You must also prove yourself on the job through completing projects, meeting deadlines and demonstrating your professionalism. Communication with clients, contractors and coworkers is essential.
This career will require a solid understanding of mathematics, physics and the ability think creatively. You'll also need to be able to analyze data and present your findings in an effective manner.
The salary for a civil engineer can vary widely, depending on the type of position and the state where you live. California, Texas and Florida pay the most for this career. Alaska, Rhode Island, and Wyoming are also states with high salaries for civil engineering.
FAQ
What does it mean to warehouse?
A warehouse or storage facility is where goods are stored before they are sold. It can be indoors or out. In some cases it could be both indoors and outdoors.
How does a production planner differ from a project manager?
The major difference between a Production Planner and a Project Manager is that a Project Manager is often the person responsible for organizing and planning the entire project. While a Production Planner is involved mainly in the planning stage,
What is the difference between manufacturing and logistics
Manufacturing refers to the process of making goods using raw materials and machines. Logistics includes all aspects related to supply chain management, such as procurement, distribution planning, inventory control and transportation. Logistics and manufacturing are often referred to as one thing. It encompasses both the creation of products and their delivery to customers.
Can we automate some parts of manufacturing?
Yes! Since ancient times, automation has been in existence. The Egyptians invented the wheel thousands of years ago. To help us build assembly lines, we now have robots.
Actually, robotics can be used in manufacturing for many purposes. These include:
-
Robots for assembly line
-
Robot welding
-
Robot painting
-
Robotics inspection
-
Robots that create products
Manufacturing could also benefit from automation in other ways. 3D printing, for example, allows us to create custom products without waiting for them to be made.
What are the 7 Rs of logistics management?
The acronym 7R's for Logistics stands to represent the seven basic principles in logistics management. It was developed by the International Association of Business Logisticians (IABL) and published in 2004 as part of its "Seven Principles of Logistics Management" series.
The following letters make up the acronym:
-
Responsible - to ensure that all actions are within the legal requirements and are not detrimental to others.
-
Reliable - have confidence in the ability to deliver on commitments made.
-
Reasonable - use resources efficiently and don't waste them.
-
Realistic - Consider all aspects of operations, including environmental impact and cost effectiveness.
-
Respectful - show respect and treat others fairly and fairly
-
Reliable - Find ways to save money and increase your productivity.
-
Recognizable provides value-added products and services to customers
What does it mean to be a manufacturer?
Manufacturing Industries is a group of businesses that produce goods for sale. Consumers are those who purchase these products. To accomplish this goal, these companies employ a range of processes including distribution, sales, management, and production. They produce goods from raw materials by using machines and other machinery. This includes all types and varieties of manufactured goods, such as food items, clothings, building supplies, furnitures, toys, electronics tools, machinery vehicles, pharmaceuticals medical devices, chemicals, among others.
What jobs are available in logistics?
There are many types of jobs in logistics. Some of them are:
-
Warehouse workers - They load trucks and pallets.
-
Transport drivers - These are people who drive trucks and trailers to transport goods or perform pick-ups.
-
Freight handlers: They sort and package freight in warehouses.
-
Inventory managers - They oversee the inventory of goods in warehouses.
-
Sales representatives - They sell products.
-
Logistics coordinators are responsible for organizing and planning logistics operations.
-
Purchasing agents - They purchase goods and services needed for company operations.
-
Customer service representatives - Answer calls and email from customers.
-
Shipping clerks - They process shipping orders and issue bills.
-
Order fillers - They fill orders based on what is ordered and shipped.
-
Quality control inspectors are responsible for inspecting incoming and outgoing products looking for defects.
-
Other - Logistics has many other job opportunities, including transportation supervisors, logistics specialists, and cargo specialists.
Statistics
- Job #1 is delivering the ordered product according to specifications: color, size, brand, and quantity. (netsuite.com)
- (2:04) MTO is a production technique wherein products are customized according to customer specifications, and production only starts after an order is received. (oracle.com)
- You can multiply the result by 100 to get the total percent of monthly overhead. (investopedia.com)
- Many factories witnessed a 30% increase in output due to the shift to electric motors. (en.wikipedia.org)
- According to a Statista study, U.S. businesses spent $1.63 trillion on logistics in 2019, moving goods from origin to end user through various supply chain network segments. (netsuite.com)
External Links
How To
Six Sigma and Manufacturing
Six Sigma is "the application statistical process control (SPC), techniques for continuous improvement." Motorola's Quality Improvement Department created Six Sigma at their Tokyo plant, Japan in 1986. The basic idea behind Six Sigma is to improve quality by improving processes through standardization and eliminating defects. This method has been adopted by many companies in recent years as they believe there are no perfect products or services. Six Sigma's main objective is to reduce variations from the production average. You can calculate the percentage of deviation from the norm by taking a sample of your product and comparing it to the average. If the deviation is excessive, it's likely that something needs to be fixed.
Understanding how your business' variability is a key step towards Six Sigma implementation is the first. Once you've understood that, you'll want to identify sources of variation. Also, you will need to identify the sources of variation. Random variations occur when people do mistakes. Symmetrical variations are caused due to factors beyond the process. For example, if you're making widgets, and some of them fall off the assembly line, those would be considered random variations. If however, you notice that each time you assemble a widget it falls apart in exactly the same spot, that is a problem.
Once you've identified the problem areas you need to find solutions. This could mean changing your approach or redesigning the entire process. After implementing the new changes, you should test them again to see if they worked. If they didn't work, then you'll need to go back to the drawing board and come up with another plan.