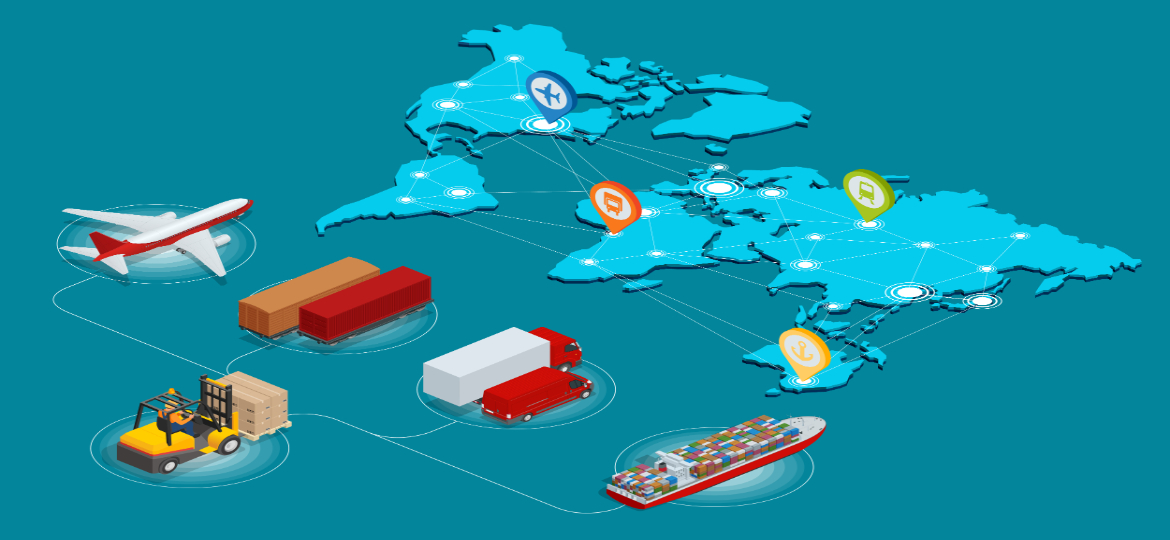
The US's manufacturing sector is a major part of its economy. The sector drives about eleven percent of the nation's total economic output. It accounts for 18.2 percentage of all world goods, and is also a significant contributor to the country's overall economic output. However, in recent decades, manufacturing's growth has been slowing.
Since 2000 the US has lost nearly a third of its manufacturing jobs. According to the Bureau of Labor Statistics in (BLS), manufacturing productivity has increased by 4.5% annually between 1995 and 2000. While manufacturing was once seen as a declining job generator, automation and other technological advances have spurred a reexamination of how technology is impacting employment.
Walmart pledged to support American jobs in January 2013. Walmart has committed to buying $250 billion in American products over the next ten-year period. Walmart can now support additional U.S. manufacturing, and encourages diverse companies to explore potential opportunities with the giant retailer.
Although the United States has emerged as a leader in the global market, the country has not been without its challenges. Some of these issues are due to the high cost and rising rate of labor overseas, as well as a high corporate tax rate and a dearth of skilled trade negotiators. These problems could be a hindrance to the sector's future.
There is also a skills shortage in the US. An estimated 1.4million workers are currently in need of more training. Trump's policies are aimed at expanding apprenticeship programs and training, but there have been concerns about the quality.
Despite the difficulties, the US' manufacturing sector has been able to rebound from the Great Recession. In the first quarter 2018, manufacturing output hit a record $2.00 trillion. This was higher than the $1.95 Trillion that was achieved in the year preceding the recession.
The US manufacturing industry has been growing at a slower rate that the overall economy. However, growth is expected in the coming years. The sector's growth is expected to be 2.4 percent in 2020, and 1.9% by 2021.
The manufacturing sector will benefit from increased exports. The industry has also seen a reduction in energy costs due to shale oil. Furthermore, the United States has a competitive corporate tax rate, which is higher than most countries in the world.
Meanwhile, China, Japan, and South Korea are experiencing manufacturing contraction. This is the first occasion that the S&P Global purchasing mangers index has fallen below 50 in these two countries in nearly two decades.
Trump is believed to be working with the federal government on a simpler program to help the manufacturing sector. One of the most important federal programs is the Manufacturing Extension Partnership (MEP). MEPs can generate $21 in client investment for every $21 invested by the federal government. The MEP also has centers in all 50 states as well as Canada, Mexico, and Europe.
The US is far less successful in trade negotiations than other industrial nations. Because of this, the US government is unable to negotiate bilateral trade deals with other countries. This means that the US faces difficulties in attracting and retaining more manufacturers.
FAQ
What does warehouse refer to?
A warehouse, or storage facility, is where goods are stored prior to being sold. It can be an outdoor or indoor area. In some cases, it may be a combination of both.
What is the responsibility of a logistics manager?
Logistics managers ensure that goods arrive on time and are unharmed. This is done through his/her expertise and knowledge about the company's product range. He/she also needs to ensure adequate stock to meet demand.
Why is logistics important in manufacturing
Logistics are an integral part any business. Logistics can help you achieve amazing results by helping to manage product flow from raw materials to finished products.
Logistics play an important role in reducing costs as well as increasing efficiency.
What is the difference between a production planner and a project manager?
The main difference between a production planner and a project manager is that a project manager is usually the person who plans and organizes the entire project, whereas a production planner is mainly involved in the planning stage of the project.
What is the role of a manager in manufacturing?
A manufacturing manager must ensure that all manufacturing processes are efficient and effective. They must also be alert to any potential problems and take appropriate action.
They should also be able communicate with other departments, such as sales or marketing.
They should also be knowledgeable about the latest trends in the industry so they can use this information for productivity and efficiency improvements.
Statistics
- It's estimated that 10.8% of the U.S. GDP in 2020 was contributed to manufacturing. (investopedia.com)
- In 2021, an estimated 12.1 million Americans work in the manufacturing sector.6 (investopedia.com)
- [54][55] These are the top 50 countries by the total value of manufacturing output in US dollars for its noted year according to World Bank.[56] (en.wikipedia.org)
- According to a Statista study, U.S. businesses spent $1.63 trillion on logistics in 2019, moving goods from origin to end user through various supply chain network segments. (netsuite.com)
- According to the United Nations Industrial Development Organization (UNIDO), China is the top manufacturer worldwide by 2019 output, producing 28.7% of the total global manufacturing output, followed by the United States, Japan, Germany, and India.[52][53] (en.wikipedia.org)
External Links
How To
How to Use Six Sigma in Manufacturing
Six Sigma is defined by "the application SPC (statistical process control) techniques to achieve continuous improvements." It was developed by Motorola's Quality Improvement Department at their plant in Tokyo, Japan, in 1986. The basic idea behind Six Sigma is to improve quality by improving processes through standardization and eliminating defects. In recent years, many companies have adopted this method because they believe there is no such thing as perfect products or services. Six Sigma's main objective is to reduce variations from the production average. This means that if you take a sample of your product, then measure its performance against the average, you can find out what percentage of the time the process deviates from the norm. If there is a significant deviation from the norm, you will know that something needs to change.
Understanding how your business' variability is a key step towards Six Sigma implementation is the first. Once you have this understanding, you will need to identify sources and causes of variation. These variations can also be classified as random or systematic. Random variations occur when people do mistakes. Symmetrical variations are caused due to factors beyond the process. These are, for instance, random variations that occur when widgets are made and some fall off the production line. You might notice that your widgets always fall apart at the same place every time you put them together.
Once you identify the problem areas, it is time to create solutions. It might mean changing the way you do business or redesigning it entirely. Once you have implemented the changes, it is important to test them again to ensure they work. If they didn't work, then you'll need to go back to the drawing board and come up with another plan.