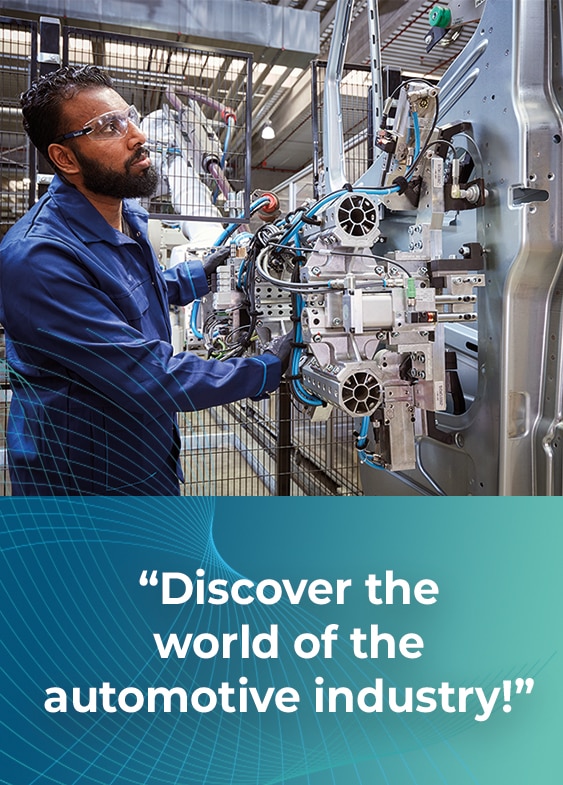
Historically, the demand of consumers has driven manufacturing. But this is changing. Technology is also changing manufacturing. This is partly due in part to advancements in predictive analysis, which allows manufacturers to move production closer toward consumers. Despite this, manufacturing still faces risks, including supply and demand. If they fail to meet the demands of consumers, manufacturers could lose customers. They could also lose customers if they produce excessively. To preserve their brand image manufacturers must comply with quality control standards.
Although there are many manufacturing processes available, they all share the same characteristics. There are three main types of manufacturing processes: repetitive manufacturing, batch manufacture, and processing manufacturing. These processes can be used on large scales to allow manufacturers to make products in bulk.
Repetitive production is where dedicated production lines produce identical or similar products year-round. Repetitive Manufacturing production lines do not require any setup or changeover. This makes it ideal for production runs that require little capital investment. They are also able to run 24-hours a day.
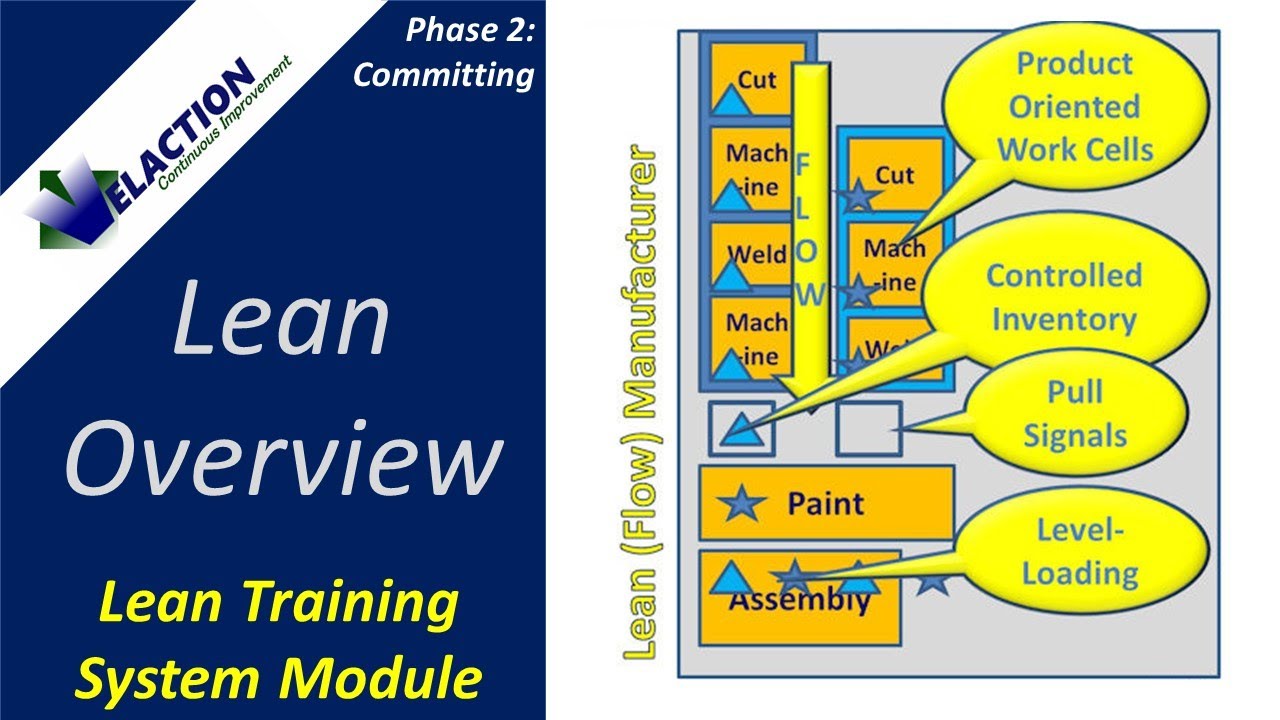
Batch manufacturing is similar to repetitive manufacturing, but it works in small, discrete batches. It is generally faster and requires less automation. It is not suitable for every type of production. This is a great option for products that have to be changed frequently. You can also use it to create custom products. It can be used to make goods out of materials that are not easily broken down.
Discrete manufacturing is the other side of process manufacturing. It involves using a bill and instructions to make finished goods. It can include items such as automobiles and toys. It can also involve the use of software and computers. Process manufacturing is different because it requires less interruptions and better quality control.
The most common process for mass manufacturing of plastic parts is injection molding. This involves melting small plastic pellets and injecting them into a mold. The molding is then cooled and mechanically ejected. The mold is then heated and rotated in order to obtain a uniform coating. This process can be used for making a variety of products, such as pipes or straws.
Atomic manufacturing is a third type of manufacturing process. This process is also called "bottom up" manufacturing. In this method, components interact spontaneously. It is also possible to produce products from biological materials in this manner. You can add parts manually or automatically in certain cases.
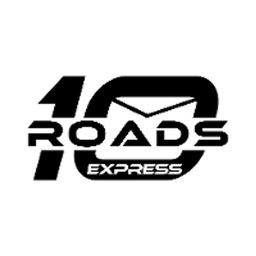
Another form of process manufacturing is intermittent manufacturing. This manufacturing method creates many identical items simultaneously and is particularly effective for small production runs. It is however difficult to customize and is not appropriate for all products.
Processing also allows for the production of products that cannot be separated, such as ceramics. Process manufacturing has the advantage of being able to produce many products while still maintaining high production quality. Also, there are fewer interruptions and a lower defect incidence in process manufacturing.
FAQ
Is automation important for manufacturing?
Automating is not just important for manufacturers, but also for service providers. It enables them to provide services faster and more efficiently. It reduces human errors and improves productivity, which in turn helps them lower their costs.
What is the difference between manufacturing and logistics
Manufacturing is the act of producing goods from raw materials using machines and processes. Logistics is the management of all aspects of supply chain activities, including procurement, production planning, distribution, warehousing, inventory control, transportation, and customer service. Manufacturing and logistics can often be grouped together to describe a larger term that covers both the creation of products, and the delivery of them to customers.
What's the difference between Production Planning & Scheduling?
Production Planning (PP) is the process of determining what needs to be produced at any given point in time. This can be done by forecasting demand and identifying production capabilities.
Scheduling is the process that assigns dates to tasks so they can get completed within a given timeframe.
What skills are required to be a production manager?
Being a production planner is not easy. You need to be organized and flexible. Communication skills are essential to ensure that you can communicate effectively with clients, colleagues, and customers.
How can I learn about manufacturing?
Hands-on experience is the best way to learn more about manufacturing. If that is not possible, you could always read books or view educational videos.
Statistics
- Job #1 is delivering the ordered product according to specifications: color, size, brand, and quantity. (netsuite.com)
- You can multiply the result by 100 to get the total percent of monthly overhead. (investopedia.com)
- In 2021, an estimated 12.1 million Americans work in the manufacturing sector.6 (investopedia.com)
- In the United States, for example, manufacturing makes up 15% of the economic output. (twi-global.com)
- [54][55] These are the top 50 countries by the total value of manufacturing output in US dollars for its noted year according to World Bank.[56] (en.wikipedia.org)
External Links
How To
How to Use Lean Manufacturing for the Production of Goods
Lean manufacturing is an approach to management that aims for efficiency and waste reduction. It was developed in Japan during the 1970s and 1980s by Taiichi Ohno, who received the Toyota Production System (TPS) award from TPS founder Kanji Toyoda. Michael L. Watkins published the original book on lean manufacturing, "The Machine That Changed the World," in 1990.
Lean manufacturing is often defined as a set of principles used to improve the quality, speed, and cost of products and services. It emphasizes the elimination and minimization of waste in the value stream. Lean manufacturing is called just-in-time (JIT), zero defect, total productive maintenance (TPM), or 5S. Lean manufacturing focuses on eliminating non-value-added activities such as rework, inspection, and waiting.
Lean manufacturing improves product quality and costs. It also helps companies reach their goals quicker and decreases employee turnover. Lean manufacturing has been deemed one of the best ways to manage the entire value-chain, including customers, distributors as well retailers and employees. Lean manufacturing practices are widespread in many industries. For example, Toyota's philosophy underpins its success in automobiles, electronics, appliances, healthcare, chemical engineering, aerospace, paper, food, etc.
Lean manufacturing includes five basic principles:
-
Define Value- Identify the added value your company brings to society. What makes you stand out from your competitors?
-
Reduce waste - Get rid of any activity that does not add value to the supply chain.
-
Create Flow - Make sure work runs smoothly without interruptions.
-
Standardize & simplify - Make processes consistent and repeatable.
-
Building Relationships – Establish personal relationships with both external and internal stakeholders.
Lean manufacturing is not a new concept, but it has been gaining popularity over the last few years due to a renewed interest in the economy following the global financial crisis of 2008. Many businesses have adopted lean manufacturing techniques to help them become more competitive. Many economists believe lean manufacturing will play a major role in economic recovery.
Lean manufacturing has many benefits in the automotive sector. These include higher customer satisfaction, lower inventory levels, lower operating expenses, greater productivity, and improved overall safety.
The principles of lean manufacturing can be applied in almost any area of an organization. Lean manufacturing is most useful in the production sector of an organisation because it ensures that each step in the value-chain is efficient and productive.
There are three main types of lean manufacturing:
-
Just-in Time Manufacturing (JIT), also known as "pull system": This form of lean manufacturing is often referred to simply as "pull". JIT is a method in which components are assembled right at the moment of use, rather than being manufactured ahead of time. This approach aims to reduce lead times, increase the availability of parts, and reduce inventory.
-
Zero Defects Manufacturing: ZDM ensures that no defective units leave the manufacturing plant. If a part needs to be fixed during the assembly line, it should be repaired rather than scrapped. This is also true for finished products that require minor repairs before shipping.
-
Continuous Improvement: Continuous Improvement aims to improve efficiency by continually identifying problems and making adjustments to eliminate or minimize waste. Continuous improvement refers to continuous improvement of processes as well people and tools.