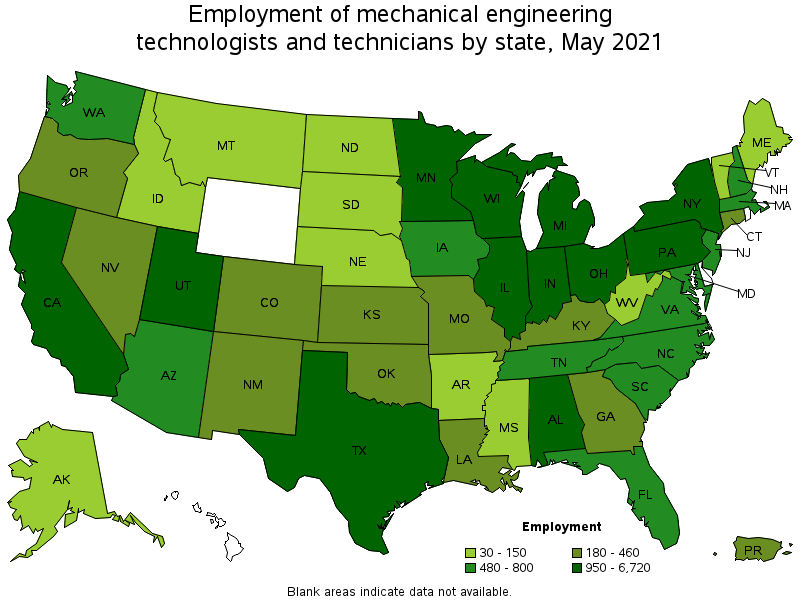
If you're looking to a career with chemistry, you might be curious as to what a salary for a chemical chemist. Below you can find an average chemist salary and an explanation of how much the various degrees can earn. A bachelor's degree is in chemistry and can bring you between $50,000 and over 100 thousand dollars. Your location, degree earned, and employer will determine how much you make each year.
Average chemist salary
According to the Bureau of Labor Statistics the average starting salary in chemistry is $81,870 per annum. The highest-paid chemical professionals earn more than $130,000 annually. The bottom-paid chemists earn around $42,960 per year. Pharmacist and medicine manufacturing companies are the most common places for chemists. The oil and gas industry offers the highest starting chemistry salary. The Bureau of Labor Statistics predicts a 7 percent increase in chemist jobs over the next decade. Graduates with laboratory experience are more likely to get better jobs than those without.
The average chemistry salary depends on the area and the amount of experience you have. The salary of a chemist can go up or down depending on experience, education and additional skills. A California-based chemist who is experienced can earn an annual salary of $85,114. In other states, however, salaries are more varied. A PhD is a great way to increase your income if you are a chemist.
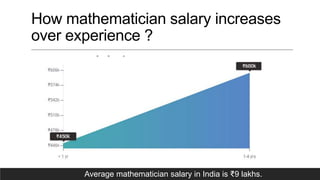
Salary range for chemists with bachelor's degree
A chemistry degree can help you find a job in many different industries. According to the Bureau of Labor Statistics, there were around 82,000 chemists in the United States in 2010. Though a bachelor's degree is usually enough to secure a chemistry-related job, a graduate degree can lead to higher income and more responsibility. According to the American Chemical Society in 2011, a chemist earned $40,000, while the starting salary for an Ph.D. is approximately $85,000.
Chemistry-related careers can be highly lucrative. However, the salary is only one factor. A Ph.D. (in chemistry) can pay upwards to $60,000 depending on experience and job type. As a general rule, the highest-paid chemists work in the federal government, research at universities, and teaching.
The salary range for chemists who have a master's degree
A chemistry master’s degree can make a person earn as much as 128,000 USD each year. Salary ranges differ greatly for this profession, though they are often close to the median. For a graduate with less than two years of work experience, you can expect to make around 40 thousand euros. An experienced chemist may earn as high as 239,000 USD annually if he or she has more than ten year of experience.
A master's or Ph.D. is required for many chemistry jobs. However, a bachelor's degree can be used. Graduates can specialize in a particular subfield. According to American Chemical Society, the median starting wage for a chemist with an undergraduate degree was $43,000. For those who worked in companies with over 25,000 employees, the salary was $50,000.
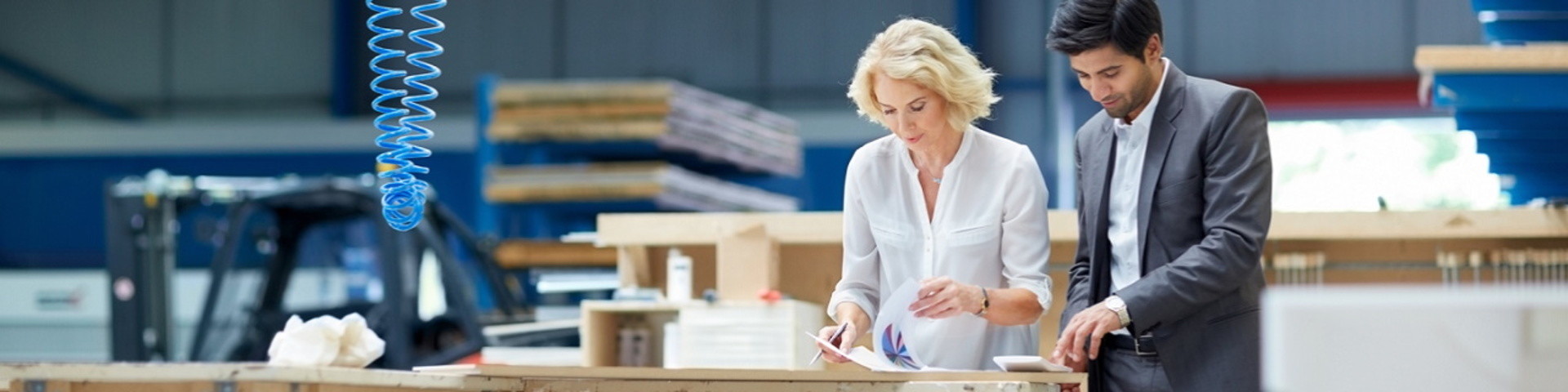
For chemists with Ph.D., the salary range is as follows:
A PhD chemist's pay will be determined by his/her work history, where and for what purpose. For example, in Germany salaries for scientists can be as high as 40,400 euros annually in small businesses. For large companies, salaries may reach as high as 50,000 Euros. Scientists will generally be paid according the collective wage agreements that are in place within the company.
The U.S. has a lot of chemists, and they make a great living. However, they also have responsibilities in education or research. University professors typically work on government-funded and private-industry-funded projects. This field is also available for secondary school teachers. According to the American Chemical Society, a chemist with a bachelor's degree earns approximately $40,000 per year, while a chemist with a master's degree earns about $46,000 per year. A Ph.D. with chemistry earned a median salary in 2011 of $85,000
FAQ
How can manufacturing overproduction be reduced?
The key to reducing overproduction lies in developing better ways to manage inventory. This would reduce the time spent on unproductive activities like purchasing, storing and maintaining excess stock. This would allow us to use our resources for more productive tasks.
A Kanban system is one way to achieve this. A Kanban Board is a visual display that tracks work progress. Work items are moved through various states to reach their destination in a Kanban system. Each state is assigned a different priority.
If work is moving from one stage to the other, then the current task can be completed and moved on to the next. If a task is still in its beginning stages, it will continue to be so until it reaches the end.
This allows work to move forward and ensures that no work is missed. Managers can see how much work has been done and the status of each task at any time with a Kanban Board. This allows them to adjust their workflows based on real-time information.
Lean manufacturing can also be used to reduce inventory levels. Lean manufacturing seeks to eliminate waste from every step of the production cycle. Waste includes anything that does not add value to the product. Here are some examples of common types.
-
Overproduction
-
Inventory
-
Packaging not required
-
Excess materials
These ideas will help manufacturers increase efficiency and lower costs.
What are the four types of manufacturing?
Manufacturing refers the process of turning raw materials into useful products with machines and processes. It can involve many activities like designing, manufacturing, testing packaging, shipping, selling and servicing.
What are the 7 Rs of logistics?
The 7R's of Logistics is an acronym for the seven basic principles of logistics management. It was published in 2004 by the International Association of Business Logisticians as part of their "Seven Principles of Logistics Management" series.
The acronym is composed of the following letters.
-
Responsible - ensure that actions are in compliance with legal requirements and do not cause harm to others.
-
Reliable - have confidence in the ability to deliver on commitments made.
-
Use resources effectively and sparingly.
-
Realistic – Consider all aspects, including cost-effectiveness as well as environmental impact.
-
Respectful - show respect and treat others fairly and fairly
-
You are resourceful and look for ways to save money while increasing productivity.
-
Recognizable: Provide customers with value-added service
What are the jobs in logistics?
There are many kinds of jobs available within logistics. Here are some examples:
-
Warehouse workers: They load and unload trucks, pallets, and other cargo.
-
Transportation drivers – These drivers drive trucks and wagons to transport goods and pick up the goods.
-
Freight handlers - They sort and pack freight in warehouses.
-
Inventory managers - They oversee the inventory of goods in warehouses.
-
Sales representatives - They sell products to customers.
-
Logistics coordinators - They organize and plan logistics operations.
-
Purchasing agents – They buy goods or services necessary to run a company.
-
Customer service representatives - Answer calls and email from customers.
-
Shippers clerks - They process shipping order and issue bills.
-
Order fillers - They fill orders based on what is ordered and shipped.
-
Quality control inspectors: They inspect outgoing and incoming products for any defects.
-
Others – There are many other types available in logistics. They include transport supervisors, cargo specialists and others.
What is the difference between a production planner and a project manager?
The difference between a product planner and project manager is that a planer is typically the one who organizes and plans the entire project. A production planner, however, is mostly involved in the planning stages.
What is the role of a logistics manager
A logistics manager makes sure that all goods are delivered on-time and in good condition. This is accomplished by using the experience and knowledge gained from working with company products. He/she also needs to ensure adequate stock to meet demand.
Statistics
- According to the United Nations Industrial Development Organization (UNIDO), China is the top manufacturer worldwide by 2019 output, producing 28.7% of the total global manufacturing output, followed by the United States, Japan, Germany, and India.[52][53] (en.wikipedia.org)
- Many factories witnessed a 30% increase in output due to the shift to electric motors. (en.wikipedia.org)
- Job #1 is delivering the ordered product according to specifications: color, size, brand, and quantity. (netsuite.com)
- In 2021, an estimated 12.1 million Americans work in the manufacturing sector.6 (investopedia.com)
- In the United States, for example, manufacturing makes up 15% of the economic output. (twi-global.com)
External Links
How To
How to use 5S to increase Productivity in Manufacturing
5S stands for "Sort", 'Set In Order", 'Standardize', & Separate>. Toyota Motor Corporation developed the 5S method in 1954. It allows companies to improve their work environment, thereby achieving greater efficiency.
This method aims to standardize production processes so that they are repeatable, measurable and predictable. This means that tasks such as cleaning, sorting, storing, packing, and labeling are performed daily. Because workers know what they can expect, this helps them perform their jobs more efficiently.
Implementing 5S requires five steps. These are Sort, Set In Order, Standardize. Separate. And Store. Each step requires a different action to increase efficiency. If you sort items, it makes them easier to find later. Once you have placed items in an ordered fashion, you will put them together. Then, after you separate your inventory into groups, you store those groups in containers that are easy to access. Labeling your containers will ensure that everything is correctly labeled.
Employees need to reflect on how they do their jobs. Employees need to be able understand their motivations and discover alternative ways to do them. They will need to develop new skills and techniques in order for the 5S system to be implemented.
The 5S method increases efficiency and morale among employees. They feel more motivated to work towards achieving greater efficiency as they see the results.