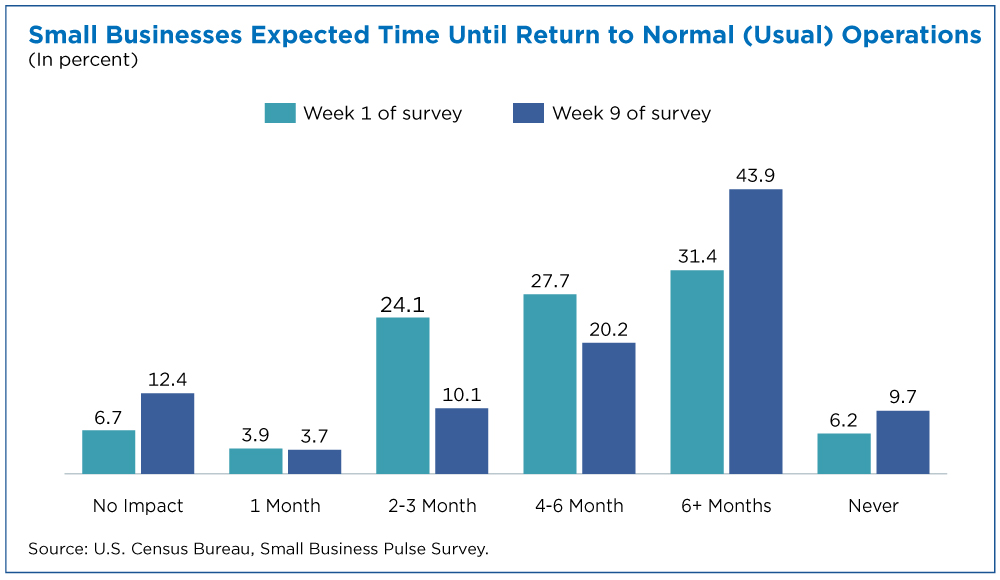
SIPOC Diagram is a visual aid that can be used to identify the inputs as well as outputs in a process. It also allows team members to identify gaps or improvements in business operations.
The sipoc chart is frequently used in conjunction with the DMAIC (Dynamic Management and Improvement Cycle), which is a process improvement framework designed to help create business processes that can be continuously improved through analysis. It helps teams and sponsor agree on project boundaries and the scope of a project, along with Key Process Input Variables and Key Process Output Variables.
What Is SIPOC?
SIPOC is a visually simple representation of the inputs to a process. Its primary function is to aid the team to understand and analyze the process from a high level. It provides a clear picture on the steps necessary to transform the inputs into the desired outputs.
What is its history?
The sipoc diagram dates back to the 1980s as part of a total quality management approach (TQM), and the Six Sigma model for business process improvement. The sipoc diagram has been used in lean production and business improvement programs for many years. It's a great tool to streamline processes, identify potential improvements and improve communication between stakeholders.
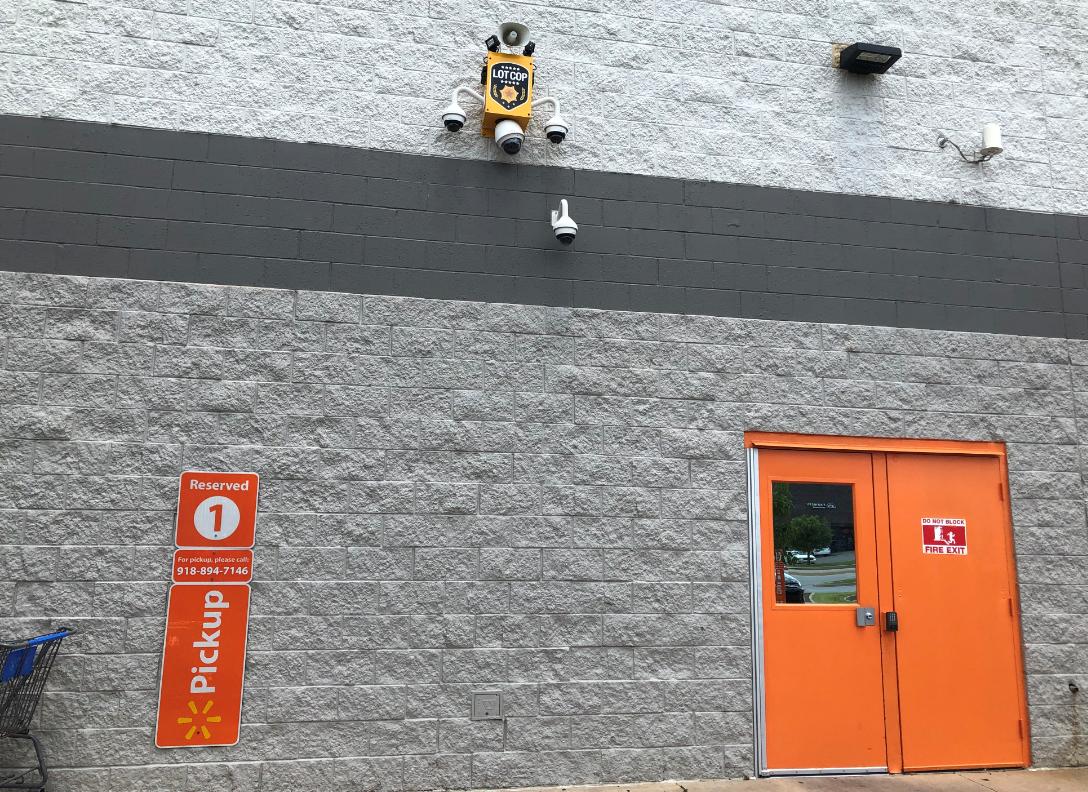
How to Make SIPOCs
The first step to creating a SIPOC is to select the business processes you wish to analyse. This will help you and your team to focus on the most important areas and ensure that no important details are overlooked.
You will then need to identify what inputs you require to make your process run and who is providing them. List all the suppliers and their contact info, as well as the raw materials each one provides to the process.
List the clients who receive the products and services, both internal and external. This can ensure that the business is providing products and services of high quality.
Inputs - This is the top section of a SIPOC Diagram and contains the information or materials specifications that are needed by the process. Material can be a physical good, like a product, but it can also be information, like a report.
Outputs - This is the next section of the SIPOC diagram. It's usually a listing of the products, completed actions, or services that result from the process. The outputs must reflect the value customers expect from the processes, and they must respond to the needs of the customer.
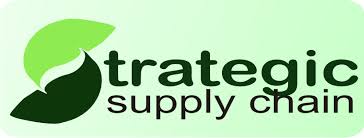
Customers: This section is the last of a SIPOC Diagram and it identifies all the clients who will receive the outputs from the process, internal or external to the organisation. The maintenance team, the line operators, as well as other internal clients and external customers can be included.
SIPOC is a powerful, visual tool which can be used to improve the communication between stakeholders and improve business processes. Easy to create, it's a great tool to help your team understand the processes you are examining. It's best to use templates that include all key diagram components such as inputs or outputs. You can save both time and energy by using a template.
FAQ
How can manufacturing efficiency improved?
First, we need to identify which factors are most critical in affecting production times. We must then find ways that we can improve these factors. If you don’t know where to begin, consider which factors have the largest impact on production times. Once you have identified the factors, then try to find solutions.
What is the job of a manufacturer manager?
The manufacturing manager should ensure that every manufacturing process is efficient and effective. They should be alert for any potential problems in the company and react accordingly.
They should also learn how to communicate effectively with other departments, including sales and marketing.
They should also be aware of the latest trends in their industry and be able to use this information to help improve productivity and efficiency.
What does warehouse mean?
Warehouses and storage facilities are where goods are kept before being sold. It can be indoors or out. In some cases, it may be a combination of both.
What makes a production planner different from a project manger?
The main difference between a production planner and a project manager is that a project manager is usually the person who plans and organizes the entire project, whereas a production planner is mainly involved in the planning stage of the project.
What are the 4 types of manufacturing?
Manufacturing refers to the transformation of raw materials into useful products by using machines and processes. It includes many different activities like designing, building and testing, packaging, shipping and selling, as well as servicing.
What is the responsibility of a logistics manager?
Logistics managers ensure that goods arrive on time and are unharmed. This is achieved by using their knowledge and experience with the products of the company. He/she also needs to ensure adequate stock to meet demand.
How can manufacturing excess production be decreased?
The key to reducing overproduction lies in developing better ways to manage inventory. This would reduce the time needed to manage inventory. By doing this, we could free up resources for other productive tasks.
You can do this by adopting a Kanban method. A Kanban board is a visual display used to track work in progress. Work items are moved through various states to reach their destination in a Kanban system. Each state represents a different priority level.
When work is completed, it can be transferred to the next stage. But if a task remains in the beginning stages it will stay that way until it reaches its end.
This allows work to move forward and ensures that no work is missed. A Kanban board allows managers to monitor how much work is being completed at any given moment. This information allows managers to adjust their workflow based off real-time data.
Lean manufacturing, another method to control inventory levels, is also an option. Lean manufacturing seeks to eliminate waste from every step of the production cycle. Anything that doesn't add value to the product is considered waste. There are several types of waste that you might encounter:
-
Overproduction
-
Inventory
-
Packaging not required
-
Overstock materials
These ideas can help manufacturers improve efficiency and reduce costs.
Statistics
- You can multiply the result by 100 to get the total percent of monthly overhead. (investopedia.com)
- [54][55] These are the top 50 countries by the total value of manufacturing output in US dollars for its noted year according to World Bank.[56] (en.wikipedia.org)
- It's estimated that 10.8% of the U.S. GDP in 2020 was contributed to manufacturing. (investopedia.com)
- Job #1 is delivering the ordered product according to specifications: color, size, brand, and quantity. (netsuite.com)
- (2:04) MTO is a production technique wherein products are customized according to customer specifications, and production only starts after an order is received. (oracle.com)
External Links
How To
How to Use the Just-In-Time Method in Production
Just-in-time (JIT) is a method that is used to reduce costs and maximize efficiency in business processes. It's the process of obtaining the right amount and timing of resources when you need them. This means that your only pay for the resources you actually use. Frederick Taylor first coined this term while working in the early 1900s as a foreman. He saw how overtime was paid to workers for work that was delayed. He decided that workers would be more productive if they had enough time to complete their work before they started to work.
JIT is an acronym that means you need to plan ahead so you don’t waste your money. The entire project should be looked at from start to finish. You need to ensure you have enough resources to tackle any issues that might arise. You can anticipate problems and have enough equipment and people available to fix them. This will prevent you from spending extra money on unnecessary things.
There are several types of JIT techniques:
-
Demand-driven: This JIT is where you place regular orders for the parts/materials that are needed for your project. This will let you track the amount of material left over after you've used it. This will let you know how long it will be to produce more.
-
Inventory-based : You can stock the materials you need in advance. This allows for you to anticipate how much you can sell.
-
Project-driven: This is an approach where you set aside enough funds to cover the cost of your project. You will be able to purchase the right amount of materials if you know what you need.
-
Resource-based JIT: This type of JIT is most commonly used. You allocate resources based on the demand. You will, for example, assign more staff to deal with large orders. If you don't have many orders, you'll assign fewer people to handle the workload.
-
Cost-based: This approach is very similar to resource-based. However, you don't just care about the number of people you have; you also need to consider how much each person will cost.
-
Price-based: This is a variant of cost-based. However, instead of focusing on the individual workers' costs, this looks at the total price of the company.
-
Material-based: This is quite similar to cost-based, but instead of looking at the total cost of the company, you're concerned with how much raw materials you spend on average.
-
Time-based: This is another variation of resource-based JIT. Instead of worrying about how much each worker costs, you can focus on how long the project takes.
-
Quality-based JIT is another variant of resource-based JIT. Instead of focusing on the cost of each worker or how long it takes, think about how high quality your product is.
-
Value-based JIT is the newest form of JIT. You don't worry about whether the products work or if they meet customer expectations. Instead, you're focused on how much value you add to the market.
-
Stock-based: This stock-based method focuses on the actual quantity of products being made at any given time. It's used when you want to maximize production while minimizing inventory.
-
Just-in time (JIT), planning: This is a combination JIT/supply chain management. It refers to the process of scheduling the delivery of components as soon as they are ordered. This is important as it reduces lead time and increases throughput.