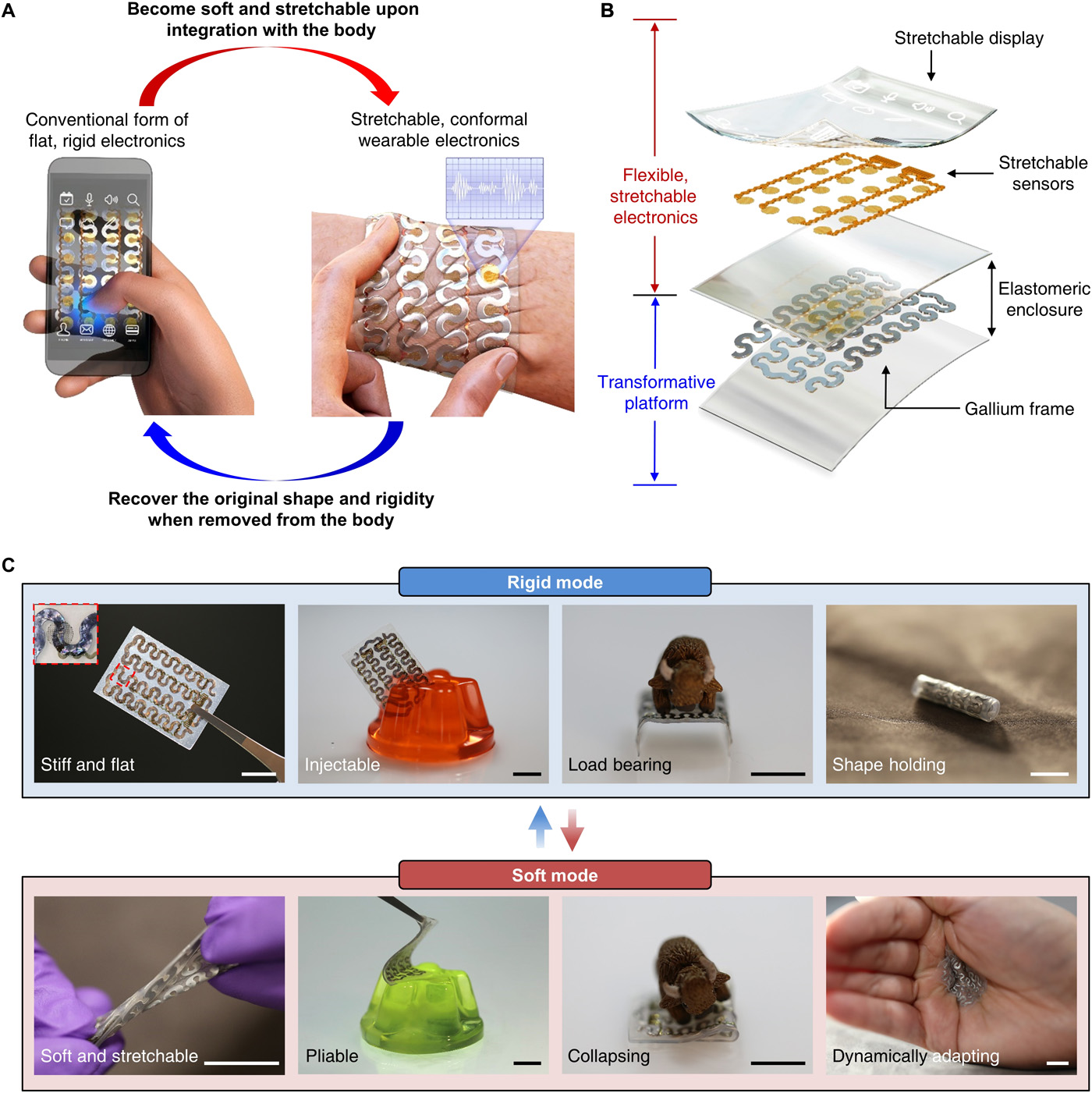
Manufacturing engineers have been highly in demand since the advent of the industrial revolution. They are responsible in designing manufacturing processes that increase productivity. Manufacturing engineers need to have a commercial awareness in addition to technical skills. A solid knowledge base in mathematics and science is essential. In addition to that, they should have leadership skills.
A manufacturing engineer's salary will vary depending on his education, skills and experience. They can make anywhere from $70,960 to $120,000 per year in the United States. They can pursue a master's degree if they want to advance their career. A master's degree can help them earn a better income. A master's program can help them improve their skills and learn new technologies.
A PhD is also possible to make a contribution as a researcher. They are also eligible to work for both the central and local governments. They may also work as consultants. They might work in different areas.
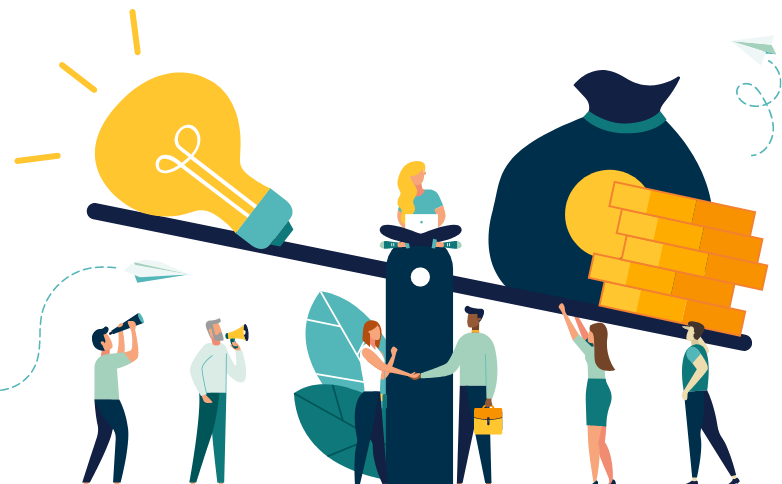
Manufacturing engineers have a tendency to earn more as they gain experience. As they gain more experience, they can be promoted to managerial positions. They will have the ability to implement automation systems and design manufacturing processes. They will be responsible for the day-today operation of the factory. They might be required to work evenings and weekends.
Apprentices and interns are the most common way to start your career as a manufacturing engineer. They can work across a range of manufacturing fields such as aerospace engineering and food manufacturing. They can also work in industrial or commercial design. After a few years, they may be eligible to become consultants. This position will allow them to manage the factory floor as well as guide engineers. They will also be responsible maintaining company best practices. They will also be expected to identify and resolve any errors in the manufacturing process.
Manufacturing engineers have to keep up with the latest manufacturing trends and technologies. They need to be able deal with any issues in a fast-paced setting and work under pressure. They will also need to be good at leadership and IT. They will get a regular salary during their first few year of employment. They can earn a slightly higher salary after they have been in the industry for a few years.
The average salary for manufacturing engineers is between $28,500-126,000 per annum. This range includes bonuses as well as taxable wages. The state where the job is situated can affect the salary. Manufacturing Engineers can make as much at $34 an hr in some states.
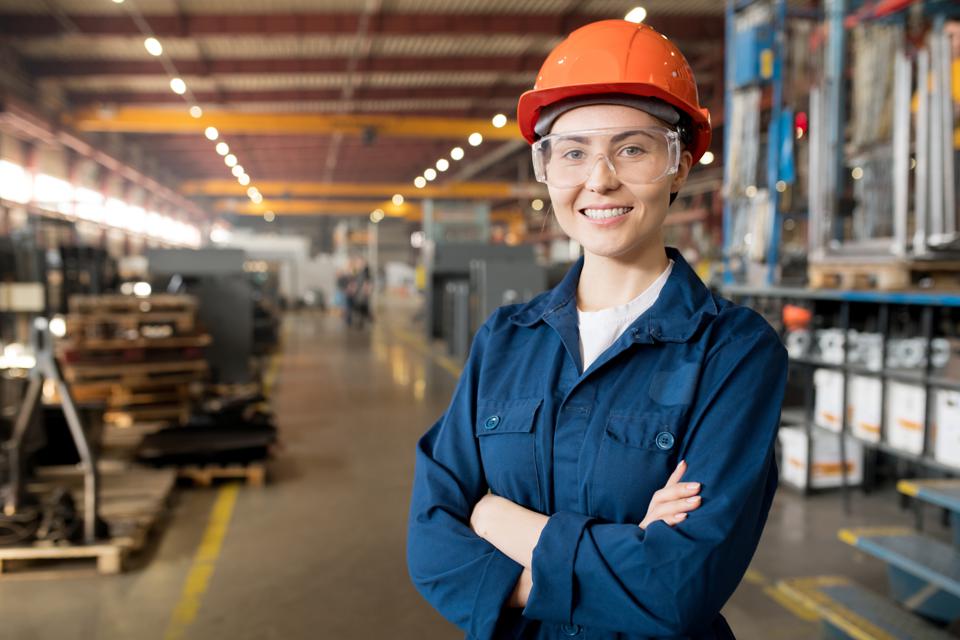
A manufacturing engineer can work in many manufacturing industries, such as aerospace, food manufacturing and pharmaceutical manufacturing. They can either work for multinational companies or smaller local operations. You can also find manufacturing engineers working for the central and local governments.
They may also be able to work in the construction of new industrial estates. Some of the largest manufacturing companies in the United States include Boeing, General Motors, and Tesla. A graduate degree is also a great way for engineers to learn about new technologies.
FAQ
Why is logistics important in manufacturing?
Logistics are an integral part any business. They can help you achieve great success by helping you manage product flow from raw material to finished goods.
Logistics are also important in reducing costs and improving efficiency.
How can manufacturing efficiency be improved?
First, identify the factors that affect production time. We must then find ways that we can improve these factors. If you aren't sure where to begin, think about the factors that have the greatest impact on production time. Once you've identified them, try to find solutions for each of those factors.
How can manufacturing avoid production bottlenecks
To avoid production bottlenecks, ensure that all processes run smoothly from the moment you receive your order to the time the product ships.
This includes both planning for capacity and quality control.
The best way to do this is to use continuous improvement techniques such as Six Sigma.
Six Sigma Management System is a method to increase quality and reduce waste throughout your organization.
It focuses on eliminating variation and creating consistency in your work.
Statistics
- Many factories witnessed a 30% increase in output due to the shift to electric motors. (en.wikipedia.org)
- According to the United Nations Industrial Development Organization (UNIDO), China is the top manufacturer worldwide by 2019 output, producing 28.7% of the total global manufacturing output, followed by the United States, Japan, Germany, and India.[52][53] (en.wikipedia.org)
- In the United States, for example, manufacturing makes up 15% of the economic output. (twi-global.com)
- In 2021, an estimated 12.1 million Americans work in the manufacturing sector.6 (investopedia.com)
- (2:04) MTO is a production technique wherein products are customized according to customer specifications, and production only starts after an order is received. (oracle.com)
External Links
How To
Six Sigma and Manufacturing
Six Sigma is defined as "the application of statistical process control (SPC) techniques to achieve continuous improvement." It was developed by Motorola's Quality Improvement Department at their plant in Tokyo, Japan, in 1986. Six Sigma's basic concept is to improve quality and eliminate defects through standardization. Many companies have adopted this method in recent years. They believe there is no such thing a perfect product or service. The main goal of Six Sigma is to reduce variation from the mean value of production. You can calculate the percentage of deviation from the norm by taking a sample of your product and comparing it to the average. If there is a significant deviation from the norm, you will know that something needs to change.
Understanding how variability works in your company is the first step to Six Sigma. Once you understand that, it is time to identify the sources of variation. It is important to identify whether the variations are random or systemic. Random variations are caused when people make mistakes. While systematic variations are caused outside of the process, they can occur. Random variations would include, for example, the failure of some widgets to fall from the assembly line. But if you notice that every widget you make falls apart at the exact same place each time, this would indicate that there is a problem.
Once you've identified where the problems lie, you'll want to design solutions to eliminate those problems. It might mean changing the way you do business or redesigning it entirely. After implementing the new changes, you should test them again to see if they worked. If they don't work you need to rework them and come up a better plan.