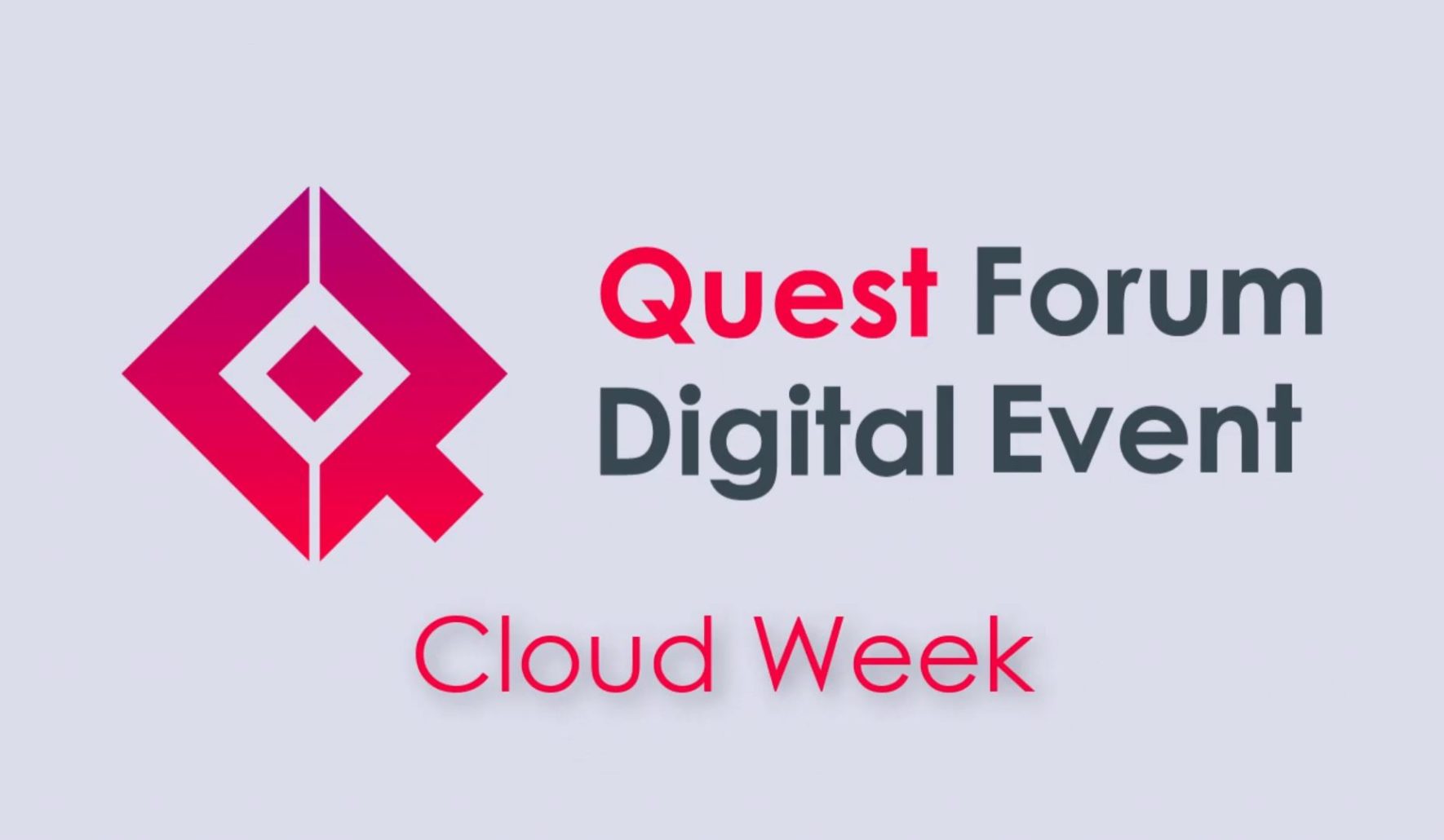
The industrial engineering technician uses their engineering and mathematics knowledge to improve the business's efficiency. This includes creating blueprints for machinery, analysing data and designing procedures. A skilled industrial engineer will be able to help management make decisions that will increase the efficiency of the company.
A typical job for an industrial engineer technician is to perform time and motion studies to improve productivity, evaluate performance, and implement changes. They may also be needed to analyze data that is part of an industrial health or safety program.
In addition, they perform other technical tasks such as preparing schematics and graphs to illustrate the workflow of a process. They also perform numerous quality tests on products to ensure they conform to standards.
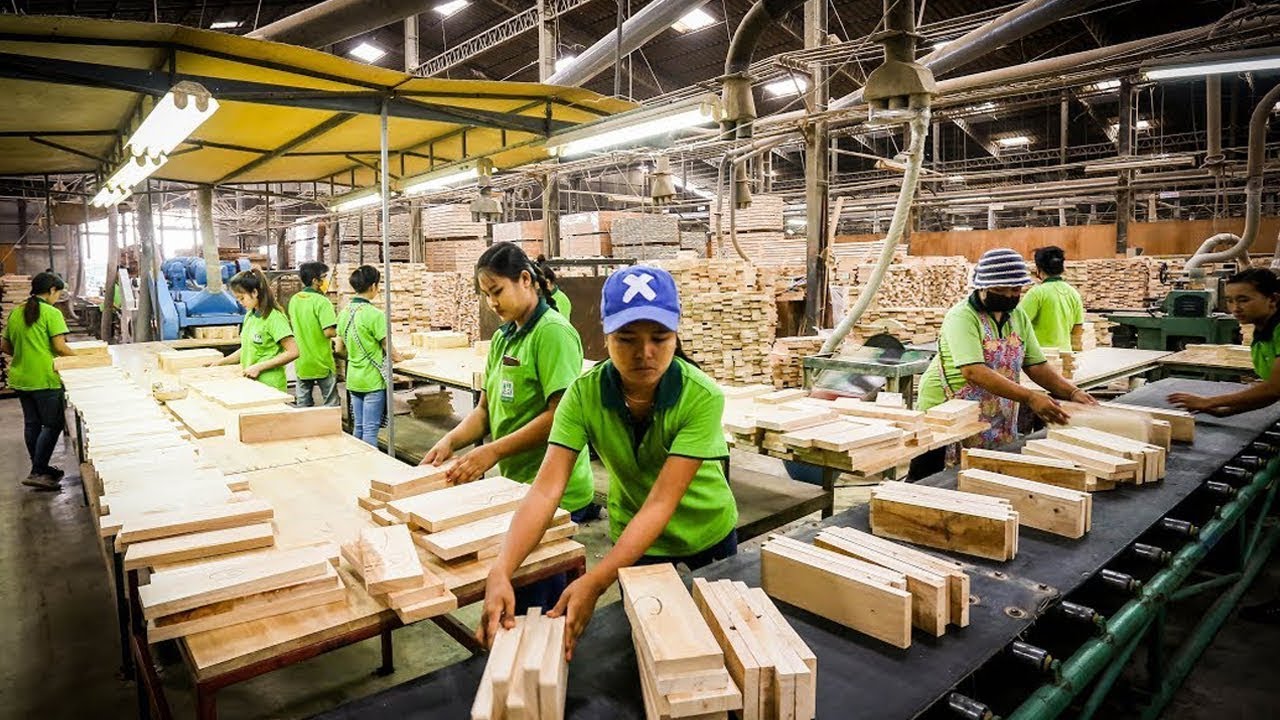
A popular job function for industrial engineers is to plan workflows, analyze production costs, gauge prototypes, assess equipment capacities, and create efficient operating procedures. They can be found in a variety of industries, including aerospace, pharmaceuticals, electronics, food, and automotive. Most work full-time. The average annual salary for these workers is $53,000, although those with more education and experience might be able to make a better living.
Industrial engineers do not need any specific degrees. You will need to be able to use your math skills, think critically, and have a good eye for detail. They must be able and willing to communicate with employees and to observe work processes.
An industrial engineer technician who is skilled in recognizing the key factors will ensure the most efficient workflow. For example, they should understand the importance to reduce waste materials and other inefficient practices. This allows them to see the value of implementing improvements at work and can save money for the company.
They are more likely to be the first in an organization to explore new ideas. The best way to achieve this is by creating a strategic plan. It's like putting together the pieces of an enormous puzzle.
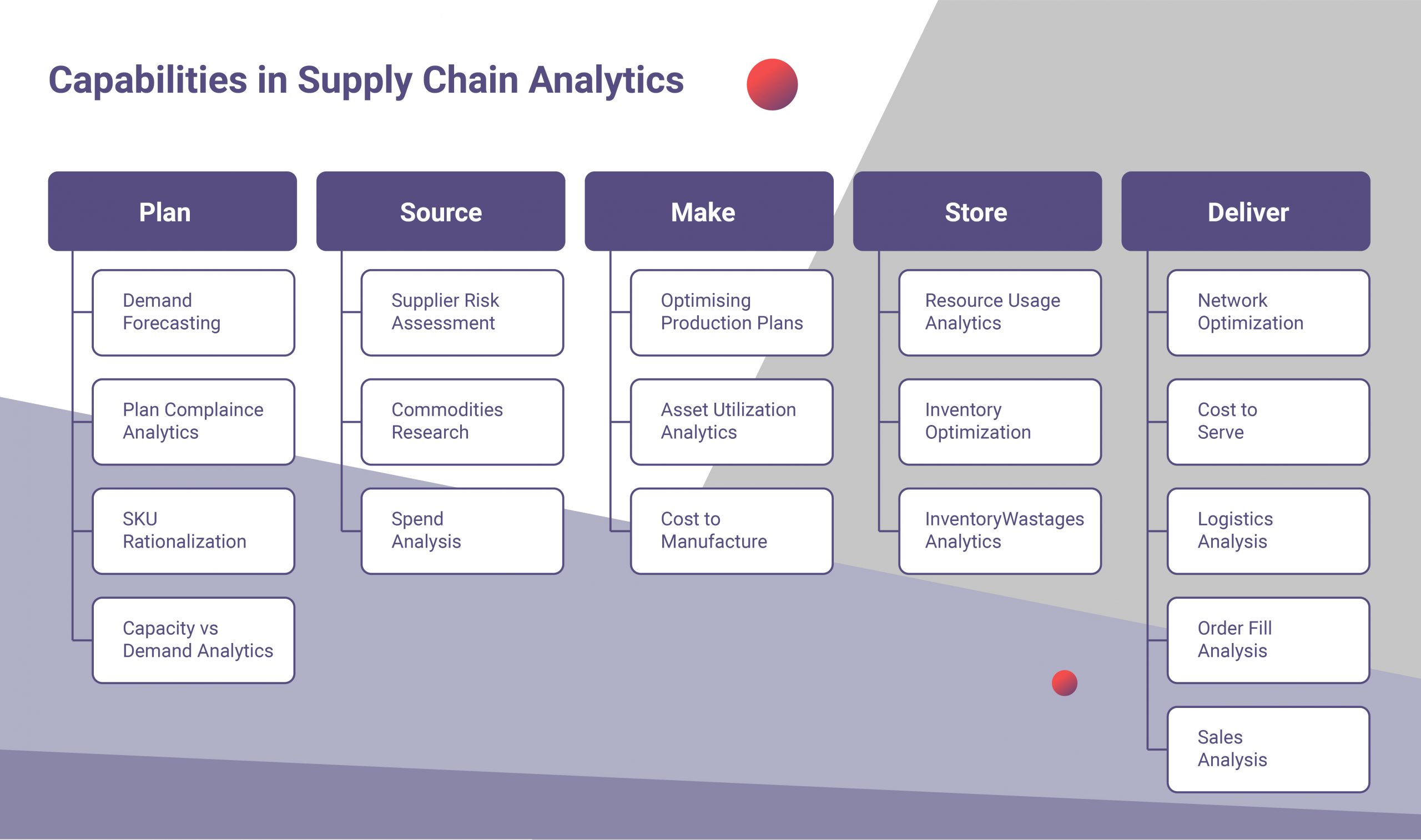
Another interesting job function of an industrial engineer is improving the quality of the output produced. Although the automation of manufacturing will decrease the number of jobs available, increasing cost control will increase the importance of industrial engineering technicians.
Engineers may choose to conduct time and motion studies to determine the task's duration. To calculate a standard rate of production, they might use the data from this study. These data will be used to improve the operations.
Many universities offer a wide variety of courses in industrial engineering technology, including Liberty University. The program helps students learn how to work together and problem solve.
FAQ
What does manufacturing mean?
Manufacturing Industries are companies that manufacture products. Consumers are the people who purchase these products. To accomplish this goal, these companies employ a range of processes including distribution, sales, management, and production. They create goods from raw materials, using machines and various other equipment. This includes all types of manufactured goods, including food items, clothing, building supplies, furniture, toys, electronics, tools, machinery, vehicles, pharmaceuticals, medical devices, chemicals, and many others.
What are the 4 types manufacturing?
Manufacturing refers the process of turning raw materials into useful products with machines and processes. It can involve many activities like designing, manufacturing, testing packaging, shipping, selling and servicing.
Why automate your warehouse
Modern warehouses are increasingly dependent on automation. E-commerce has increased the demand for quicker delivery times and more efficient processes.
Warehouses need to adapt quickly to meet changing needs. They must invest heavily in technology to do this. The benefits of automating warehouses are numerous. These are some of the benefits that automation can bring to warehouses:
-
Increases throughput/productivity
-
Reduces errors
-
Increases accuracy
-
Safety enhancements
-
Eliminates bottlenecks
-
This allows companies to scale easily
-
Increases efficiency of workers
-
Provides visibility into everything that happens in the warehouse
-
Enhances customer experience
-
Improves employee satisfaction
-
It reduces downtime, and increases uptime
-
Quality products delivered on time
-
Human error can be eliminated
-
This helps to ensure compliance with regulations
What is the role and responsibility of a Production Planner?
Production planners make sure that every aspect of the project is delivered on-time, within budget, and within schedule. A production planner ensures that the service and product meet the client's expectations.
Is it necessary to be familiar with Manufacturing Processes before we learn about Logistics.
No. No. It is important to know about the manufacturing processes in order to understand how logistics works.
What is production plan?
Production Planning refers to the development of a plan for every aspect of production. It is important to have everything ready and planned before you start shooting. It should also provide information about how best to produce the best results while on set. This includes shooting schedules, locations, cast lists, crew details, and equipment requirements.
The first step in filming is to define what you want. You may already know where you want the film to be shot, or perhaps you have specific locations and sets you wish to use. Once you have determined your scenes and locations, it is time to start figuring out the elements that you will need for each scene. You might decide you need a car, but not sure what make or model. You could look online for cars to see what options are available, and then narrow down your choices by selecting between different makes or models.
Once you have found the right vehicle, you can think about adding accessories. Are you looking for people to sit in the front seats? Or maybe you just need someone to push the car around. Maybe you'd like to change the interior from black to a white color. These questions can help you decide the right look for your car. You can also think about the type of shots you want to get. You will be filming close-ups and wide angles. Perhaps you want to show the engine or the steering wheel? These things will help you to identify the car that you are looking for.
Once you have determined all of the above, you can move on to creating a schedule. You can use a schedule to determine when and where you need it to be shot. Every day will have a time for you to arrive at the location, leave when you are leaving and return home when you are done. Everyone knows exactly what they should do and when. Book extra staff ahead of time if you need them. It's not worth paying someone to show up if you haven't told him.
Also, consider how many days you will be filming your schedule. Some projects are quick and easy, while others take weeks. While creating your schedule, it is important to remember whether you will require more than one shot per day. Multiple takes at the same place will result in higher costs and longer completion times. You can't be certain if you will need multiple takes so it is better not to shoot too many.
Budgeting is another important aspect of production planning. A realistic budget will help you work within your means. You can always lower the budget if you encounter unexpected problems. But, don't underestimate how much money you'll spend. Underestimating the cost will result in less money after you have paid for other items.
Production planning can be a complex process. However, once you know how everything works together it will become easier to plan future projects.
What does warehouse refer to?
A warehouse or storage facility is where goods are stored before they are sold. It can be indoors or out. In some cases, it may be a combination of both.
Statistics
- It's estimated that 10.8% of the U.S. GDP in 2020 was contributed to manufacturing. (investopedia.com)
- According to a Statista study, U.S. businesses spent $1.63 trillion on logistics in 2019, moving goods from origin to end user through various supply chain network segments. (netsuite.com)
- In 2021, an estimated 12.1 million Americans work in the manufacturing sector.6 (investopedia.com)
- Many factories witnessed a 30% increase in output due to the shift to electric motors. (en.wikipedia.org)
- (2:04) MTO is a production technique wherein products are customized according to customer specifications, and production only starts after an order is received. (oracle.com)
External Links
How To
How to use the Just-In Time Method in Production
Just-intime (JIT), a method used to lower costs and improve efficiency in business processes, is called just-in-time. It's a way to ensure that you get the right resources at just the right time. This means that only what you use is charged to your account. Frederick Taylor first coined this term while working in the early 1900s as a foreman. He noticed that workers were often paid overtime when they had to work late. He concluded that if workers were given enough time before they start work, productivity would increase.
JIT is a way to plan ahead and make sure you don't waste any money. You should also look at the entire project from start to finish and make sure that you have sufficient resources available to deal with any problems that arise during the course of your project. If you anticipate that there might be problems, you'll have enough people and equipment to fix them. This way, you won't end up paying extra money for things that weren't really necessary.
There are many JIT methods.
-
Demand-driven JIT: You order the parts and materials you need for your project every other day. This will allow you to track how much material you have left over after using it. You'll also be able to estimate how long it will take to produce more.
-
Inventory-based: This allows you to store the materials necessary for your projects in advance. This allows one to predict how much they will sell.
-
Project-driven: This means that you have enough money to pay for your project. If you know the amount you require, you can buy the materials you need.
-
Resource-based JIT : This is probably the most popular type of JIT. You allocate resources based on the demand. You will, for example, assign more staff to deal with large orders. If you don’t have many orders you will assign less people to the work.
-
Cost-based: This is a similar approach to resource-based but you are not only concerned with how many people you have, but also how much each one costs.
-
Price-based: This is a variant of cost-based. However, instead of focusing on the individual workers' costs, this looks at the total price of the company.
-
Material-based: This is quite similar to cost-based, but instead of looking at the total cost of the company, you're concerned with how much raw materials you spend on average.
-
Time-based JIT: This is another variant of resource-based JIT. Instead of focusing solely on the amount each employee costs, focus on how long it takes for the project to be completed.
-
Quality-based: This is yet another variation of resource-based JIT. Instead of thinking about the cost of each employee or the time it takes to produce something, you focus on how good your product quality.
-
Value-based JIT: This is the latest form of JIT. You don't worry about whether the products work or if they meet customer expectations. Instead, your goal is to add value to the market.
-
Stock-based: This inventory-based approach focuses on how many items are being produced at any one time. This method is useful when you want to increase production while decreasing inventory.
-
Just-in-time planning (JIT): This is a combination JIT and supply-chain management. This refers to the scheduling of the delivery of components as soon after they are ordered. It's important as it reduces leadtimes and increases throughput.