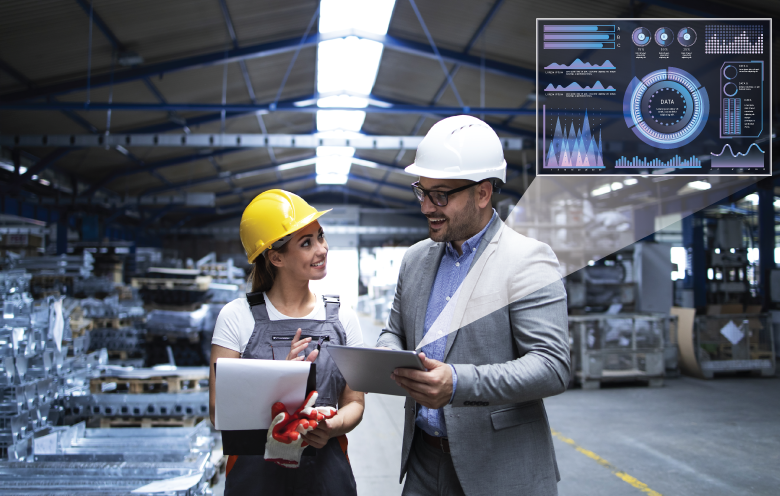
Supply chain management software will help you improve your efficiency and streamline your processes, no matter if you work for a large corporation or small business. These systems can give you a central view to your entire supply network, allowing for planning production, shipment planning, as well as delivery routes. They help you automate and streamline processes, freeing up your employees' time to focus on other areas of the business. Supply chain management software is important to every organization that controls shipping and manufacturing.
In order to choose the best supply chain management software, you should look for several features and capabilities. These features include integration with other applications, scalability, usability, and ease-of-use. You also need to consider the provider's credibility and the features that they offer. Additionally, it is important to find a solution within your budget. No matter whether you are looking for a SaaS option or a full-scale package, you should be able to adapt to your changing needs.
E2open is a leading provider of supply chain management software. It specializes in cloud-based solutions that provide better demand forecasting, operations management, and other benefits. E2open also provides advanced features and a technology platform. The software can be used by businesses in all industries, such as manufacturing, transport, and retail.
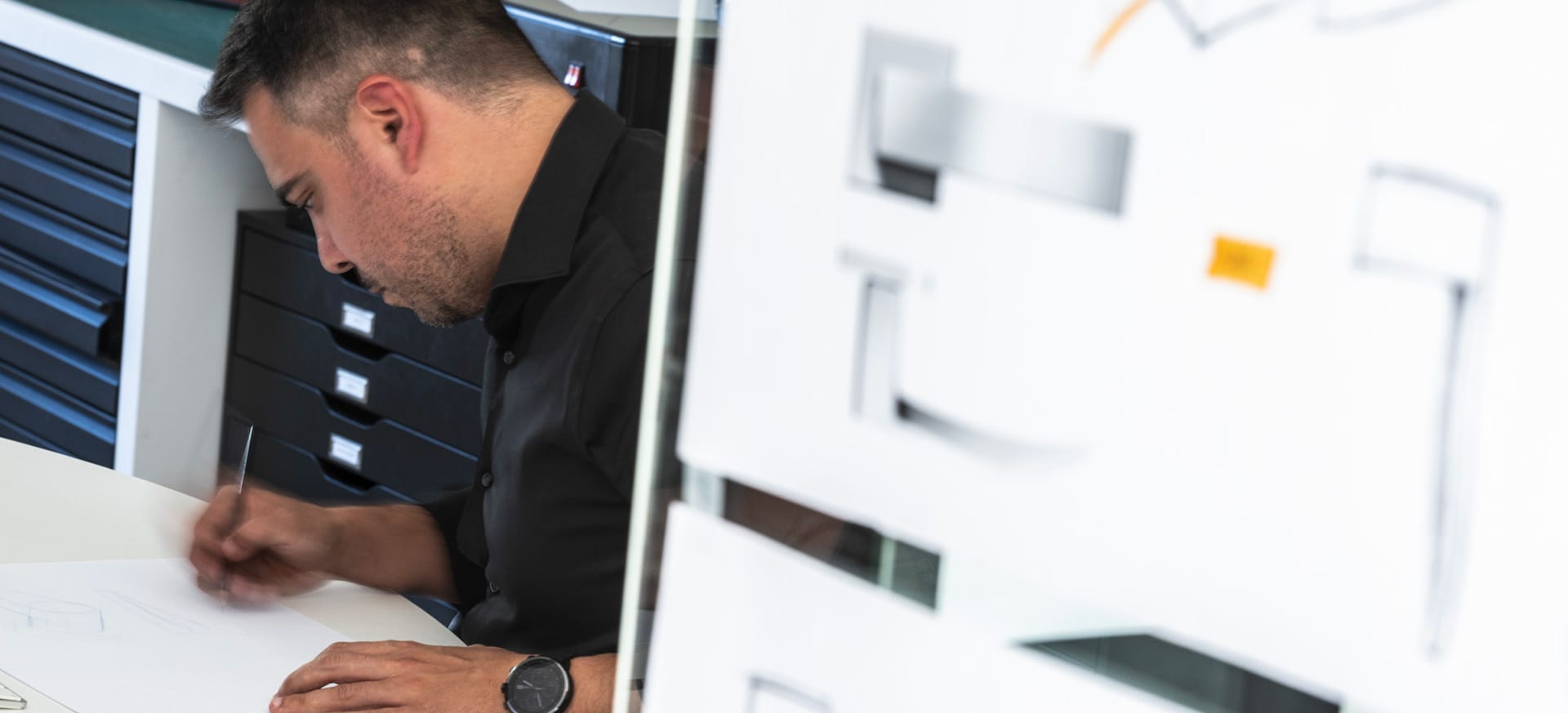
Real-time visibility is an important feature of supply chain software. This software allows you to track and monitor your inventory as well as your shipments. This helps ensure your customers always have the right product at the right time. It allows you to create long-term plans for managing demand-supply imbalance.
Kinaxis provides a comprehensive supply-chain management software solution. It breaks down silos to streamline processes. It combines human and machine intelligence to help you make better decisions. It can also help you plan inventory and capacity, so you can better respond to opportunities.
Sales forecasting software allows you to better understand historical sales, sales cycles, and seasonality. It also makes use of machine learning to predict future sales. This software can help you forecast your sales and prepare your sales team for the future. This software allows you to view data from multiple sources and gives you a complete picture of your operations.
Descartes Systems Group is the largest competitor in supply-chain management software. Descartes Systems Group is the leading vendor for many companies. This company has more than 13,000 active customers, and its products compete against SAP SCM, Megaventory and JDA.

Another major competitor to supply chain management software is Manhattan Associates. This software company has thousands of users, and its revenue is about $617.5 million. Eddie Capel runs the company. This company competes against JDA and Logility.
Infor SCM is one of the best supply chain management software platforms. It is a perfect solution for businesses of any size and one of the most widely-used supply chain management platforms. It's a cloud-based application that unifies all enterprise processes. It also offers analytics at its core, which can be used to optimize your end-to–end supply chain.
FAQ
What does it take for a logistics enterprise to succeed?
To run a successful logistics company, you need a lot knowledge and skills. For clients and suppliers to be successful, you need to have excellent communication skills. You will need to know how to interpret data and draw conclusions. You will need to be able handle pressure well and work in stressful situations. You need to be innovative and creative to come up with new ways to increase efficiency. You will need strong leadership skills to motivate and direct your team members towards achieving their organizational goals.
It is also important to be efficient and well organized in order meet deadlines.
How can manufacturing prevent production bottlenecks?
To avoid production bottlenecks, ensure that all processes run smoothly from the moment you receive your order to the time the product ships.
This includes planning for capacity requirements as well as quality control measures.
This can be done by using continuous improvement techniques, such as Six Sigma.
Six Sigma Management System is a method to increase quality and reduce waste throughout your organization.
It emphasizes consistency and eliminating variance in your work.
What makes a production planner different from a project manger?
The primary difference between a producer planner and a manager of a project is that the manager usually plans and organizes the whole project, while a production planner is only involved in the planning stage.
What do we need to know about Manufacturing Processes in order to learn more about Logistics?
No. No. But, being familiar with manufacturing processes will give you a better understanding about how logistics works.
Statistics
- In the United States, for example, manufacturing makes up 15% of the economic output. (twi-global.com)
- It's estimated that 10.8% of the U.S. GDP in 2020 was contributed to manufacturing. (investopedia.com)
- According to the United Nations Industrial Development Organization (UNIDO), China is the top manufacturer worldwide by 2019 output, producing 28.7% of the total global manufacturing output, followed by the United States, Japan, Germany, and India.[52][53] (en.wikipedia.org)
- In 2021, an estimated 12.1 million Americans work in the manufacturing sector.6 (investopedia.com)
- [54][55] These are the top 50 countries by the total value of manufacturing output in US dollars for its noted year according to World Bank.[56] (en.wikipedia.org)
External Links
How To
Six Sigma in Manufacturing
Six Sigma is defined by "the application SPC (statistical process control) techniques to achieve continuous improvements." Motorola's Quality Improvement Department, Tokyo, Japan, developed it in 1986. Six Sigma's main goal is to improve process quality by standardizing processes and eliminating defects. In recent years, many companies have adopted this method because they believe there is no such thing as perfect products or services. Six Sigma seeks to reduce variation between the mean production value. It is possible to measure the performance of your product against an average and find the percentage of time that it differs from the norm. If the deviation is excessive, it's likely that something needs to be fixed.
Understanding the nature of variability in your business is the first step to Six Sigma. Once you've understood that, you'll want to identify sources of variation. You'll also want to determine whether these variations are random or systematic. Random variations are caused when people make mistakes. While systematic variations are caused outside of the process, they can occur. For example, if you're making widgets, and some of them fall off the assembly line, those would be considered random variations. But if you notice that every widget you make falls apart at the exact same place each time, this would indicate that there is a problem.
Once you have identified the problem, you can design solutions. That solution might involve changing the way you do things or redesigning the process altogether. You should then test the changes again after they have been implemented. If they don't work you need to rework them and come up a better plan.