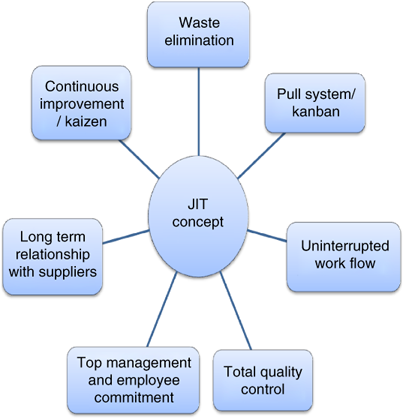
Six-Sigma and Lean both offer complementary methods for improving processes. Both tools can be used to solve problems but each approach has its own strengths. Six-Sigma refers to a statistical control technique. Lean, on the other hand, starts with the assumption that a product should add value to its customers, not just make it. Lean aims to reduce waste and improve product quality as it is produced.
Problem solving in PDCA
Although there are differences in DMAIC problem solving and PDCA, they both use the DMAIC approach. The PDCA cycle is more complex and requires more analysis. PDCA is not as effective as DMAIC for urgent problems. This approach requires a problem solver with technical skills. Six Sigma is looking for a problem-solving partner who is certified as a Six Sigma green belt practitioner.
Six Sigma's problem-solving cycle was introduced in the 1950s by W. Edwards Deming. It was intended to be used together with continuous improvement techniques to rebuild Japan’s industries. Real data must be collected and a clear mission statement must created in the P (Plan). The team must then decide on a solution after the PDCA stage.
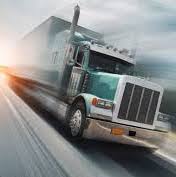
Process maps
One key difference between Six Sigma processes maps and Lean is the way each describes them. Both focus on the details of a process, but each methodology will be more focused on certain aspects. Lean, on the other hand, is about mapping actual processes rather than standard operating procedures. Make sure to include major activities, decisions, approvals, and other sources of approval when creating process maps. Consider areas that use multiple methods, factors, and other obstacles. Match roles carefully and examine the flow of the process.
A process map should include steps, symbols, and arrows to show the flow of a process. To ensure that each process accurately depicts the actual process, several people should review it. Also, a process map should include the date it was created and who to contact if there are any questions. Process maps can be a great way to improve any process. However, they may be overly complex.
Analyse cause-effect
Six Sigma and lean project management techniques involve statistical analysis and stochastic optimization. The Cause and Effect Matrix, also known as the Cause and Effect Matrix (CAE), links each step of a process to its inputs and outputs. Customers' requirements are listed in order they are most important to them. Inputs and outputs are then ranked according to their impact on the outcome. You should identify the key input variables to your process and rank them accordingly.
Although each technique is unique, they all offer different benefits. Lean Six Sigma utilizes a process-improvement methodology that is based in Frederick Winslow Taylor’s Principles of Scientific Management. Taylor understood business processes as interconnected processes that are linked together. In addition to eliminating variation, he recommended reducing waste. Six-Sigma (and lean) are complementary in the effort to reduce waste.

Eliminating Variation
Variability is part of every manufacturing process. This variability causes uncertainty in the outcome. Professional results require consistency. Six Sigma and Lean manufacturing methods strive to eliminate variation. Some amount of variation is fine, but too much leads to repairs, rework, and possibly even out-of-business consequences. The best way to manage variation is to identify the root cause.
Look for variations at decision points first. Process maps, which are represented in diamonds, identify decision points. Six Sigma teams can begin by identifying decision points, and then start eliminating variations. This information can be obtained from the Six Sigma team or the process owner. The Six Sigma group cannot focus on a process that is not governed by a standard process if it's owner. If the Six Sigma team does not have sufficient technical ability to make adjustments, a process diagram may not be useful.
FAQ
How can I find out more about manufacturing?
The best way to learn about manufacturing is through hands-on experience. But if that is not possible you can always read books and watch educational videos.
Is it necessary to be familiar with Manufacturing Processes before we learn about Logistics.
No. You don't have to know about manufacturing processes before learning about logistics. However, knowing about manufacturing processes will definitely give you a better understanding of how logistics works.
What jobs are available in logistics?
There are many types of jobs in logistics. These are some of the jobs available in logistics:
-
Warehouse workers – They load, unload and transport pallets and trucks.
-
Transportation drivers: They drive trucks and trailers and deliver goods and make pick-ups.
-
Freight handlers - They sort and pack freight in warehouses.
-
Inventory managers - These are responsible for overseeing the stock of goods in warehouses.
-
Sales reps are people who sell products to customers.
-
Logistics coordinators: They plan and manage logistics operations.
-
Purchasing agents - They buy goods and services that are necessary for company operations.
-
Customer service representatives - Answer calls and email from customers.
-
Shippers clerks - They process shipping order and issue bills.
-
Order fillers - These people fill orders based on what has been ordered.
-
Quality control inspectors are responsible for inspecting incoming and outgoing products looking for defects.
-
Others – There are many other types available in logistics. They include transport supervisors, cargo specialists and others.
What does it mean to warehouse?
A warehouse, or storage facility, is where goods are stored prior to being sold. It can be an indoor space or an outdoor area. It could be one or both.
What is the difference in Production Planning and Scheduling, you ask?
Production Planning (PP), or production planning, is the process by which you determine what products are needed at any given time. This is accomplished by forecasting the demand and identifying production resources.
Scheduling is the process that assigns dates to tasks so they can get completed within a given timeframe.
How can manufacturing reduce production bottlenecks?
Avoiding production bottlenecks is as simple as keeping all processes running smoothly, from the time an order is received until the product ships.
This includes both quality control and capacity planning.
Continuous improvement techniques like Six Sigma are the best way to achieve this.
Six Sigma is a management method that helps to improve quality and reduce waste.
It seeks to eliminate variation and create consistency in your work.
What does manufacturing mean?
Manufacturing Industries are those businesses that make products for sale. Consumers are the people who purchase these products. These companies use various processes such as production, distribution, retailing, management, etc., to fulfill this purpose. They make goods from raw materials with machines and other equipment. This includes all types manufactured goods such as clothing, building materials, furniture, electronics, tools and machinery.
Statistics
- According to a Statista study, U.S. businesses spent $1.63 trillion on logistics in 2019, moving goods from origin to end user through various supply chain network segments. (netsuite.com)
- It's estimated that 10.8% of the U.S. GDP in 2020 was contributed to manufacturing. (investopedia.com)
- You can multiply the result by 100 to get the total percent of monthly overhead. (investopedia.com)
- (2:04) MTO is a production technique wherein products are customized according to customer specifications, and production only starts after an order is received. (oracle.com)
- In the United States, for example, manufacturing makes up 15% of the economic output. (twi-global.com)
External Links
How To
How to use 5S in Manufacturing to Increase Productivity
5S stands for "Sort", "Set In Order", "Standardize", "Separate" and "Store". Toyota Motor Corporation created the 5S methodology in 1954. This methodology helps companies improve their work environment to increase efficiency.
This method aims to standardize production processes so that they are repeatable, measurable and predictable. This means that tasks such as cleaning, sorting, storing, packing, and labeling are performed daily. Because workers know what they can expect, this helps them perform their jobs more efficiently.
There are five steps that you need to follow in order to implement 5S. Each step requires a different action, which increases efficiency. For example, when you sort things, you make them easy to find later. You arrange items by placing them in an order. Once you have separated your inventory into groups and organized them, you will store these groups in easily accessible containers. You can also label your containers to ensure everything is properly labeled.
Employees will need to be more critical about their work. Employees must be able to see why they do what they do and find a way to achieve them without having to rely on their old methods. They will need to develop new skills and techniques in order for the 5S system to be implemented.
In addition to improving efficiency, the 5S system also increases morale and teamwork among employees. Once they start to notice improvements, they are motivated to keep working towards their goal of increasing efficiency.