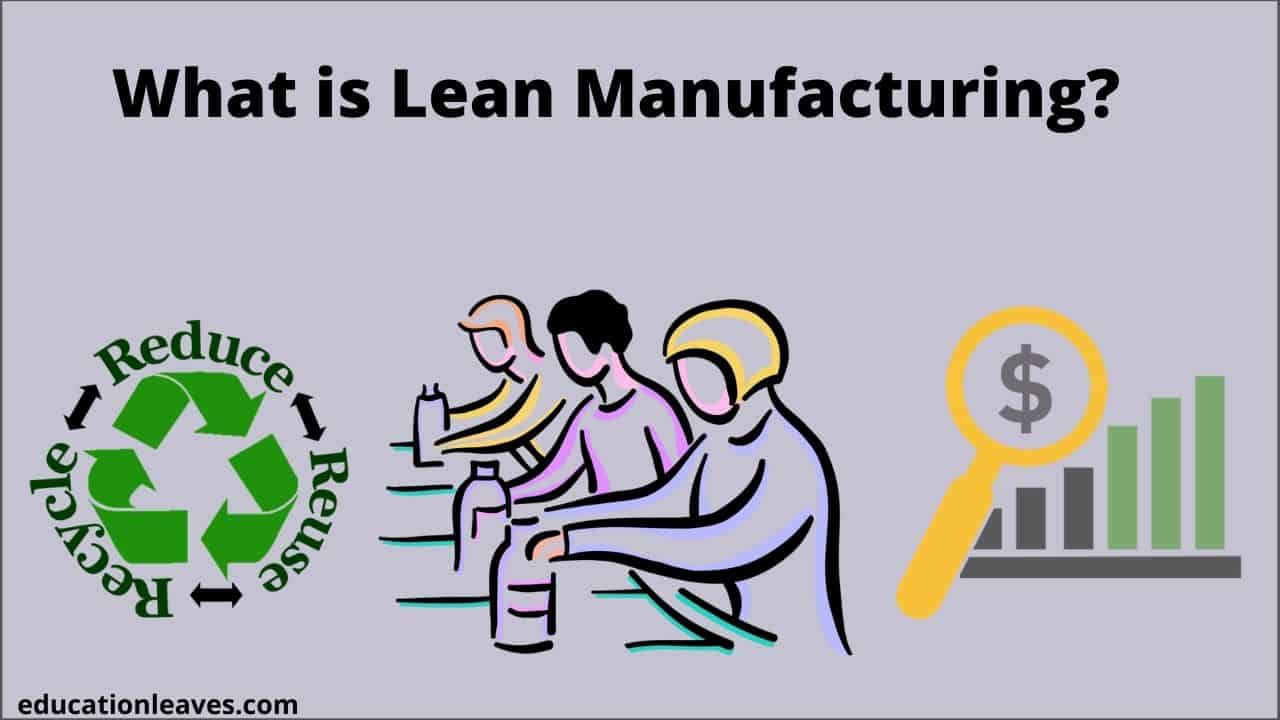
Integrated supply chain management allows companies to optimize and monitor the performance of their supply chains. It results in a more responsive and efficient production network. The more streamlined and responsive your supply chain is, the more efficient your operations will be. Integrated supply chain management will increase profits and reduce waste. This allows you to produce products that are better quality, reliable, and cheaper.
Integrated supply chain management can increase the reliability and predictability of your orders. Your production schedule can be more responsive, inventory levels more accurate, and your delivery dates more flexible. Integrated supply chains are also better at managing risk. It can also lower greenhouse gas emissions. This allows you to achieve your environmental goals.
First, you need to create a contract for integration with your vendors. These agreements should be tailored for your company's specific needs. The agreement should provide information about your production schedule and materials, as well as the costs. Your preferred suppliers must also be able demonstrate how their services will benefit the organization. Higher volumes of goods and services can lead to lower prices.
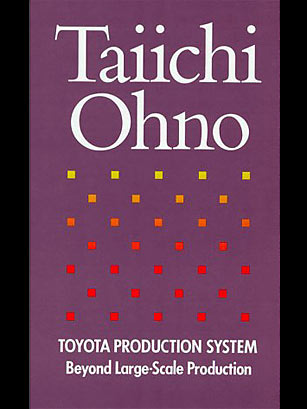
It is important to have a thorough understanding of your supply chain connections and how they impact your business. This will allow you to avoid costly mistakes and identify potential opportunities for improving performance. You should also have a comprehensive end-to-end plan to meet your needs. The plan should be flexible enough to handle any differences in production needs. This will also help to avoid delays.
Just-in-time distribution is a good example of integrated supply chains. This strategy lowers warehouse space and operational costs. It can also lead to accurate forecasting. Using an integrated supply chain is also important for reducing greenhouse gas emissions. You can do this by reducing your use of large fixed assets.
Vertical integration refers to when all the elements are in place for a product. This includes a manufacturer and vendor. This could allow the manufacturer to take a greater share of the profits. A widget manufacturer or firm that produces widgets might be a good option. This can enable you to gain control over your competitor's businesses and ensure that you charge a fair amount for widgets.
Container management strategies are another example of an integrated supply chains. This allows for you to monitor inventory levels and make adjustments as necessary to your container pulling strategies. It also allows for you to make adjustments to your production schedule live.
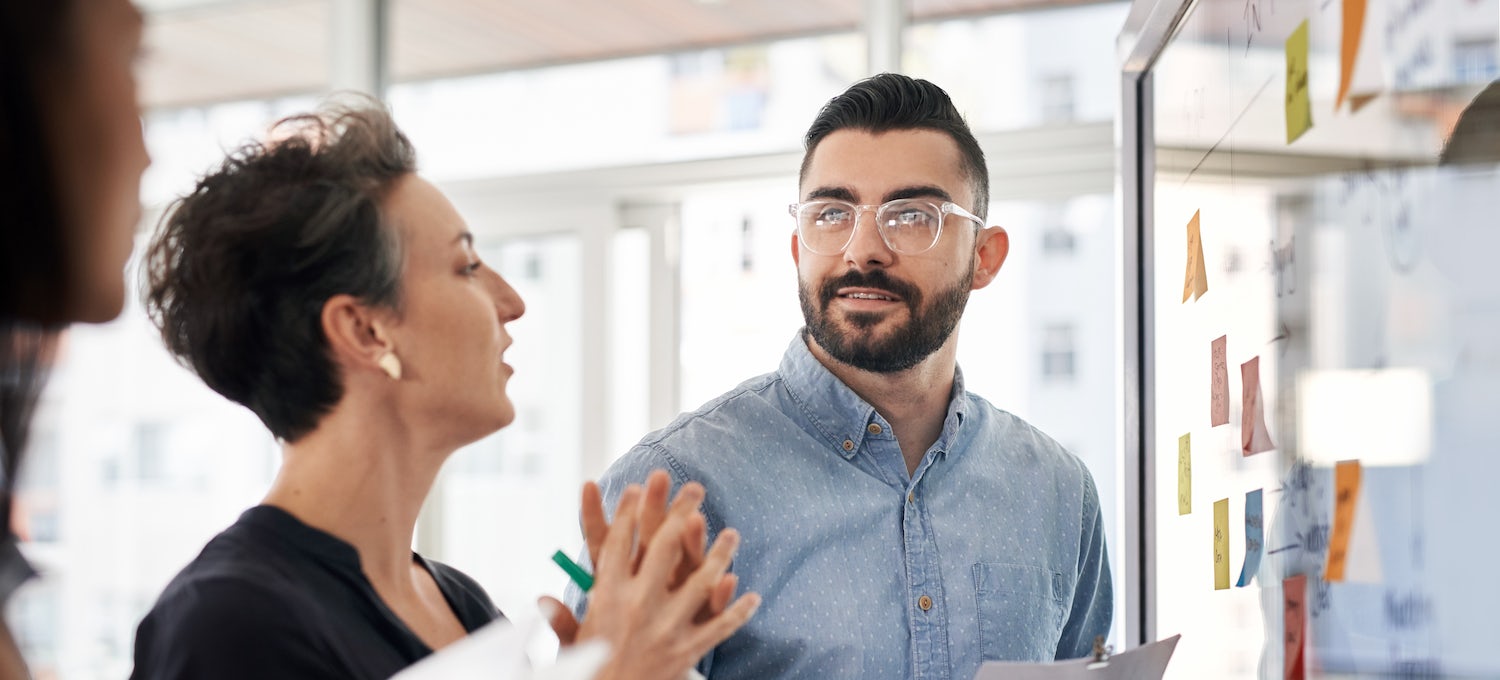
If you can clearly see your goals, a supply chain management plan will be more efficient. Integrated supply chains aim to improve performance and provide customers with the best possible products. An integrated supply chain can be used to reduce the amount of plastic waste and other waste generated during manufacturing. This can help you to improve your profit margins and reduce your greenhouse gas emissions.
FAQ
What are the differences between these four types?
Manufacturing refers to the transformation of raw materials into useful products by using machines and processes. It includes many different activities like designing, building and testing, packaging, shipping and selling, as well as servicing.
What are my options for learning more about manufacturing
You can learn the most about manufacturing by getting involved in it. But if that is not possible you can always read books and watch educational videos.
What is the role and responsibility of a Production Planner?
A production planner makes sure all project elements are delivered on schedule, within budget, as well as within the agreed scope. They also ensure that the product/service meets the client’s needs.
How can manufacturing excess production be decreased?
In order to reduce excess production, you need to develop better inventory management methods. This would decrease the time that is spent on inefficient activities like purchasing, storing, or maintaining excess stock. This could help us free up our time for other productive tasks.
A Kanban system is one way to achieve this. A Kanbanboard is a visual tool that allows you to keep track of the work being done. Kanban systems are where work items travel through a series of states until reaching their final destination. Each state has a different priority level.
If work is moving from one stage to the other, then the current task can be completed and moved on to the next. But if a task remains in the beginning stages it will stay that way until it reaches its end.
This allows for work to continue moving forward, while also ensuring that there is no work left behind. Managers can view the Kanban board to see how much work they have done. This data allows them adjust their workflow based upon real-time data.
Lean manufacturing is another option to control inventory levels. Lean manufacturing emphasizes eliminating waste in all phases of production. Any product that isn't adding value can be considered waste. The following are examples of common waste types:
-
Overproduction
-
Inventory
-
Packaging not required
-
Overstock materials
By implementing these ideas, manufacturers can improve efficiency and cut costs.
What kind of jobs are there in logistics?
There are different kinds of jobs available in logistics. Some examples are:
-
Warehouse workers – They load and unload pallets and trucks.
-
Transportation drivers – These drivers drive trucks and wagons to transport goods and pick up the goods.
-
Freight handlers, - They sort out and pack freight in warehouses.
-
Inventory managers - They oversee the inventory of goods in warehouses.
-
Sales representatives: They sell products to customers.
-
Logistics coordinators - They organize and plan logistics operations.
-
Purchasing agents are those who purchase goods and services for the company.
-
Customer service agents - They answer phone calls and respond to emails.
-
Shippers clerks - They process shipping order and issue bills.
-
Order fillers: They fill orders based off what has been ordered and shipped.
-
Quality control inspectors: They inspect outgoing and incoming products for any defects.
-
Others - There is a variety of other jobs in logistics. These include transportation supervisors and cargo specialists.
What is it like to manage a logistics company?
It takes a lot of skills and knowledge to run a successful logistics business. Good communication skills are essential to effectively communicate with your suppliers and clients. You must be able analyze data and draw out conclusions. You must be able to work well under pressure and handle stressful situations. You must be creative and innovative to develop new ideas to improve efficiency. You need to have strong leadership qualities to motivate team members and direct them towards achieving organizational goals.
To meet tight deadlines, you must also be efficient and organized.
How can we improve manufacturing efficiency?
First, determine which factors have the greatest impact on production time. We then need to figure out how to improve these variables. If you aren't sure where to begin, think about the factors that have the greatest impact on production time. Once you've identified them, try to find solutions for each of those factors.
Statistics
- Many factories witnessed a 30% increase in output due to the shift to electric motors. (en.wikipedia.org)
- According to a Statista study, U.S. businesses spent $1.63 trillion on logistics in 2019, moving goods from origin to end user through various supply chain network segments. (netsuite.com)
- In 2021, an estimated 12.1 million Americans work in the manufacturing sector.6 (investopedia.com)
- It's estimated that 10.8% of the U.S. GDP in 2020 was contributed to manufacturing. (investopedia.com)
- (2:04) MTO is a production technique wherein products are customized according to customer specifications, and production only starts after an order is received. (oracle.com)
External Links
How To
How to use the Just-In Time Method in Production
Just-in-time (JIT) is a method that is used to reduce costs and maximize efficiency in business processes. It's a way to ensure that you get the right resources at just the right time. This means that your only pay for the resources you actually use. Frederick Taylor developed the concept while working as foreman in early 1900s. After observing how workers were paid overtime for late work, he realized that overtime was a common practice. He concluded that if workers were given enough time before they start work, productivity would increase.
JIT is a way to plan ahead and make sure you don't waste any money. You should also look at the entire project from start to finish and make sure that you have sufficient resources available to deal with any problems that arise during the course of your project. If you expect problems to arise, you will be able to provide the necessary equipment and personnel to address them. This will prevent you from spending extra money on unnecessary things.
There are many JIT methods.
-
Demand-driven: This type of JIT allows you to order the parts/materials required for your project on a regular basis. This will allow for you to track the material that you have left after using it. You'll also be able to estimate how long it will take to produce more.
-
Inventory-based: This is a type where you stock the materials required for your projects in advance. This allows you to forecast how much you will sell.
-
Project-driven : This is a method where you make sure that enough money is set aside to pay the project's cost. When you know how much you need, you'll purchase the appropriate amount of materials.
-
Resource-based JIT: This type of JIT is most commonly used. Here you can allocate certain resources based purely on demand. For instance, if you have a lot of orders coming in, you'll assign more people to handle them. If there aren't many orders, you will assign fewer people.
-
Cost-based : This is similar in concept to resource-based. But here, you aren't concerned about how many people your company has but how much each individual costs.
-
Price-based: This approach is very similar to the cost-based method except that you don't look at individual workers costs but the total cost of the company.
-
Material-based is an alternative to cost-based. Instead of looking at the total cost in the company, this method focuses on the average amount of raw materials that you consume.
-
Time-based JIT is another form of resource-based JIT. Instead of focusing only on how much each employee is costing, you should focus on how long it takes to complete your project.
-
Quality-based JIT - This is another form of resource-based JIT. Instead of worrying about the costs of each employee or how long it takes for something to be made, you should think about how quality your product is.
-
Value-based: This is one of the newest forms of JIT. In this instance, you are not concerned about the product's performance or meeting customer expectations. Instead, you are focused on adding value to the marketplace.
-
Stock-based: This is an inventory-based method that focuses on the actual number of items being produced at any given time. It is used when production goals are met while inventory is kept to a minimum.
-
Just-intime (JIT), planning is a combination JIT management and supply chain management. It's the process of scheduling delivery of components immediately after they are ordered. It reduces lead times and improves throughput.