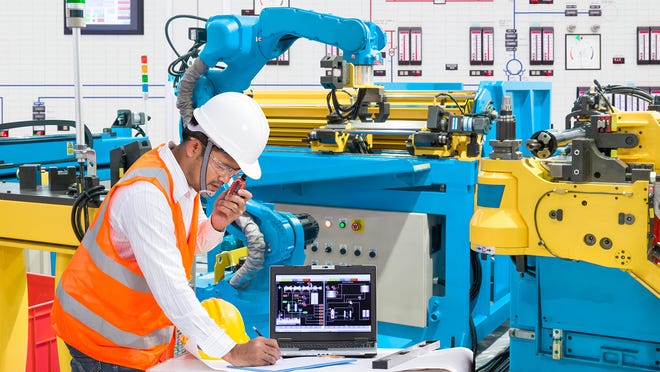
DFSS (Design for Six Sigma), is a design method that employs a variety of techniques to create a product, process, or service. It is intended to reduce waste, improve quality and increase market share. This is a highly effective method that can improve your products.
DFSS is a process that takes customer needs into account throughout the design process. This ensures that the product/service you design is most appropriate for the customer. It also ensures that your product has a high level of quality when it is introduced to the market. DFSS is often used to design a product or service from the ground up. It can also be used in the design of products and/or services to replace or enhance existing products.
The DFSS team will determine what the customer wants and needs in the initial phase. This can include gathering information on existing processes, interviewing customers, and surveying customers. The design team then evaluates alternative products and designs to find the best fit. This phase includes the development and classification of functional requirements, as well as substitute concepts. Depending on the complexity and scope of the project, additional steps may be necessary.
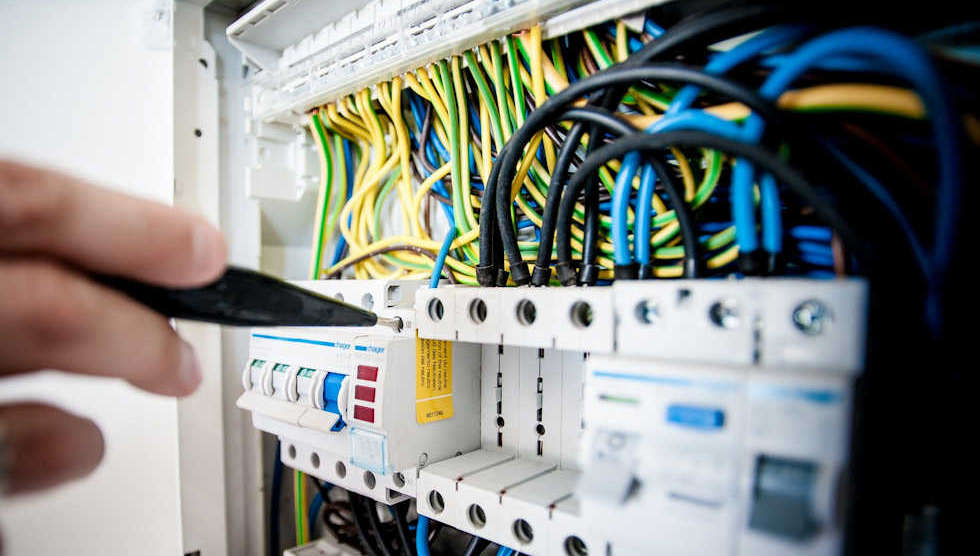
DFSS is a design method that allows companies to design products and services efficiently. It can also be used to identify potential issues before they become serious problems. It reduces waste and improves profitability for your company. It is designed to improve the effectiveness of a product/service by identifying processes that make it more efficient.
There are different methodologies for implementing DFSS. The most common is the DMADV method, which uses a five-step process. The process begins with the definition of the customer and their needs. Next, they create a design concept. This method has a solid engineering foundation and is frequently used to develop new products or services. The analysis and measurement phases are used to assess the product's performance.
The optimization step is the second phase. This involves evaluating product performance across multiple performance levels. This step is especially useful in developing new business procedures. This stage aims to reduce variability and ensure stability over time.
Verification is the final stage. This is used often to confirm that the product's stability. This stage also validates that the product is capable of performing over time. This process also includes validation testing. This step is usually completed after the design has been validated.
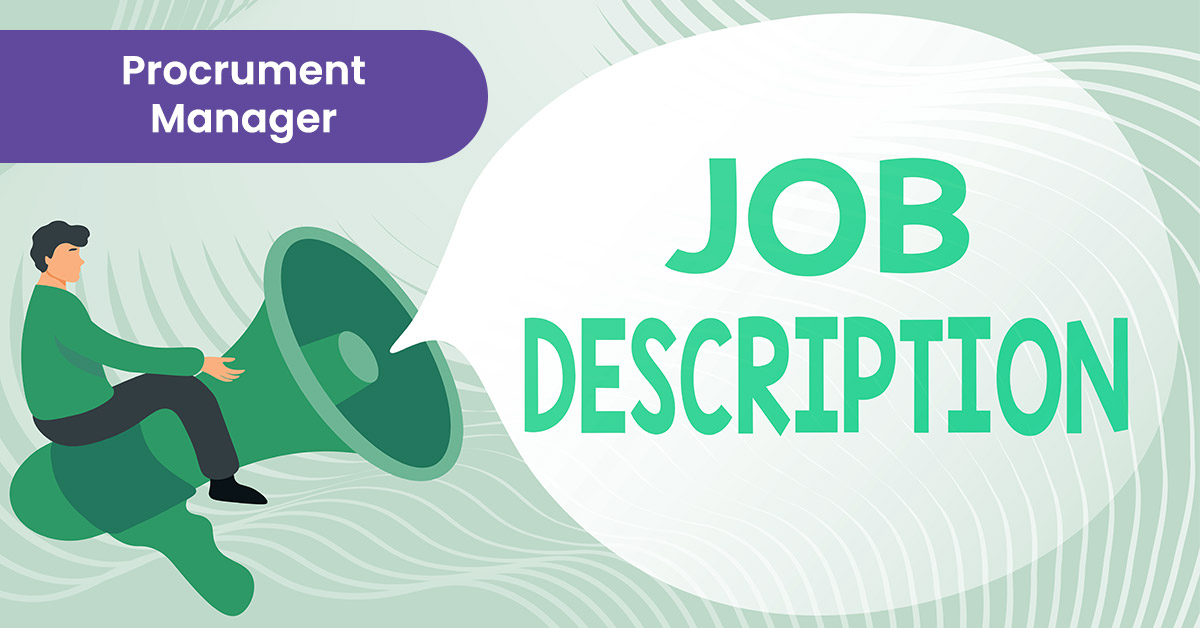
A detailed process map is essential to ensure that DFSS can be successfully implemented. It should show the various workflows involved in each step of the design process. It should include details about resources, timelines and milestones. External involvement should also be identified. To ensure the product meets customer needs, you may need to create a prototype. Implementing DFSS in an environment with clear rewards is a great way to achieve the project's goals.
FAQ
What are the 7 Rs of logistics?
The acronym 7R's for Logistics stands to represent the seven basic principles in logistics management. It was developed by International Association of Business Logisticians (IABL), and published as part of their "Seven Principles of Logistics Management Series" in 2004.
The following letters make up the acronym:
-
Responsible - ensure that all actions taken are within legal requirements and are not harmful to others.
-
Reliable – have faith in your ability and capability to keep promises.
-
Reasonable - use resources efficiently and don't waste them.
-
Realistic - Consider all aspects of operations, including environmental impact and cost effectiveness.
-
Respectful – Treat others fairly and equitably.
-
Resourceful - look for opportunities to save money and increase productivity.
-
Recognizable - provide customers with value-added services.
What makes a production planner different from a project manger?
The primary difference between a producer planner and a manager of a project is that the manager usually plans and organizes the whole project, while a production planner is only involved in the planning stage.
What are the products of logistics?
Logistics are the activities involved in moving goods from point A to point B.
They include all aspects associated with transport including packaging, loading transporting, unloading storage, warehousing inventory management customer service, distribution returns and recycling.
Logisticians make sure that the right product arrives at the right place at the correct time and in safe conditions. They help companies manage their supply chain efficiency by providing information on demand forecasts, stock levels, production schedules, and availability of raw materials.
They can also track shipments in transit and monitor quality standards.
Is it possible to automate certain parts of manufacturing
Yes! Automation has been around since ancient times. The Egyptians created the wheel thousands years ago. To help us build assembly lines, we now have robots.
There are many applications for robotics in manufacturing today. They include:
-
Robots for assembly line
-
Robot welding
-
Robot painting
-
Robotics inspection
-
Robots create products
Manufacturing can also be automated in many other ways. For example, 3D printing allows us to make custom products without having to wait for weeks or months to get them manufactured.
Statistics
- According to a Statista study, U.S. businesses spent $1.63 trillion on logistics in 2019, moving goods from origin to end user through various supply chain network segments. (netsuite.com)
- Job #1 is delivering the ordered product according to specifications: color, size, brand, and quantity. (netsuite.com)
- It's estimated that 10.8% of the U.S. GDP in 2020 was contributed to manufacturing. (investopedia.com)
- Many factories witnessed a 30% increase in output due to the shift to electric motors. (en.wikipedia.org)
- According to the United Nations Industrial Development Organization (UNIDO), China is the top manufacturer worldwide by 2019 output, producing 28.7% of the total global manufacturing output, followed by the United States, Japan, Germany, and India.[52][53] (en.wikipedia.org)
External Links
How To
How to Use the Just-In-Time Method in Production
Just-in-time (JIT) is a method that is used to reduce costs and maximize efficiency in business processes. It's a way to ensure that you get the right resources at just the right time. This means you only pay what you use. The term was first coined by Frederick Taylor, who developed his theory while working as a foreman in the early 1900s. After observing how workers were paid overtime for late work, he realized that overtime was a common practice. He decided to ensure workers have enough time to do their jobs before starting work to improve productivity.
JIT is an acronym that means you need to plan ahead so you don’t waste your money. It is important to look at your entire project from beginning to end and ensure that you have enough resources to handle any issues that may arise. If you expect problems to arise, you will be able to provide the necessary equipment and personnel to address them. You won't have to pay more for unnecessary items.
There are several types of JIT techniques:
-
Demand-driven: This JIT is where you place regular orders for the parts/materials that are needed for your project. This will enable you to keep track of how much material is left after you use it. This will let you know how long it will be to produce more.
-
Inventory-based: This allows you to store the materials necessary for your projects in advance. This allows you to forecast how much you will sell.
-
Project-driven: This approach involves setting aside sufficient funds to cover your project's costs. Knowing how much money you have available will help you purchase the correct amount of materials.
-
Resource-based JIT : This is probably the most popular type of JIT. Here, you allocate certain resources based on demand. You might assign more people to help with orders if there are many. If you don't receive many orders, then you'll assign fewer employees to handle the load.
-
Cost-based: This is similar to resource-based, except that here you're not just concerned about how many people you have but how much each person costs.
-
Price-based: This is a variant of cost-based. However, instead of focusing on the individual workers' costs, this looks at the total price of the company.
-
Material-based: This is very similar to cost-based but instead of looking at total costs of the company you are concerned with how many raw materials you use on an average.
-
Time-based JIT is another form of resource-based JIT. Instead of worrying about how much each worker costs, you can focus on how long the project takes.
-
Quality-based JIT: Another variation on resource-based JIT. Instead of worrying about the costs of each employee or how long it takes for something to be made, you should think about how quality your product is.
-
Value-based JIT : This is the newest type of JIT. In this case, you're not concerned with how well the products perform or whether they meet customer expectations. Instead, your goal is to add value to the market.
-
Stock-based: This inventory-based approach focuses on how many items are being produced at any one time. It is used when production goals are met while inventory is kept to a minimum.
-
Just-intime planning (JIT), is a combination JIT/sales chain management. It is the process of scheduling components' delivery as soon as they have been ordered. This is important as it reduces lead time and increases throughput.