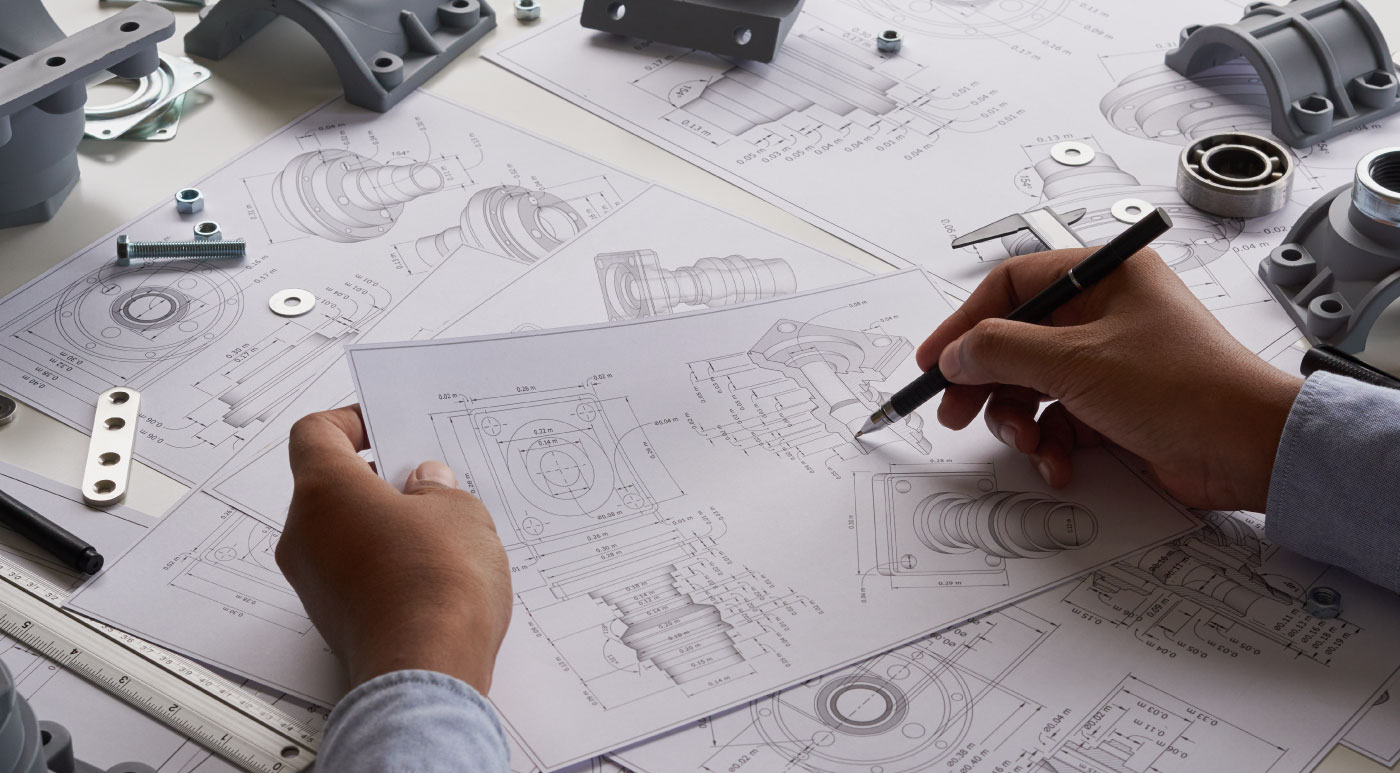
Industrial engineers are specialists who apply their knowledge of manufacturing technology in order to improve processes. They are responsible in developing new methods, analysing existing systems, and training workers on new policies. Because of their experience, they are highly sought after in engineering services, consulting, and research and design firms.
Although industrial engineers may work in many places, their primary focus is on improving the production process, reducing waste and internal costs. These engineers use creativity and logic to design new and improved processes for production. Some industrial engineers are involved in automated manufacturing processes.
The vast majority of industrial engineers have a solid background in mathematics, and other scientific principles. They must also be skilled at problem-solving as well as critical thinking. They should also be able to communicate well and work with others. Industrial engineers should have the ability to view a large system and spot weaknesses and potential strengths.
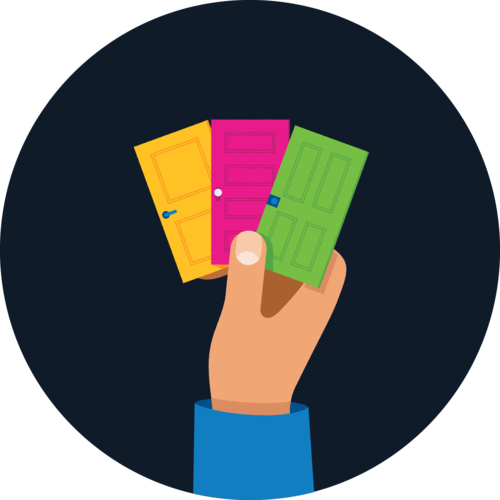
For industrial engineering careers, you must have a bachelor's degree with at least 4 years of experience. You can then apply for certification through the Society of Manufacturing Engineers. The master's degree will enable you to specialize in your chosen field.
The demand for industrial engineers is high. Their job openings will grow faster than the average national rate over the next ten year. During this time, employment of this professional is projected to increase by 10 percent. While most of the work is full-time, hours can vary depending upon the project. The median salary for industrial engineers in Nashville is $73,856. However, the wage can vary widely from one employer to the next, based on geographic location, employer, and individual qualifications.
You should highlight your professional and academic credentials when looking for a job as an industrial engineer in Nashville. Industry-specific certifications are also required. A professional engineer license is required if you plan to work for a government agency.
Many companies hire interns in order to help them understand the intricacies behind industrial engineering. Interns learn about lean manufacturing, value stream mapping, and kaizen. Your skills and the company may allow you to progress your career to a managerial position.
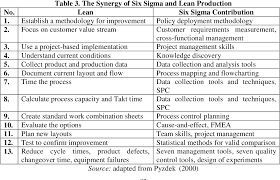
Whether you're working in a lab or an office, you'll need to develop interpersonal communication skills to work effectively with colleagues and managers. Other than communicating with colleagues, you must also be able communicate with customers and suppliers.
With an increasing demand for industrial engineering professionals, you can expect to find jobs in a variety of industries. These include equipment manufacturers, electronics and transportation manufacturers, as well engineering service firms. Several colleges offer 5-year degree programs in industrial engineering. Many graduates can find entry-level jobs in many industries. However, some colleges offer programs that are more specific to certain areas such as automated manufacturing.
FAQ
Can we automate some parts of manufacturing?
Yes! Yes! Automation has existed since ancient times. The Egyptians discovered the wheel thousands and years ago. We now use robots to help us with assembly lines.
There are many uses of robotics today in manufacturing. They include:
-
Line robots
-
Robot welding
-
Robot painting
-
Robotics inspection
-
Robots that produce products
Manufacturing could also benefit from automation in other ways. For example, 3D printing allows us to make custom products without having to wait for weeks or months to get them manufactured.
Why automate your warehouse?
Modern warehousing has seen automation take center stage. Increased demand for efficient and faster delivery has resulted in a rise in e-commerce.
Warehouses should be able adapt quickly to new needs. They must invest heavily in technology to do this. Automation warehouses can bring many benefits. Here are some benefits of investing in automation
-
Increases throughput/productivity
-
Reduces errors
-
Accuracy is improved
-
Boosts safety
-
Eliminates bottlenecks
-
Allows companies scale more easily
-
It makes workers more efficient
-
Gives you visibility into all that is happening in your warehouse
-
Enhances customer experience
-
Improves employee satisfaction
-
Minimizes downtime and increases uptime
-
Quality products delivered on time
-
Removing human error
-
Assure compliance with regulations
Why is logistics important for manufacturing?
Logistics are an essential part of any business. They can help you achieve great success by helping you manage product flow from raw material to finished goods.
Logistics play a key role in reducing expenses and increasing efficiency.
Is automation necessary in manufacturing?
Not only is automation important for manufacturers, but it's also vital for service providers. It allows them provide faster and more efficient services. It reduces human errors and improves productivity, which in turn helps them lower their costs.
What is the responsibility of a manufacturing manager?
A manufacturing manager must ensure that all manufacturing processes are efficient and effective. They should also be aware of any problems within the company and act accordingly.
They should also be able communicate with other departments, such as sales or marketing.
They should also be knowledgeable about the latest trends in the industry so they can use this information for productivity and efficiency improvements.
What are the 7 R's of logistics?
The acronym 7R's of Logistic is an acronym that stands for seven fundamental principles of logistics management. It was published in 2004 by the International Association of Business Logisticians as part of their "Seven Principles of Logistics Management" series.
The acronym consists of the following letters:
-
Responsible - to ensure that all actions are within the legal requirements and are not detrimental to others.
-
Reliable – have faith in your ability and capability to keep promises.
-
Use resources effectively and sparingly.
-
Realistic - consider all aspects of operations, including cost-effectiveness and environmental impact.
-
Respectful: Treat others with fairness and equity
-
Reliable - Find ways to save money and increase your productivity.
-
Recognizable: Provide customers with value-added service
What does manufacturing industry mean?
Manufacturing Industries refers to businesses that manufacture products. Consumers are people who purchase these goods. This is accomplished by using a variety of processes, including production, distribution and retailing. They manufacture goods from raw materials using machines and other equipment. This includes all types manufactured goods such as clothing, building materials, furniture, electronics, tools and machinery.
Statistics
- Job #1 is delivering the ordered product according to specifications: color, size, brand, and quantity. (netsuite.com)
- According to a Statista study, U.S. businesses spent $1.63 trillion on logistics in 2019, moving goods from origin to end user through various supply chain network segments. (netsuite.com)
- According to the United Nations Industrial Development Organization (UNIDO), China is the top manufacturer worldwide by 2019 output, producing 28.7% of the total global manufacturing output, followed by the United States, Japan, Germany, and India.[52][53] (en.wikipedia.org)
- Many factories witnessed a 30% increase in output due to the shift to electric motors. (en.wikipedia.org)
- (2:04) MTO is a production technique wherein products are customized according to customer specifications, and production only starts after an order is received. (oracle.com)
External Links
How To
How to use Lean Manufacturing in the production of goods
Lean manufacturing is an approach to management that aims for efficiency and waste reduction. It was first developed in Japan in the 1970s/80s by Taiichi Ahno, who was awarded the Toyota Production System (TPS), award from KanjiToyoda, the founder of TPS. The first book published on lean manufacturing was titled "The Machine That Changed the World" written by Michael L. Watkins and published in 1990.
Lean manufacturing is often defined as a set of principles used to improve the quality, speed, and cost of products and services. It is about eliminating defects and waste from all stages of the value stream. Lean manufacturing is also known as just in time (JIT), zero defect total productive maintenance(TPM), and five-star (S). Lean manufacturing eliminates non-value-added tasks like inspection, rework, waiting.
Lean manufacturing can help companies improve their product quality and reduce costs. Additionally, it helps them achieve their goals more quickly and reduces employee turnover. Lean manufacturing is considered one of the most effective ways to manage the entire value chain, including suppliers, customers, distributors, retailers, and employees. Lean manufacturing can be found in many industries. Toyota's philosophy has been a key driver of success in many industries, including automobiles and electronics.
Lean manufacturing is based on five principles:
-
Define value - Find out what your business contributes to society, and what makes it different from other competitors.
-
Reduce Waste - Eliminate any activity that doesn't add value along the supply chain.
-
Create Flow - Make sure work runs smoothly without interruptions.
-
Standardize & simplify - Make processes consistent and repeatable.
-
Build Relationships- Develop personal relationships with both internal as well as external stakeholders.
Although lean manufacturing isn't a new concept in business, it has gained popularity due to renewed interest in the economy after the 2008 global financial crisis. Many businesses have adopted lean manufacturing techniques to help them become more competitive. Some economists even believe that lean manufacturing can be a key factor in economic recovery.
With many benefits, lean manufacturing is becoming more common in the automotive industry. These include improved customer satisfaction, reduced inventory levels, lower operating costs, increased productivity, and better overall safety.
Lean manufacturing can be applied to almost every aspect of an organization. This is because it ensures efficiency and effectiveness in all stages of the value chain.
There are three main types:
-
Just-in-Time Manufacturing: Also known as "pull systems", this type of lean manufacturing uses just-in-time manufacturing (JIT). JIT is a method in which components are assembled right at the moment of use, rather than being manufactured ahead of time. This approach reduces lead time, increases availability and reduces inventory.
-
Zero Defects Manufacturing - ZDM: ZDM focuses its efforts on making sure that no defective units leave a manufacturing facility. You should repair any part that needs to be repaired during an assembly line. This also applies to finished products that need minor repairs before being shipped.
-
Continuous Improvement (CI), also known as Continuous Improvement, aims at improving the efficiency of operations through continuous identification and improvement to minimize or eliminate waste. Continuous Improvement (CI) involves continuous improvement in processes, people, tools, and infrastructure.