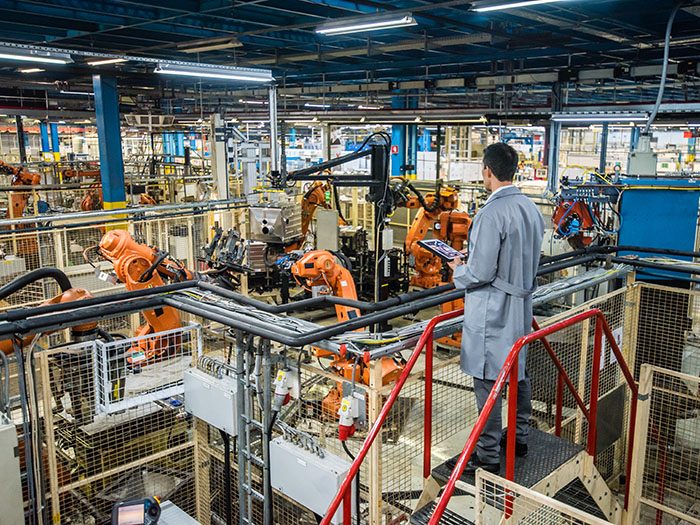
Increasing interest in sustainable development has driven manufacturing process industries to incorporate environmental management systems into their processes. These systems include formal monitoring, problem solving and continuous improvement. These systems are based in the ISO 14001 Standard, which requires that all organizations have an Environmental Management System to reduce waste, pollution, and improve the environment.
Lean Production techniques have been shown to improve environmental performance through reducing waste. Waste is any activity that absorbs resources. However, waste is not a source of value. It reduces the materials required for production. It has a negative effect upon the environment. Companies need to adopt aligned environmental management strategies in order reduce waste. Lean manufacturing techniques can help implement these strategies. These techniques include 5S - Just in Time, Kaizen Circle, Total Productive maintenance and Continuous improvement.
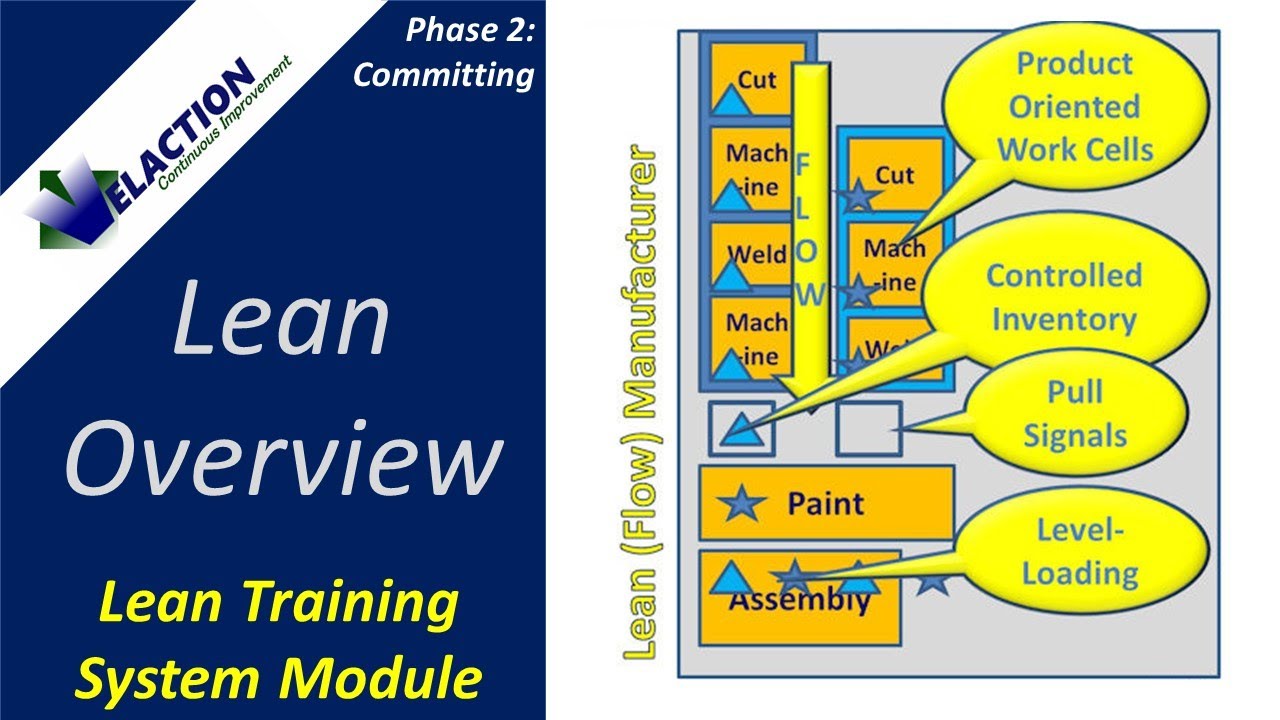
This study explores the link between Lean Production practices implementation and Environmental Management practices. We found a positive correlation between the concepts using multiple case studies. We identified several areas where LM and Green practices could be of benefit. These areas include supply, logistics, production, quality management, and environmental protection. These practices were applied in North Portugal companies. We also studied the factors that can affect the level and effectiveness of these practices. We examined, specifically, whether lean practices have a positive effect on the use of green practices.
A questionnaire was used to assess the level of implementation of LM/Green practices in these companies. The questionnaire consisted of a first part, which included questions about the company, and a second part, which included questions about environmental management practices. SEM analysis was used to analyze the first portion. The results were consistent with the data sample. The SEM approach revealed that 76% (or 76%) of the variance in environmental practices could be explained by the model.
The results of this test were consistent with what is published. However, the test results were in agreement with the literature. We need to rethink the role that pressure plays and how employees are involved in the implementation of green policies. This is because a passive attitude may result in poor results. It is important to acknowledge the significant contribution of practice bundles. Also, we found that green practices and LM have a positive influence on environmental performance.
We also found that the relationship between the implementation of lean management and the application of green practices was influenced by employee involvement. This is because LM involves employee engagement and participation in the production process, which leads to higher efficiency. This could also impact the relationship between lean practices, environmental performance, and other aspects of lean. This is why it is crucial to study the relationship between lean tools as well as environmental practices.
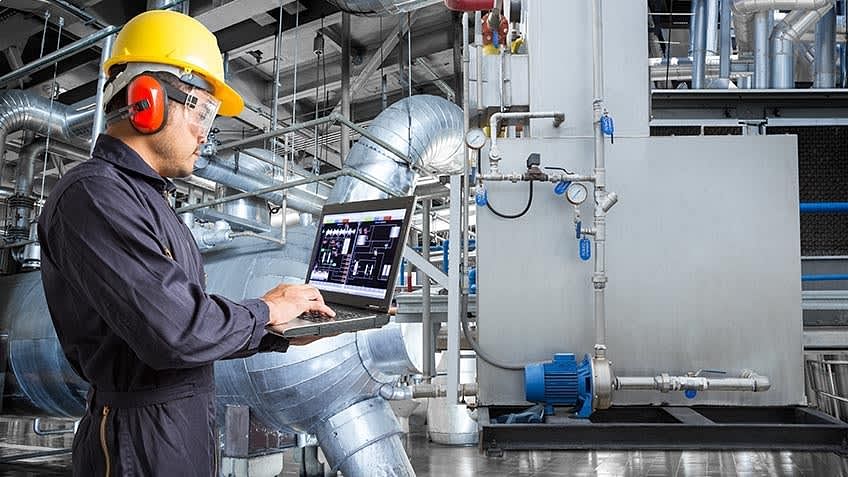
Most respondents believed that Lean Production technology reduced environmental impact. However, the majority of respondents stated that they do not recognize Lean and Green concepts as part of their strategic planning.
FAQ
What are manufacturing & logistics?
Manufacturing refers to the process of making goods using raw materials and machines. Logistics covers all aspects involved in managing supply chains, including procurement and production planning. Manufacturing and logistics can often be grouped together to describe a larger term that covers both the creation of products, and the delivery of them to customers.
What is the role of a production manager?
Production planners ensure that all project aspects are completed on time, within budget and within the scope. They also ensure that the product/service meets the client’s needs.
What are the jobs in logistics?
There are many kinds of jobs available within logistics. Here are some examples:
-
Warehouse workers – They load and unload pallets and trucks.
-
Transportation drivers – They drive trucks or trailers to transport goods and perform pick-ups.
-
Freight handlers are people who sort and pack freight into warehouses.
-
Inventory managers - These are responsible for overseeing the stock of goods in warehouses.
-
Sales representatives - They sell products.
-
Logistics coordinators - They organize and plan logistics operations.
-
Purchasing agents: They are responsible for purchasing goods and services to support company operations.
-
Customer service representatives – They answer emails and phone calls from customers.
-
Shipping clerks: They process shipping requests and issue bills.
-
Order fillers – They fill orders based upon what was ordered and shipped.
-
Quality control inspectors: They inspect outgoing and incoming products for any defects.
-
Other - Logistics has many other job opportunities, including transportation supervisors, logistics specialists, and cargo specialists.
How can I find out more about manufacturing?
Experience is the best way for you to learn about manufacturing. However, if that's not possible, you can always read books or watch educational videos.
Statistics
- According to a Statista study, U.S. businesses spent $1.63 trillion on logistics in 2019, moving goods from origin to end user through various supply chain network segments. (netsuite.com)
- In 2021, an estimated 12.1 million Americans work in the manufacturing sector.6 (investopedia.com)
- You can multiply the result by 100 to get the total percent of monthly overhead. (investopedia.com)
- According to the United Nations Industrial Development Organization (UNIDO), China is the top manufacturer worldwide by 2019 output, producing 28.7% of the total global manufacturing output, followed by the United States, Japan, Germany, and India.[52][53] (en.wikipedia.org)
- (2:04) MTO is a production technique wherein products are customized according to customer specifications, and production only starts after an order is received. (oracle.com)
External Links
How To
How to Use the Just In Time Method in Production
Just-in-time (JIT) is a method that is used to reduce costs and maximize efficiency in business processes. It is a process where you get the right amount of resources at the right moment when they are needed. This means you only pay what you use. Frederick Taylor first coined this term while working in the early 1900s as a foreman. He saw how overtime was paid to workers for work that was delayed. He then concluded that if he could ensure that workers had enough time to do their job before starting to work, this would improve productivity.
JIT is about planning ahead. You should have all the necessary resources ready to go so that you don’t waste money. Also, you should look at the whole project from start-to-finish and make sure you have the resources necessary to address any issues. You will have the resources and people to solve any problems you anticipate. This will prevent you from spending extra money on unnecessary things.
There are many JIT methods.
-
Demand-driven JIT: You order the parts and materials you need for your project every other day. This will allow for you to track the material that you have left after using it. It will also allow you to predict how long it takes to produce more.
-
Inventory-based : You can stock the materials you need in advance. This allows you to predict how much you can expect to sell.
-
Project-driven: This method allows you to set aside enough funds for your project. When you know how much you need, you'll purchase the appropriate amount of materials.
-
Resource-based JIT : This is probably the most popular type of JIT. Here you can allocate certain resources based purely on demand. For example, if there is a lot of work coming in, you will have more people assigned to them. You'll have fewer orders if you have fewer.
-
Cost-based: This is similar to resource-based, except that here you're not just concerned about how many people you have but how much each person costs.
-
Price-based: This is very similar to cost-based, except that instead of looking at how much each individual worker costs, you look at the overall price of the company.
-
Material-based: This is very similar to cost-based but instead of looking at total costs of the company you are concerned with how many raw materials you use on an average.
-
Time-based: Another variation of resource-based JIT. Instead of focusing on how much each employee costs, you focus on how long it takes to complete the project.
-
Quality-based JIT - This is another form of resource-based JIT. Instead of focusing on the cost of each worker or how long it takes, think about how high quality your product is.
-
Value-based JIT: One of the most recent forms of JIT. In this instance, you are not concerned about the product's performance or meeting customer expectations. Instead, your goal is to add value to the market.
-
Stock-based: This stock-based method focuses on the actual quantity of products being made at any given time. It is used when production goals are met while inventory is kept to a minimum.
-
Just-intime (JIT), planning is a combination JIT management and supply chain management. This refers to the scheduling of the delivery of components as soon after they are ordered. This is important as it reduces lead time and increases throughput.