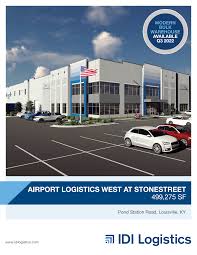
What is supply chain management? The supply chain management process is cross-functional and focuses on the management relationships throughout the entire supply network. Supply chain management helps improve business performance by improving operational and financial performance. This article will outline the basic concepts of supply-chain management and how they can benefit your organization. Let's dive in! What is supply chains management? What is supply chain management? Why is it so important? These are just a few ways it can help your business.
Management of supply chain relationships is the goal of supply chain management
Products companies must consider how to acquire raw materials, create parts, and distribute finished products. The physical flow is initiated by a supplier. From there, it moves on to various stages, including a distributor, manufacturer, retailer, and finally to the consumer. Some supply chains skip steps but the actual goods must be moved from one location to another, kept for a certain time, and then delivered to the end consumer. This process requires organization and planning.
Integrating all business functions is essential for successful supply chain management. Vendors and suppliers need to have open communication. Information sharing helps both sides understand each other, reduce costs and improve quality. Collaboration across the supply chain improves communication and collaboration, which in turn benefits both sides. The customer should be aware of the company's operational process, and the vendor must know how to deliver emergency materials. Particularly important when selling perishable goods, lead times are critical.
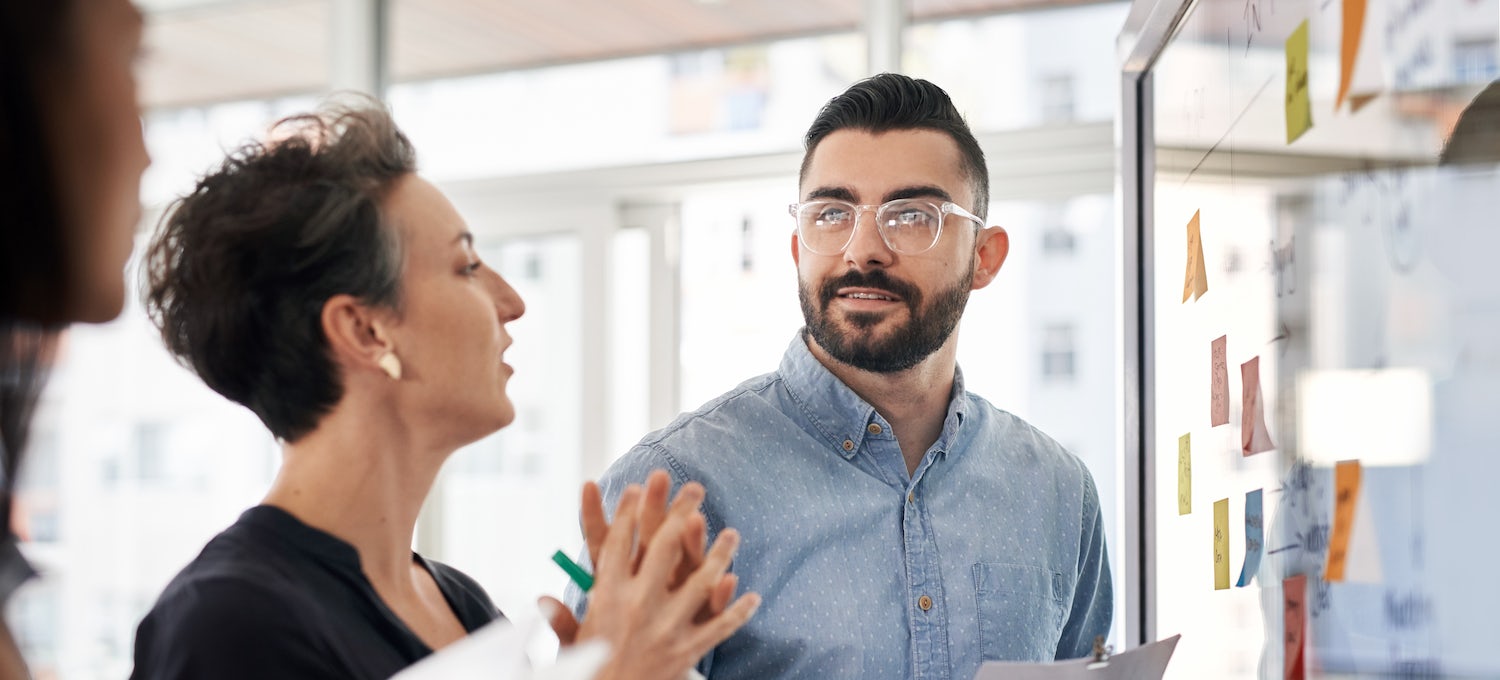
It's cross-functional.
When it comes to a company’s supply chains, there are many critical cross-functional elements that must be taken into consideration. Suppliers must be able deliver goods on-time to ensure a successful supply network. This is why it is important to coordinate with them. Follow these steps to avoid any problems. Companies will be able to improve their efficiency and save money by following these steps.
Management must also understand the interdependencies between the supply chain. This will allow them to improve the overall system's profitability. It is crucial to create guidelines that will allow everyone to reap the benefits from improved processes. In some cases, parties in the supply chain may not see the benefits from an improved process unless it is based on a common measurement system. It might be deemed ineffective if the value isn't captured.
It reduces operating and maintenance costs
Streamlining ordering processes can be one of the best ways reduce operating costs. Your employees are less likely to be confused by multiple requisitions and order too much product if you use one software platform. A process for approval can be set up to limit the quantity of goods ordered. This will help to lower operating costs. A simplified software system will not only eliminate mistakes and confusion, but it will also enable you to keep track of your inventory, order only what you need, and block shipments if they aren't needed.
Another method to reduce operating costs is by improving communication between warehouse employees. The first step is to examine the current workflow and find any bottlenecks. Reduce transportation costs by consolidating shipments or using dedicated transportation services. Operating costs will drop dramatically if you can do this. This will help you not only lower your transport costs but also speed up the delivery of your products.
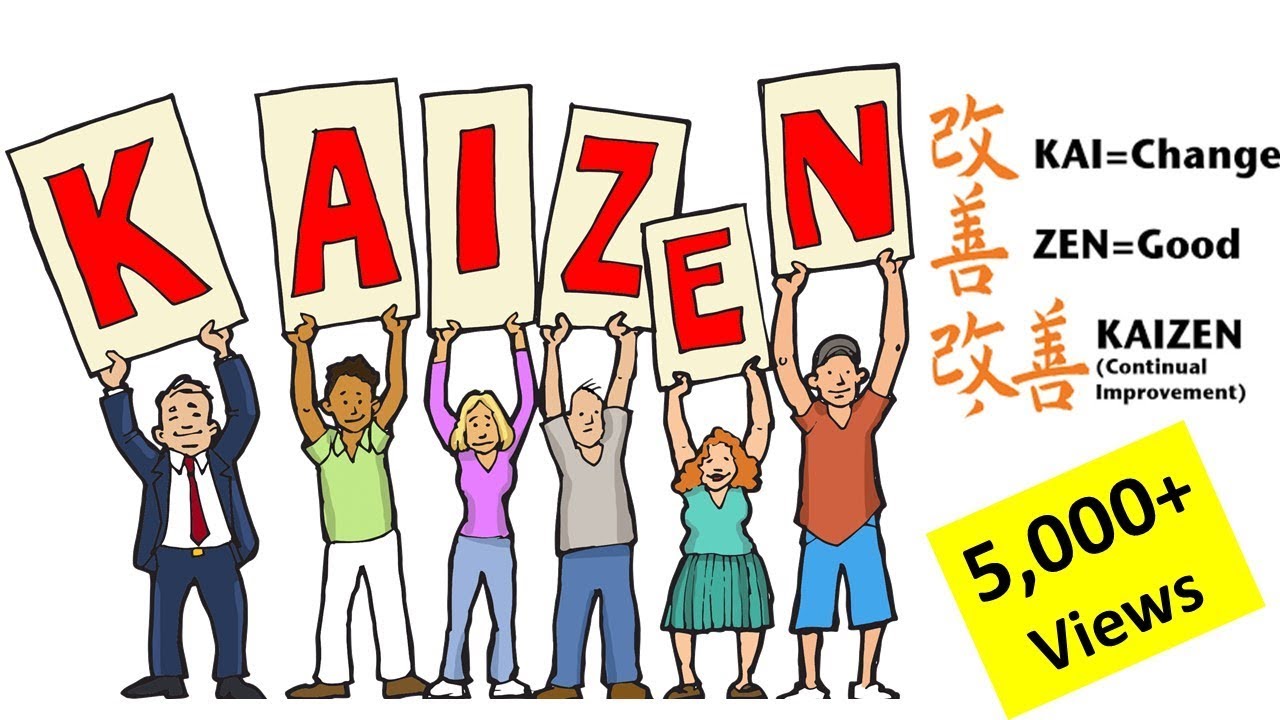
It improves financial position
In many ways, supply chain management can help improve a business’s financial performance. Supply chain managers who are skilled in managing supply chains can help to reduce production costs and maximize variable costs. The ability to control costs increases profit margins. Another benefit is the improvement of cash flow. An earlier delivery of products can allow a company to invoice customers sooner, and reduce the need for costly building space. Also, a better supply channel reduces fixed asset costs.
The Statement of Shareholders' Equity (SSE) is a key financial statement that summarizes the ownership portion of a company. An improvement in a company's supply chain could increase its after-tax cash flow by 8.5%. An improvement in supply chain performance can help a company reduce costs by up to 10% and improve customer satisfaction. Supply chain management can improve financial performance and lead to greater operational efficiencies, which in turn leads to higher profits.
FAQ
What does warehouse mean?
Warehouses and storage facilities are where goods are kept before being sold. You can have it indoors or outdoors. In some cases it could be both indoors and outdoors.
How can overproduction in manufacturing be reduced?
In order to reduce excess production, you need to develop better inventory management methods. This would reduce time spent on activities such as purchasing, stocking, and maintaining excess stock. This could help us free up our time for other productive tasks.
One way to do this is to adopt a Kanban system. A Kanban board is a visual display used to track work in progress. Kanban systems allow work items to move through different states until they reach their final destination. Each state represents a different priority level.
For instance, when work moves from one stage to another, the current task is complete enough to be moved to the next stage. A task that is still in the initial stages of a process will be considered complete until it moves on to the next stage.
This allows for work to continue moving forward, while also ensuring that there is no work left behind. A Kanban board allows managers to monitor how much work is being completed at any given moment. This data allows them adjust their workflow based upon real-time data.
Lean manufacturing can also be used to reduce inventory levels. Lean manufacturing seeks to eliminate waste from every step of the production cycle. Waste includes anything that does not add value to the product. These are some of the most common types.
-
Overproduction
-
Inventory
-
Packaging that is not necessary
-
Overstock materials
By implementing these ideas, manufacturers can improve efficiency and cut costs.
How is a production manager different from a producer planner?
The main difference between a production planner and a project manager is that a project manager is usually the person who plans and organizes the entire project, whereas a production planner is mainly involved in the planning stage of the project.
What skills should a production planner have?
Production planners must be flexible, organized, and able handle multiple tasks. Also, you must be able and willing to communicate with clients and coworkers.
What are the responsibilities of a logistic manager?
Logistics managers make sure all goods are delivered on schedule and without damage. This is done through his/her expertise and knowledge about the company's product range. He/she must also ensure sufficient stock to meet the demand.
What are the responsibilities of a production planner
A production planner ensures all aspects of the project are delivered on time, within budget, and within scope. They also ensure the quality of the product and service meets the client's requirements.
How can manufacturing prevent production bottlenecks?
Avoiding production bottlenecks is as simple as keeping all processes running smoothly, from the time an order is received until the product ships.
This includes both planning for capacity and quality control.
Continuous improvement techniques such Six Sigma can help you achieve this.
Six Sigma Management System is a method to increase quality and reduce waste throughout your organization.
It's all about eliminating variation and creating consistency in work.
Statistics
- (2:04) MTO is a production technique wherein products are customized according to customer specifications, and production only starts after an order is received. (oracle.com)
- [54][55] These are the top 50 countries by the total value of manufacturing output in US dollars for its noted year according to World Bank.[56] (en.wikipedia.org)
- In the United States, for example, manufacturing makes up 15% of the economic output. (twi-global.com)
- Many factories witnessed a 30% increase in output due to the shift to electric motors. (en.wikipedia.org)
- According to the United Nations Industrial Development Organization (UNIDO), China is the top manufacturer worldwide by 2019 output, producing 28.7% of the total global manufacturing output, followed by the United States, Japan, Germany, and India.[52][53] (en.wikipedia.org)
External Links
How To
How to Use the Just In Time Method in Production
Just-in time (JIT), is a process that reduces costs and increases efficiency in business operations. It's a way to ensure that you get the right resources at just the right time. This means that you only pay the amount you actually use. Frederick Taylor, a 1900s foreman, first coined the term. He saw how overtime was paid to workers for work that was delayed. He realized that workers should have enough time to complete their jobs before they begin work. This would help increase productivity.
JIT is an acronym that means you need to plan ahead so you don’t waste your money. Look at your entire project, from start to end. Make sure you have enough resources in place to deal with any unexpected problems. You will have the resources and people to solve any problems you anticipate. This way, you won't end up paying extra money for things that weren't really necessary.
There are several types of JIT techniques:
-
Demand-driven JIT: You order the parts and materials you need for your project every other day. This will allow you to track how much material you have left over after using it. This will allow to you estimate the time it will take for more to be produced.
-
Inventory-based: This type allows you to stock the materials needed for your projects ahead of time. This allows you to predict how much you can expect to sell.
-
Project-driven: This is an approach where you set aside enough funds to cover the cost of your project. If you know the amount you require, you can buy the materials you need.
-
Resource-based JIT : This is probably the most popular type of JIT. Here, you allocate certain resources based on demand. For example, if there is a lot of work coming in, you will have more people assigned to them. If you don’t have many orders you will assign less people to the work.
-
Cost-based: This is the same as resource-based except that you don't care how many people there are but how much each one of them costs.
-
Price-based: This is similar to cost-based but instead of looking at individual workers' salaries, you look at the total company price.
-
Material-based: This is very similar to cost-based but instead of looking at total costs of the company you are concerned with how many raw materials you use on an average.
-
Time-based JIT is another form of resource-based JIT. Instead of focusing on the cost of each employee, you will focus on the time it takes to complete a project.
-
Quality-based JIT: Another variation on resource-based JIT. Instead of focusing on the cost of each worker or how long it takes, think about how high quality your product is.
-
Value-based: This is one of the newest forms of JIT. In this scenario, you're not concerned about how products perform or whether customers expect them to meet their expectations. Instead, your focus is on the value you bring to the market.
-
Stock-based: This inventory-based approach focuses on how many items are being produced at any one time. It's useful when you want maximum production and minimal inventory.
-
Just-intime (JIT), planning is a combination JIT management and supply chain management. It refers to the process of scheduling the delivery of components as soon as they are ordered. It is essential because it reduces lead-times and increases throughput.