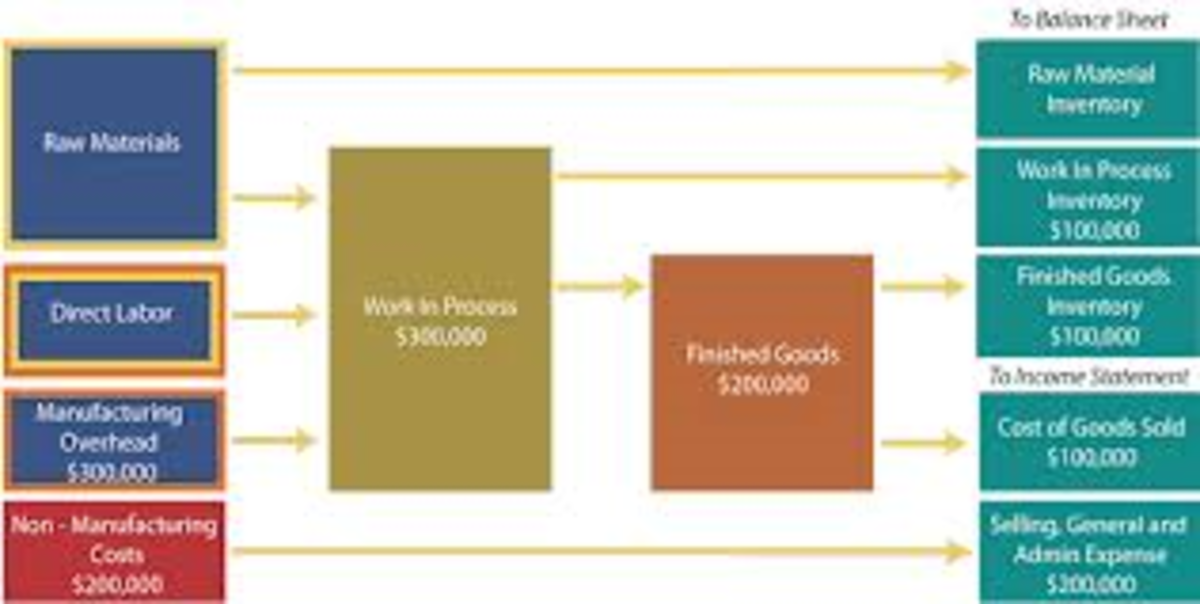
Whether you are looking for a new career, or want to enhance your skills to keep up with the changes in the business landscape, supply chain analytics courses can help you find your way. It is an essential part of every organization's operations. The tools that are used to analyze and collect data can help organizations meet the expectations of their customers.
You will learn how to use supply chain analytics to understand voluminous data, to make sense of it, and to identify patterns that can guide your future decisions. It can help identify the most efficient actions, which can lead to more precise and quicker decisions. It can help you increase your working capital. It can help you identify the inventory levels needed to provide your customers with the services they expect. It can help you reduce potential risks.
There are always new developments in the global marketplace, so it is important to keep up with current trends. Data is being used by many companies to improve the efficiency of their supply chain. Data can also be used for forecasting future demand. This course teaches how to analyze supply chains using predictive analytics and data mining. These techniques can help you develop inventory policies, forecast future demand, and perform predictive maintenance.
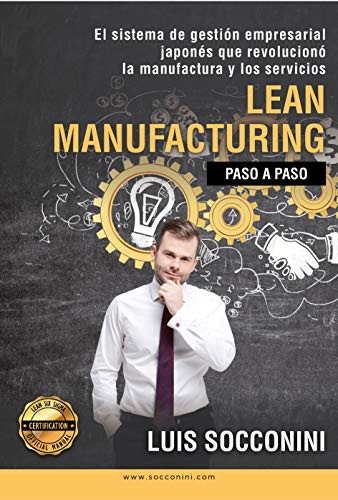
This course also covers how supply chains are composed of multiple parts and how these parts can all be combined to create one system. This includes logistics planning, shipping and import procedures, and containerisation. It also covers shipping scheduling, inventory management, air cargo management, and shipment management. It also contains information about data cleansing, visualization, and other topics.
You will also be introduced to machine learning, which is a field that uses algorithms to find patterns in data. This is particularly useful for the supply chain industry. It is used to perform customer segmentation, and can be used with Python to develop predictive models.
The course also teaches about ethics and the key drivers of supply chain management. It also explains basic concepts of inventory management and supplier selection as well as how lean six sigma can be applied. It discusses the importance of flexibility, innovation, and adaptability.
The supply chain analytics courses will give you an understanding of why data-driven decision making is so important in today’s business environment. It helps you to make better decisions, which can save money and increase efficiency. You can also use it to analyze your data and find ways to improve your company. This can help you improve your bottom line and is an essential component of any supply chain management course.
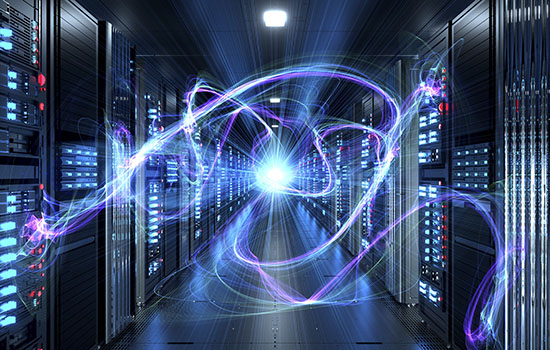
The course is taught by faculty with real-world experience in supply chain management. It will provide an overview and teach you how to select the right technology for your requirements. It will also show you the various models of supply chain management, including inventory management. It will also explain the most popular software tools used to analyze data and how they can be used to improve supply chain efficiency.
FAQ
What is manufacturing and logistics?
Manufacturing refers the process of producing goods from raw materials through machines and processes. Logistics includes all aspects related to supply chain management, such as procurement, distribution planning, inventory control and transportation. Manufacturing and logistics can often be grouped together to describe a larger term that covers both the creation of products, and the delivery of them to customers.
Do we need to know about Manufacturing Processes before learning about Logistics?
No. No. But, being familiar with manufacturing processes will give you a better understanding about how logistics works.
What is production planning?
Production Planning involves developing a plan for all aspects of the production, including scheduling, budgeting, casting, crew, location, equipment, props, etc. It is important to have everything ready and planned before you start shooting. It should also provide information about how best to produce the best results while on set. This includes information on shooting times, locations, cast lists and crew details.
The first step is to decide what you want. You may already know where you want the film to be shot, or perhaps you have specific locations and sets you wish to use. Once you have identified the scenes and locations, you can start to determine which elements are required for each scene. If you decide you need a car and don't know what model to choose, this could be an example. This is where you can look up car models online and narrow down your options by choosing from different makes and models.
Once you have found the right vehicle, you can think about adding accessories. Do you have people who need to be seated in the front seat? Maybe you need someone to move around in the back. You may want to change the interior's color from black or white. These questions can help you decide the right look for your car. Another thing you can do is think about what type of shots are desired. Will you be filming close-ups or wide angles? Maybe you want to show the engine and the steering wheel. These factors will help you determine which car style you want to film.
Once you have made all the necessary decisions, you can start to create a schedule. You will know when you should start and when you should finish shooting. The schedule will show you when to get there, what time to leave, and when to return home. Everyone will know what they need and when. If you need to hire extra staff, you can make sure you book them in advance. There is no point in hiring someone who won't turn up because you didn't let him know.
Your schedule will also have to be adjusted to reflect the number of days required to film. Some projects can be completed in a matter of days or weeks. Others may take several days. You should consider whether you will need more than one shot per week when creating your schedule. Multiple takes at the same place will result in higher costs and longer completion times. You can't be certain if you will need multiple takes so it is better not to shoot too many.
Budgeting is another crucial aspect of production plan. A realistic budget will help you work within your means. You can always lower the budget if you encounter unexpected problems. But, don't underestimate how much money you'll spend. If you underestimate how much something costs, you'll have less money to pay for other items.
Production planning is a complicated process. But once you understand how everything works together, it becomes much easier to plan future project.
What are the products of logistics?
Logistics refers to all activities that involve moving goods from A to B.
These include all aspects related to transport such as packaging, loading and transporting, storing, transporting, unloading and warehousing inventory management, customer service. Distribution, returns, recycling are some of the options.
Logisticians ensure that the right product reaches the right place at the right time and under safe conditions. They assist companies with their supply chain efficiency through information on demand forecasts. Stock levels, production times, and availability.
They can also track shipments in transit and monitor quality standards.
What type of jobs is there in logistics
Logistics can offer many different jobs. These are some of the jobs available in logistics:
-
Warehouse workers – They load, unload and transport pallets and trucks.
-
Transportation drivers – These drivers drive trucks and wagons to transport goods and pick up the goods.
-
Freight handlers – They sort and package freight at warehouses.
-
Inventory managers – These people oversee inventory at warehouses.
-
Sales reps are people who sell products to customers.
-
Logistics coordinators are responsible for organizing and planning logistics operations.
-
Purchasing agents: They are responsible for purchasing goods and services to support company operations.
-
Customer service representatives - They answer calls and emails from customers.
-
Shipping clerks: They process shipping requests and issue bills.
-
Order fillers - They fill orders based on what is ordered and shipped.
-
Quality control inspectors (QCI) - They inspect all incoming and departing products for potential defects.
-
Other - Logistics has many other job opportunities, including transportation supervisors, logistics specialists, and cargo specialists.
What is the difference between a production planner and a project manager?
The major difference between a Production Planner and a Project Manager is that a Project Manager is often the person responsible for organizing and planning the entire project. While a Production Planner is involved mainly in the planning stage,
What are the 7 R's of logistics?
The acronym 7R's of Logistic is an acronym that stands for seven fundamental principles of logistics management. It was created by the International Association of Business Logisticians and published in 2004 under its "Seven Principles of Logistics Management".
The following letters make up the acronym:
-
Responsible – ensure that all actions are legal and don't cause harm to anyone else.
-
Reliable - You can have confidence that you will fulfill your promises.
-
Use resources effectively and sparingly.
-
Realistic - Take into consideration all aspects of operations including cost-effectiveness, environmental impact, and other factors.
-
Respectful - treat people fairly and equitably.
-
Reliable - Find ways to save money and increase your productivity.
-
Recognizable - Provide value-added services to customers
Statistics
- Many factories witnessed a 30% increase in output due to the shift to electric motors. (en.wikipedia.org)
- (2:04) MTO is a production technique wherein products are customized according to customer specifications, and production only starts after an order is received. (oracle.com)
- According to a Statista study, U.S. businesses spent $1.63 trillion on logistics in 2019, moving goods from origin to end user through various supply chain network segments. (netsuite.com)
- In 2021, an estimated 12.1 million Americans work in the manufacturing sector.6 (investopedia.com)
- According to the United Nations Industrial Development Organization (UNIDO), China is the top manufacturer worldwide by 2019 output, producing 28.7% of the total global manufacturing output, followed by the United States, Japan, Germany, and India.[52][53] (en.wikipedia.org)
External Links
How To
Six Sigma in Manufacturing
Six Sigma is defined by "the application SPC (statistical process control) techniques to achieve continuous improvements." Motorola's Quality Improvement Department created Six Sigma at their Tokyo plant, Japan in 1986. Six Sigma is a method to improve quality through standardization and elimination of defects. Many companies have adopted this method in recent years. They believe there is no such thing a perfect product or service. Six Sigma's primary goal is to reduce variation from the average value of production. If you take a sample and compare it with the average, you will be able to determine how much of the production process is different from the norm. If there is a significant deviation from the norm, you will know that something needs to change.
Understanding how variability works in your company is the first step to Six Sigma. Once you have this understanding, you will need to identify sources and causes of variation. These variations can also be classified as random or systematic. Random variations occur when people make mistakes; systematic ones are caused by factors outside the process itself. For example, if you're making widgets, and some of them fall off the assembly line, those would be considered random variations. If however, you notice that each time you assemble a widget it falls apart in exactly the same spot, that is a problem.
Once you identify the problem areas, it is time to create solutions. This could mean changing your approach or redesigning the entire process. To verify that the changes have worked, you need to test them again. If they don’t work, you’ll need to go back and rework the plan.