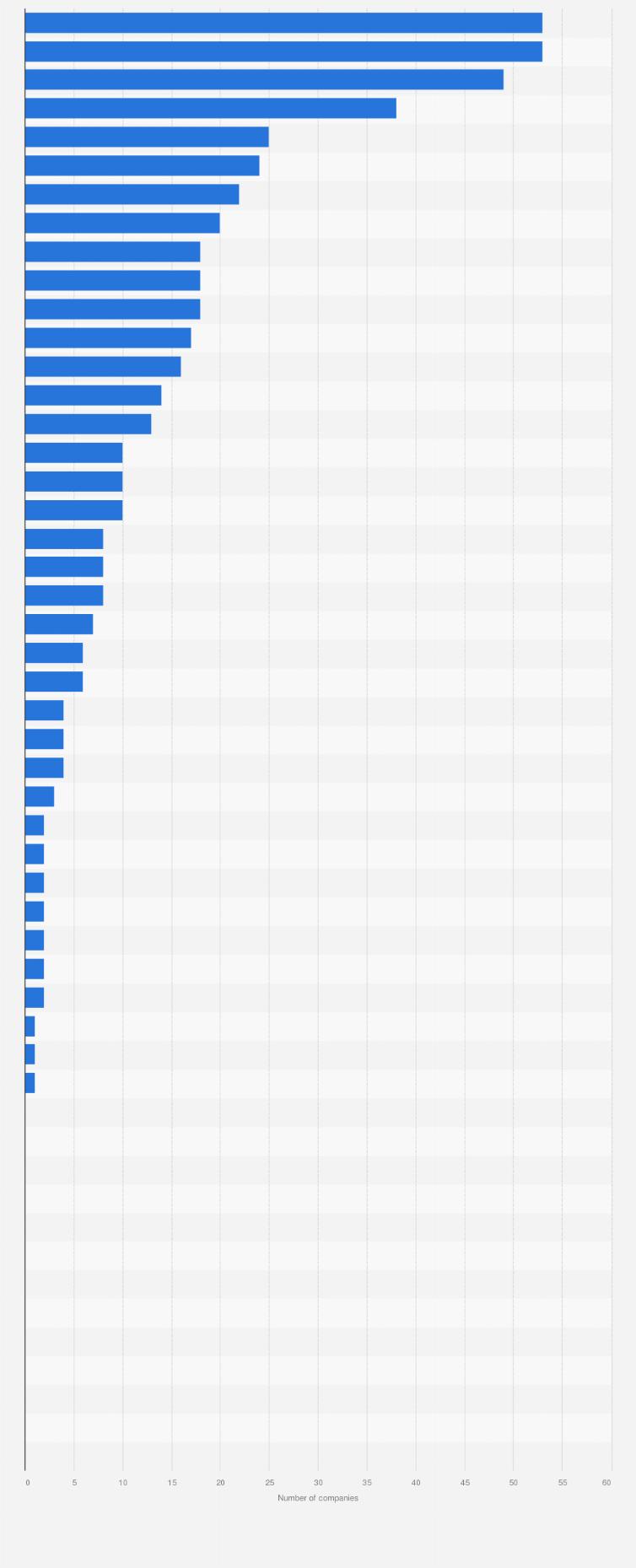
Looking for an industrial engineering job? Continue reading to learn more about the types of jobs available. This article will discuss the types and average salaries of various jobs as well as the education requirements. We'll also discuss what skills are required, and where to look for these jobs. You can then apply for the job that appeals to you the most! Good luck! You should carefully read the job description before applying for an industrial engineer job.
Job description
Industrial engineers are not for the weak of heart. The work entails applying engineering principles and technology to improve overall production processes and layouts in companies. This engineer is responsible in developing analytics and tools that assist companies with monitoring their costs and scheduling. The engineer also reviews production data to find areas for improvement, compiles equipment and materials lists, cost analyses, production cost estimates, and buy orders before implementing any new projects.
An undergraduate degree in mechanical engineer is required for a job as an industrial engineering specialist. This field requires a broad knowledge of engineering principles and practices, as well as a knack for problem-solving. An industrial engineer must combine technical knowledge with an understanding and appreciation of human capabilities. Industrial engineers should be well-organized, have strong analytical abilities, and communicate well. They are responsible both for improving production and for managing warehouses or factories.
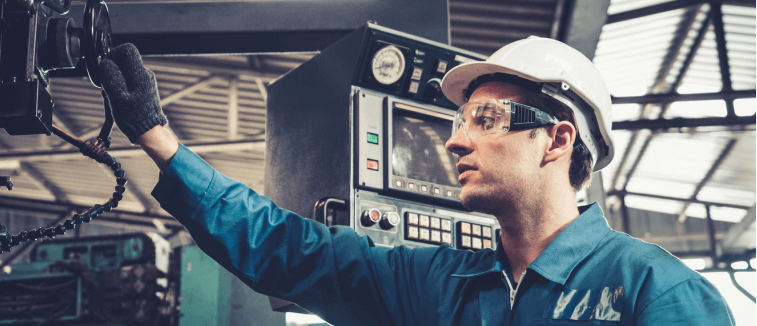
Salary range
Industrial engineers can earn a range of salaries depending on their experience. The starting salary is around $85,000 but can rise to as high as $100,000 depending on experience. The following table shows the average salary for industrial engineers according to experience. Ventura, California is home to an Entry Level Engineer who can make approximately $86,000 per annum. For an experienced Industrial Engineer, the salary range is $85,000 to $100,000 per year. An optional four-year degree is required for Project Engineers.
The average income for an industrial engineer varies according to where you live, your industry, and your years of experience. New York's industrial engineers can expect to earn between $60,700 and $140,000 annually. Although it is hard to see the upward trend in salaries, national averages have increased by more than 40% over the past 10 years. They are expected to continue rising. Monster's Salary Tools will give you more information on the range of salaries in your area.
Education Required
Although it is sometimes required to work for government contracts, licensing is not usually necessary for industrial engineers. License is not necessary for industrial engineers. For professional licensure, however, they will need to have relevant experience and a degree from an institution that is accredited. Industrial engineers often work in factories and offices. Many industrial engineers work in the aerospace and engineering industries, as well as in medical and control instrument manufacturing.
Many industrial engineers prefer to work as interns in their college years. This is a great way to gain valuable experience. Industrial engineering jobs at entry level don't require any professional experience. However, having more experience in engineering can give you an advantage over your competitors. Internships are also a good option if you plan to work for a government agency or another organization. Additionally to internships and security clearance, industrial engineers may also require it.
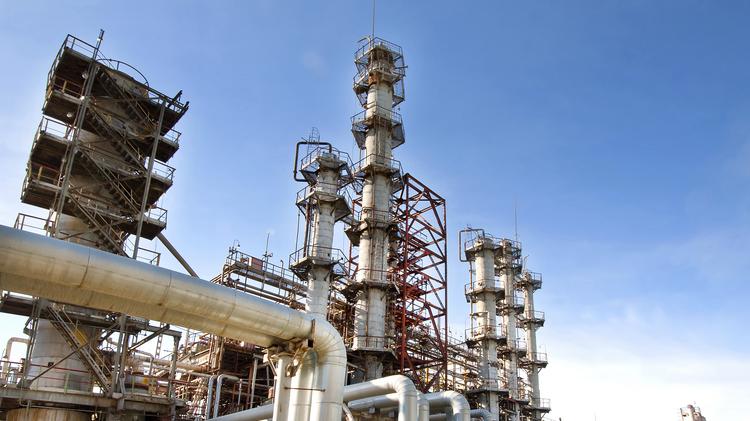
Places
Many industrial engineering jobs are available and highly rewarding. Entry-level positions in the field typically involve completing calculations, installing monitoring and testing devices, and documenting findings. They may also assist in the creation of budgets and tracking metrics. A lot of standing is required for industrial engineers. Industrial engineers must communicate clearly. Sometimes they work with a more senior engineer.
Industrial engineers collaborate with companies to design efficient production processes that require the least energy and resource. Their primary objective is to maximize efficiency and reduce costs while maintaining high labor productivity. Industrial engineers are employed in factories and offices to make improvements to the organization's operations. Entry-level positions in industrial engineering require a bachelor's degree in industrial engineering or a related field. According to the Bureau of Labor Statistics the average salary for industrial engineers is $95,300 by 2021.
FAQ
Why is logistics so important in manufacturing?
Logistics is an integral part of every business. They help you achieve great results by helping you manage all aspects of product flow, from raw materials to finished goods.
Logistics also play a major role in reducing costs and increasing efficiency.
What is the responsibility of a manufacturing manager?
A manufacturing manager has to ensure that all manufacturing processes work efficiently and effectively. They should be alert for any potential problems in the company and react accordingly.
They should also learn how to communicate effectively with other departments, including sales and marketing.
They should be informed about industry trends and be able make use of this information to improve their productivity and efficiency.
What are the responsibilities of a production planner
A production planner ensures all aspects of the project are delivered on time, within budget, and within scope. They ensure that the product or service is of high quality and meets client requirements.
Is it possible to automate certain parts of manufacturing
Yes! Since ancient times, automation has been in existence. The Egyptians invent the wheel thousands of year ago. Robots are now used to assist us in assembly lines.
Actually, robotics can be used in manufacturing for many purposes. They include:
-
Automated assembly line robots
-
Robot welding
-
Robot painting
-
Robotics inspection
-
Robots that create products
Automation can be applied to manufacturing in many other ways. 3D printing, for example, allows us to create custom products without waiting for them to be made.
How can manufacturing excess production be decreased?
Improved inventory management is the key to reducing overproduction. This would reduce the amount of time spent on unnecessary activities such as purchasing, storing, and maintaining excess stock. This could help us free up our time for other productive tasks.
A Kanban system is one way to achieve this. A Kanban Board is a visual display that tracks work progress. In a Kanban system, work items move through a sequence of states until they reach their final destination. Each state has a different priority level.
If work is moving from one stage to the other, then the current task can be completed and moved on to the next. However, if a task is still at the beginning stages, it will remain so until it reaches the end of the process.
This allows for work to continue moving forward, while also ensuring that there is no work left behind. Managers can see how much work has been done and the status of each task at any time with a Kanban Board. This data allows them adjust their workflow based upon real-time data.
Lean manufacturing is another option to control inventory levels. Lean manufacturing works to eliminate waste throughout every stage of the production chain. Anything that doesn't add value to the product is considered waste. The following are examples of common waste types:
-
Overproduction
-
Inventory
-
Unnecessary packaging
-
Materials in excess
By implementing these ideas, manufacturers can improve efficiency and cut costs.
What can I do to learn more about manufacturing?
Experience is the best way for you to learn about manufacturing. You can also read educational videos or take classes if this isn't possible.
Statistics
- Job #1 is delivering the ordered product according to specifications: color, size, brand, and quantity. (netsuite.com)
- According to a Statista study, U.S. businesses spent $1.63 trillion on logistics in 2019, moving goods from origin to end user through various supply chain network segments. (netsuite.com)
- [54][55] These are the top 50 countries by the total value of manufacturing output in US dollars for its noted year according to World Bank.[56] (en.wikipedia.org)
- In 2021, an estimated 12.1 million Americans work in the manufacturing sector.6 (investopedia.com)
- Many factories witnessed a 30% increase in output due to the shift to electric motors. (en.wikipedia.org)
External Links
How To
How to use Lean Manufacturing in the production of goods
Lean manufacturing is an approach to management that aims for efficiency and waste reduction. It was developed by Taiichi Okono in Japan, during the 1970s & 1980s. TPS founder Kanji Takoda awarded him the Toyota Production System Award (TPS). Michael L. Watkins published the first book on lean manufacturing in 1990.
Lean manufacturing, often described as a set and practice of principles, is aimed at improving the quality, speed, cost, and efficiency of products, services, and other activities. It is about eliminating defects and waste from all stages of the value stream. Lean manufacturing can be described as just-in–time (JIT), total productive maintenance, zero defect (TPM), or even 5S. Lean manufacturing focuses on eliminating non-value-added activities such as rework, inspection, and waiting.
Lean manufacturing is a way for companies to achieve their goals faster, improve product quality, and lower costs. Lean Manufacturing is one of the most efficient ways to manage the entire value chains, including suppliers and customers as well distributors and retailers. Lean manufacturing practices are widespread in many industries. Toyota's philosophy, for example, is what has enabled it to be successful in electronics, automobiles, medical devices, healthcare and chemical engineering as well as paper and food.
Five principles are the basis of lean manufacturing:
-
Define Value - Identify the value your business adds to society and what makes you different from competitors.
-
Reduce Waste – Eliminate all activities that don't add value throughout the supply chain.
-
Create Flow. Ensure that your work is uninterrupted and flows seamlessly.
-
Standardize and Simplify – Make processes as consistent, repeatable, and as simple as possible.
-
Build relationships - Develop and maintain personal relationships with both your internal and external stakeholders.
Lean manufacturing is not a new concept, but it has been gaining popularity over the last few years due to a renewed interest in the economy following the global financial crisis of 2008. Many businesses have adopted lean production techniques to make them more competitive. Economists think that lean manufacturing is a crucial factor in economic recovery.
Lean manufacturing is now becoming a common practice in the automotive industry, with many benefits. These benefits include increased customer satisfaction, reduced inventory levels and lower operating costs.
You can apply Lean Manufacturing to virtually any aspect of your organization. However, it is particularly useful when applied to the production side of an organization because it ensures that all steps in the value chain are efficient and effective.
There are three main types:
-
Just-in-Time Manufacturing: Also known as "pull systems", this type of lean manufacturing uses just-in-time manufacturing (JIT). JIT is a method in which components are assembled right at the moment of use, rather than being manufactured ahead of time. This strategy aims to decrease lead times, increase availability of parts and reduce inventory.
-
Zero Defects Manufacturing, (ZDM): ZDM is focused on ensuring that no defective products leave the manufacturing facility. You should repair any part that needs to be repaired during an assembly line. This applies to finished products, which may need minor repairs before they are shipped.
-
Continuous Improvement (CI: Continuous improvement aims to increase the efficiency of operations by constantly identifying and making improvements to reduce or eliminate waste. Continuous improvement involves continuous improvement of processes and people as well as tools.