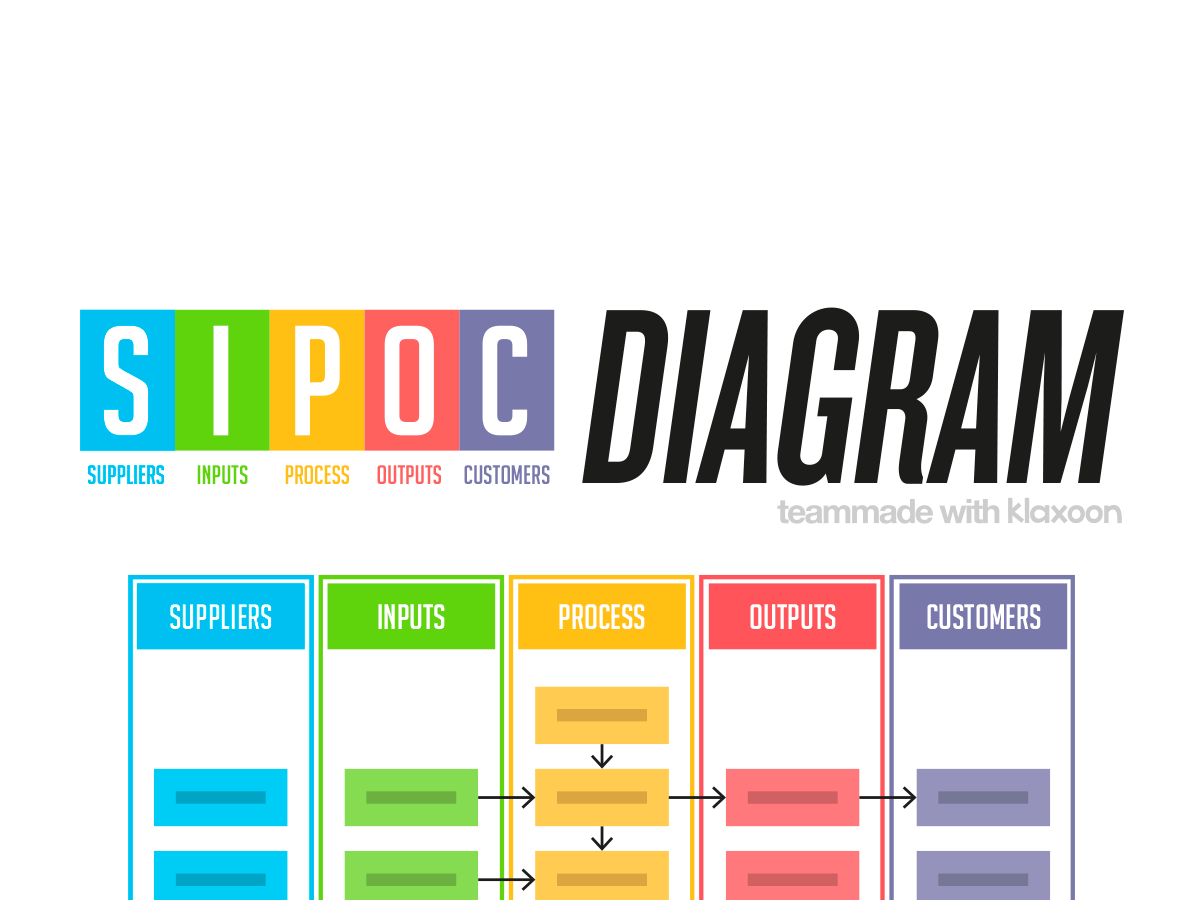
A paper company is an industrial firm that produces papers like newsprint, tissue and paperboard. They may also produce packaging such as bags and shipping boxes. They are generally located in the United States.
The paper sector is a significant part of American economic activity. It produces billions of dollars of goods each year and employs tens of thousands of people. Its products are used in all facets of everyday life, including consumer goods, commercial services, and industrial applications.
Paper companies have their headquarters in different parts of the United States. Some are more regionally focused while others are specialized in certain types of products.
These paper companies, regardless of their location, have one common goal: To create and supply products that people can use every day. Some of the companies are also concerned with environmental sustainability.
International Paper and WestRock have the highest market share in the USA. Both companies are listed in the Fortune 500, and they rank among the biggest paper companies in world.
International Paper's dominance in the US paper industry can be attributed to its extensive portfolio of forest land. It owns more than 42 millions acres of forests and has a variety of pulp, sheet, and containerboard manufacturing facilities in North America.
International Paper’s dominance of the paper market is also due to its focus on diversity. With a diverse staff, it is easier for employees and managers to work together.
In addition to this, having a diverse workforce is important for companies that want to be successful because it allows them to better understand the needs of their customers and prospects.
It can help them to better serve their market and provide the best possible products. They can improve their financial performance through a reduction in costs and expenses.
The diversity of their workforce can also be a great way to attract and retain good workers. A diverse workforce can help improve employee morale. That is crucial for companies like paper, which are constantly dealing with issues like globalization and economic expansion.
Focusing on sustainable development these companies implement policies that can reduce environmental impact while increasing energy efficiency. They are also collaborating with their suppliers to find ways to reduce waste and increase recycling.
FAQ
Can some manufacturing processes be automated?
Yes! Yes! Automation has existed since ancient times. The Egyptians invent the wheel thousands of year ago. Today, robots assist in the assembly of lines.
Robotics is used in many manufacturing processes today. These include:
-
Assembly line robots
-
Robot welding
-
Robot painting
-
Robotics inspection
-
Robots create products
Automation can be applied to manufacturing in many other ways. For example, 3D printing allows us to make custom products without having to wait for weeks or months to get them manufactured.
What is manufacturing and logistics?
Manufacturing is the act of producing goods from raw materials using machines and processes. Logistics includes all aspects related to supply chain management, such as procurement, distribution planning, inventory control and transportation. As a broad term, manufacturing and logistics often refer to both the creation and delivery of products.
What is the responsibility of a logistics manager?
Logistics managers make sure all goods are delivered on schedule and without damage. This is done through his/her expertise and knowledge about the company's product range. He/she also needs to ensure adequate stock to meet demand.
Statistics
- You can multiply the result by 100 to get the total percent of monthly overhead. (investopedia.com)
- It's estimated that 10.8% of the U.S. GDP in 2020 was contributed to manufacturing. (investopedia.com)
- According to a Statista study, U.S. businesses spent $1.63 trillion on logistics in 2019, moving goods from origin to end user through various supply chain network segments. (netsuite.com)
- In 2021, an estimated 12.1 million Americans work in the manufacturing sector.6 (investopedia.com)
- In the United States, for example, manufacturing makes up 15% of the economic output. (twi-global.com)
External Links
How To
How to Use Just-In-Time Production
Just-intime (JIT), which is a method to minimize costs and maximize efficiency in business process, is one way. It is a process where you get the right amount of resources at the right moment when they are needed. This means that your only pay for the resources you actually use. The term was first coined by Frederick Taylor, who developed his theory while working as a foreman in the early 1900s. He saw how overtime was paid to workers for work that was delayed. He decided that workers would be more productive if they had enough time to complete their work before they started to work.
JIT is a way to plan ahead and make sure you don't waste any money. You should also look at the entire project from start to finish and make sure that you have sufficient resources available to deal with any problems that arise during the course of your project. If you anticipate that there might be problems, you'll have enough people and equipment to fix them. This way, you won't end up paying extra money for things that weren't really necessary.
There are many JIT methods.
-
Demand-driven: This is a type of JIT where you order the parts/materials needed for your project regularly. This will allow to track how much material has been used up. This will allow you to calculate how long it will take to make more.
-
Inventory-based: This is a type where you stock the materials required for your projects in advance. This allows one to predict how much they will sell.
-
Project-driven: This approach involves setting aside sufficient funds to cover your project's costs. When you know how much you need, you'll purchase the appropriate amount of materials.
-
Resource-based JIT: This is the most popular form of JIT. You assign certain resources based off demand. You might assign more people to help with orders if there are many. If there aren't many orders, you will assign fewer people.
-
Cost-based: This is similar to resource-based, except that here you're not just concerned about how many people you have but how much each person costs.
-
Price-based: This approach is very similar to the cost-based method except that you don't look at individual workers costs but the total cost of the company.
-
Material-based is an alternative to cost-based. Instead of looking at the total cost in the company, this method focuses on the average amount of raw materials that you consume.
-
Time-based JIT is another form of resource-based JIT. Instead of focusing on the cost of each employee, you will focus on the time it takes to complete a project.
-
Quality-based JIT: This is another variation of resource based JIT. Instead of looking at the labor costs and time it takes to make a product, think about its quality.
-
Value-based JIT: This is the latest form of JIT. This is where you don't care about how the products perform or whether they meet customers' expectations. Instead, you are focused on adding value to the marketplace.
-
Stock-based: This is an inventory-based method that focuses on the actual number of items being produced at any given time. This is used to increase production and minimize inventory.
-
Just-intime planning (JIT), is a combination JIT/sales chain management. It is the process of scheduling components' delivery as soon as they have been ordered. It reduces lead times and improves throughput.