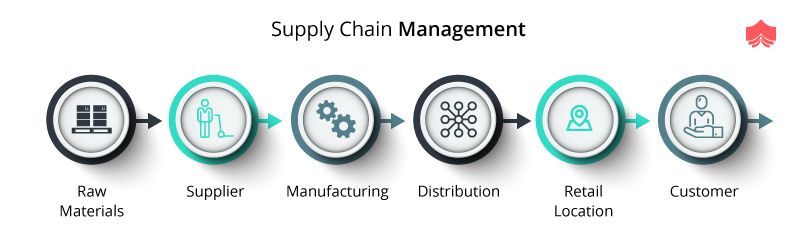
When he graduated from high school, Watts had no idea that he was going to end up as a supply chain major at Towson University. Jack Jensen - the managing director for the Moore School's Supply Chain Management program - was able sell him the program after telling him he could work on the capstone consulting project of the school.
The capstone project is one of the more prestigious undergraduate courses. It allows students to dive into supply chain challenges on real projects for companies or nonprofits. Jensen claims that Moore School students have worked with more 150 companies to identify savings totaling $175 million in the last 8 years.
During their coursework, students work closely with faculty advisors and organizations to analyze real-world supply chain issues using data science tools like Lean Manufacturing and Six Sigma. They also learn to prepare, organize, and transform data, build models, and evaluate results.
After the completion of the course, the students must complete a final project where they will present a problem, its importance to business theory, background research on the project and a clearly defined method.
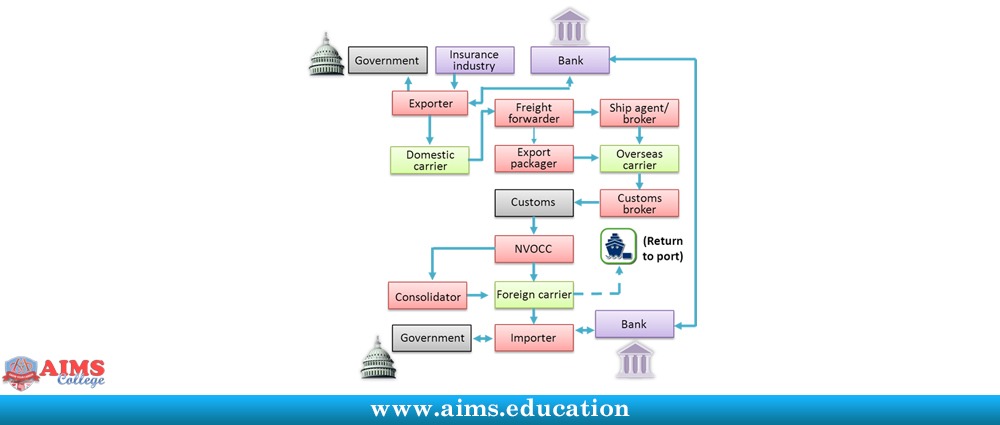
The capstone project provides a unique opportunity to put into practice the knowledge and skills you have gained throughout your degree. It is also a way to show your dedication to your education.
As a result of this, many schools allow their students to do a capstone project for their graduation. These projects can be very challenging, and students often need to spend a significant amount of time and effort to complete them.
The project could be carried out over a course of one semester or more. The project should be completed in between 100 and 120 hours.
Towson Apartments is a student-housing community that offers studios and one- and two bedroom apartments. Capstone Management is responsible for the professional management of this community. Residents enjoy a wide range of amenities.
Millennium Hall is an upscale community consisting of three buildings and 400 beds. It was developed with Towson university in collaboration, and it was delivered in 2001. Both undergraduate and graduate students are tenants of the building. The complex consists of studios as well one and two bedroom units. There is also a central mailbox and a laundry facility.
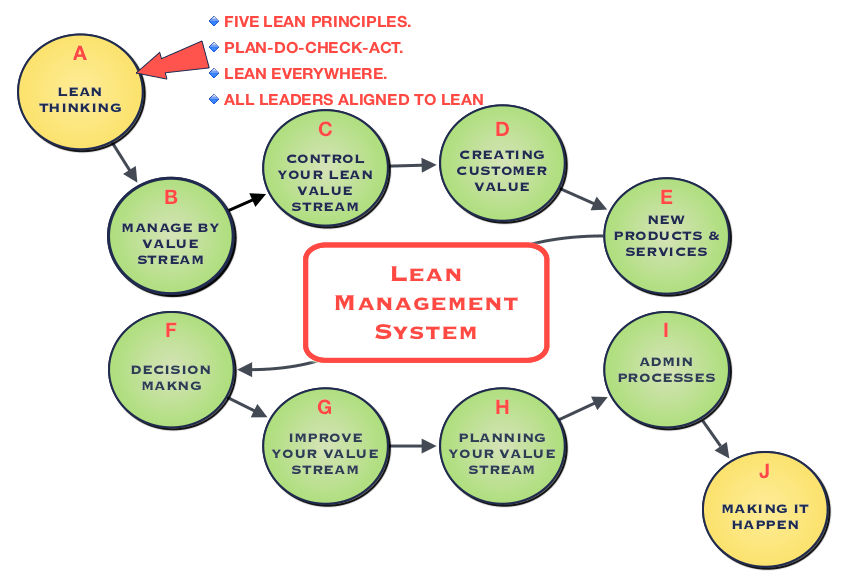
MEDCO leases Millennium Hall and Paca and Tubman Houses from TU. Capstone Properties Inc. will manage the daily operations for MEDCO.
Multiple families have filed suit against MEDCO for breach of contract claiming that they are being held hostage by their lease agreements as TU shifts to distance-learning. The families claim that MEDCO has refused to refund their rents and release them from their lease agreements, despite following guidelines established by TU Housing and Residence Life, the University of Maryland Campus Living Services and the Center for Disease Control.
The lawsuit was first filed in march 2018 but has not yet been settled. Lucchi received responses from MEDCO’s Legal Council and he will continue to pursue this case.
FAQ
What is the role of a production manager?
A production planner ensures all aspects of the project are delivered on time, within budget, and within scope. They also ensure that the product/service meets the client’s needs.
What are manufacturing and logistics?
Manufacturing is the production of goods using raw materials. Logistics manages all aspects of the supply chain, including procurement, production planning and distribution, inventory control, transportation, customer service, and transport. Sometimes manufacturing and logistics are combined to refer to a wider term that includes both the process of creating products as well as their delivery to customers.
What are the 7 Rs of logistics?
The acronym 7R's of Logistic is an acronym that stands for seven fundamental principles of logistics management. It was published in 2004 by the International Association of Business Logisticians as part of their "Seven Principles of Logistics Management" series.
The following letters form the acronym:
-
Responsible – ensure that all actions are legal and don't cause harm to anyone else.
-
Reliable – have faith in your ability and capability to keep promises.
-
Be responsible - Use resources efficiently and avoid wasting them.
-
Realistic - consider all aspects of operations, including cost-effectiveness and environmental impact.
-
Respectful: Treat others with fairness and equity
-
Resourceful - look for opportunities to save money and increase productivity.
-
Recognizable - provide customers with value-added services.
What is the responsibility for a logistics manager
A logistics manager makes sure that all goods are delivered on-time and in good condition. This is done using his/her knowledge of the company's products. He/she must also ensure sufficient stock to meet the demand.
Statistics
- In 2021, an estimated 12.1 million Americans work in the manufacturing sector.6 (investopedia.com)
- According to a Statista study, U.S. businesses spent $1.63 trillion on logistics in 2019, moving goods from origin to end user through various supply chain network segments. (netsuite.com)
- It's estimated that 10.8% of the U.S. GDP in 2020 was contributed to manufacturing. (investopedia.com)
- In the United States, for example, manufacturing makes up 15% of the economic output. (twi-global.com)
- Many factories witnessed a 30% increase in output due to the shift to electric motors. (en.wikipedia.org)
External Links
How To
How to Use 5S to Increase Productivity in Manufacturing
5S stands to stand for "Sort", “Set In Order", “Standardize", and "Store". Toyota Motor Corporation developed the 5S method in 1954. It assists companies in improving their work environments and achieving higher efficiency.
This method aims to standardize production processes so that they are repeatable, measurable and predictable. It means tasks like cleaning, sorting or packing, labeling, and storing are done every day. Workers can be more productive by knowing what to expect.
Five steps are required to implement 5S: Sort, Set In Order, Standardize. Separate. Each step is a different action that leads to greater efficiency. By sorting, for example, you make it easy to find the items later. Once you have placed items in an ordered fashion, you will put them together. Once you have separated your inventory into groups and organized them, you will store these groups in easily accessible containers. You can also label your containers to ensure everything is properly labeled.
This process requires employees to think critically about how they do their job. Employees should understand why they do the tasks they do, and then decide if there are better ways to accomplish them. They will need to develop new skills and techniques in order for the 5S system to be implemented.
In addition to increasing efficiency, the 5S method also improves morale and teamwork among employees. As they begin to see improvements, they feel motivated to continue working towards the goal of achieving higher levels of efficiency.