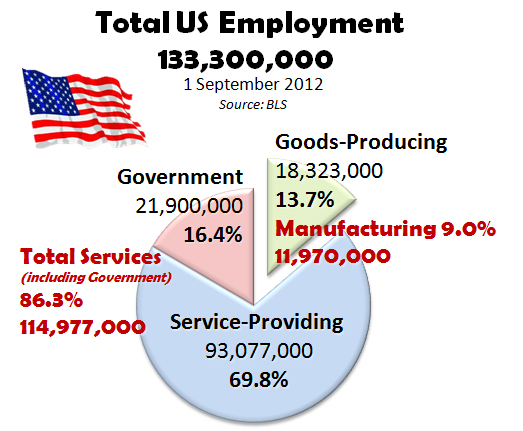
The machines that machine operators use to make repairs are a wide range of machines. These machines make repairs on metal products such as a car. They can also create precision metal parts or new alloys. Machine operators are frequently exposed to toxic chemicals. A skilled machinist will be detail-oriented, have strong communication skills, and be able to read mechanical blueprints.
Machinists can work part-time or full-time. Many of them start their careers right after graduating high school. Some machinists work as apprentices before moving into a full-time job. Others take associate degrees in machining. Some machinists may even pursue a degree in engineering or computer-aided design (CAD).
Machine builders often work in factories, or in specialty shops. These positions can be noisy, and they are exposed to potentially hazardous materials. However, these positions offer tremendous opportunities for problem solving. Machines used in machinists' work can be either manual or automatic. People with extensive experience in this field may be able to move up to managerial or supervisory positions. As the baby boomers begin to retire, so does the need for machine operators. In addition, as machine shops retool for automation, job security is enhanced.
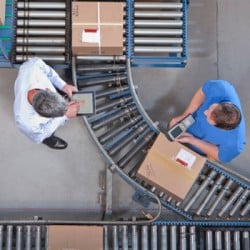
Depending on their employer, machinists could be assigned specific tasks such as setting up machines, fixing them, or making sure the parts they produce are compliant with quality standards. They may also be assigned to work on assembly lines. These are machines that can be operated by either a person or a machine. They also have to use a computer for programming and monitoring the machines and interpret blueprints.
Machinists work in a variety of metals, including steel, aluminum brass, copper, and others. Most machinists work on machines that produce metal parts. However, sometimes they need to work with other materials.
Although machinists typically have a high school diploma in most cases, some employers may require a bachelor's degree. If you are interested in becoming a machinist, you can start with a training program that can last up to four years. To gain more knowledge and experience, you can work with a mentor at your workplace. Be sure to ask your mentor about other opportunities for training, such as apprenticeships or additional education.
Machine operators must collaborate with others, regardless of their company. You can work with them in a group or alone. However, they must follow safety procedures. This includes wearing proper safety equipment, such as earplugs, gloves, and masks. Also, machinists are frequently exposed to fumes, chemicals, and other environmental hazards. Fortunately, machinists do not have to be under constant time pressure.
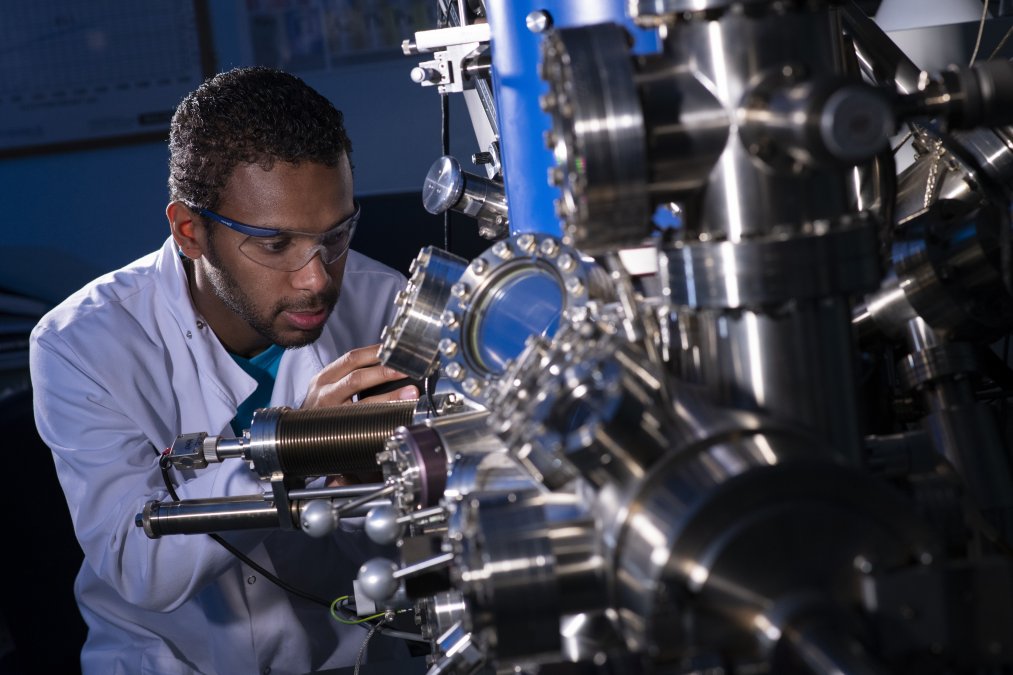
Besides on-the-job training, machinists can enroll in college courses or join trade unions. Machinists who are members of a union have better job security and benefits. Union members have access to health insurance and retirement plans. A number of colleges offer two-year machining associates degrees.
With a degree in machinist work, you can move up the corporate ladder. As the demand for car parts increases, machinists will be needed more and more. Between 2020 and 2030, the projected job growth will be 7%. Additionally, the demand for machinists is expected to increase with the increased use and retooling of automated machinery.
FAQ
What skills should a production planner have?
You must be flexible and organized to become a productive production planner. It is also important to be able communicate with colleagues and clients.
Why automate your factory?
Modern warehouses are increasingly dependent on automation. Increased demand for efficient and faster delivery has resulted in a rise in e-commerce.
Warehouses should be able adapt quickly to new needs. In order to do this, they need to invest in technology. The benefits of automating warehouses are numerous. These are some of the benefits that automation can bring to warehouses:
-
Increases throughput/productivity
-
Reduces errors
-
Accuracy is improved
-
Safety Boosts
-
Eliminates bottlenecks
-
Companies can scale up more easily
-
This makes workers more productive
-
Gives you visibility into all that is happening in your warehouse
-
Enhances customer experience
-
Improves employee satisfaction
-
Reducing downtime and increasing uptime
-
High quality products delivered on-time
-
Eliminates human error
-
Helps ensure compliance with regulations
What are the products of logistics?
Logistics is the process of moving goods from one point to another.
They include all aspects of transport, including packaging, loading, transporting, unloading, storing, warehousing, inventory management, customer service, distribution, returns, and recycling.
Logisticians ensure that products reach the right destination at the right moment and under safe conditions. Logisticians assist companies in managing their supply chains by providing information such as demand forecasts, stock levels and production schedules.
They coordinate with vendors and suppliers, keep track of shipments, monitor quality standards and perform inventory and order replenishment.
Is it necessary to be familiar with Manufacturing Processes before we learn about Logistics.
No. No. However, knowing about manufacturing processes will definitely give you a better understanding of how logistics works.
What are the 7 Rs of logistics.
The acronym 7R's for Logistics stands to represent the seven basic principles in logistics management. It was developed by International Association of Business Logisticians (IABL), and published as part of their "Seven Principles of Logistics Management Series" in 2004.
The acronym is composed of the following letters.
-
Responsible - ensure that all actions taken are within legal requirements and are not harmful to others.
-
Reliable - Have confidence in your ability to fulfill all of your commitments.
-
Be responsible - Use resources efficiently and avoid wasting them.
-
Realistic – consider all aspects of operations, from cost-effectiveness to environmental impact.
-
Respectful - Treat people fairly and equitably
-
Responsive - Look for ways to save time and increase productivity.
-
Recognizable provides value-added products and services to customers
Statistics
- You can multiply the result by 100 to get the total percent of monthly overhead. (investopedia.com)
- In 2021, an estimated 12.1 million Americans work in the manufacturing sector.6 (investopedia.com)
- (2:04) MTO is a production technique wherein products are customized according to customer specifications, and production only starts after an order is received. (oracle.com)
- [54][55] These are the top 50 countries by the total value of manufacturing output in US dollars for its noted year according to World Bank.[56] (en.wikipedia.org)
- It's estimated that 10.8% of the U.S. GDP in 2020 was contributed to manufacturing. (investopedia.com)
External Links
How To
Six Sigma in Manufacturing
Six Sigma refers to "the application and control of statistical processes (SPC) techniques in order to achieve continuous improvement." Motorola's Quality Improvement Department in Tokyo, Japan developed Six Sigma in 1986. Six Sigma is a method to improve quality through standardization and elimination of defects. In recent years, many companies have adopted this method because they believe there is no such thing as perfect products or services. Six Sigma seeks to reduce variation between the mean production value. It is possible to measure the performance of your product against an average and find the percentage of time that it differs from the norm. If there is a significant deviation from the norm, you will know that something needs to change.
Understanding the nature of variability in your business is the first step to Six Sigma. Once you understand that, it is time to identify the sources of variation. This will allow you to decide if these variations are random and systematic. Random variations are caused when people make mistakes. While systematic variations are caused outside of the process, they can occur. For example, if you're making widgets, and some of them fall off the assembly line, those would be considered random variations. But if you notice that every widget you make falls apart at the exact same place each time, this would indicate that there is a problem.
After identifying the problem areas, you will need to devise solutions. This could mean changing your approach or redesigning the entire process. To verify that the changes have worked, you need to test them again. If they don't work, you will need to go back to the drawing boards and create a new plan.