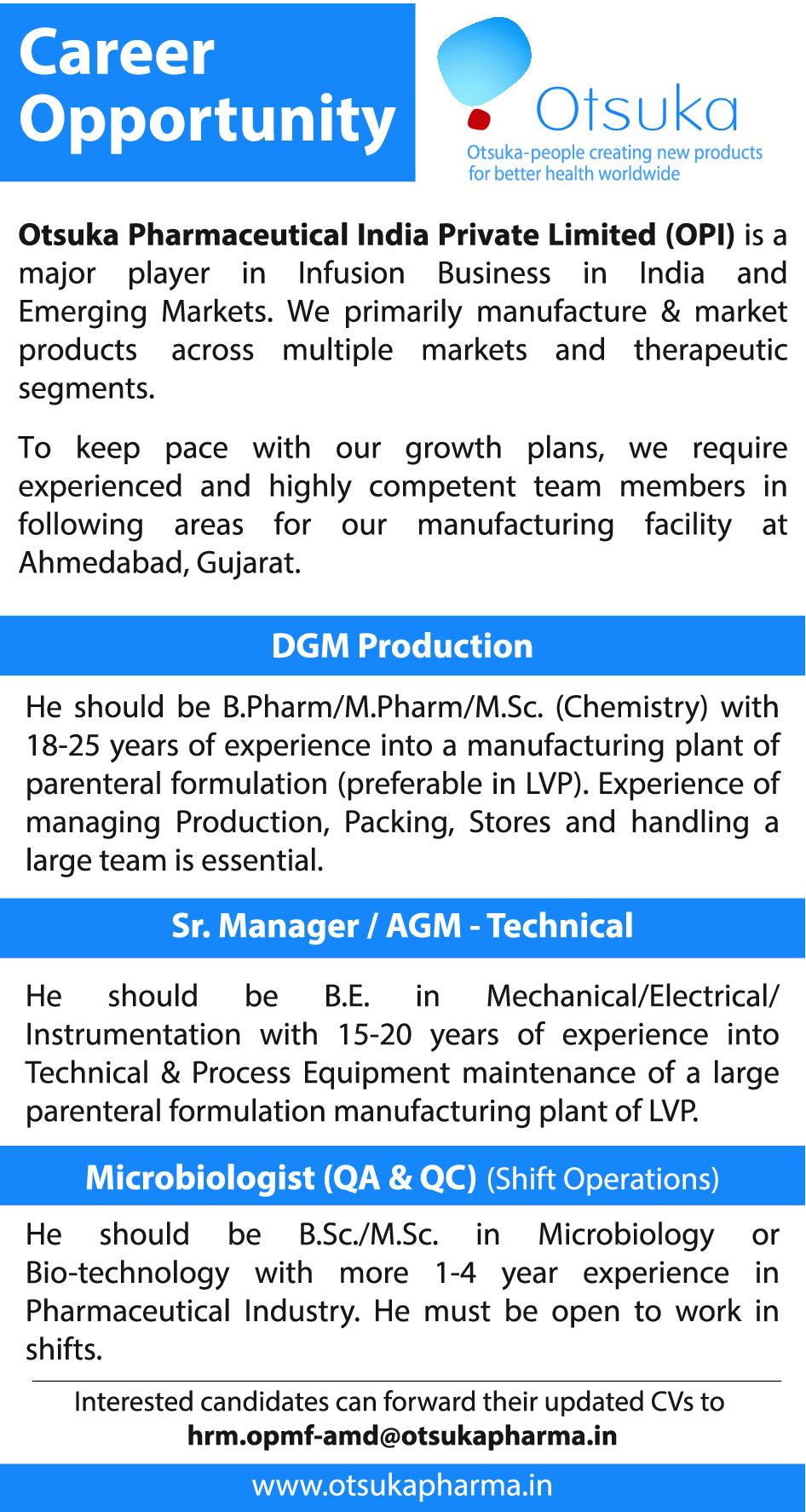
Advanced manufacturing refers the use of innovative technology in order to enhance products or processes. This technology can be classified as either "advanced", "innovative," and "cutting-edge". As the number of companies that use advanced manufacturing increases, these industries are increasingly integrating new and innovative technologies into their manufacturing processes. Here are some examples for advanced manufacturing. These are the most popular technologies in advanced manufacturing.
Continuous manufacturing
Continuous manufacturing was first described in the 1700s, when it was used for making pig iron in blast furnaces. The concept has since spread across various industries, including the automotive, food, oil and refining, chemicals, and pulp and paper industries. Continuous manufacturing is now gaining significant traction in biopharmaceutical, drawing the attention and support of CMOs as well as big pharma players.
In a recent commentary, the FDA and its partners discussed the benefits of using continuous manufacturing to produce therapeutic proteins. This legislation would establish national centers to help companies develop standards and advance the field. This legislation is intended to improve the creation and use of medical products. It would encourage companies to use continuous production to improve and develop products. But, it is crucial to ensure that continuous production processes are safe.
Automated processes
Automating manufacturing processes can have many benefits. Automating processes in advanced manufacturing is the best way to maximize production efficiency and make the most of your floor space. In order to reduce costs and increase production efficiency, manufacturers can collect data and leverage automation technologies. Automation in the process industry also helps to save time and money. While the initial investment can be high, it will eventually increase the bottom line of a manufacturing company.
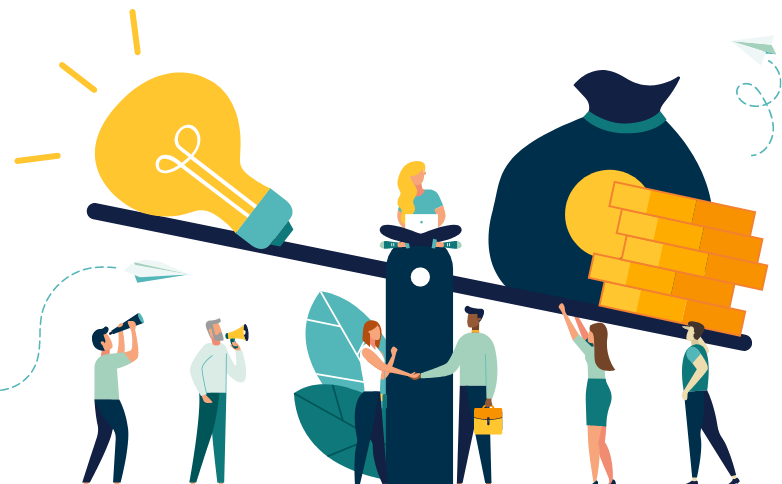
Companies are now combining automated manufacturing processes with advanced manufacturing processes. Audi is an example of a company that uses automated welding to bond its products. This allows them to cut down on production time and also saves energy and weight. Advanced manufacturing techniques, such as regenerative braking for conveyor systems are used. 3D printing represents the greatest advancement in manufacturing. It has been around for a while, but it is only now that it is mainstream. But what makes it so attractive to manufacturers?
Internet of Things (IoT)
The IIoT revolution in manufacturing is changing through the use sensors to monitor machines, and their processes. These sensors collect data from all parts of the manufacturing process and send it to a central base station. This data is then processed and analyzed, which can be used to improve processes and eliminate waste. Advanced manufacturers use IIoT to monitor production processes and optimize their output. The IIoT can be described as the industrial equivalent of key fobs.
IIoT deployment requires a comprehensive roadmap, and the ability to develop capabilities to roll out use case in an effective and scalable fashion. The following roadmap is provided by an automaker. It shows three phases of deployment.
Cost-effectiveness
Costs of advanced manufacturing may not be directly comparable to traditional production systems. The traditional cost-benefit analysis, however, is not sufficient to evaluate economic benefits. A holistic model that takes into account both the benefits and costs of technology can identify new benefits, and help speed decision-making. Munker, Schroer, and Munker present a cost-benefit calculator that addresses key issues related to AMS implementation.
Information technology advancements are quickly changing the face of manufacturing. Production systems are becoming increasingly networked and intelligent. Cost pressure is increasing productivity and a company’s ability to respond quickly to customer requirements. The adoption of modern manufacturing technologies will accelerate the development of new technologies and increase their cost-effectiveness. As the industry continues digitizing, it is likely that such technologies will be adopted more quickly.
Human error reduction
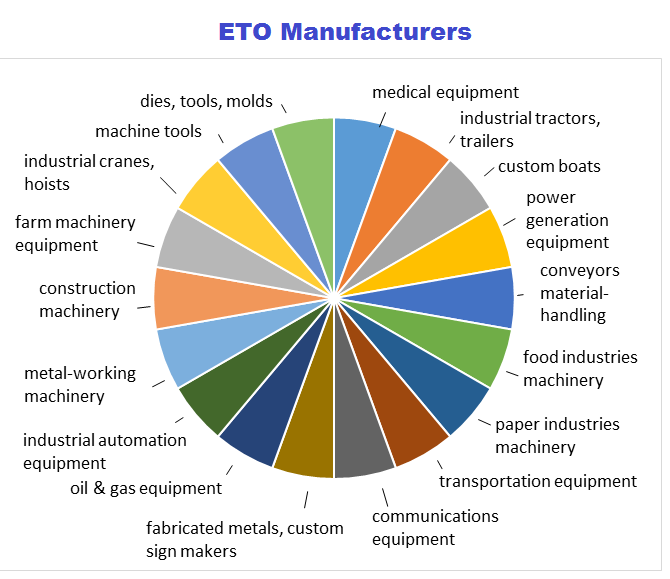
Although humans can make mistakes, the manufacturing process used to create a product is designed to minimize them. Employees who fail to follow written instructions or don't understand them can cause human error. Pharmaceutical laboratories, for example, have to follow very specific procedures when they are making drugs. An employee might think they understand the process, and so proceed to make the drug mixture without reading the written instructions.
Effective communication between senior and junior employees is another way to reduce human error. Managers must refrain from punishing employees for asking question. Employees are more likely than ever to make mistakes if they're treated harshly. Employees should feel comfortable asking question and will not hesitate to ask for clarification if they are uncomfortable. It is important to establish a healthy relationship between senior and junior employees. Also, it is important to address communication issues in a polite and professional manner.
FAQ
What is the job of a production plan?
A production planner makes sure all project elements are delivered on schedule, within budget, as well as within the agreed scope. They also ensure the quality of the product and service meets the client's requirements.
What are the logistics products?
Logistics refers to the movement of goods from one place to another.
These include all aspects related to transport such as packaging, loading and transporting, storing, transporting, unloading and warehousing inventory management, customer service. Distribution, returns, recycling are some of the options.
Logisticians ensure the product reaches its destination in the most efficient manner. Logisticians assist companies in managing their supply chains by providing information such as demand forecasts, stock levels and production schedules.
They coordinate with vendors and suppliers, keep track of shipments, monitor quality standards and perform inventory and order replenishment.
What are the requirements to start a logistics business?
To run a successful logistics company, you need a lot knowledge and skills. Good communication skills are essential to effectively communicate with your suppliers and clients. You need to understand how to analyze data and draw conclusions from it. You will need to be able handle pressure well and work in stressful situations. To improve efficiency, you must be innovative and creative. You will need strong leadership skills to motivate and direct your team members towards achieving their organizational goals.
You should also be organized and efficient to meet tight deadlines.
Statistics
- You can multiply the result by 100 to get the total percent of monthly overhead. (investopedia.com)
- It's estimated that 10.8% of the U.S. GDP in 2020 was contributed to manufacturing. (investopedia.com)
- (2:04) MTO is a production technique wherein products are customized according to customer specifications, and production only starts after an order is received. (oracle.com)
- According to a Statista study, U.S. businesses spent $1.63 trillion on logistics in 2019, moving goods from origin to end user through various supply chain network segments. (netsuite.com)
- [54][55] These are the top 50 countries by the total value of manufacturing output in US dollars for its noted year according to World Bank.[56] (en.wikipedia.org)
External Links
How To
Six Sigma in Manufacturing
Six Sigma is "the application statistical process control (SPC), techniques for continuous improvement." Motorola's Quality Improvement Department in Tokyo, Japan developed Six Sigma in 1986. Six Sigma's core idea is to improve the quality of processes by standardizing and eliminating defects. This method has been adopted by many companies in recent years as they believe there are no perfect products or services. Six Sigma aims to reduce variation in the production's mean value. You can calculate the percentage of deviation from the norm by taking a sample of your product and comparing it to the average. If you notice a large deviation, then it is time to fix it.
Understanding the nature of variability in your business is the first step to Six Sigma. Once you understand that, it is time to identify the sources of variation. These variations can also be classified as random or systematic. Random variations happen when people make errors; systematic variations are caused externally. For example, if you're making widgets, and some of them fall off the assembly line, those would be considered random variations. But if you notice that every widget you make falls apart at the exact same place each time, this would indicate that there is a problem.
Once you've identified the problem areas you need to find solutions. The solution could involve changing how you do things, or redesigning your entire process. You should then test the changes again after they have been implemented. If they didn't work, then you'll need to go back to the drawing board and come up with another plan.