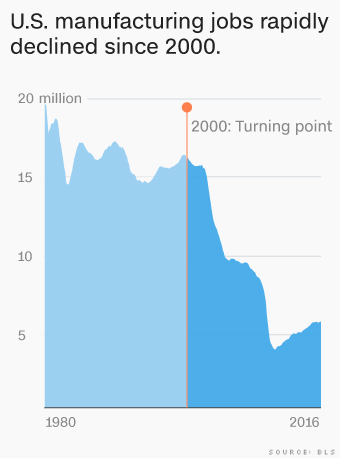
There are many types and styles of manufacturers. Which one is best for you business? Learn about discrete manufacturing, continuous manufacturing, job shop manufacturing, or process manufacturing. Each type has its own advantages and disadvantages. This article will describe the differences among these four types. You can choose the best model for your business based on your industry, location, and product type. Once you have determined which type is best, you need to take into account your sales, production and quality control.
Discrete Manufacturing
Discrete production is when distinct products are manufactured. Toys, cars, and aeroplanes are just a few examples of discrete manufacturing. Discrete Manufacturing allows companies to focus more on their individual products than on mass production. For example, discrete manufacturing makes it possible to create unique parts for an aeroplane by integrating several manufacturing processes. Discrete manufacturing is a popular method for manufacturing high-tech products.
Discrete manufacturing produces distinct items. Instead of making multiple identical products, discrete manufacture produces distinct items that can easily be identified using serial numbers, labels, or other numerical attributes. One example is a smartphone that may be made from many parts, each of which are assembled when the product is finished. The same is true for the smartphone's case. It might contain different parts of several plants, including the Missouri plant and headquarters.
Process manufacturing
Process manufacturing refers to a type of manufacturing that uses formulas and recipes. Process manufacturing is different from discrete manufacturing which is focused on individual units, bills and assembly of components. The two manufacturing methods have very different goals. Each is essential to the manufacturing process. These are three ways to distinguish between process and discrete manufacturing. Let's look at each one.
Batch process manufacturing can be compared to continuous process production. It uses larger batches of raw materials, and works around the clock. Batch process manufacturing is used in many industries, including pharmaceuticals, paper production and bookbinding. This method may not be the right fit for all industries. It's often too complex and costly for smaller-scale businesses to use. This is why most companies resort to this method when producing large quantities of the same product.
Manufacturing jobs
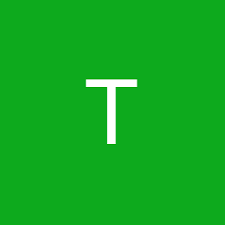
Job shop manufacturing can be described as a small-scale production system that specializes only in custom, batch and semi-custom manufacturing. As each job is completed, job shop systems can move on to the next. This method of production is also called lean manufacturing, as a single-shift operation is more efficient than many other methods. Here are some advantages of job shop production. Learn more about this manufacturing method. For your business, it might be worth considering for your product and service needs.
First, job shops have to be more efficient. Incorporating new manufacturing principles is key to achieving lean manufacturing systems. These principles apply to high-volume operations as they emphasize quality control, just-in time production, and are very relevant. Job shops can increase productivity and decrease costs by adopting new manufacturing methods. Additionally, every job should be processed individually, so there should not be a queue.
Continuous manufacturing
Continuous manufacturing allows for flexible tracking which is one of the greatest advantages. This is especially helpful in the event of product failure. Product data such as the amount of raw material used and the time stamp at each production line can be used for identifying defective batches. The increased tracking also helps the manufacturer reduce waste and the chance of a product shortage. In the pharmaceutical industry, continuous manufacturing is also gaining popularity.
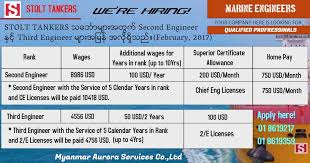
While continuous manufacturing is a great option, it can be slow to implement. The fact that continuous manufacturing is not fully integrated into the company is often what hinders its implementation. Regardless of the benefits, continuous manufacturing has the potential to be a game changer for the pharmaceutical industry. Continuous manufacturing is only possible if the process integrates with end-to–end integration and continuous flow. The pharmaceutical industry has long recognized the benefits of continuous manufacturing, but implementation has been slow.
FAQ
Can we automate some parts of manufacturing?
Yes! Since ancient times, automation has been in existence. The Egyptians invented the wheel thousands of years ago. Today, robots assist in the assembly of lines.
Robotics is used in many manufacturing processes today. These include:
-
Automated assembly line robots
-
Robot welding
-
Robot painting
-
Robotics inspection
-
Robots that create products
Automation could also be used to improve manufacturing. 3D printing, for example, allows us to create custom products without waiting for them to be made.
How can efficiency in manufacturing be improved?
First, we need to identify which factors are most critical in affecting production times. We then need to figure out how to improve these variables. If you don't know where to start, then think about which factor(s) have the biggest impact on production time. Once you have identified the factors, then try to find solutions.
What are manufacturing and logistic?
Manufacturing refers the process of producing goods from raw materials through machines and processes. Logistics is the management of all aspects of supply chain activities, including procurement, production planning, distribution, warehousing, inventory control, transportation, and customer service. Manufacturing and logistics can often be grouped together to describe a larger term that covers both the creation of products, and the delivery of them to customers.
What jobs are available in logistics?
Logistics can offer many different jobs. Some examples are:
-
Warehouse workers – They load, unload and transport pallets and trucks.
-
Transportation drivers - They drive trucks and trailers to deliver goods and carry out pick-ups.
-
Freight handlers – They sort and package freight at warehouses.
-
Inventory managers: They are responsible for the inventory and management of warehouses.
-
Sales representatives - They sell products.
-
Logistics coordinators - They organize and plan logistics operations.
-
Purchasing agents - They purchase goods and services needed for company operations.
-
Customer service agents - They answer phone calls and respond to emails.
-
Shipping clerks – They process shipping orders, and issue bills.
-
Order fillers - They fill orders based on what is ordered and shipped.
-
Quality control inspectors – They inspect incoming and outgoing products to ensure that there are no defects.
-
Other - Logistics has many other job opportunities, including transportation supervisors, logistics specialists, and cargo specialists.
What does it mean to warehouse?
A warehouse is a place where goods are stored until they are sold. It can be either an indoor or outdoor space. It could be one or both.
What is the importance of automation in manufacturing?
Automation is important not only for manufacturers but also for service providers. Automation allows them to deliver services quicker and more efficiently. It also helps to reduce costs and improve productivity.
Statistics
- It's estimated that 10.8% of the U.S. GDP in 2020 was contributed to manufacturing. (investopedia.com)
- According to the United Nations Industrial Development Organization (UNIDO), China is the top manufacturer worldwide by 2019 output, producing 28.7% of the total global manufacturing output, followed by the United States, Japan, Germany, and India.[52][53] (en.wikipedia.org)
- [54][55] These are the top 50 countries by the total value of manufacturing output in US dollars for its noted year according to World Bank.[56] (en.wikipedia.org)
- Many factories witnessed a 30% increase in output due to the shift to electric motors. (en.wikipedia.org)
- According to a Statista study, U.S. businesses spent $1.63 trillion on logistics in 2019, moving goods from origin to end user through various supply chain network segments. (netsuite.com)
External Links
How To
How to use Lean Manufacturing in the production of goods
Lean manufacturing (or lean manufacturing) is a style of management that aims to increase efficiency, reduce waste and improve performance through continuous improvement. It was developed in Japan between 1970 and 1980 by Taiichi Ohno. TPS founder Kanji Tyoda gave him the Toyota Production System, or TPS award. Michael L. Watkins published the "The Machine That Changed the World", the first book about lean manufacturing. It was published in 1990.
Lean manufacturing, often described as a set and practice of principles, is aimed at improving the quality, speed, cost, and efficiency of products, services, and other activities. It emphasizes the elimination and minimization of waste in the value stream. Lean manufacturing is also known as just in time (JIT), zero defect total productive maintenance(TPM), and five-star (S). Lean manufacturing eliminates non-value-added tasks like inspection, rework, waiting.
Lean manufacturing improves product quality and costs. It also helps companies reach their goals quicker and decreases employee turnover. Lean manufacturing is a great way to manage the entire value chain including customers, suppliers, distributors and retailers as well as employees. Lean manufacturing is widely used in many industries. Toyota's philosophy, for example, is what has enabled it to be successful in electronics, automobiles, medical devices, healthcare and chemical engineering as well as paper and food.
Lean manufacturing is based on five principles:
-
Define value - Find out what your business contributes to society, and what makes it different from other competitors.
-
Reduce waste - Get rid of any activity that does not add value to the supply chain.
-
Create Flow: Ensure that the work process flows without interruptions.
-
Standardize & Simplify - Make processes as consistent and repeatable as possible.
-
Building Relationships – Establish personal relationships with both external and internal stakeholders.
Lean manufacturing, although not new, has seen renewed interest in the economic sector since 2008. Many companies have adopted lean manufacturing methods to increase their marketability. In fact, some economists believe that lean manufacturing will be an important factor in economic recovery.
Lean manufacturing is now becoming a common practice in the automotive industry, with many benefits. These include higher customer satisfaction, lower inventory levels, lower operating expenses, greater productivity, and improved overall safety.
You can apply Lean Manufacturing to virtually any aspect of your organization. It is especially useful for the production aspect of an organization, as it ensures that every step in the value chain is efficient and effective.
There are three main types in lean manufacturing
-
Just-in Time Manufacturing, (JIT): This kind of lean manufacturing is also commonly known as "pull-systems." JIT is a process in which components can be assembled at the point they are needed, instead of being made ahead of time. This approach is designed to reduce lead times and increase the availability of components. It also reduces inventory.
-
Zero Defects Manufacturing, (ZDM): ZDM is focused on ensuring that no defective products leave the manufacturing facility. If a part needs to be fixed during the assembly line, it should be repaired rather than scrapped. This applies to finished products, which may need minor repairs before they are shipped.
-
Continuous Improvement (CI): CI aims to improve the efficiency of operations by continuously identifying problems and making changes in order to eliminate or minimize waste. Continuous improvement involves continuous improvement of processes and people as well as tools.