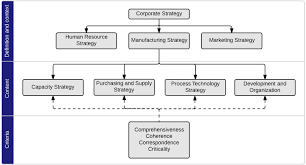
If you're interested in a supply chain management career, you can start by researching industries that offer good opportunities. Find out the number of people working in that industry, their skills, and what job opportunities are available. When it comes to job search, you can connect with recruiters or human resource professionals. Depending upon your goals, you might also consider joining a professional group to learn about certification programs.
Supply chain management is an exciting field that requires a variety of skills. It may seem difficult and complex, but it's also extremely rewarding. You will have lots of opportunities and flexibility.
Logistics and supply chain management require critical thinking, project management, interpersonal communications, and sustainability skills. Aside from being able to communicate effectively with stakeholders at all levels, logistics and supply chain managers must have the ability to do so. They need to be able implement new technologies and comply with international regulations.
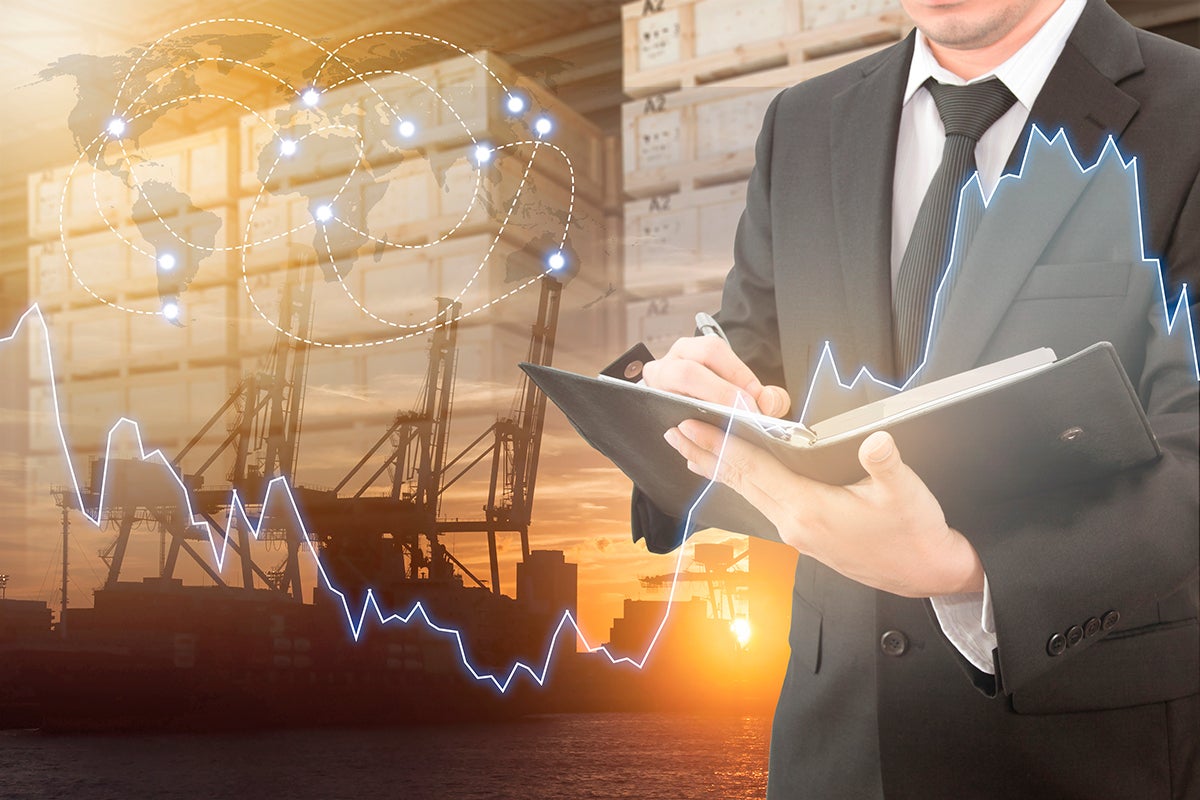
Companies today look at their supply chains from a larger perspective. As a result, you'll find that one supply chain model does not fit all. While a large company may have many product lines you can work on, a small family-owned business might offer less career progression opportunities. Your satisfaction can also be affected greatly by the company's size.
To get started you will need a strong support network. You should get to know supply chain managers and HR professionals. Also, learn about the industries that are of interest to you. Once you have a strong network, it's possible to search for a job in supply chain. Most supply chain jobs are competitive, and you'll have to show that you have the requisite expertise and experience.
Supply chain management is unpredictable and fast-paced. It is essential to be flexible as well as able to resolve problems quickly. You can avoid disruptions in your supply chain and help your organization achieve its goals by solving problems quickly.
As part of a supply-chain career, you will also need to organize and collect data. This is an essential asset for making effective decisions and allocating team resources. To support the entire process of serving customers, it is important to have good data management and collection.
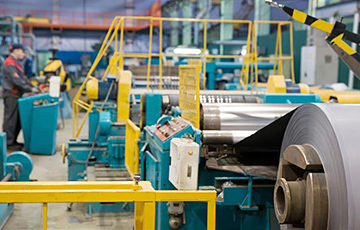
Supply chain managers should also be able to manage projects and oversee finances. They may have to manage several projects at once but should be able prioritize them and decide what is most important. They'll need the ability to weigh both the benefits and disadvantages of each decision.
You can find supply chain management positions in healthcare, transportation, manufacturing and food service for those who are looking to make a career out of it. The salary and job opportunities for these positions are varied. For each industry, you will need to possess a minimum of three years of experience.
There are many jobs in supply chain management, which is a rapidly growing field. Take into account what you enjoy most about working alongside people and how you can make this a career in this fast-paced industry.
FAQ
Why automate your factory?
Automation has become increasingly important in modern warehousing. Increased demand for efficient and faster delivery has resulted in a rise in e-commerce.
Warehouses need to adapt quickly to meet changing needs. To do so, they must invest heavily in technology. Automation of warehouses offers many benefits. These are just a few reasons to invest in automation.
-
Increases throughput/productivity
-
Reduces errors
-
Improves accuracy
-
Safety Boosts
-
Eliminates bottlenecks
-
Allows companies scale more easily
-
It makes workers more efficient
-
This gives you visibility into what happens in the warehouse
-
Enhances customer experience
-
Improves employee satisfaction
-
Minimizes downtime and increases uptime
-
High quality products delivered on-time
-
Removing human error
-
Helps ensure compliance with regulations
What skills should a production planner have?
Production planners must be flexible, organized, and able handle multiple tasks. You must also be able to communicate effectively with clients and colleagues.
What are the 7 Rs of logistics management?
The acronym 7Rs of Logistics refers to the seven core principles of logistics management. It was developed by International Association of Business Logisticians (IABL), and published as part of their "Seven Principles of Logistics Management Series" in 2004.
The following letters make up the acronym:
-
Responsible - ensure that all actions taken are within legal requirements and are not harmful to others.
-
Reliable – have faith in your ability and capability to keep promises.
-
Use resources effectively and sparingly.
-
Realistic - Consider all aspects of operations, including environmental impact and cost effectiveness.
-
Respectful: Treat others with fairness and equity
-
You are resourceful and look for ways to save money while increasing productivity.
-
Recognizable - provide customers with value-added services.
What are the responsibilities of a manufacturing manager
The manufacturing manager should ensure that every manufacturing process is efficient and effective. They should also be aware and responsive to any company problems.
They should also be able communicate with other departments, such as sales or marketing.
They must also keep up-to-date with the latest trends in their field and be able use this information to improve productivity and efficiency.
Is automation important for manufacturing?
Automating is not just important for manufacturers, but also for service providers. It allows them to offer services faster and more efficiently. It helps them to lower costs by reducing human errors, and improving productivity.
What are my options for learning more about manufacturing
Hands-on experience is the best way to learn more about manufacturing. If that is not possible, you could always read books or view educational videos.
Statistics
- It's estimated that 10.8% of the U.S. GDP in 2020 was contributed to manufacturing. (investopedia.com)
- In the United States, for example, manufacturing makes up 15% of the economic output. (twi-global.com)
- [54][55] These are the top 50 countries by the total value of manufacturing output in US dollars for its noted year according to World Bank.[56] (en.wikipedia.org)
- You can multiply the result by 100 to get the total percent of monthly overhead. (investopedia.com)
- Job #1 is delivering the ordered product according to specifications: color, size, brand, and quantity. (netsuite.com)
External Links
How To
Six Sigma in Manufacturing:
Six Sigma is defined as "the application of statistical process control (SPC) techniques to achieve continuous improvement." Motorola's Quality Improvement Department in Tokyo, Japan developed Six Sigma in 1986. Six Sigma is a method to improve quality through standardization and elimination of defects. Since there are no perfect products, or services, this approach has been adopted by many companies over the years. Six Sigma aims to reduce variation in the production's mean value. If you take a sample and compare it with the average, you will be able to determine how much of the production process is different from the norm. If there is a significant deviation from the norm, you will know that something needs to change.
Understanding the nature of variability in your business is the first step to Six Sigma. Once you have a good understanding of the basics, you can identify potential sources of variation. It is important to identify whether the variations are random or systemic. Random variations are caused by human errors. Systematic variations can be caused by outside factors. For example, if you're making widgets, and some of them fall off the assembly line, those would be considered random variations. But if you notice that every widget you make falls apart at the exact same place each time, this would indicate that there is a problem.
Once you have identified the problem, you can design solutions. It might mean changing the way you do business or redesigning it entirely. You should then test the changes again after they have been implemented. If they didn't work, then you'll need to go back to the drawing board and come up with another plan.