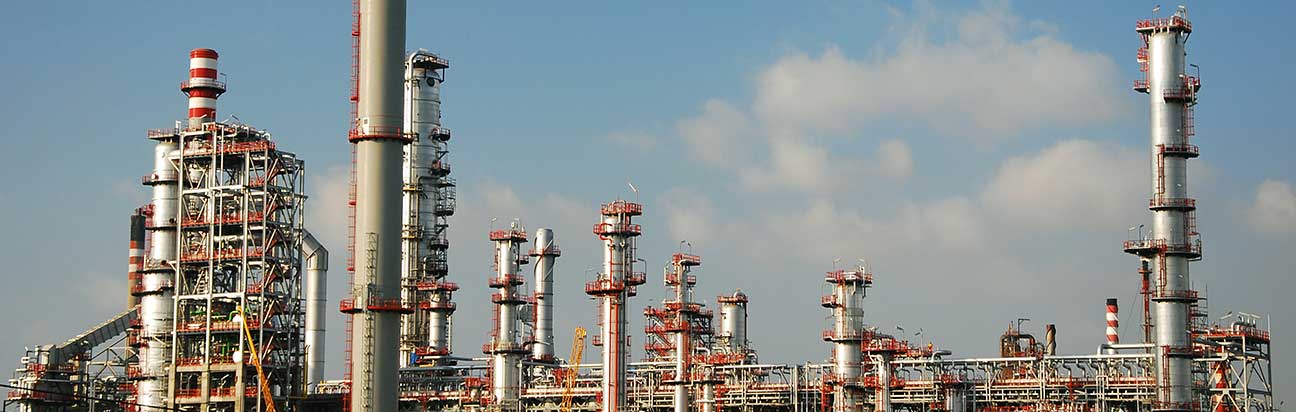
The right qualifications are essential if you want to work as a maintenance engineer. Here are some of these certifications and the expected earnings. Maintenance engineers are a job that is perfect for those who have a keen eye for detail. These professionals are responsible for maintaining a building's infrastructure and ensure that it stays operating at optimal levels.
Qualifications required to work as a maintenance engineer
These are the key elements to consider if you are looking for a career as an engineer in maintenance. You can get a high school diploma, but you should also consider enrolling in college courses in engineering. It will be beneficial to take courses in chemistry and math. You can also gain work experience. A technical school might be an option, depending on your company's needs.
The maintenance engineer is responsible in maintaining machinery, equipment, infrastructures, and other systems. Their job is to keep industrial machinery operating as efficiently as possible. They also manage the supply of spare part and supplies. Certain jobs in this sector require working shifts, especially in manufacturing. Maintenance engineers can move up to managerial positions depending on their work. They may also pursue other jobs in the same industry. After they have gained experience, they may be able to start their own business.
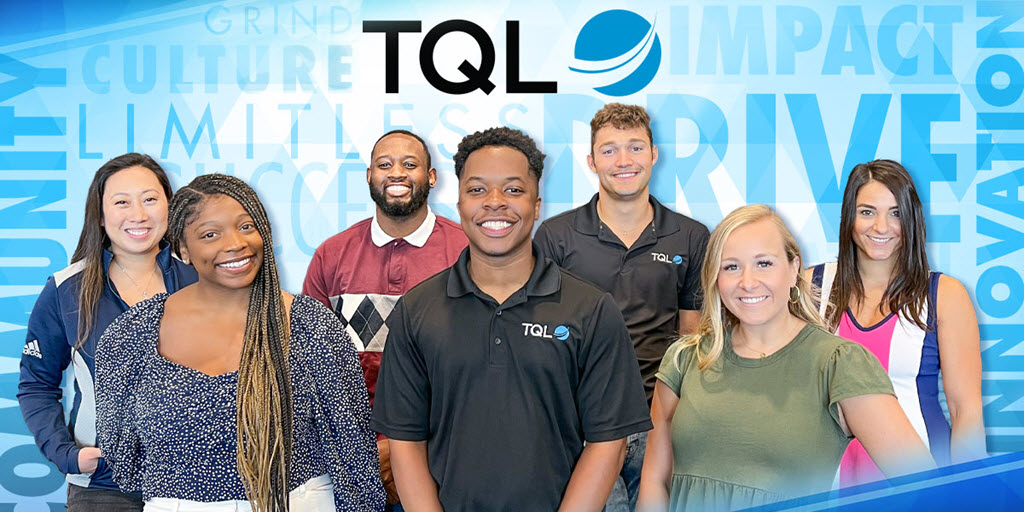
Maintenance engineers earn between PS20,000 and PS25,000 on average. Salaries can vary depending on the size and industry of the organization. Maintenance engineers can also move up to managerial positions that require leadership skills. You may also be able to achieve Chartered status, which can help you move up in your career.
Certifications are required
As a maintenance engineer, you may be required to hold several certifications. These certifications can be specific to one system or may relate to hazardous material handling. The International Maintenance Institute offers several levels of professional certification. These certifications include certifications at the lower levels for Certified Maintenance Technicians as well as certifications at the higher levels for Certified Management Professionals and Maintenance Managers.
Consider your educational background before you consider becoming a maintenance technician. Although certification agencies don't require you to have any particular educational qualifications, some prefer that you have a highschool diploma or GED. This is the minimum requirement for most employers and recruiters. If you have previous work experience in the same industry, you may be able to obtain certification without a degree.
While a bachelor's is not necessary to become a maintenance engineering professional, a degree that's relevant will help you stand apart from the crowd. An engineering degree in mechanical engineering, electrical engineering or facilities management might be helpful. Even if a degree in engineering is not necessary, you could find work as either a maintenance technician or working your way up to maintenance engineer with experience and training.
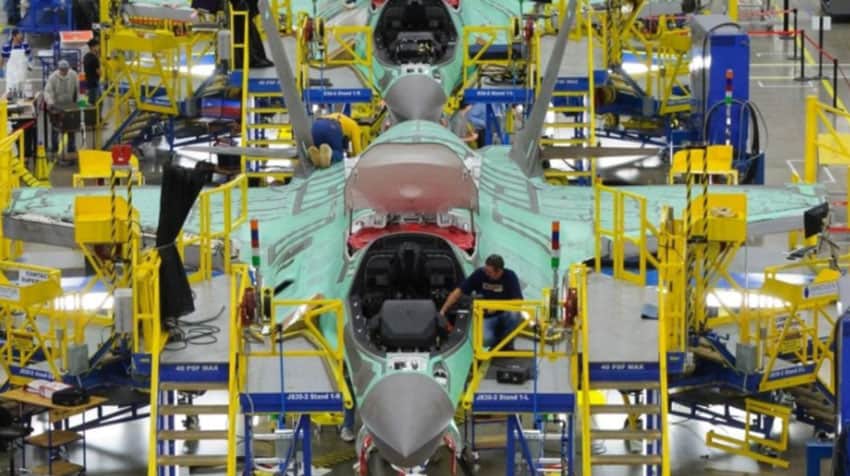
Salary
Although the Bureau of Labor Statistics doesn't monitor the salaries of maintenance engineers, it projects job growth in related areas. General maintenance workers and mechanical engineers will see a 8% increase, while construction managers could see an 11% increase in employment. It is important to focus your search for entry-level job opportunities in industries with high growth if you are considering a career of maintenance engineer.
Maintenance engineer salary: In 2008 the median salary was $88,570. The lowest 25% earned $48,270 while the highest 10% earned more than $110,000.
FAQ
What does it take to run a logistics business?
It takes a lot of skills and knowledge to run a successful logistics business. For clients and suppliers to be successful, you need to have excellent communication skills. You must be able analyze data and draw out conclusions. You must be able and able to handle stress situations and work under pressure. In order to innovate and create new ways to improve efficiency, creativity is essential. To motivate and guide your team towards reaching organizational goals, you must have strong leadership skills.
It is also important to be efficient and well organized in order meet deadlines.
How can I find out more about manufacturing?
Practical experience is the best way of learning about manufacturing. You can also read educational videos or take classes if this isn't possible.
What are the responsibilities of a production planner
Production planners make sure that every aspect of the project is delivered on-time, within budget, and within schedule. They also ensure the quality of the product and service meets the client's requirements.
What is the role of a logistics manager
Logistics managers are responsible for ensuring that all goods arrive in perfect condition and on time. This is done using his/her knowledge of the company's products. He/she should make sure that enough stock is on hand to meet the demands.
Statistics
- According to a Statista study, U.S. businesses spent $1.63 trillion on logistics in 2019, moving goods from origin to end user through various supply chain network segments. (netsuite.com)
- Job #1 is delivering the ordered product according to specifications: color, size, brand, and quantity. (netsuite.com)
- According to the United Nations Industrial Development Organization (UNIDO), China is the top manufacturer worldwide by 2019 output, producing 28.7% of the total global manufacturing output, followed by the United States, Japan, Germany, and India.[52][53] (en.wikipedia.org)
- Many factories witnessed a 30% increase in output due to the shift to electric motors. (en.wikipedia.org)
- In the United States, for example, manufacturing makes up 15% of the economic output. (twi-global.com)
External Links
How To
How to Use Lean Manufacturing for the Production of Goods
Lean manufacturing is an approach to management that aims for efficiency and waste reduction. It was first developed in Japan in the 1970s/80s by Taiichi Ahno, who was awarded the Toyota Production System (TPS), award from KanjiToyoda, the founder of TPS. Michael L. Watkins published the original book on lean manufacturing, "The Machine That Changed the World," in 1990.
Lean manufacturing, often described as a set and practice of principles, is aimed at improving the quality, speed, cost, and efficiency of products, services, and other activities. It emphasizes reducing defects and eliminating waste throughout the value chain. Lean manufacturing is also known as just in time (JIT), zero defect total productive maintenance(TPM), and five-star (S). Lean manufacturing eliminates non-value-added tasks like inspection, rework, waiting.
Lean manufacturing not only improves product quality but also reduces costs. Companies can also achieve their goals faster by reducing employee turnover. Lean Manufacturing is one of the most efficient ways to manage the entire value chains, including suppliers and customers as well distributors and retailers. Lean manufacturing is widely practiced in many industries around the world. For example, Toyota's philosophy underpins its success in automobiles, electronics, appliances, healthcare, chemical engineering, aerospace, paper, food, etc.
Five basic principles of Lean Manufacturing are included in lean manufacturing
-
Define Value- Identify the added value your company brings to society. What makes you stand out from your competitors?
-
Reduce Waste – Eliminate all activities that don't add value throughout the supply chain.
-
Create Flow - Ensure work moves smoothly through the process without interruption.
-
Standardize and simplify - Make your processes as consistent as possible.
-
Build Relationships - Establish personal relationships with both internal and external stakeholders.
Although lean manufacturing has always been around, it is gaining popularity in recent years because of a renewed interest for the economy after 2008's global financial crisis. Many businesses have adopted lean production techniques to make them more competitive. Many economists believe lean manufacturing will play a major role in economic recovery.
Lean manufacturing, which has many benefits, is now a standard practice in the automotive industry. These include higher customer satisfaction levels, reduced inventory levels as well as lower operating costs.
The principles of lean manufacturing can be applied in almost any area of an organization. It is especially useful for the production aspect of an organization, as it ensures that every step in the value chain is efficient and effective.
There are three main types in lean manufacturing
-
Just-in-Time Manufacturing (JIT): This type of lean manufacturing is commonly referred to as "pull systems." JIT refers to a system in which components are assembled at the point of use instead of being produced ahead of time. This method reduces lead times, increases availability, and decreases inventory.
-
Zero Defects Manufacturing (ZDM),: ZDM is a system that ensures no defective units are left the manufacturing facility. If a part needs to be fixed during the assembly line, it should be repaired rather than scrapped. This is also true for finished products that require minor repairs before shipping.
-
Continuous Improvement (CI), also known as Continuous Improvement, aims at improving the efficiency of operations through continuous identification and improvement to minimize or eliminate waste. Continuous Improvement (CI) involves continuous improvement in processes, people, tools, and infrastructure.