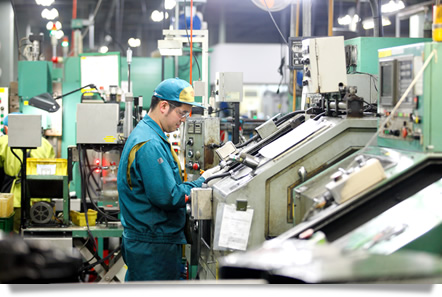
Although value stream mapping can be a great way to improve manufacturing processes, it can be difficult. This involves mapping product families and their products. To do it properly, your team needs training, and you might even have a value stream manager. The leadership should also be involved in the implementation of the strategy. Larger companies have value stream managers who are responsible for the mapping process. Although smaller companies may be able to do without a VSM manager it is beneficial to communicate with the leadership about the potential improvements.
Lean Six Sigma
Value Stream Mapping with Lean Six Sigma allows you record the flow from customers to suppliers using Value Stream Mapping. Your customer is the first thing you should put on your value streammap. If you are in the shipping region, begin there and work upwards. Include a box that contains customer's data. This will show you how often the product must be made to meet the demand. You'll also need to know the Takt time (the amount of time it takes to produce a product), and how it compares to the cycle time of the product. If Takt time is longer than the cycle time, it indicates a bottleneck.
Value stream maps can be used to help companies identify and eliminate waste in every stage of their business processes. Value stream mapping helps you to identify and analyze non-value-added activity and the flow information. It is also useful in identifying bottlenecks or determining how to improve the efficiency of the whole process. Value Stream mapping in Lean Six Sigma is more than just improving the flow information. A Value Stream Map may be a valuable tool to help implement Lean Six Sigma.
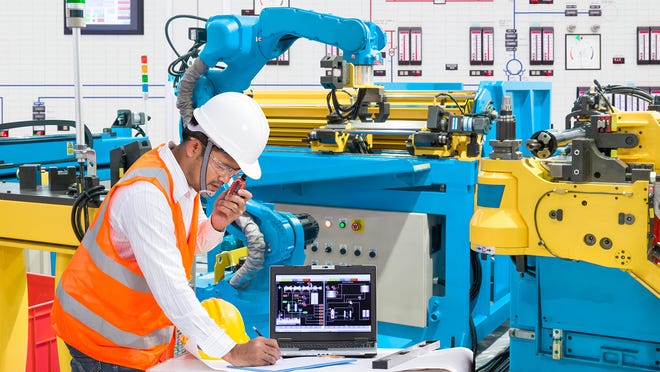
Lean Healthcare
Value stream mapping can be used to improve the synchronization between activities within the medical field. It helps to identify opportunities for improvement and determines strategies for implementation. A map could show a patient's flow, from their arrival at the hospital to when they leave after treatment. These flow paths can be used to visualize the entire process and help identify value-added and waste-generating actions.
To make VSM in Lean Healthcare more efficient, the authors recommend that clear definitions be established for all terms. They also recommend establishing appropriate indicators and sharing examples of success and failure. These will allow the results to be replicated and modified for specific situations. Positive outcomes are more likely to be achieved by using lean methods in the healthcare sector. The authors suggest that there be a common definition and use of value stream mapping within the healthcare sector to ensure that these benefits are shared across the entire health care system.
Lean Manufacturing
In order to begin value stream mapping, you need input from key stakeholders. This team should include the people responsible for fulfilling customer needs. They should also include people who perform critical tasks and activities to ensure the flow of information. This value stream mapping process can be used to identify waste and increase efficiency by gathering input from key stakeholders. The scope of the value streaming mapping process must be defined.
Next, identify the product/process you wish to improve. Then, train your team on value stream mapping. The mapping process begins by identifying the customer's needs. This includes all information received, as well as the communication and decision-making processes. Value stream mapping ultimately aims to eliminate waste while increasing customer satisfaction. Lean manufacturing can help companies find a viable, sustainable solution to their challenges. It involves identifying and eliminating the elements that are important for customer satisfaction.
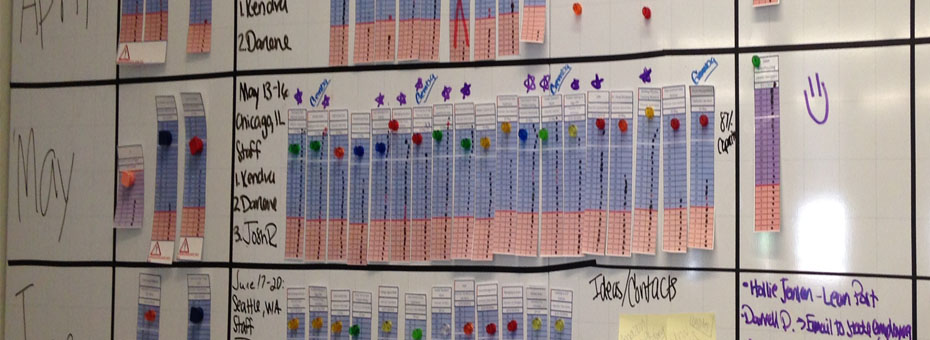
Future state value stream mapping
Future state value streaming mapping is an excellent tool to identify waste. This mapping has two goals: to identify and eliminate the causes of waste. Future state ideas are marked with the same symbols as current state mapping. Takt Time is important to be aware of when planning for future state value streams mapping. It helps you efficiently allocate resources and pinpoint areas of waste. Your company can also use the future state value stream map as a powerful tool.
Once you have identified where there are problems and how they relate to the future, it's now time to map the steps necessary to get there. The future state map can be used by teams as a guideline for completing projects and reaching the target value. You need to keep your future state value stream map updated every six to 12 months so that you can track your progress. You should update your future state map as new projects are launched and modifications made.
FAQ
Do we need to know about Manufacturing Processes before learning about Logistics?
No. It doesn't matter if you don't know anything about manufacturing before you learn about logistics. Understanding the manufacturing process will allow you to better understand logistics.
How can we increase manufacturing efficiency?
First, we need to identify which factors are most critical in affecting production times. We then need to figure out how to improve these variables. If you don't know where to start, then think about which factor(s) have the biggest impact on production time. Once you've identified them, try to find solutions for each of those factors.
What is the job of a logistics manger?
A logistics manager ensures that all goods are delivered on time and without damage. This is achieved by using their knowledge and experience with the products of the company. He/she should also ensure enough stock is available to meet demand.
What is production planning?
Production Planning is the creation of a plan to cover all aspects, such as scheduling, budgeting. Location, crew, equipment, props and other details. This document will ensure everything is in order and ready to go when you need it. It should also contain information on achieving the best results on set. This includes location information, crew details, equipment specifications, and casting lists.
The first step is to outline what you want to film. You may have already chosen the location you want, or there are locations or sets you prefer. Once you have identified the scenes and locations, you can start to determine which elements are required for each scene. For example, you might decide that you need a car but don't know exactly what model you want. To narrow your options, you can search online for available models.
After you have selected the car you want, you can begin to think about additional features. What about additional seating? Maybe you need someone to move around in the back. You may want to change the interior's color from black or white. These questions will help to determine the style and feel of your car. Also, think about what kind of shots you would like to capture. Do you want to film close-ups, or wider angles? Maybe the engine or steering wheel is what you are looking to film. All of these things will help you identify the exact style of car you want to film.
Once you have established all the details, you can create a schedule. You will know when you should start and when you should finish shooting. The schedule will show you when to get there, what time to leave, and when to return home. It will help everyone know exactly what they have to do and when. It is possible to make arrangements in advance for additional staff if you are looking to hire. You should not hire anyone who doesn't show up because of your inaction.
When creating your schedule, you will also need to consider the number of days you need to film. Some projects can be completed in a matter of days or weeks. Others may take several days. You should consider whether you will need more than one shot per week when creating your schedule. Shooting multiple takes over the same location will increase costs and take longer to complete. It is better to be cautious and take fewer shots than you risk losing money if you are not sure if multiple takes are necessary.
Budgeting is another crucial aspect of production plan. Setting a realistic budget is essential as it will allow you to work within your means. If you have to reduce your budget due to unexpected circumstances, you can always lower it later. However, it is important not to overestimate the amount that you will spend. You'll end up with less money after paying for other things if the cost is underestimated.
Production planning is a very detailed process, but once you understand how everything works together, it becomes easier to plan future projects.
What does it take to run a logistics business?
You need to have a lot of knowledge and skills to manage a successful logistic business. You must have good communication skills to interact effectively with your clients and suppliers. It is important to be able to analyse data and draw conclusions. You need to be able work under pressure and manage stressful situations. You need to be innovative and creative to come up with new ways to increase efficiency. Strong leadership qualities are essential to motivate your team and help them achieve their organizational goals.
You should also be organized and efficient to meet tight deadlines.
What are the 7 Rs of logistics.
The 7R's of Logistics is an acronym for the seven basic principles of logistics management. It was developed by the International Association of Business Logisticians (IABL) and published in 2004 as part of its "Seven Principles of Logistics Management" series.
The acronym is composed of the following letters.
-
Responsible - ensure that actions are in compliance with legal requirements and do not cause harm to others.
-
Reliable: Have faith in your ability or the ability to honor any promises made.
-
It is reasonable to use resources efficiently and not waste them.
-
Realistic – consider all aspects of operations, from cost-effectiveness to environmental impact.
-
Respectful - treat people fairly and equitably.
-
Resourceful - look for opportunities to save money and increase productivity.
-
Recognizable: Provide customers with value-added service
Statistics
- According to the United Nations Industrial Development Organization (UNIDO), China is the top manufacturer worldwide by 2019 output, producing 28.7% of the total global manufacturing output, followed by the United States, Japan, Germany, and India.[52][53] (en.wikipedia.org)
- In the United States, for example, manufacturing makes up 15% of the economic output. (twi-global.com)
- [54][55] These are the top 50 countries by the total value of manufacturing output in US dollars for its noted year according to World Bank.[56] (en.wikipedia.org)
- Many factories witnessed a 30% increase in output due to the shift to electric motors. (en.wikipedia.org)
- According to a Statista study, U.S. businesses spent $1.63 trillion on logistics in 2019, moving goods from origin to end user through various supply chain network segments. (netsuite.com)
External Links
How To
How to Use Six Sigma in Manufacturing
Six Sigma is "the application statistical process control (SPC), techniques for continuous improvement." Motorola's Quality Improvement Department created Six Sigma at their Tokyo plant, Japan in 1986. Six Sigma's basic concept is to improve quality and eliminate defects through standardization. Since there are no perfect products, or services, this approach has been adopted by many companies over the years. Six Sigma aims to reduce variation in the production's mean value. This means that you can take a sample from your product and then compare its performance to the average to find out how often the process differs from the norm. If this deviation is too big, you know something needs fixing.
Understanding the nature of variability in your business is the first step to Six Sigma. Once you have a good understanding of the basics, you can identify potential sources of variation. This will allow you to decide if these variations are random and systematic. Random variations occur when people do mistakes. Symmetrical variations are caused due to factors beyond the process. Random variations would include, for example, the failure of some widgets to fall from the assembly line. If however, you notice that each time you assemble a widget it falls apart in exactly the same spot, that is a problem.
Once you identify the problem areas, it is time to create solutions. The solution could involve changing how you do things, or redesigning your entire process. Test them again once you've implemented the changes. If they didn't work, then you'll need to go back to the drawing board and come up with another plan.