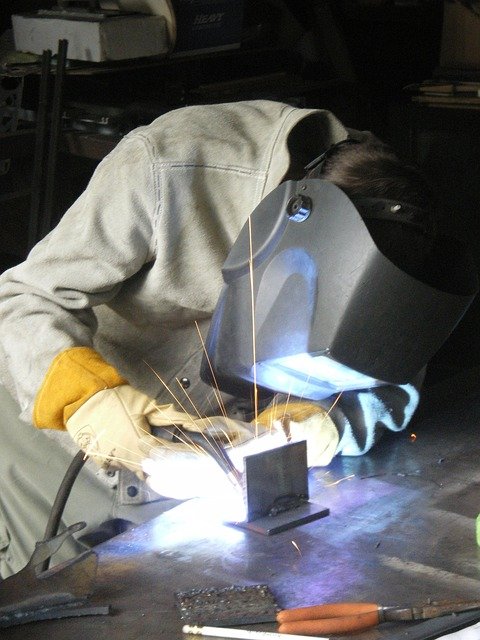
Advanced manufacturing is the application of new technology to improve products and processes. The technology used to achieve this can be classified as "advanced," "innovative," or "cutting edge." Advanced manufacturing is becoming more popular as companies use newer and more innovative technologies in their manufacturing processes. Below are examples of advanced production. Below are some of most used technologies for advanced manufacturing.
Continuous manufacturing
Continuous manufacturing is first mentioned in the 1700s as a method of making pig iron in blast ovens. This concept has spread to many industries such as the automotive, food oil and refining industries, chemical industries, and pulp and papers industries. Continuous manufacturing has captured the attention of CMOs from top pharma and other big players in the biopharmaceutical market.
In a recent commentary, FDA and its collaborators discussed the benefits to continuous manufacturing when producing therapeutic proteins. This legislation would create national centres to promote the field and assist companies in creating standards. The goal is to help the industry improve the process of creating and using medical products. This would encourage companies using continuous manufacturing to improve their products. But it is essential to ensure that continuous manufacture processes are safe.
Automated processes
Automating advanced manufacturing processes is a great way to increase efficiency and reduce costs. In many cases, automation is the most effective way to make the most of floor space while also maximizing production efficiency. Utilizing automation technologies and data collection, manufacturers can lower costs and increase productivity through better equipment use. Automation of the process industry can also help save time and money. Although the initial investment may be large, the end result will increase the profitability of a manufacturing business.
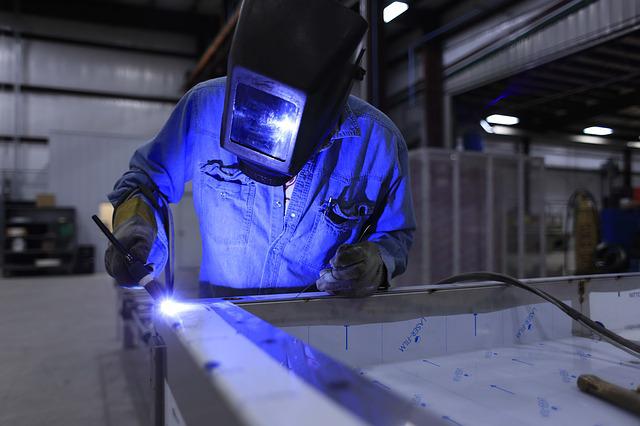
Companies combine automated processes with advanced manufacturing techniques today. For example, companies such as Audi are using automated welding and bonding processes to reduce production time, while simultaneously saving energy and weight. Advanced manufacturing systems, such as regenerative brakes in conveyor systems, are also used by them. 3D printing has made the biggest leap in manufacturing, although it's been around since at least 1980s. However, this technology has only recently gained mainstream acceptance. But what makes it so appealing to manufacturers, you ask?
Internet of Things
The IIoT revolution transforms manufacturing by using sensors to monitor machines as well as their processes. These sensors collect data from various parts of the manufacturing process, and then feed it into a central station. The data can be analysed and used to optimize processes and eliminate wasted. Advanced manufacturers use IIoT to monitor production processes and optimize their output. The IIoT can be described as the industrial equivalent of key fobs.
IIoT deployment needs a detailed roadmap and development capabilities in order to deploy use cases efficiently and scale effectively. Three waves of deployment are shown in the following roadmap from an automaker:
Cost-effectiveness
Advanced manufacturing is not always cheaper than traditional production. It is more likely that the traditional cost-benefit model is insufficient to assess economic benefits. However, a holistic model that considers both costs and benefits of technology can help to identify new benefits and accelerate decision-making processes. Munker and Schroer develop a cost-benefit tool to address the main issues involved in AMS implementation.
Information technology advances are changing rapidly the face of manufacturing, as well as their costs. Manufacturing systems are becoming more connected and intelligent. Meanwhile, cost pressure is putting increased focus on productivity and a company's ability to respond to customer needs. Rapid adoption of advanced manufacturing technology will likely speed up the implementation of these technologies as well as their cost-effectiveness. As the industry digitizes, so will the adoption of these technologies.
Human error reduction
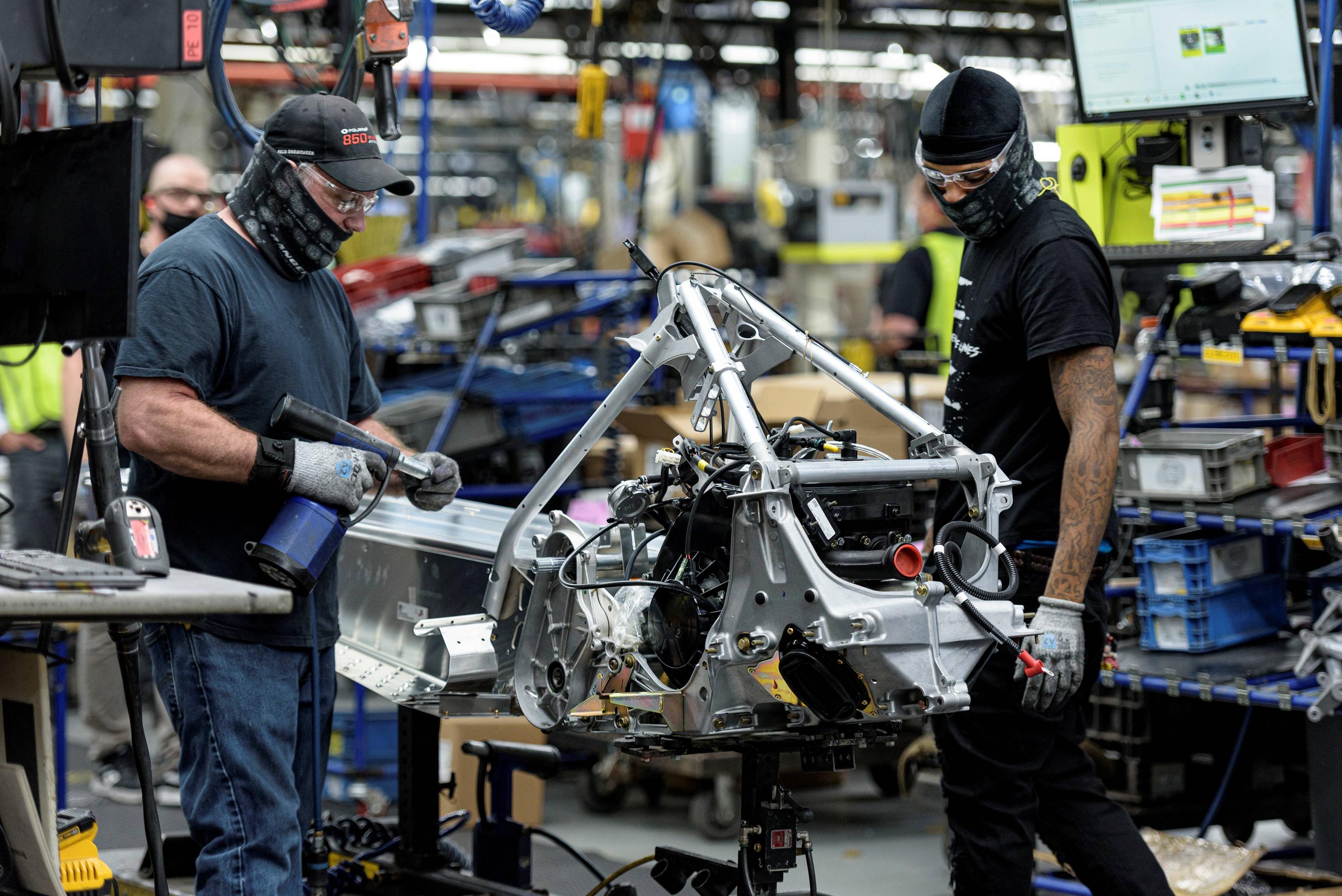
Although human beings can make mistakes sometimes, the production process is often designed to protect them. Human error may occur when employees do not follow the instructions or fail in writing. When they make drugs, pharmaceutical laboratories for example must follow certain procedures. Sometimes, employees might believe that they have learned the process and are familiar with the precise amounts of ingredients. So they start to make the mixture, without ever consulting the written instructions.
Effective communication between senior and junior employees is another way to reduce human error. Managers must refrain from punishing employees for asking question. Employees are more likely than ever to make mistakes if they're treated harshly. Employees need to feel comfortable asking questions, and if they feel uncomfortable with the way they are treated, they will not be likely to take corrective actions. It is important to establish a healthy relationship between senior and junior employees. Also, it is important to address communication issues in a polite and professional manner.
FAQ
How can manufacturing avoid production bottlenecks
You can avoid bottlenecks in production by making sure that everything runs smoothly throughout the production cycle, from the moment you receive an order to the moment the product is shipped.
This includes planning to meet capacity requirements and quality control.
Continuous improvement techniques such Six Sigma are the best method to accomplish this.
Six Sigma Management System is a method to increase quality and reduce waste throughout your organization.
It is focused on creating consistency and eliminating variation in your work.
How does a Production Planner differ from a Project Manager?
The difference between a product planner and project manager is that a planer is typically the one who organizes and plans the entire project. A production planner, however, is mostly involved in the planning stages.
What does "warehouse" mean?
A warehouse is a place where goods are stored until they are sold. It can be either an indoor or outdoor space. Sometimes, it can be both an indoor and outdoor space.
What does it mean to be a manufacturer?
Manufacturing Industries are companies that manufacture products. Consumers are people who purchase these goods. This is accomplished by using a variety of processes, including production, distribution and retailing. They create goods from raw materials, using machines and various other equipment. This includes all types if manufactured goods.
Statistics
- Job #1 is delivering the ordered product according to specifications: color, size, brand, and quantity. (netsuite.com)
- (2:04) MTO is a production technique wherein products are customized according to customer specifications, and production only starts after an order is received. (oracle.com)
- In 2021, an estimated 12.1 million Americans work in the manufacturing sector.6 (investopedia.com)
- In the United States, for example, manufacturing makes up 15% of the economic output. (twi-global.com)
- [54][55] These are the top 50 countries by the total value of manufacturing output in US dollars for its noted year according to World Bank.[56] (en.wikipedia.org)
External Links
How To
Six Sigma and Manufacturing
Six Sigma can be described as "the use of statistical process control (SPC), techniques to achieve continuous improvement." Motorola's Quality Improvement Department, Tokyo, Japan, developed it in 1986. Six Sigma is a method to improve quality through standardization and elimination of defects. In recent years, many companies have adopted this method because they believe there is no such thing as perfect products or services. Six Sigma seeks to reduce variation between the mean production value. If you take a sample and compare it with the average, you will be able to determine how much of the production process is different from the norm. If this deviation is too big, you know something needs fixing.
Understanding how your business' variability is a key step towards Six Sigma implementation is the first. Once you have a good understanding of the basics, you can identify potential sources of variation. It is important to identify whether the variations are random or systemic. Random variations are caused when people make mistakes. While systematic variations are caused outside of the process, they can occur. If you make widgets and some of them end up on the assembly line, then those are considered random variations. However, if you notice that every time you assemble a widget, it always falls apart at exactly the same place, then that would be a systematic problem.
Once you've identified where the problems lie, you'll want to design solutions to eliminate those problems. This could mean changing your approach or redesigning the entire process. You should then test the changes again after they have been implemented. If they fail, you can go back to the drawing board to come up with a different plan.