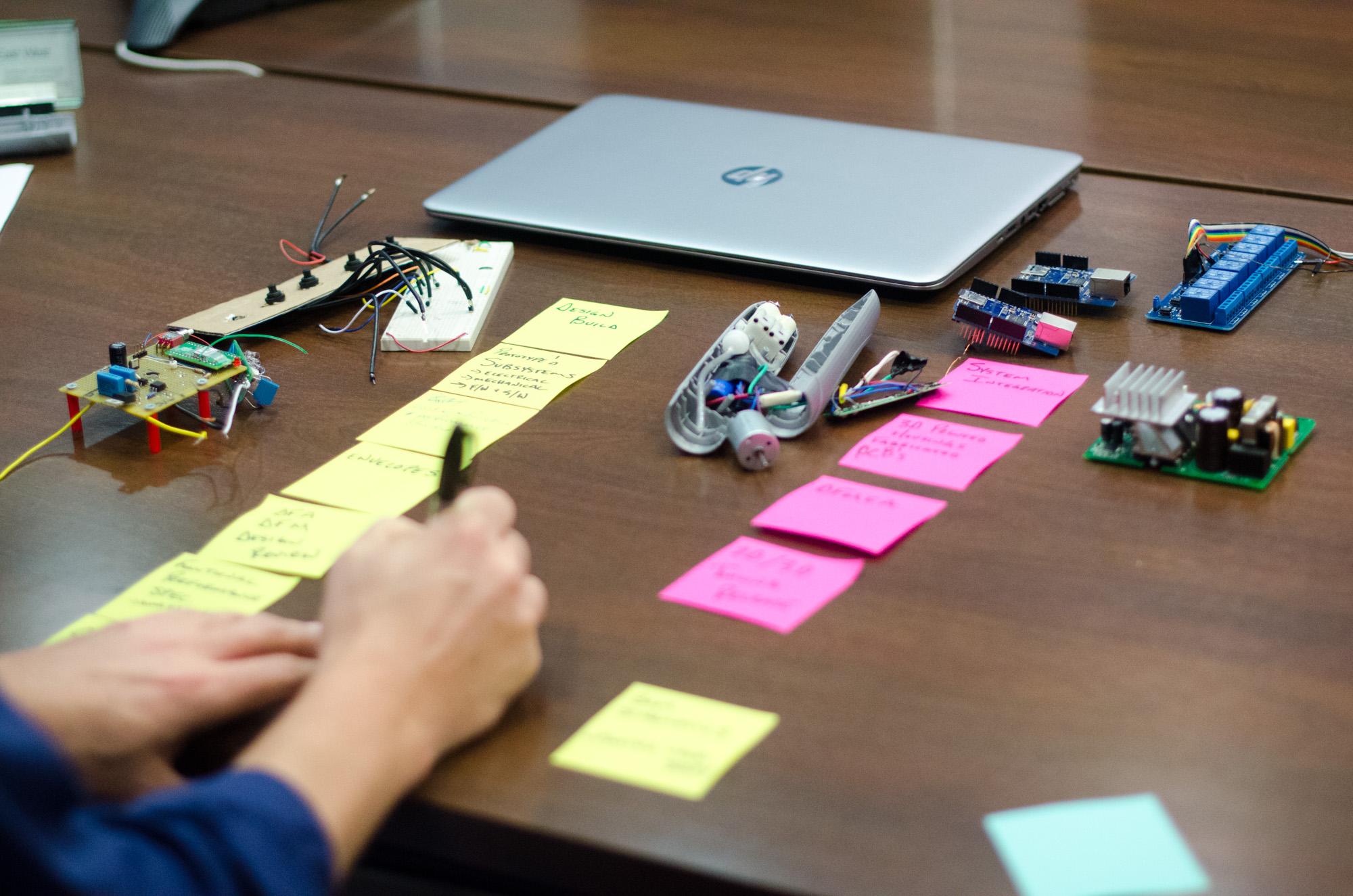
Supply networks are complex adaptive systems in which many companies participate in the delivery and collection of goods and services. A supply network is composed of several interrelated industries that supply raw materials, goods and other commodities. A supply network can be used for more than just traditional functions. It can also be used as a platform to distribute digital resources and flows.
As supply networks develop, they take on many forms. The key is to make sure that your system is resilient to unexpected events. This requires knowledge of the different supply networks, and how they might react to disruptions. This problem has been addressed by several approaches.
One approach to assessing resilience is to analyze the flow of information. This is a good place where to begin: the information flow between the customer and the preceding organizations. It's also an effective way to gauge the strength or a relationship. For example, if the first supplier is connected to second supplier, the manufacturer might be in a position to spot missing links.
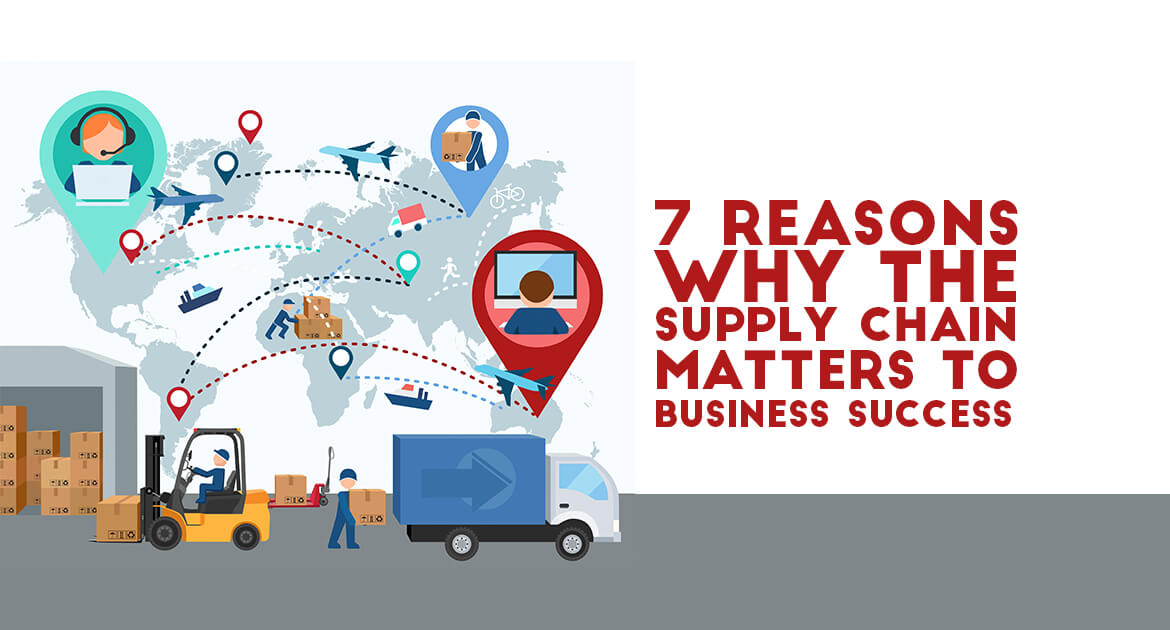
A supply network that facilitates this type of flow will be able to deliver the desired product or services to the end-customer. Implementing such a smart approach to supply chain management isn't as easy as it sounds. First, companies need to find a way out of the existing network constraints. Second, they must ensure that their approach to managing the flow of information is sufficiently robust to withstand disruptions.
Another important aspect of the supply network is the role of intermediaries. These entities are often not well-understood. As an example, a semiconductor manufacturer may move work-in process material from fabrication to assembly. Manufacturing companies can speed up and improve their production efficiency by properly moving these materials. Likewise, a manufacturing firm that has a strong reliance on procuring subcomponents from other firms can scale up or down depending on its production needs.
Unexpected results can be achieved by incorporating the different intermediaries into your supply network model. Better communication can result, among other benefits, in higher productivity and efficiency. Additionally, strong partnerships can help organisations improve their service to customers.
High to moderate levels of complexity are common in supply networks. This is because suppliers are responsible for making decisions about which goods to buy and which items to re-sell. The overall network must also be functional. Therefore, power asymmetries can be common. These are easily managed by a few key strategies.
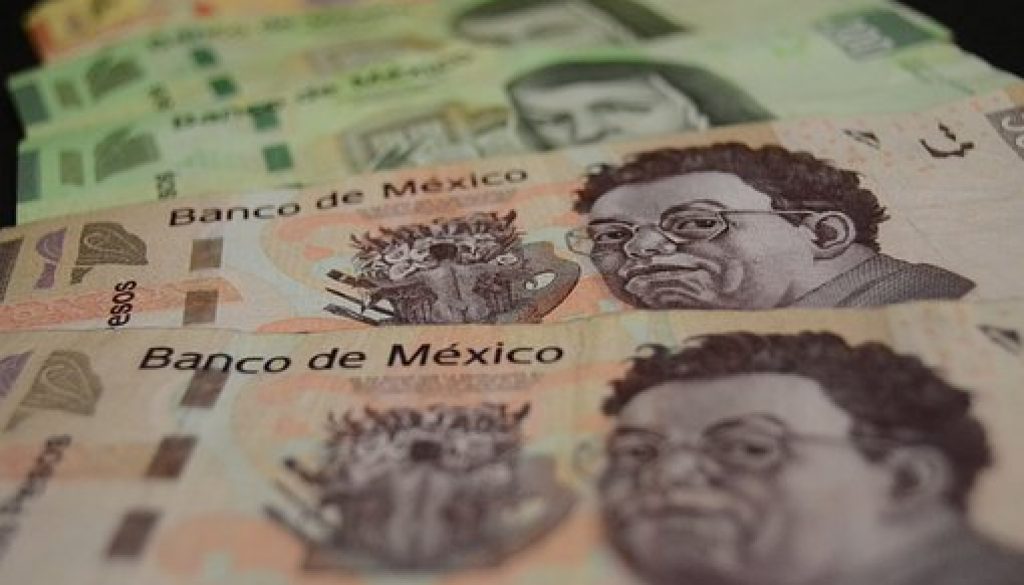
There are several ways to reduce this problem. One way is to set up a control tower that monitors and manages suppliers. Another way is to create a data center to analyse and gather data. A third option is to use an automated decision-making system. You can also use a rebalancing program to correct imbalances or a buffer plan to protect your network in case it is disrupted. Lastly, suppliers who are able to anticipate and meet their clients' needs may be able to avoid a supply network meltdown.
FAQ
What are the essential elements of running a logistics firm?
To run a successful logistics company, you need a lot knowledge and skills. To communicate effectively with clients and suppliers, you must be able to communicate well. It is important to be able to analyse data and draw conclusions. You need to be able work under pressure and manage stressful situations. You need to be innovative and creative to come up with new ways to increase efficiency. Strong leadership qualities are essential to motivate your team and help them achieve their organizational goals.
To meet tight deadlines, you must also be efficient and organized.
What are the 7 Rs of logistics?
The 7R's of Logistics is an acronym for the seven basic principles of logistics management. It was developed and published by the International Association of Business Logisticians in 2004 as part of the "Seven Principles of Logistics Management".
The acronym consists of the following letters:
-
Responsible - to ensure that all actions are within the legal requirements and are not detrimental to others.
-
Reliable: Have faith in your ability or the ability to honor any promises made.
-
Use resources effectively and sparingly.
-
Realistic - Take into consideration all aspects of operations including cost-effectiveness, environmental impact, and other factors.
-
Respectful - treat people fairly and equitably.
-
Be resourceful: Look for opportunities to save money or increase productivity.
-
Recognizable - provide customers with value-added services.
What are manufacturing and logistic?
Manufacturing is the act of producing goods from raw materials using machines and processes. Logistics manages all aspects of the supply chain, including procurement, production planning and distribution, inventory control, transportation, customer service, and transport. Manufacturing and logistics are often considered together as a broader term that encompasses both the process of creating products and delivering them to customers.
What does "warehouse" mean?
A warehouse is a place where goods are stored until they are sold. It can be an indoor space or an outdoor area. In some cases it could be both indoors and outdoors.
How can manufacturing avoid production bottlenecks
Avoiding production bottlenecks is as simple as keeping all processes running smoothly, from the time an order is received until the product ships.
This includes both planning for capacity and quality control.
Continuous improvement techniques such Six Sigma can help you achieve this.
Six Sigma is a management method that helps to improve quality and reduce waste.
It is focused on creating consistency and eliminating variation in your work.
Why automate your factory?
Modern warehouses are increasingly dependent on automation. With the rise of ecommerce, there is a greater demand for faster delivery times as well as more efficient processes.
Warehouses must be able to quickly adapt to changing demands. Technology investment is necessary to enable warehouses to respond quickly to changing demands. Automation warehouses can bring many benefits. Here are some of the reasons automation is worth your investment:
-
Increases throughput/productivity
-
Reduces errors
-
Accuracy is improved
-
Safety increases
-
Eliminates bottlenecks
-
Allows companies to scale more easily
-
Makes workers more efficient
-
Gives you visibility into all that is happening in your warehouse
-
Enhances customer experience
-
Improves employee satisfaction
-
Reduces downtime and improves uptime
-
High quality products delivered on-time
-
Human error can be eliminated
-
Helps ensure compliance with regulations
Statistics
- According to the United Nations Industrial Development Organization (UNIDO), China is the top manufacturer worldwide by 2019 output, producing 28.7% of the total global manufacturing output, followed by the United States, Japan, Germany, and India.[52][53] (en.wikipedia.org)
- (2:04) MTO is a production technique wherein products are customized according to customer specifications, and production only starts after an order is received. (oracle.com)
- Job #1 is delivering the ordered product according to specifications: color, size, brand, and quantity. (netsuite.com)
- In the United States, for example, manufacturing makes up 15% of the economic output. (twi-global.com)
- Many factories witnessed a 30% increase in output due to the shift to electric motors. (en.wikipedia.org)
External Links
How To
Six Sigma in Manufacturing:
Six Sigma is "the application statistical process control (SPC), techniques for continuous improvement." Motorola's Quality Improvement Department in Tokyo, Japan developed Six Sigma in 1986. Six Sigma's basic concept is to improve quality and eliminate defects through standardization. Many companies have adopted this method in recent years. They believe there is no such thing a perfect product or service. The main goal of Six Sigma is to reduce variation from the mean value of production. This means that you can take a sample from your product and then compare its performance to the average to find out how often the process differs from the norm. If there is a significant deviation from the norm, you will know that something needs to change.
Understanding the nature of variability in your business is the first step to Six Sigma. Once you understand this, you can then identify the causes of variation. You'll also want to determine whether these variations are random or systematic. Random variations occur when people do mistakes. Symmetrical variations are caused due to factors beyond the process. These are, for instance, random variations that occur when widgets are made and some fall off the production line. It would be considered a systematic problem if every widget that you build falls apart at the same location each time.
Once you have identified the problem, you can design solutions. You might need to change the way you work or completely redesign the process. You should then test the changes again after they have been implemented. If they didn't work, then you'll need to go back to the drawing board and come up with another plan.