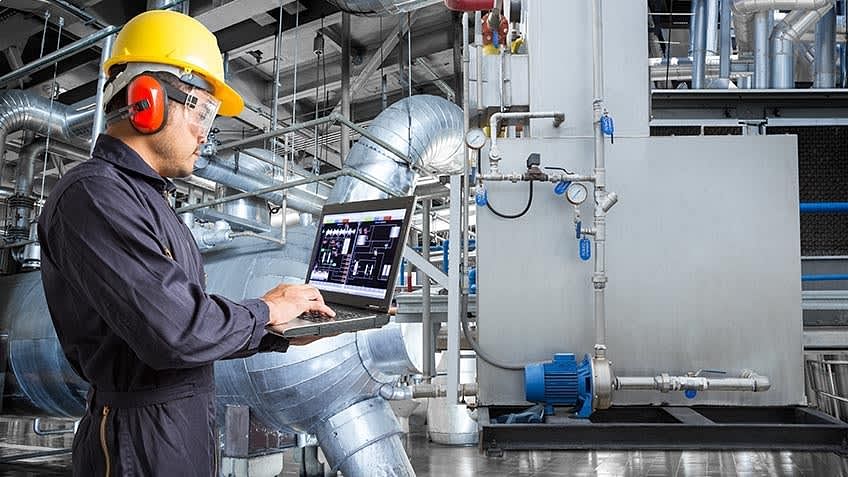
For the job of an engineering and architectural manager, an education degree is typically required. Many of these professionals work in offices but some also work on construction sites. They have either a bachelor's or master's degree in engineering or architecture and have extensive field experience. To complement their education, some choose to pursue a graduate degree in business administration. There are many paths to advancement in this profession. Consider a MBA to help you get a job as an architect or engineer manager.
The occupational outlook for engineering and architectural managers
The outlook for employment of architectural and engineering managers is favorable. Over the next decade, the number of job openings is expected to grow by about two percent. This will be due in part to the growth of several industries. Nevertheless, competition for available jobs will be stiff. The O*NET website provides more information about the career outlook in this field.
Engineer and architectural managers plan and manage activities within an engineering or architectural firm. Using their knowledge of architecture, they are responsible for the planning, design, construction, and management of a wide range of activities. This could include large-scale building design, construction and maintenance, as well as engineering research or site management. They are also responsible to the design and development of new products. They need to determine the desired technical goals of the company and develop detailed plans to achieve these goals.
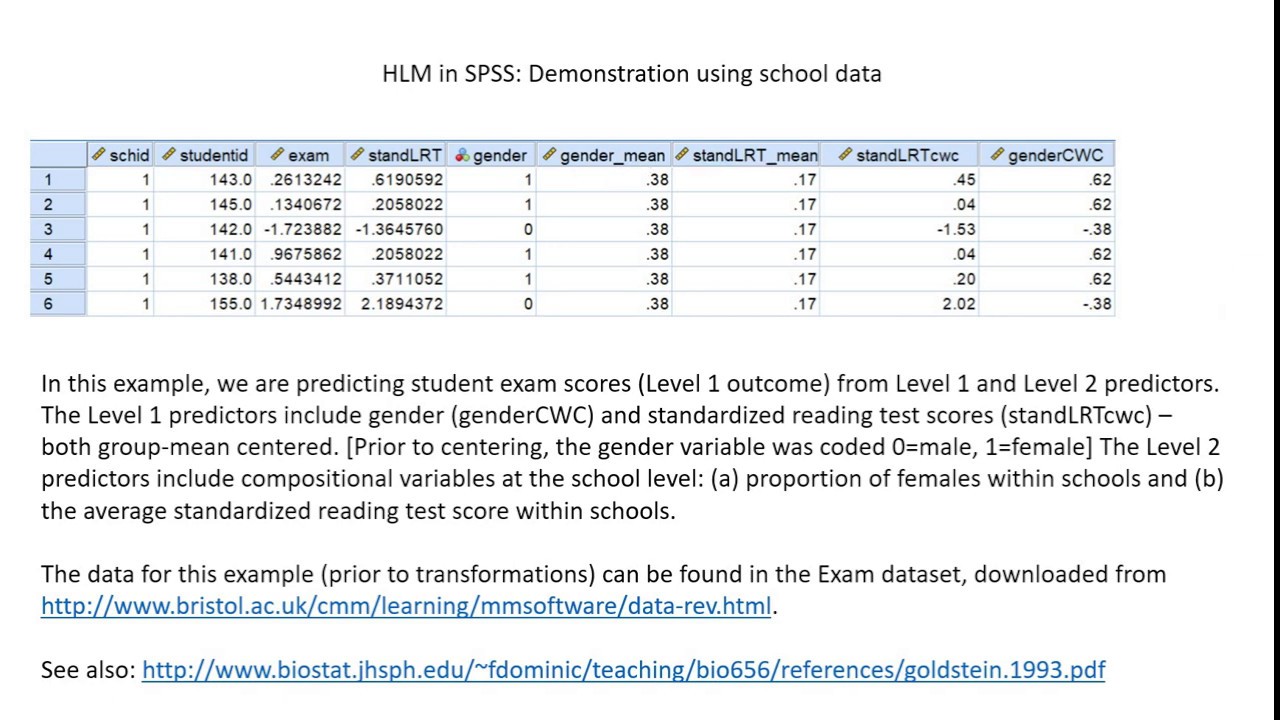
This field requires applicants to have at least a master's in management. It all depends on your choice of type of management role. An engineering master's can prepare you for technical managerial positions while a master's of business administration can give you broader management skills. Both types of graduate programs require at least one year to complete.
Education Required
Engineering managers and architects need to be educated. These managers oversee the day-today operations of engineering departments. They provide supervision and training for staff. They provide guidance and budgeting for employees. However, if you're considering a career in this field, consider getting a bachelor's degree in this field.
While the vast majority of these managers have a bachelor's degree in engineering or architecture, many have obtained advanced degrees in business administration or technology management. A graduate degree in engineering management or technology management, known as MsEM, will also give you the necessary management skills for the position. Strong communication and analytical skills are essential.
The responsibility of architects and engineers managers is to implement new projects while maintaining high quality end products. They consider the impact on the environment, as well the needs and wants of users. These professionals prepare detailed plans and budgets based on technical specifications. They supervise teams of engineers to successfully execute projects.
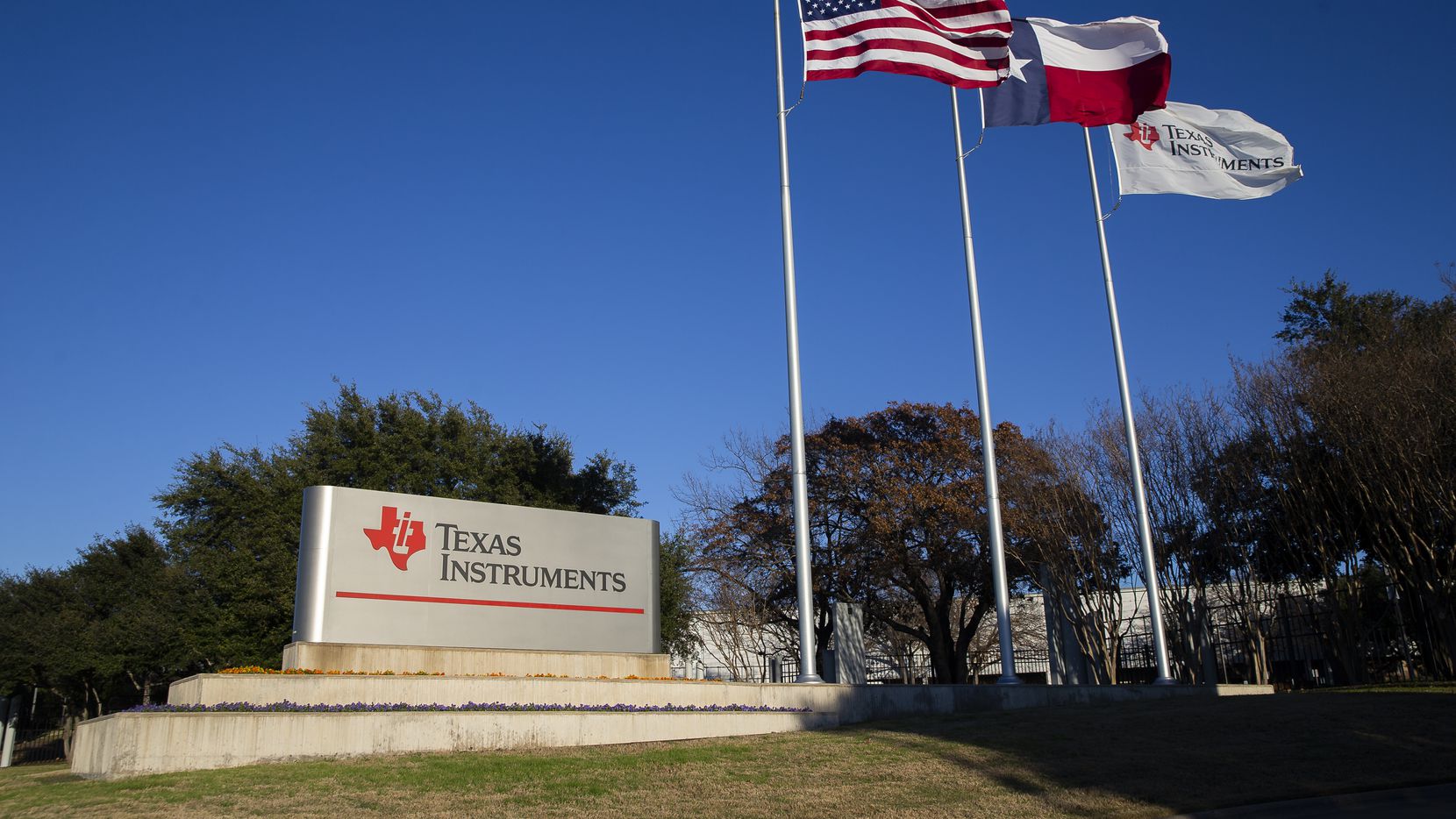
Earning potential
Over the next decade, the earning potential of engineers and architects will increase by 13 percent. The growth in the engineering sector is expected to lead to an increase in the number of job opportunities in this field. Despite the fact that the number of jobs in this industry is expected to increase, competition will remain intense. The industry's growth rate will be lower than the average for all occupations.
This occupation's salary range will vary depending on the level of education and whereabouts you live. A salary range of $75,190 for an entry-level job in this field is typical. A candidate with between four and five years of work experience will earn at least $104,800. Meanwhile, those with at least ten years of experience can expect to make around $156,620 per year.
FAQ
What type of jobs is there in logistics
There are many kinds of jobs available within logistics. Some of them are:
-
Warehouse workers - They load and unload trucks and pallets.
-
Transportation drivers – These drivers drive trucks and wagons to transport goods and pick up the goods.
-
Freight handlers - They sort and pack freight in warehouses.
-
Inventory managers – These people oversee inventory at warehouses.
-
Sales reps are people who sell products to customers.
-
Logistics coordinators - They plan and organize logistics operations.
-
Purchasing agents - They buy goods and services that are necessary for company operations.
-
Customer service agents - They answer phone calls and respond to emails.
-
Shipping clerks: They process shipping requests and issue bills.
-
Order fillers – They fill orders based upon what was ordered and shipped.
-
Quality control inspectors - They check incoming and outgoing products for defects.
-
Others - There is a variety of other jobs in logistics. These include transportation supervisors and cargo specialists.
What are the 7 Rs of logistics?
The acronym 7R's for Logistics stands to represent the seven basic principles in logistics management. It was developed and published by the International Association of Business Logisticians in 2004 as part of the "Seven Principles of Logistics Management".
The acronym is composed of the following letters.
-
Responsible - to ensure that all actions are within the legal requirements and are not detrimental to others.
-
Reliable - have confidence in the ability to deliver on commitments made.
-
Be responsible - Use resources efficiently and avoid wasting them.
-
Realistic – Consider all aspects, including cost-effectiveness as well as environmental impact.
-
Respectful - Treat people fairly and equitably
-
You are resourceful and look for ways to save money while increasing productivity.
-
Recognizable: Provide customers with value-added service
How can overproduction in manufacturing be reduced?
In order to reduce excess production, you need to develop better inventory management methods. This would decrease the time that is spent on inefficient activities like purchasing, storing, or maintaining excess stock. This would allow us to use our resources for more productive tasks.
This can be done by using a Kanban system. A Kanban board can be used to monitor work progress. Work items are moved through various states to reach their destination in a Kanban system. Each state represents an individual priority level.
To illustrate, work can move from one stage or another when it is complete enough for it to be moved to a new stage. But if a task remains in the beginning stages it will stay that way until it reaches its end.
This allows work to move forward and ensures that no work is missed. Managers can monitor the work being done by Kanban boards to see what is happening at any given time. This allows them to adjust their workflows based on real-time information.
Lean manufacturing is another option to control inventory levels. Lean manufacturing seeks to eliminate waste from every step of the production cycle. Anything that does nothing to add value to a product is waste. The following are examples of common waste types:
-
Overproduction
-
Inventory
-
Packaging that is not necessary
-
Exceed materials
These ideas can help manufacturers improve efficiency and reduce costs.
What are the requirements to start a logistics business?
You need to have a lot of knowledge and skills to manage a successful logistic business. Effective communication skills are necessary to work with suppliers and clients. You will need to know how to interpret data and draw conclusions. You must be able manage stress and pressure under pressure. You must be creative and innovative to develop new ideas to improve efficiency. You will need strong leadership skills to motivate and direct your team members towards achieving their organizational goals.
You should also be organized and efficient to meet tight deadlines.
What is manufacturing and logistics?
Manufacturing is the act of producing goods from raw materials using machines and processes. Logistics covers all aspects involved in managing supply chains, including procurement and production planning. As a broad term, manufacturing and logistics often refer to both the creation and delivery of products.
Statistics
- Many factories witnessed a 30% increase in output due to the shift to electric motors. (en.wikipedia.org)
- It's estimated that 10.8% of the U.S. GDP in 2020 was contributed to manufacturing. (investopedia.com)
- (2:04) MTO is a production technique wherein products are customized according to customer specifications, and production only starts after an order is received. (oracle.com)
- According to a Statista study, U.S. businesses spent $1.63 trillion on logistics in 2019, moving goods from origin to end user through various supply chain network segments. (netsuite.com)
- [54][55] These are the top 50 countries by the total value of manufacturing output in US dollars for its noted year according to World Bank.[56] (en.wikipedia.org)
External Links
How To
How to use the Just-In Time Method in Production
Just-intime (JIT), which is a method to minimize costs and maximize efficiency in business process, is one way. It's a way to ensure that you get the right resources at just the right time. This means that you only pay the amount you actually use. Frederick Taylor developed the concept while working as foreman in early 1900s. He noticed that workers were often paid overtime when they had to work late. He concluded that if workers were given enough time before they start work, productivity would increase.
JIT is a way to plan ahead and make sure you don't waste any money. It is important to look at your entire project from beginning to end and ensure that you have enough resources to handle any issues that may arise. If you anticipate that there might be problems, you'll have enough people and equipment to fix them. This way, you won't end up paying extra money for things that weren't really necessary.
There are several types of JIT techniques:
-
Demand-driven: This JIT is where you place regular orders for the parts/materials that are needed for your project. This will allow you to track how much material you have left over after using it. You'll also be able to estimate how long it will take to produce more.
-
Inventory-based: This is a type where you stock the materials required for your projects in advance. This allows one to predict how much they will sell.
-
Project-driven: This approach involves setting aside sufficient funds to cover your project's costs. Knowing how much money you have available will help you purchase the correct amount of materials.
-
Resource-based: This is the most common form of JIT. This is where you assign resources based upon demand. If you have many orders, you will assign more people to manage them. If you don't have many orders, you'll assign fewer people to handle the workload.
-
Cost-based: This is a similar approach to resource-based but you are not only concerned with how many people you have, but also how much each one costs.
-
Price-based: This is very similar to cost-based, except that instead of looking at how much each individual worker costs, you look at the overall price of the company.
-
Material-based is an alternative to cost-based. Instead of looking at the total cost in the company, this method focuses on the average amount of raw materials that you consume.
-
Time-based: Another variation of resource-based JIT. Instead of focusing on the cost of each employee, you will focus on the time it takes to complete a project.
-
Quality-based JIT: This is another variation of resource based JIT. Instead of worrying about the costs of each employee or how long it takes for something to be made, you should think about how quality your product is.
-
Value-based JIT: This is the latest form of JIT. This is where you don't care about how the products perform or whether they meet customers' expectations. Instead, you are focused on adding value to the marketplace.
-
Stock-based: This is an inventory-based method that focuses on the actual number of items being produced at any given time. It is used when production goals are met while inventory is kept to a minimum.
-
Just-intime planning (JIT), is a combination JIT/sales chain management. This refers to the scheduling of the delivery of components as soon after they are ordered. This is important as it reduces lead time and increases throughput.