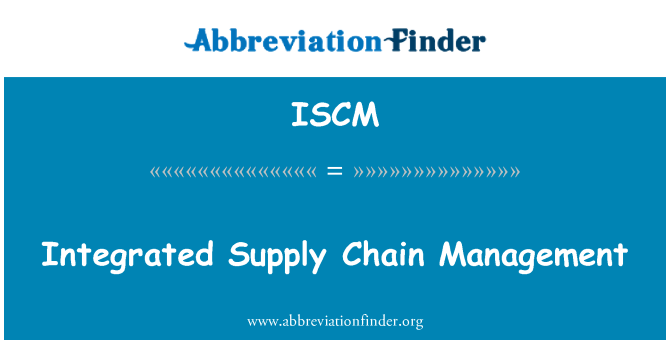
A manufacturing contraction is an economic downturn which affects industrial production. It can be triggered in a number ways, including by low confidence when it comes to investments, oil prices, federal policy, or even housing bubbles. Typically, manufacturers are more affected than the rest of the economy. However, when a manufacturing recession ends, the industry often recovers faster than the overall economy.
A recession is defined as a period of economic contraction that lasts for at least two quarters. A recession is defined by economic data and employment statistics.
Recessions are common components of the global economy, and manufacturers have to adjust to remain successful.
There are several ways to deal with a manufacturing downturn. A common strategy is to focus on reducing unprofitable areas, optimizing operations and investing in areas that can continue to grow or stabilize during the downturn.
It has been a tradition for manufacturers to increase their productivity by improving their use of equipment and talent during recessions. These improvements resulted despite flat capacity utilization in a recession in significant gains of output and productivity.
According to a recent report from the Institute of Supply Management, the US manufacturing industry is in recession and has likely entered a mid-cycle slowdown. This is a bad sign for the economy and President Donald Trump's chances of re-election in 2020.
Manufacturing is an industry that is vulnerable to the recession
Recessions can affect any industry, but manufacturing has a higher risk of a recession due to the export-oriented nature of its business model. Manufacturing in the US has been slowed by the trade war between China and the United States, but global trade imbalances are also a factor.
US manufacturers are being forced to reduce their sales and cut jobs due to the trade wars. They struggle with high imports, a slowing of global demand and high costs for raw materials. In August, US manufacturers added only 3,000 new jobs. This is the lowest increase since September 2009.
The reason workers are reluctant to quit their manufacturing jobs is that they do not receive enough money to support them and their families in this recession. The phenomenon of labor hoarding has prevented widespread layoffs in manufacturing.
A slowdown of the manufacturing sector is bound to have an effect on other industries. To grow and expand the economic system, the services sector relies on an increasing pool of workers who have purchasing power. When the services industry slows, consumers will start to reduce spending. Manufacturing is then affected.
During a recession, the manufacturing industry may experience difficulty attracting and retaining employees because of low wage rates and strained supply chains. NAM advocates for immigration reforms as well other solutions that will improve the manufacturing sector's ability to compete.
As a consequence, it is crucial that manufacturers invest strategically in their businesses to improve technology and innovation during the downturn, to set them up for growth and long-term success. Manufacturers must also build up a strong cash reserve in order to cover future operations and avoid a liquidity crisis during retrenchment.
FAQ
What are the responsibilities of a manufacturing manager
A manufacturing manager must ensure that all manufacturing processes are efficient and effective. They should also be aware and responsive to any company problems.
They should also know how to communicate with other departments such as sales and marketing.
They should also be knowledgeable about the latest trends in the industry so they can use this information for productivity and efficiency improvements.
How can I learn about manufacturing?
Experience is the best way for you to learn about manufacturing. However, if that's not possible, you can always read books or watch educational videos.
What skills do production planners need?
You must be flexible and organized to become a productive production planner. It is also important to be able communicate with colleagues and clients.
What is the responsibility of a logistics manager?
Logistics managers are responsible for ensuring that all goods arrive in perfect condition and on time. This is done using his/her knowledge of the company's products. He/she should ensure that sufficient stock is available in order to meet customer demand.
Statistics
- In the United States, for example, manufacturing makes up 15% of the economic output. (twi-global.com)
- [54][55] These are the top 50 countries by the total value of manufacturing output in US dollars for its noted year according to World Bank.[56] (en.wikipedia.org)
- According to a Statista study, U.S. businesses spent $1.63 trillion on logistics in 2019, moving goods from origin to end user through various supply chain network segments. (netsuite.com)
- In 2021, an estimated 12.1 million Americans work in the manufacturing sector.6 (investopedia.com)
- Many factories witnessed a 30% increase in output due to the shift to electric motors. (en.wikipedia.org)
External Links
How To
How to Use the Just-In-Time Method in Production
Just-intime (JIT), which is a method to minimize costs and maximize efficiency in business process, is one way. It's a way to ensure that you get the right resources at just the right time. This means you only pay what you use. Frederick Taylor was the first to coin this term. He developed it while working as a foreman during the early 1900s. Taylor observed that overtime was paid to workers if they were late in working. He realized that workers should have enough time to complete their jobs before they begin work. This would help increase productivity.
JIT is an acronym that means you need to plan ahead so you don’t waste your money. Also, you should look at the whole project from start-to-finish and make sure you have the resources necessary to address any issues. You can anticipate problems and have enough equipment and people available to fix them. This will ensure that you don't spend more money on things that aren't necessary.
There are many JIT methods.
-
Demand-driven: This is a type of JIT where you order the parts/materials needed for your project regularly. This will allow to track how much material has been used up. You'll also be able to estimate how long it will take to produce more.
-
Inventory-based: This is a type where you stock the materials required for your projects in advance. This allows you to forecast how much you will sell.
-
Project-driven: This is an approach where you set aside enough funds to cover the cost of your project. If you know the amount you require, you can buy the materials you need.
-
Resource-based JIT is the most widespread form. This is where you assign resources based upon demand. For example, if there is a lot of work coming in, you will have more people assigned to them. You'll have fewer orders if you have fewer.
-
Cost-based: This approach is very similar to resource-based. However, you don't just care about the number of people you have; you also need to consider how much each person will cost.
-
Price-based: This approach is very similar to the cost-based method except that you don't look at individual workers costs but the total cost of the company.
-
Material-based: This is very similar to cost-based but instead of looking at total costs of the company you are concerned with how many raw materials you use on an average.
-
Time-based: This is another variation of resource-based JIT. Instead of focusing solely on the amount each employee costs, focus on how long it takes for the project to be completed.
-
Quality-based JIT: Another variation on resource-based JIT. Instead of focusing on the cost of each worker or how long it takes, think about how high quality your product is.
-
Value-based JIT is the newest form of JIT. This is where you don't care about how the products perform or whether they meet customers' expectations. Instead, your goal is to add value to the market.
-
Stock-based is an inventory-based system that measures the number of items produced at any given moment. It is used when production goals are met while inventory is kept to a minimum.
-
Just-in-time planning (JIT): This is a combination JIT and supply-chain management. This refers to the scheduling of the delivery of components as soon after they are ordered. This is important as it reduces lead time and increases throughput.