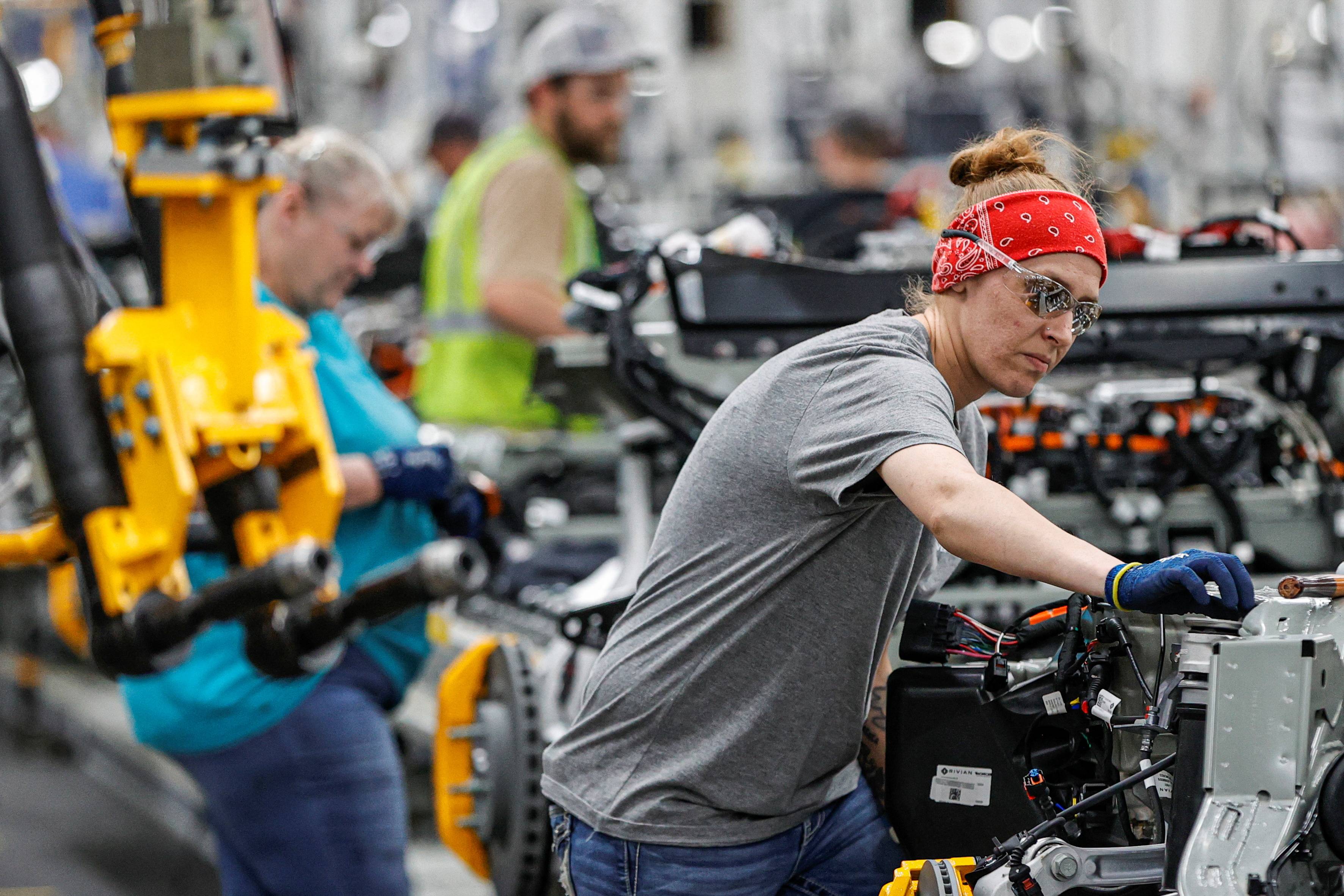
OSHA compliance is just as important as experience for food producers. Here are three things to consider when choosing a company to automate your production process:
Experience is important for food manufacturers
A position as a food manufacturer often requires high levels of industry experience. However, there are also opportunities for those with little or no experience. Many food companies prefer to hire from their own ranks. It is important to have a high school diploma, but it is not required. As assistants to more skilled workers, entry-level employees begin as such. They then learn the job. Some entry-level tasks are easy and can be completed in as little as a couple of days. Some of the most common entry-level tasks include operating bread slicers. Experience is vital in every area of food manufacturing.
Conformance to OSHA regulations
OSHA regulations for food producers are enforced by an inspection. This can be triggered either by an incident, complaint or "programmed inspection". An OSHA enforcement visit at a yogurt manufacturing facility, for example, followed a complaint and was preceded by a planned inspection. Many cases result in multiple violations of process safety management standards, including those on guarding machinery and stairs and platforms, emergency escape, forklift operation, hearing protection and standard on hazard communication.
Develop a plan for food safety
Although most businesses must comply with federal regulations, certain businesses may be exempted from these requirements. Although it is impossible, there are methods to prevent and manage possible hazards in food manufacturing. Food safety is not only a concern for consumers' health but also can have negative consequences for businesses. Recalls may affect supply chain operations as well. These recalls can happen for many reasons, including adulteration or misbranding and violative products. In addition to the health risks, food recalls can be an expensive exercise for a food manufacturer.
Automation Costs
Food manufacturers are facing increasing costs of automation. Some regions have to import ingredients in order to compete with local producers. The suppliers also have a decreasing profit margin as they pass on the cost to consumers. But automation can help to reduce costs and increase efficiency in production. In this article, we'll discuss how automation can help improve the overall efficiency for food manufacturers. Access to our industry expertise is also possible.
Competition with major food companies: Challenges
To protect their market dominance, to prevent competition and to increase their profits, the top food companies use three main strategies. These strategies include the acquisition and development of valuable intangible asset, enforcement of production and marketing efficiencies, control over the supply chain, and monitoring and controlling costs. These strategies create barriers for entry. Here are some of the most important challenges faced by emerging food and beverage companies. Let's discuss each strategy in more detail.
FAQ
How can we improve manufacturing efficiency?
First, determine which factors have the greatest impact on production time. The next step is to identify the most important factors that affect production time. If you don’t know how to start, look at which factors have the greatest impact upon production time. Once you have identified them, it is time to identify solutions.
What are the 7 R's of logistics?
The 7R's of Logistics is an acronym for the seven basic principles of logistics management. It was developed by International Association of Business Logisticians (IABL), and published as part of their "Seven Principles of Logistics Management Series" in 2004.
The following letters form the acronym:
-
Responsible - ensure that all actions taken are within legal requirements and are not harmful to others.
-
Reliable: Have faith in your ability or the ability to honor any promises made.
-
Be responsible - Use resources efficiently and avoid wasting them.
-
Realistic – Consider all aspects, including cost-effectiveness as well as environmental impact.
-
Respectful - Treat people fairly and equitably
-
Reliable - Find ways to save money and increase your productivity.
-
Recognizable - provide customers with value-added services.
Do we need to know about Manufacturing Processes before learning about Logistics?
No. It doesn't matter if you don't know anything about manufacturing before you learn about logistics. Knowing about manufacturing processes will help you understand how logistics works.
What is the responsibility of a production planner?
A production planner makes sure all project elements are delivered on schedule, within budget, as well as within the agreed scope. They make sure that the product and services meet client expectations.
What makes a production planner different from a project manger?
The difference between a product planner and project manager is that a planer is typically the one who organizes and plans the entire project. A production planner, however, is mostly involved in the planning stages.
Statistics
- (2:04) MTO is a production technique wherein products are customized according to customer specifications, and production only starts after an order is received. (oracle.com)
- Job #1 is delivering the ordered product according to specifications: color, size, brand, and quantity. (netsuite.com)
- According to a Statista study, U.S. businesses spent $1.63 trillion on logistics in 2019, moving goods from origin to end user through various supply chain network segments. (netsuite.com)
- You can multiply the result by 100 to get the total percent of monthly overhead. (investopedia.com)
- Many factories witnessed a 30% increase in output due to the shift to electric motors. (en.wikipedia.org)
External Links
How To
How to Use Lean Manufacturing in the Production of Goods
Lean manufacturing (or lean manufacturing) is a style of management that aims to increase efficiency, reduce waste and improve performance through continuous improvement. It was first developed in Japan in the 1970s/80s by Taiichi Ahno, who was awarded the Toyota Production System (TPS), award from KanjiToyoda, the founder of TPS. The first book published on lean manufacturing was titled "The Machine That Changed the World" written by Michael L. Watkins and published in 1990.
Lean manufacturing is often described as a set if principles that help improve the quality and speed of products and services. It emphasizes reducing defects and eliminating waste throughout the value chain. Just-in-time (JIT), zero defect (TPM), and 5S are all examples of lean manufacturing. Lean manufacturing eliminates non-value-added tasks like inspection, rework, waiting.
Lean manufacturing not only improves product quality but also reduces costs. Companies can also achieve their goals faster by reducing employee turnover. Lean manufacturing can be used to manage all aspects of the value chain. Customers, suppliers, distributors, retailers and employees are all included. Lean manufacturing is widely practiced in many industries around the world. Toyota's philosophy has been a key driver of success in many industries, including automobiles and electronics.
Five principles are the basis of lean manufacturing:
-
Define value - Find out what your business contributes to society, and what makes it different from other competitors.
-
Reduce waste - Get rid of any activity that does not add value to the supply chain.
-
Create Flow. Ensure that your work is uninterrupted and flows seamlessly.
-
Standardize and simplify - Make your processes as consistent as possible.
-
Develop Relationships: Establish personal relationships both with internal and external stakeholders.
Lean manufacturing isn’t new, but it has seen a renewed interest since 2008 due to the global financial crisis. Many businesses have adopted lean production techniques to make them more competitive. Some economists even believe that lean manufacturing can be a key factor in economic recovery.
With many benefits, lean manufacturing is becoming more common in the automotive industry. These include higher customer satisfaction levels, reduced inventory levels as well as lower operating costs.
You can apply Lean Manufacturing to virtually any aspect of your organization. However, it is particularly useful when applied to the production side of an organization because it ensures that all steps in the value chain are efficient and effective.
There are three main types of lean manufacturing:
-
Just-in Time Manufacturing (JIT), also known as "pull system": This form of lean manufacturing is often referred to simply as "pull". JIT is a method in which components are assembled right at the moment of use, rather than being manufactured ahead of time. This method reduces lead times, increases availability, and decreases inventory.
-
Zero Defects Manufacturing: ZDM ensures that no defective units leave the manufacturing plant. If a part needs to be fixed during the assembly line, it should be repaired rather than scrapped. This is true even for finished products that only require minor repairs prior to shipping.
-
Continuous Improvement (CI: Continuous improvement aims to increase the efficiency of operations by constantly identifying and making improvements to reduce or eliminate waste. Continuous Improvement involves continuous improvement of processes.