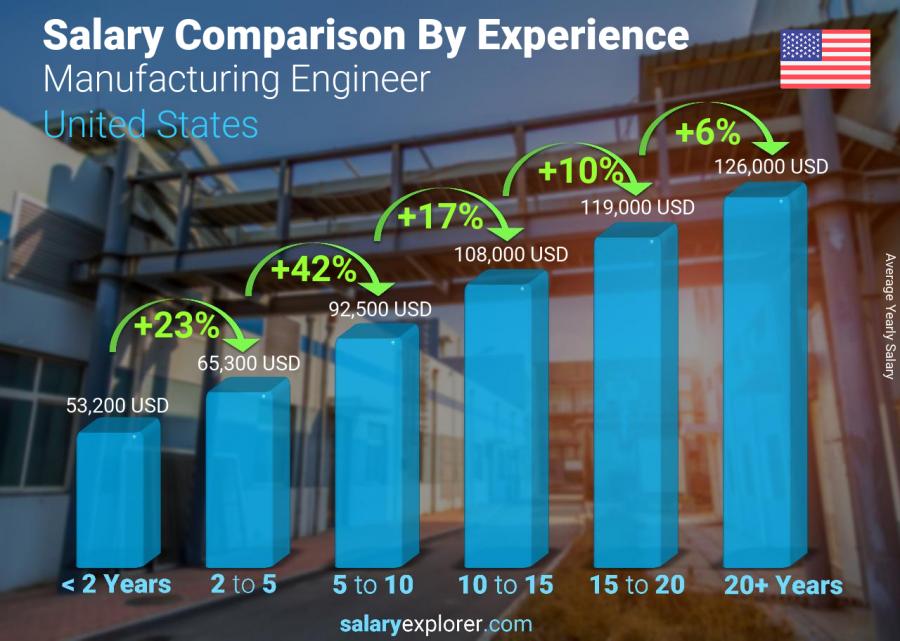
A director of manufacturing is responsible for managing the production process for a company. They are responsible for overseeing all aspects of manufacturing, from design through to production. This role requires a lot of experience in manufacturing, as well as a good knowledge of new technologies. These technologies include 3D printing and robotics. The director who is up-to-date with these technologies will be a valuable asset to the company. The director's role in the manufacturing industry will change as it evolves. He or she will need to work closely with engineering and operations, as well as placing greater emphasis on quality control in the manufacturing plant.
Director of manufacturing salary
A Director of Manufacturing's salary can vary greatly, depending on the region they work in. Many directors earn in the six-figures range. Some directors make significantly more than others. Based on years of education and experience, the salary of a Director in Manufacturing can also vary. There are a few things that can influence the amount you earn in your region.
The salary for a director of manufacturing varies but it's generally higher if you have more work experience. Pay can be affected by your location and cost of living. While you may earn more if your location is a major city, it's possible to make a living in that area. It is important that you are always willing to negotiate a higher salary when the opportunity arises.
A Director of Manufacturing Operations makes between $181,500 and $66,000 a year. Director of Manufacturing Operations salaries can vary widely and can differ up to 8 percent between cities. Fremont's director manufacturing operations can expect to earn $128.493 to $164.500. This makes Fremont, CA a significantly better place than the national average. The salary of a Director in Manufacturing Operations can vary depending on where you live, how experienced you are, and what company you work for.
Education is required
Director of manufacturing is responsible to manage a manufacturing facility and supervise the production process. This job includes managing new employees, quality assurance, working with designers and meeting production standards. A director of manufacturing typically reports to the senior management team and executes policy and sales initiatives. Candidates must have some manufacturing experience and be able communicate well. Companies have different requirements when it comes to education.
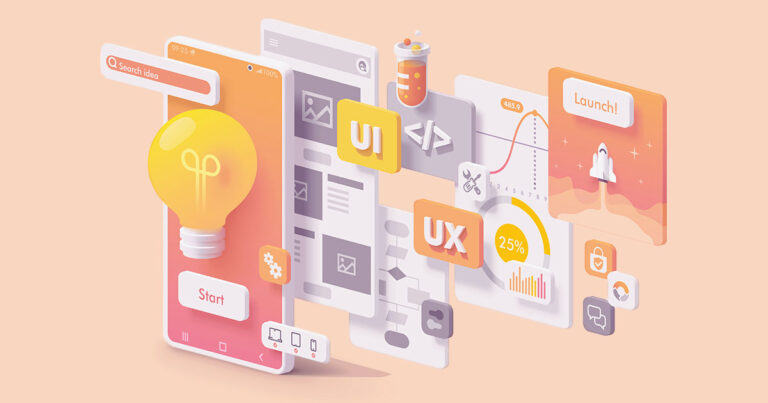
Although a master's degree in engineering does not necessarily make you a director in manufacturing, having a post-secondary education is a great way to increase your knowledge and skill set. An MBA program in industrial management or business administration is a great choice for this position, as it helps candidates to learn about management, economics, and organization. You will eventually have to manage a diverse workforce.
As a director in manufacturing you will work closely alongside engineers and designers during the product design phase. You will play a key role in this stage by evaluating new processes and making sure quality standards are met before you commit resources to larger productions. Successful directors also play a role as coaches and mentors for employees. They will guide them in risk mitigation and best practice. In addition to overseeing the entire production process, a manufacturing director must be able to develop strong problem-solving skills.
Experience required
This position often requires a bachelor's degree in a relevant area and five to ten years of progressive work experience. Manufacturing companies will prefer to employ internal workers for this position. A candidate who is a good fit for this role will have an in-depth understanding of manufacturing processes and business goals. Employers may require a graduate degree. Additional training may be required for candidates in their chosen field.
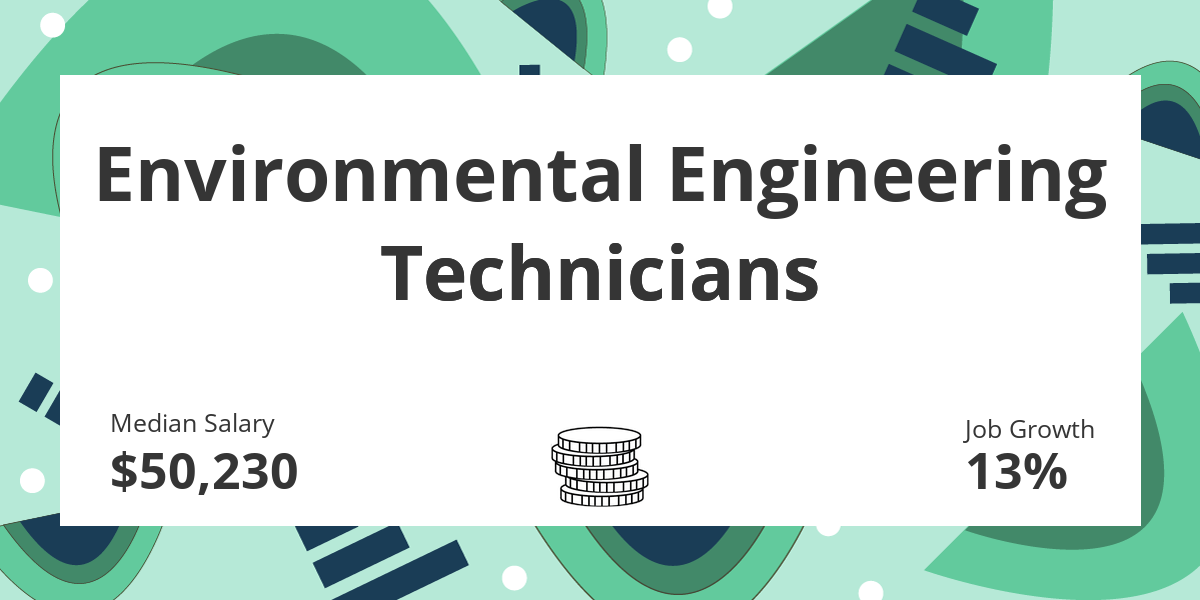
The production process is overseen by a director of manufacturing, which includes engineers, supervisors, workers, and other personnel. They may be responsible in solving problems and creating solutions. They could also be responsible, in addition to supervising production, for creating and implementing quality-control programmes. A director of manufacturing reports directly to the top executive of the manufacturing organization. Manufacturing experience is a must. If you are looking to succeed in the manufacturing management position, it is important that you have some experience.
Experience as a manufacturing director is essential. Directors should have at least 10 years' experience in a manufacturing setting. Some of these people may have started as manufacturing supervisors or technicians. They must also be able to communicate well. A director of manufacturing should also have a thorough understanding of business strategy. Finally, a director of manufacturing must be able to work effectively with other departments within the organization. The director of manufacturing oversees production and ensures it meets high quality standards.
FAQ
What does manufacturing industry mean?
Manufacturing Industries are those businesses that make products for sale. Consumers are those who purchase these products. These companies use various processes such as production, distribution, retailing, management, etc., to fulfill this purpose. These companies produce goods using raw materials and other equipment. This covers all types of manufactured goods including clothing, food, building supplies and furniture, as well as electronics, tools, machinery, vehicles and pharmaceuticals.
What does warehouse refer to?
A warehouse, or storage facility, is where goods are stored prior to being sold. It can be indoors or out. Sometimes, it can be both an indoor and outdoor space.
How can excess manufacturing production be reduced?
Better inventory management is key to reducing excess production. This would decrease the time that is spent on inefficient activities like purchasing, storing, or maintaining excess stock. This could help us free up our time for other productive tasks.
You can do this by adopting a Kanban method. A Kanban board can be used to monitor work progress. Work items are moved through various states to reach their destination in a Kanban system. Each state has a different priority level.
As an example, if work is progressing from one stage of the process to another, then the current task is complete and can be transferred to the next. But if a task remains in the beginning stages it will stay that way until it reaches its end.
This allows work to move forward and ensures that no work is missed. With a Kanban board, managers can see exactly how much work is being done at any given moment. This information allows managers to adjust their workflow based off real-time data.
Lean manufacturing can also be used to reduce inventory levels. Lean manufacturing emphasizes eliminating waste in all phases of production. Waste includes anything that does not add value to the product. There are several types of waste that you might encounter:
-
Overproduction
-
Inventory
-
Unnecessary packaging
-
Excess materials
These ideas will help manufacturers increase efficiency and lower costs.
Statistics
- Job #1 is delivering the ordered product according to specifications: color, size, brand, and quantity. (netsuite.com)
- You can multiply the result by 100 to get the total percent of monthly overhead. (investopedia.com)
- According to the United Nations Industrial Development Organization (UNIDO), China is the top manufacturer worldwide by 2019 output, producing 28.7% of the total global manufacturing output, followed by the United States, Japan, Germany, and India.[52][53] (en.wikipedia.org)
- [54][55] These are the top 50 countries by the total value of manufacturing output in US dollars for its noted year according to World Bank.[56] (en.wikipedia.org)
- In 2021, an estimated 12.1 million Americans work in the manufacturing sector.6 (investopedia.com)
External Links
How To
How to Use Lean Manufacturing in the Production of Goods
Lean manufacturing is a management style that aims to increase efficiency and reduce waste through continuous improvement. It was first developed in Japan in the 1970s/80s by Taiichi Ahno, who was awarded the Toyota Production System (TPS), award from KanjiToyoda, the founder of TPS. Michael L. Watkins published the original book on lean manufacturing, "The Machine That Changed the World," in 1990.
Lean manufacturing refers to a set of principles that improve the quality, speed and costs of products and services. It emphasizes the elimination of defects and waste throughout the value stream. Just-in-time (JIT), zero defect (TPM), and 5S are all examples of lean manufacturing. Lean manufacturing seeks to eliminate non-value added activities, such as inspection, work, waiting, and rework.
In addition to improving product quality and reducing costs, lean manufacturing helps companies achieve their goals faster and reduces employee turnover. Lean manufacturing can be used to manage all aspects of the value chain. Customers, suppliers, distributors, retailers and employees are all included. Lean manufacturing is widely practiced in many industries around the world. Toyota's philosophy is a great example of this. It has helped to create success in automobiles as well electronics, appliances and healthcare.
Five principles are the basis of lean manufacturing:
-
Define Value - Determine the value that your business brings to society. Also, identify what sets you apart from your competitors.
-
Reduce Waste – Eliminate all activities that don't add value throughout the supply chain.
-
Create Flow - Make sure work runs smoothly without interruptions.
-
Standardize & Simplify - Make processes as consistent and repeatable as possible.
-
Build Relationships - Establish personal relationships with both internal and external stakeholders.
Lean manufacturing, although not new, has seen renewed interest in the economic sector since 2008. To increase their competitiveness, many businesses have turned to lean manufacturing. Many economists believe lean manufacturing will play a major role in economic recovery.
With many benefits, lean manufacturing is becoming more common in the automotive industry. These benefits include increased customer satisfaction, reduced inventory levels and lower operating costs.
Lean manufacturing can be applied to almost every aspect of an organization. Because it makes sure that all value chains are efficient and effectively managed, Lean Manufacturing is particularly helpful for organizations.
There are three types of lean manufacturing.
-
Just-in Time Manufacturing, (JIT): This kind of lean manufacturing is also commonly known as "pull-systems." JIT is a process in which components can be assembled at the point they are needed, instead of being made ahead of time. This approach reduces lead time, increases availability and reduces inventory.
-
Zero Defects Manufacturing: ZDM ensures that no defective units leave the manufacturing plant. If a part is required to be repaired on the assembly line, it should not be scrapped. This applies to finished goods that may require minor repairs before shipment.
-
Continuous Improvement (CI): CI aims to improve the efficiency of operations by continuously identifying problems and making changes in order to eliminate or minimize waste. Continuous improvement involves continuous improvement of processes and people as well as tools.