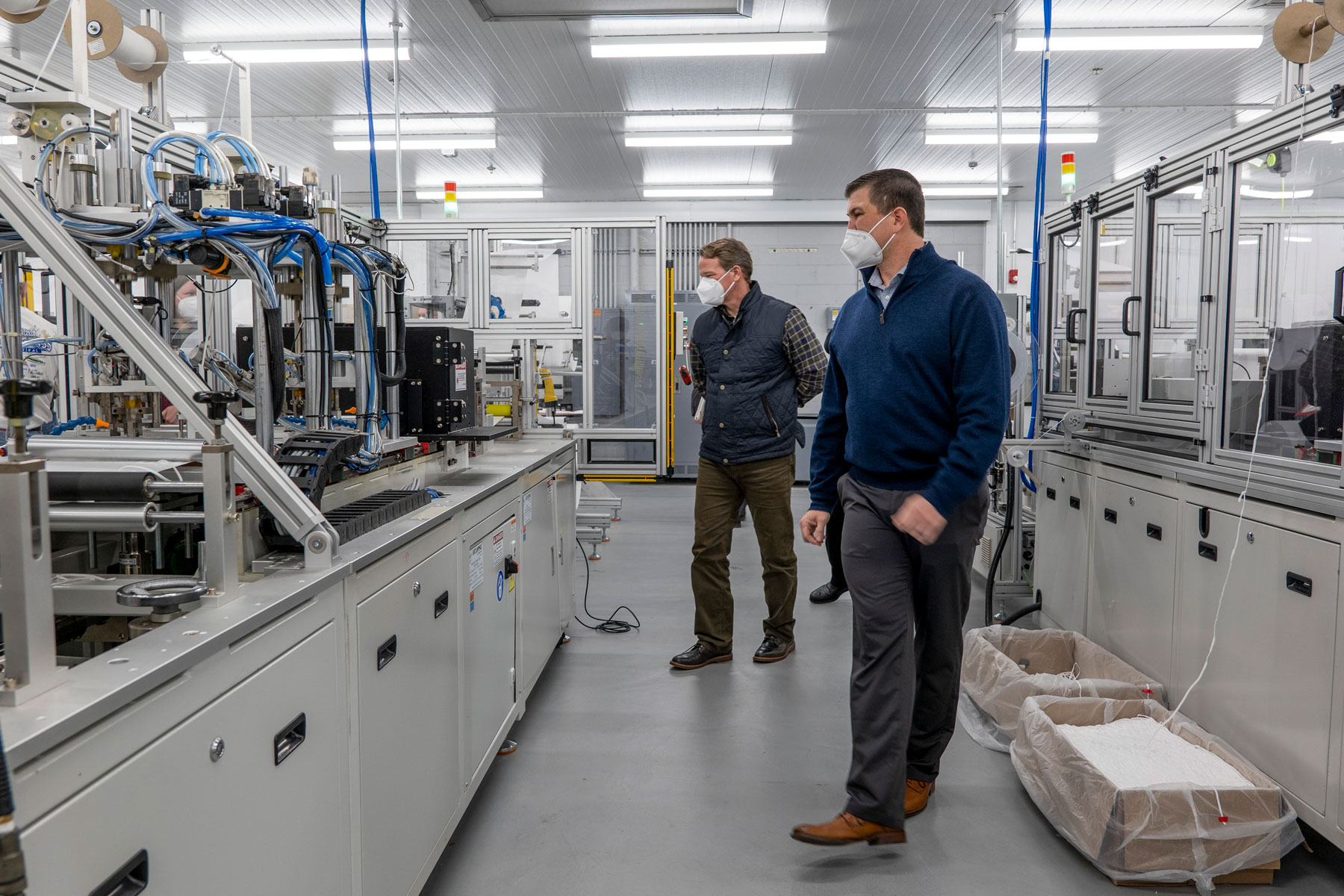
You will need to have the right education and training to be a manufacturing engineer. Some graduates may choose to pursue a master's program in order to acquire the necessary business, process, and product knowledge. A majority of manufacturing engineers complete their degree programs. They have hands-on experience in standard and experimental testing, measurement, and experimentation. To be allowed to do business, they must have a license. This shows employers that the candidate is qualified.
Skills required to be a manufacturing engineer
Manufacturing engineers can progress from an entry level position to a management position depending on the position. Their job description will contain the skills that they will need to succeed. They must be proficient in math and critical thinking. They should also have excellent communication skills to work with different levels of an organization. These are just some of the many skills a manufacturing engineer must have to succeed in their job.
Manufacturing engineers' main tasks will include the development, maintenance, modification, and support of various systems and processes. They will also be responsible to assess the environmental impact on manufacturing processes. They should be analytical thinkers and designers who have a deep understanding of manufacturing processes. A manufacturing engineer must keep current with current trends and regulations, as well as stay on top of industry news. A manufacturing engineer must be able work well with other engineers.
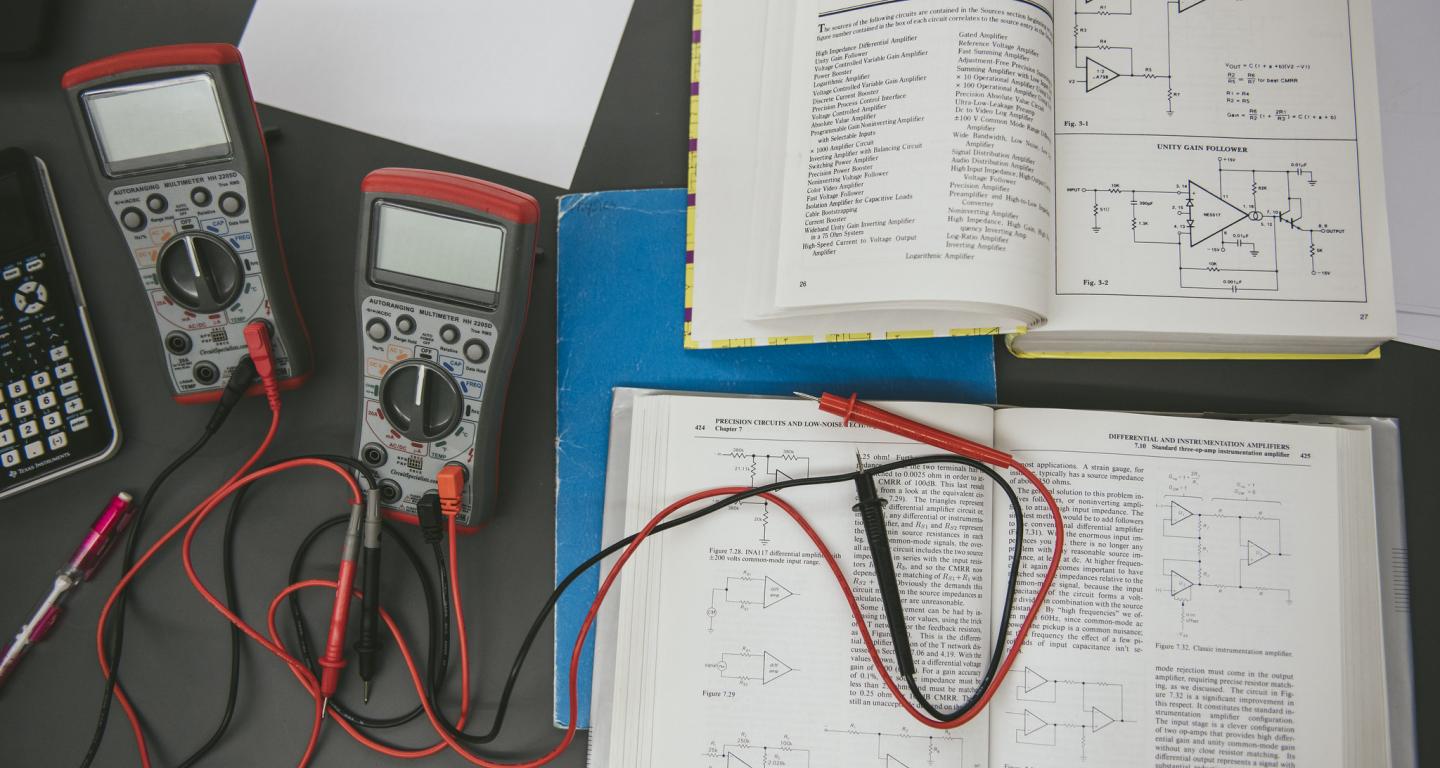
Responsibilities as a Manufacturing Engineer
Manufacturing engineers have many responsibilities, including the development of processes and the determination of production costs. In addition to designing and developing production processes, they also perform mathematical calculations, troubleshoot problems, and evaluate manufacturing processes and materials. Although they are often based in offices, some may need to travel to other locations such as the factory floor. Sometimes, manufacturing engineers are required to direct or supervise technicians and production staff. These employees are responsible for the smooth running of a production line.
The main responsibility of a manufacturing engineer is to design and implement manufacturing processes, as well as to monitor their efficiency. Manufacturing engineers also analyze production processes, design equipment and processes, and create quality control systems to ensure products are of the highest quality. Manufacturing engineers are responsible for the design and development of manufacturing processes. They also adhere to safety and quality regulations. Manufacturing engineers also have other responsibilities beyond the work place. They are required to conduct research, prepare reports, and document.
For manufacturing engineers, the future looks bright
Manufacturing engineers have an excellent career outlook. Although they grow slower than other occupations in the economy, there is still a lot of job growth. The manufacturing sector's growth will lead to more manufacturing engineers. Manufacturing companies must be able to plan, manage logistics and develop new production methods. Despite slow growth there is a high demand for mechanical engineering. Most job seekers will start in the school system.
The number of manufacturing engineers in the U.S. is expected to increase by 9% through 2026, according to the Bureau of Labor Statistics. This profession requires teamwork and a challenging environment. Career satisfaction is high for manufacturing engineers, and they typically remain in the field for a long time. Manufacturing engineers can work in factories that create cars and trucks. Manufacturing engineers may also be employed in consulting services, research and development firms, or wholesale trade. Industrial engineers may leave engineering to go into management.
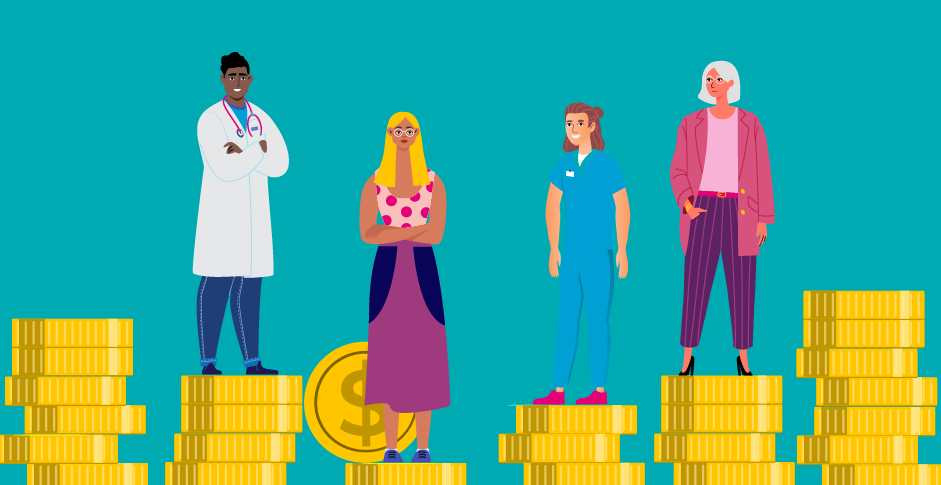
For manufacturing engineers, education requirements
For most jobs as a manufacturing engineer, a bachelor's degree in engineering (BSE), is required. Students will be able to learn about general science, math and engineering concepts. They can also use computer-aided design software (CAD). They can also expect to develop strong communication skills and a solid foundation in mathematics. Additional courses that may be required include courses in ethics and the humanities. There are many education requirements for manufacturing engineering engineers, but they can be varied, but BSEs are generally well-rounded.
A career in manufacturing engineering requires strong mathematics and science educations, as well analytical and problem solving skills. In addition to creativity, they must have strong team-working and creative skills. Manufacturing engineers often work full-time after graduating. They are required to travel to observe and learn about manufacturing operations at different locations as part of their job. Manufacturing engineers must be able to work hard and eager to learn the latest trends in manufacturing.
FAQ
What skills are required to be a production manager?
Production planners must be flexible, organized, and able handle multiple tasks. Also, you must be able and willing to communicate with clients and coworkers.
What does manufacturing industry mean?
Manufacturing Industries refers to businesses that manufacture products. Consumers are people who purchase these goods. To accomplish this goal, these companies employ a range of processes including distribution, sales, management, and production. They make goods from raw materials with machines and other equipment. This includes all types manufactured goods such as clothing, building materials, furniture, electronics, tools and machinery.
What are the products and services of logistics?
Logistics refers to all activities that involve moving goods from A to B.
They encompass all aspects transport, including packaging and loading, transporting, storage, unloading.
Logisticians ensure that products reach the right destination at the right moment and under safe conditions. They help companies manage their supply chain efficiency by providing information on demand forecasts, stock levels, production schedules, and availability of raw materials.
They keep track and monitor the transit of shipments, maintain quality standards, order replenishment and inventories, coordinate with suppliers, vendors, and provide support for sales and marketing.
Why automate your warehouse?
Modern warehousing is becoming more automated. With the rise of ecommerce, there is a greater demand for faster delivery times as well as more efficient processes.
Warehouses should be able adapt quickly to new needs. In order to do this, they need to invest in technology. Automation of warehouses offers many benefits. Here are some reasons why it's worth investing in automation:
-
Increases throughput/productivity
-
Reduces errors
-
Accuracy is improved
-
Safety is boosted
-
Eliminates bottlenecks
-
Allows companies to scale more easily
-
This makes workers more productive
-
Provides visibility into everything that happens in the warehouse
-
Enhances customer experience
-
Improves employee satisfaction
-
Reducing downtime and increasing uptime
-
High quality products delivered on-time
-
Eliminates human error
-
It ensures compliance with regulations
Statistics
- According to a Statista study, U.S. businesses spent $1.63 trillion on logistics in 2019, moving goods from origin to end user through various supply chain network segments. (netsuite.com)
- (2:04) MTO is a production technique wherein products are customized according to customer specifications, and production only starts after an order is received. (oracle.com)
- Many factories witnessed a 30% increase in output due to the shift to electric motors. (en.wikipedia.org)
- In 2021, an estimated 12.1 million Americans work in the manufacturing sector.6 (investopedia.com)
- [54][55] These are the top 50 countries by the total value of manufacturing output in US dollars for its noted year according to World Bank.[56] (en.wikipedia.org)
External Links
How To
How to Use the 5S to Increase Productivity In Manufacturing
5S stands in for "Sort", the "Set In Order", "Standardize", or "Separate". The 5S methodology was developed at Toyota Motor Corporation in 1954. It improves the work environment and helps companies to achieve greater efficiency.
The basic idea behind this method is to standardize production processes, so they become repeatable, measurable, and predictable. This means that every day tasks such cleaning, sorting/storing, packing, and labeling can be performed. Workers can be more productive by knowing what to expect.
Implementing 5S involves five steps: Sort, Set in Order, Standardize Separate, Store, and Each step involves a different action which leads to increased efficiency. You can make it easy for people to find things later by sorting them. When you set items in an order, you put items together. Once you have separated your inventory into groups and organized them, you will store these groups in easily accessible containers. Make sure everything is correctly labeled when you label your containers.
This process requires employees to think critically about how they do their job. Employees should understand why they do the tasks they do, and then decide if there are better ways to accomplish them. In order to use the 5S system effectively, they must be able to learn new skills.
The 5S method increases efficiency and morale among employees. As they begin to see improvements, they feel motivated to continue working towards the goal of achieving higher levels of efficiency.