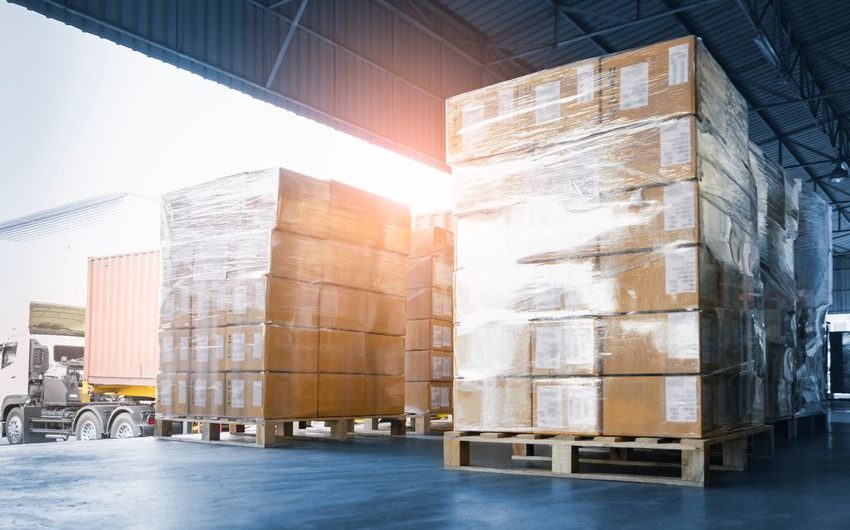
Civil engineers create infrastructure like roads, railways airports, dams, harbors, and bridges. They design and manage irrigation, water and sewerage system projects.
Obtaining a career as a civil engineer requires several skills and a commitment to education. Students who wish to enter this field need a bachelor's in civil engineering, or another related field such as business administration or construction. One-fifth or more of civil engineering professionals have a graduate degree. This increases the chances that you will get a position as a junior engineer. Senior engineers may need a license from ABET.
For entry-level roles, a bachelor's or master's degree is required in civil engineering. Most civil engineer degrees require four or five year to complete. Many schools offer programs that make it possible to earn a degree more affordable.
Graduates with civil engineering degrees can work in many roles, such a design engineer or project manager. They usually start in a graduate training scheme, where they work under an experienced professional to develop their skills. After gaining more experience, engineers can progress to full-time roles and eventually become lead engineers.
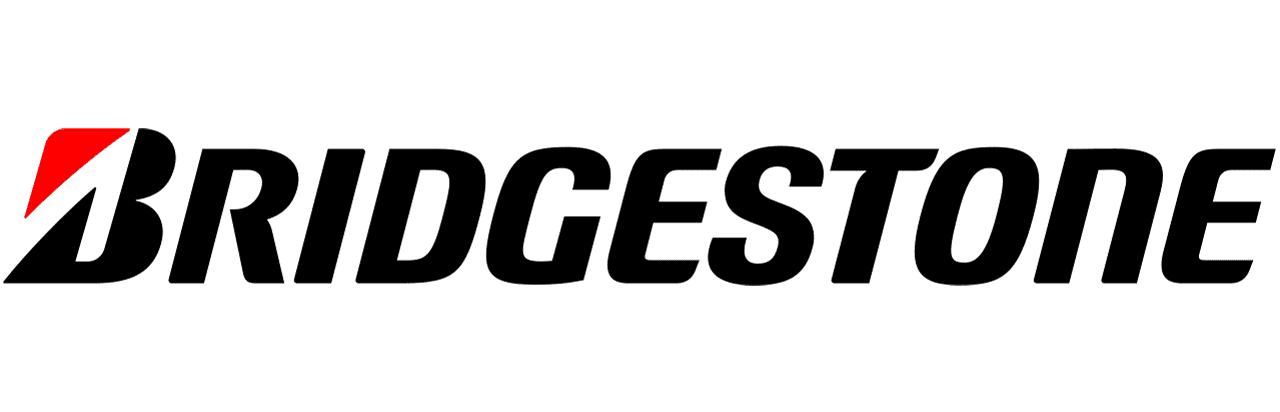
A career as a civil engineer can be exciting and challenging, with plenty of room for advancement. You can find civil engineering careers in many different industries such as manufacturing, transportation, energy and energy.
Employers seek candidates with strong communication, critical reasoning and creativity abilities. These skills help you solve technical problems and improve processes for your employer.
As you supervise the construction of many projects, leadership and teamwork are important. It's important to be able communicate effectively with both your team and the vendors so that you can quickly resolve issues.
Civil engineering is a profession that changes with the industry. It's important to stay up-to-date with new trends and regulations. For a career in civil engineering, it is important to stay current with trends and regulations. This profession evolves along with the needs of industry.
Also, decision-making is key to this job. Budgeting, safety and other concerns will be important to you.
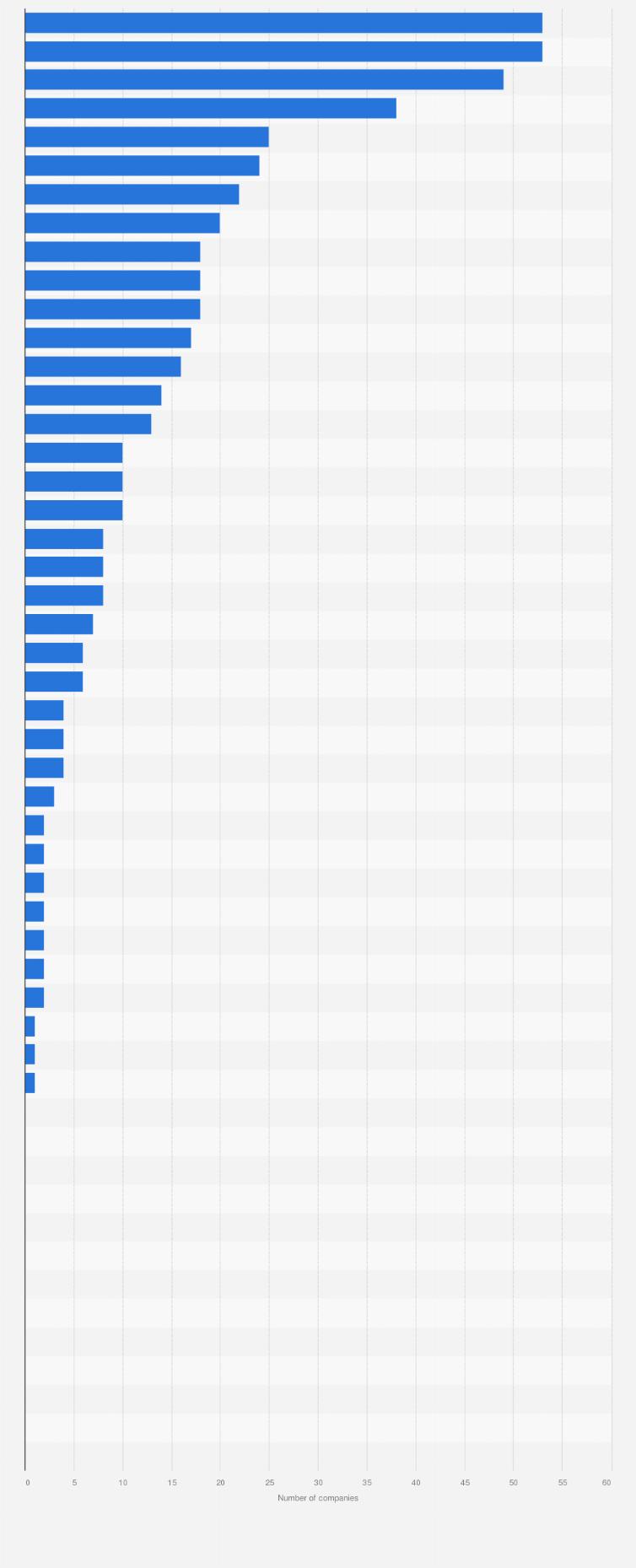
Your educational and training background will play a big role in your ability to succeed as a civil engineer, and you'll need to prove your worth on the job by completing projects and meeting deadlines. Communication with clients, contractors and coworkers is essential.
Also, you will need to be creative and innovative in order to succeed. You'll have to be able both to analyze and present data effectively.
Salary can be very different for a civil engineering depending on where you live and what type of job you have. California, Texas, and Florida offer the best salaries for this profession. Alaska, Rhode Island, and Wyoming are also states with high salaries for civil engineering.
FAQ
What is the responsibility for a logistics manager
Logistics managers make sure all goods are delivered on schedule and without damage. This is done by using his/her experience and knowledge of the company's products. He/she must also ensure sufficient stock to meet the demand.
What are manufacturing & logistics?
Manufacturing is the act of producing goods from raw materials using machines and processes. Logistics includes all aspects related to supply chain management, such as procurement, distribution planning, inventory control and transportation. Logistics and manufacturing are often referred to as one thing. It encompasses both the creation of products and their delivery to customers.
What is production management?
Production Planning includes planning for all aspects related to production. This document is designed to make sure everything is ready for when you're ready to shoot. You should also have information to ensure the best possible results on set. This includes location information, crew details, equipment specifications, and casting lists.
The first step is to outline what you want to film. You may have decided where to shoot or even specific locations you want to use. Once you have identified the scenes and locations, you can start to determine which elements are required for each scene. You might decide you need a car, but not sure what make or model. If this is the case, you might start searching online for car models and then narrow your options by selecting from different makes.
Once you have found the right vehicle, you can think about adding accessories. Are you looking for people to sit in the front seats? Or maybe you just need someone to push the car around. Perhaps you would like to change the interior colour from black to white. These questions will help you determine the exact look and feel of your car. Also, think about what kind of shots you would like to capture. What type of shots will you choose? Maybe the engine or steering wheel is what you are looking to film. All of these things will help you identify the exact style of car you want to film.
Once you have determined all of the above, you can move on to creating a schedule. A schedule will tell you when you need to start shooting and when you need to finish. A schedule for each day will detail when you should arrive at the location and when you need leave. This way, everyone knows what they need to do and when. If you need to hire extra staff, you can make sure you book them in advance. You should not hire anyone who doesn't show up because of your inaction.
You will need to factor in the days that you have to film when creating your schedule. Some projects only take one or two days, while others may last weeks. It is important to consider whether you require more than one photo per day when you create your schedule. Multiplying takes in the same area will result both in increased costs and a longer time. It's better to be safe than sorry and shoot less takes if you're not certain whether you need more takes.
Budget setting is another important aspect in production planning. It is important to set a realistic budget so you can work within your budget. Keep in mind that you can always reduce your budget if you face unexpected difficulties. It is important to not overestimate how much you will spend. Underestimating the cost will result in less money after you have paid for other items.
Planning production is a tedious process. Once you have a good understanding of how everything works together, planning future projects becomes easy.
How does a Production Planner differ from a Project Manager?
The major difference between a Production Planner and a Project Manager is that a Project Manager is often the person responsible for organizing and planning the entire project. While a Production Planner is involved mainly in the planning stage,
Statistics
- Many factories witnessed a 30% increase in output due to the shift to electric motors. (en.wikipedia.org)
- According to the United Nations Industrial Development Organization (UNIDO), China is the top manufacturer worldwide by 2019 output, producing 28.7% of the total global manufacturing output, followed by the United States, Japan, Germany, and India.[52][53] (en.wikipedia.org)
- You can multiply the result by 100 to get the total percent of monthly overhead. (investopedia.com)
- Job #1 is delivering the ordered product according to specifications: color, size, brand, and quantity. (netsuite.com)
- According to a Statista study, U.S. businesses spent $1.63 trillion on logistics in 2019, moving goods from origin to end user through various supply chain network segments. (netsuite.com)
External Links
How To
How to Use Lean Manufacturing in the Production of Goods
Lean manufacturing is a management style that aims to increase efficiency and reduce waste through continuous improvement. It was created in Japan by Taiichi Ohno during the 1970s and 80s. He received the Toyota Production System award (TPS), from Kanji Toyoda, founder of TPS. The first book published on lean manufacturing was titled "The Machine That Changed the World" written by Michael L. Watkins and published in 1990.
Lean manufacturing can be described as a set or principles that are used to improve quality, speed and cost of products or services. It emphasizes the elimination and minimization of waste in the value stream. Lean manufacturing can be described as just-in–time (JIT), total productive maintenance, zero defect (TPM), or even 5S. Lean manufacturing seeks to eliminate non-value added activities, such as inspection, work, waiting, and rework.
Lean manufacturing improves product quality and costs. It also helps companies reach their goals quicker and decreases employee turnover. Lean manufacturing is a great way to manage the entire value chain including customers, suppliers, distributors and retailers as well as employees. Lean manufacturing practices are widespread in many industries. Toyota's philosophy is the foundation of its success in automotives, electronics and appliances, healthcare, chemical engineers, aerospace, paper and food, among other industries.
Five principles are the basis of lean manufacturing:
-
Define Value: Identify the social value of your business and what sets you apart.
-
Reduce Waste – Eliminate all activities that don't add value throughout the supply chain.
-
Create Flow – Ensure that work flows smoothly throughout the process.
-
Standardize and simplify – Make processes as repeatable and consistent as possible.
-
Develop Relationships: Establish personal relationships both with internal and external stakeholders.
Lean manufacturing is not a new concept, but it has been gaining popularity over the last few years due to a renewed interest in the economy following the global financial crisis of 2008. To increase their competitiveness, many businesses have turned to lean manufacturing. Economists think that lean manufacturing is a crucial factor in economic recovery.
With many benefits, lean manufacturing is becoming more common in the automotive industry. These include higher customer satisfaction levels, reduced inventory levels as well as lower operating costs.
You can apply Lean Manufacturing to virtually any aspect of your organization. Because it makes sure that all value chains are efficient and effectively managed, Lean Manufacturing is particularly helpful for organizations.
There are three types of lean manufacturing.
-
Just-in Time Manufacturing, (JIT): This kind of lean manufacturing is also commonly known as "pull-systems." JIT is a method in which components are assembled right at the moment of use, rather than being manufactured ahead of time. This strategy aims to decrease lead times, increase availability of parts and reduce inventory.
-
Zero Defects Manufacturing, (ZDM): ZDM is focused on ensuring that no defective products leave the manufacturing facility. If a part needs to be fixed during the assembly line, it should be repaired rather than scrapped. This is also true for finished products that require minor repairs before shipping.
-
Continuous Improvement: Continuous Improvement aims to improve efficiency by continually identifying problems and making adjustments to eliminate or minimize waste. Continuous Improvement involves continuous improvement of processes.