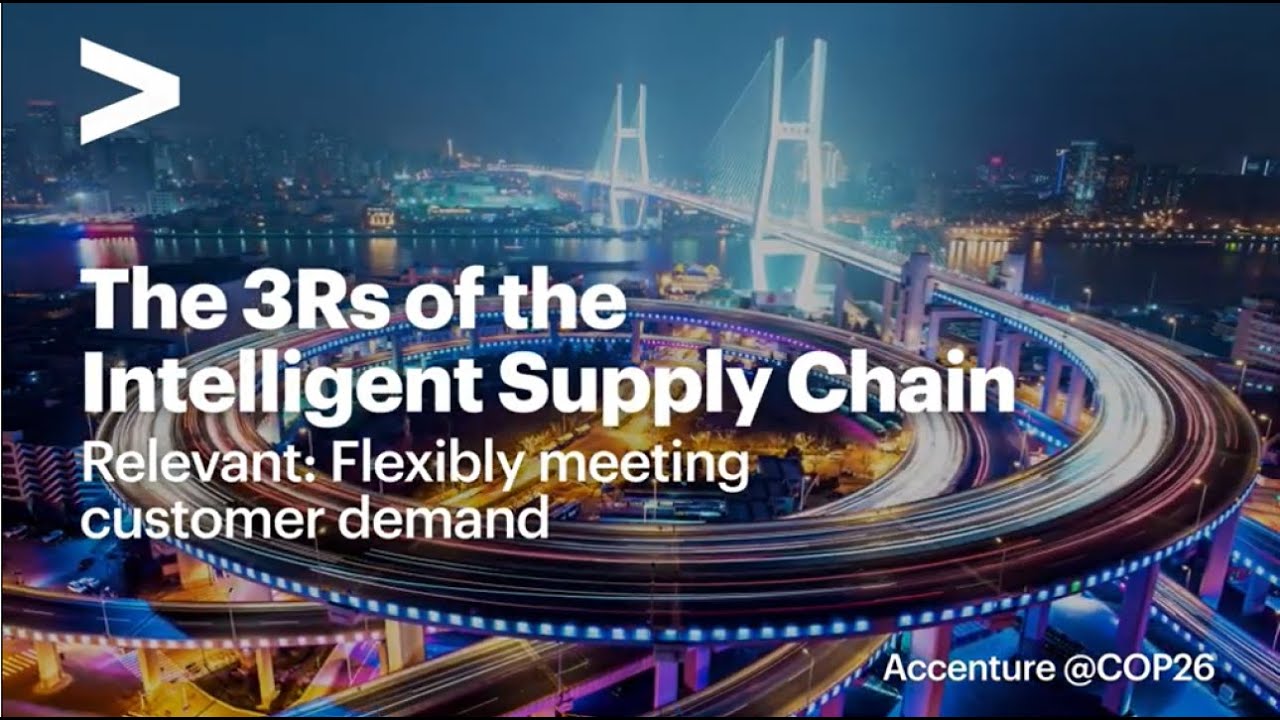
Manufacturing Extension Partnerships Centers (MEPs), located in every state and Puerto Rico, offer a comprehensive range of business services to assist small and middle-sized companies grow and flourish. MEP Centers can be found in all 50 states and Puerto Rico. They are trusted advisors who help manufacturers identify growth opportunities and solve their challenges.
MEP centers hire subject matter experts who have specific knowledge of their local industry and experience assisting small and medium-sized manufacturers in that sector. They offer support in a wide range of areas, including productivity enhancement, cybersecurity protection and growth for businesses. They also create tools that SMMs can use internally or develop with their suppliers, according to Sharon Ohman, senior services manager for Purdue University's MEP center in Fort Wayne.
Centers receive federal funding, of which one-half is allocated to each. The remaining funds are provided by state or local governments and/or by private entities. In January 2017, American Innovation and Competitiveness Act re-adjusted the cost share ratio of MEP centers. This allows them to retain more non-federal funding.
Many MEP centers are nonprofit organizations or are affiliated with universities. Other MEP center are run by the state government, or an agency in the same states as the center.
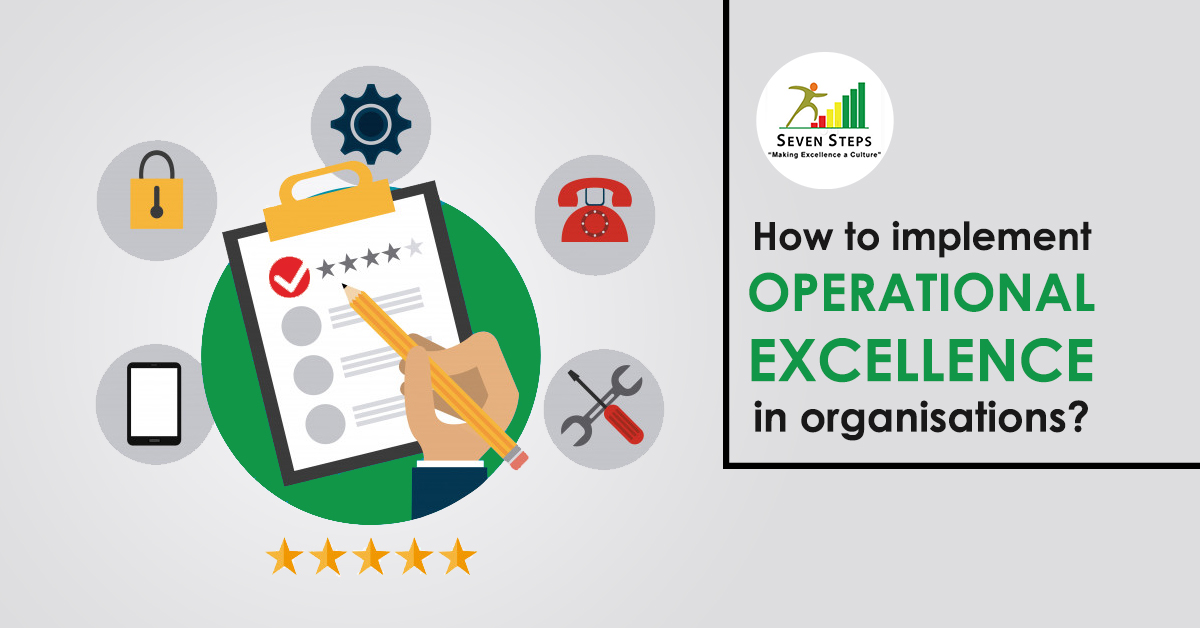
These centers may be staffed by professional technicians, managers or consultants. Some centers have more advanced technology and include laboratories or a center for research.
Some centers also offer training and consultation to other companies. Nebraska MEP offers support to manufacturers in implementing new technologies.
MEP services can be delivered to a manufacturer's employees or even to the company itself. Some centers provide specialists that travel to the site of manufacturing to work with the leader team.
During the past year, MEP centers connected with more than 3,000 manufacturers. It helped them to generate $14.4B in sales and $1.5B in cost-savings, $5.2B in new investments from clients, and 125,746 job creations across the U.S.
The MEP National Network is comprised of the NIST MEP Programme Office, 51 MEP Centers, and an MEP advisory board. These partners have an important role to play in the success of the MEP system by helping to ensure that the MEP system remains effective and has the capacity to expand its reach to U.S. manufacturers in the future.
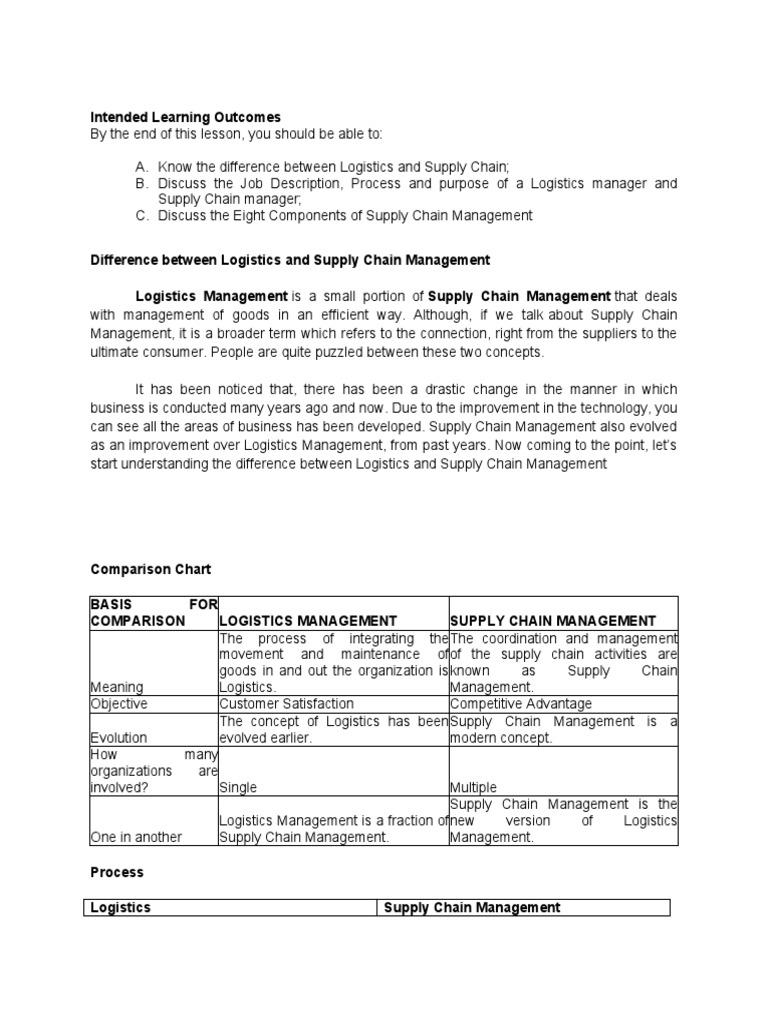
MEP Network's information infrastructure and pilots help MEP Centers and smaller manufacturers access the technical data they need to run their businesses. These projects aim to accelerate electronic commerce adoption by MEP centres and smaller manufacturers.
The MEP National Network also forms a major part of a national strategy that aims to help small and medium manufacturers adopt technology in order to grow their businesses and achieve economic growth. MEP National Network works to connect with more than 7 000 manufacturers annually, and their work contributes to innovation, growth of the economy and creation of jobs in the United States.
FAQ
What are the requirements to start a logistics business?
To run a successful logistics company, you need a lot knowledge and skills. Effective communication skills are necessary to work with suppliers and clients. It is important to be able to analyse data and draw conclusions. You need to be able work under pressure and manage stressful situations. In order to innovate and create new ways to improve efficiency, creativity is essential. You need to have strong leadership qualities to motivate team members and direct them towards achieving organizational goals.
You should also be organized and efficient to meet tight deadlines.
How can we improve manufacturing efficiency?
The first step is to identify the most important factors affecting production time. We then need to figure out how to improve these variables. If you don’t know where to begin, consider which factors have the largest impact on production times. Once you identify them, look for solutions.
Why automate your warehouse
Modern warehouses have become more dependent on automation. E-commerce has increased the demand for quicker delivery times and more efficient processes.
Warehouses should be able adapt quickly to new needs. They must invest heavily in technology to do this. Automating warehouses has many benefits. These are just a few reasons to invest in automation.
-
Increases throughput/productivity
-
Reduces errors
-
Increases accuracy
-
Safety is boosted
-
Eliminates bottlenecks
-
This allows companies to scale easily
-
Makes workers more efficient
-
It gives visibility to everything that happens inside the warehouse
-
Enhances customer experience
-
Improves employee satisfaction
-
This reduces downtime while increasing uptime
-
This ensures that quality products are delivered promptly
-
Eliminates human error
-
It helps ensure compliance with regulations
Do we need to know about Manufacturing Processes before learning about Logistics?
No. You don't have to know about manufacturing processes before learning about logistics. Understanding the manufacturing process will allow you to better understand logistics.
Why is logistics so important in manufacturing?
Logistics are essential to any business. They help you achieve great results by helping you manage all aspects of product flow, from raw materials to finished goods.
Logistics also play a major role in reducing costs and increasing efficiency.
What do you mean by warehouse?
Warehouses and storage facilities are where goods are kept before being sold. It can be an outdoor or indoor area. It may also be an indoor space or an outdoor area.
What is the responsibility for a logistics manager
Logistics managers make sure all goods are delivered on schedule and without damage. This is done by using his/her experience and knowledge of the company's products. He/she also needs to ensure adequate stock to meet demand.
Statistics
- (2:04) MTO is a production technique wherein products are customized according to customer specifications, and production only starts after an order is received. (oracle.com)
- You can multiply the result by 100 to get the total percent of monthly overhead. (investopedia.com)
- In 2021, an estimated 12.1 million Americans work in the manufacturing sector.6 (investopedia.com)
- Job #1 is delivering the ordered product according to specifications: color, size, brand, and quantity. (netsuite.com)
- In the United States, for example, manufacturing makes up 15% of the economic output. (twi-global.com)
External Links
How To
How to use the Just In-Time Production Method
Just-in-time is a way to cut costs and increase efficiency in business processes. This is where you have the right resources at the right time. This means that your only pay for the resources you actually use. Frederick Taylor was the first to coin this term. He developed it while working as a foreman during the early 1900s. He observed how workers were paid overtime if there were delays in their work. He realized that workers should have enough time to complete their jobs before they begin work. This would help increase productivity.
JIT is an acronym that means you need to plan ahead so you don’t waste your money. The entire project should be looked at from start to finish. You need to ensure you have enough resources to tackle any issues that might arise. You can anticipate problems and have enough equipment and people available to fix them. This will ensure that you don't spend more money on things that aren't necessary.
There are many types of JIT methods.
-
Demand-driven JIT: You order the parts and materials you need for your project every other day. This will enable you to keep track of how much material is left after you use it. You'll also be able to estimate how long it will take to produce more.
-
Inventory-based: You stock materials in advance to make your projects easier. This allows for you to anticipate how much you can sell.
-
Project-driven : This is a method where you make sure that enough money is set aside to pay the project's cost. Knowing how much money you have available will help you purchase the correct amount of materials.
-
Resource-based JIT: This type of JIT is most commonly used. This is where you assign resources based upon demand. For example, if there is a lot of work coming in, you will have more people assigned to them. If you don't receive many orders, then you'll assign fewer employees to handle the load.
-
Cost-based: This is similar to resource-based, except that here you're not just concerned about how many people you have but how much each person costs.
-
Price-based pricing: This is similar in concept to cost-based but instead you look at how much each worker costs, it looks at the overall company's price.
-
Material-based is an alternative to cost-based. Instead of looking at the total cost in the company, this method focuses on the average amount of raw materials that you consume.
-
Time-based JIT: This is another variant of resource-based JIT. Instead of focusing on how much each employee costs, you focus on how long it takes to complete the project.
-
Quality-based JIT - This is another form of resource-based JIT. Instead of thinking about how much each employee costs or how long it takes to manufacture something, you think about how good the quality of your product is.
-
Value-based JIT is the newest form of JIT. In this instance, you are not concerned about the product's performance or meeting customer expectations. Instead, you're focused on how much value you add to the market.
-
Stock-based: This inventory-based approach focuses on how many items are being produced at any one time. It's useful when you want maximum production and minimal inventory.
-
Just-in time (JIT), planning: This is a combination JIT/supply chain management. It is the process of scheduling components' delivery as soon as they have been ordered. It reduces lead times and improves throughput.