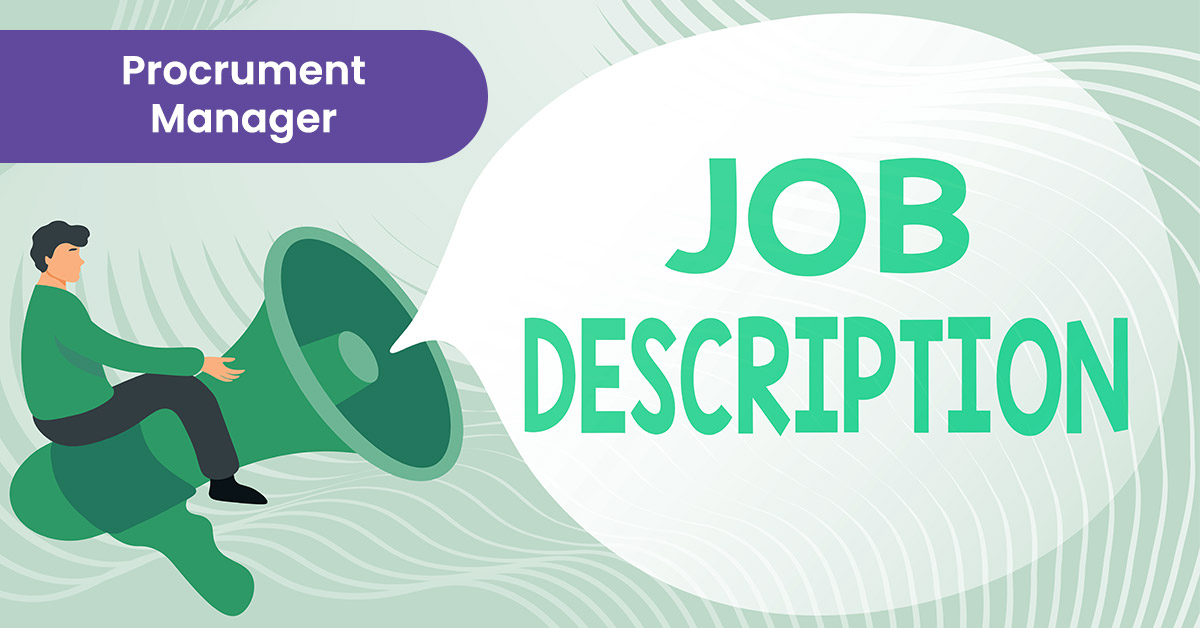
Whether you are running a small business or the enterprise arm of a major corporation, supply chain risk management is a necessary component to maintaining a robust operation. Risks vary from the mundane to the downright disastrous. Your organization can be protected from losses with a well-planned plan and an effective implementation strategy.
One of the most important aspects of a supply chain continuity plan is data sharing. If your organization is dependent on a single supplier it can lead to supplier disputes and vendor failures. However, if your company is part of a multi-supplier consortium, you are more likely to avoid supply disruptions. You might also be able negotiate with an alternative supplier.
A complex network of contractors can also increase your risk of vendor fraud and duplicate billing. You can create a risk assessment method to help reduce these risks. This can include a thorough assessment of your partners, suppliers, and other tier-one components.
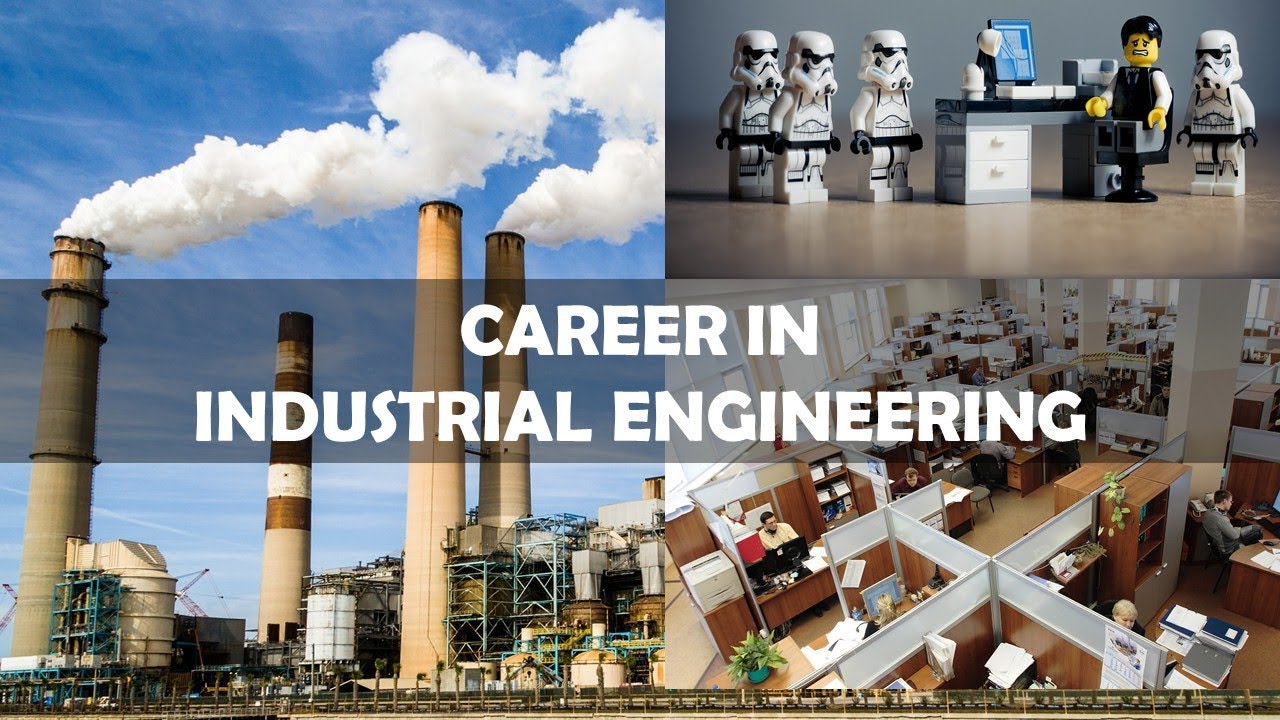
When developing a good supply chain risk management program, you should first identify the important elements of a good supply chain, then quantify and measure them, and then devise an action plan. This should involve the aforementioned items, plus a few more. A proactive monitoring system is the most important component. It is important that your executives have access to real-time, accurate information regarding supply chain risk. Real-time supply chain risk tracking will help you make informed decisions and respond promptly.
When assessing and quantifying risks, you must remember that resilience of your supply chain is a function governance. It is important to take into account the role of stakeholders. The supplier bankruptcy that caused disruption in the supply chain of the pharmaceutical industry could have easily been avoided if the company had correctly scoredcarded all its suppliers.
The first step to reducing supply chain disruptions is having a plan. It isn't always easy to implement the right contingency planning. Many businesses neglect to make the effort to have enough contingency planning for every risk they face. This should start with the greatest possible impact.
The PPPR, or preventive preparedness, readiness, response and recovery, is a global standard for supply-chain risk management. This is a strong approach that will help improve your ability monitor and respond to disruptions in supply chains. It can also be used in conjunction other strategies to protect your business from potential risks. Using a PPPR guide to your organization can mean the difference between survival and success in today's market.
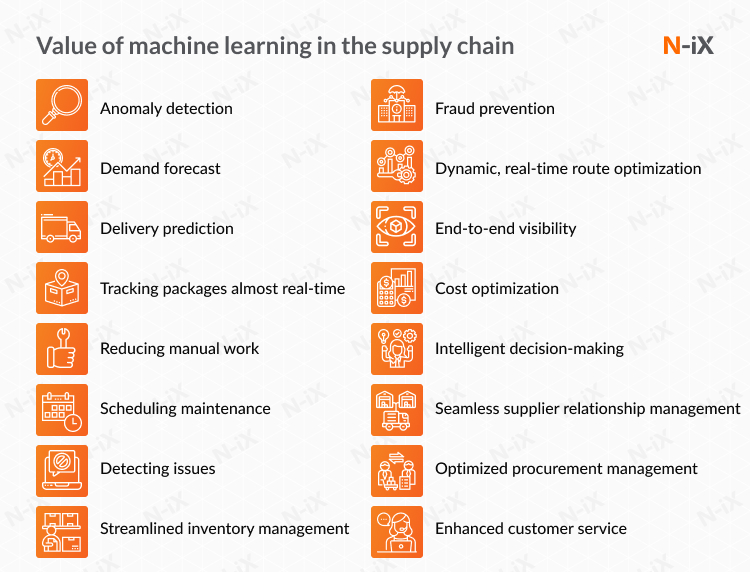
The right data can help you understand your suppliers' history and what they offer. This data can be used to inform your decision-making. Information that is reliable can help you offer the right risk premiums for your insurers.
FAQ
What is the importance of automation in manufacturing?
Automation is important not only for manufacturers but also for service providers. It allows them to offer services faster and more efficiently. It helps them to lower costs by reducing human errors, and improving productivity.
What is the responsibility for a logistics manager
Logistics managers ensure that goods arrive on time and are unharmed. This is done using his/her knowledge of the company's products. He/she should also ensure enough stock is available to meet demand.
Can certain manufacturing steps be automated?
Yes! Automation has been around since ancient times. The Egyptians invented the wheel thousands of years ago. We now use robots to help us with assembly lines.
Actually, robotics can be used in manufacturing for many purposes. These include:
-
Assembly line robots
-
Robot welding
-
Robot painting
-
Robotics inspection
-
Robots that produce products
Automation can be applied to manufacturing in many other ways. 3D printing, for example, allows us to create custom products without waiting for them to be made.
Statistics
- [54][55] These are the top 50 countries by the total value of manufacturing output in US dollars for its noted year according to World Bank.[56] (en.wikipedia.org)
- (2:04) MTO is a production technique wherein products are customized according to customer specifications, and production only starts after an order is received. (oracle.com)
- In the United States, for example, manufacturing makes up 15% of the economic output. (twi-global.com)
- Many factories witnessed a 30% increase in output due to the shift to electric motors. (en.wikipedia.org)
- Job #1 is delivering the ordered product according to specifications: color, size, brand, and quantity. (netsuite.com)
External Links
How To
How to Use Six Sigma in Manufacturing
Six Sigma is defined by "the application SPC (statistical process control) techniques to achieve continuous improvements." Motorola's Quality Improvement Department created Six Sigma at their Tokyo plant, Japan in 1986. Six Sigma's basic concept is to improve quality and eliminate defects through standardization. Since there are no perfect products, or services, this approach has been adopted by many companies over the years. Six Sigma's primary goal is to reduce variation from the average value of production. If you take a sample and compare it with the average, you will be able to determine how much of the production process is different from the norm. If the deviation is excessive, it's likely that something needs to be fixed.
Understanding how your business' variability is a key step towards Six Sigma implementation is the first. Once you understand that, it is time to identify the sources of variation. Also, you will need to identify the sources of variation. Random variations occur when people make mistakes; systematic ones are caused by factors outside the process itself. Random variations would include, for example, the failure of some widgets to fall from the assembly line. You might notice that your widgets always fall apart at the same place every time you put them together.
Once you've identified where the problems lie, you'll want to design solutions to eliminate those problems. It might mean changing the way you do business or redesigning it entirely. You should then test the changes again after they have been implemented. If they don’t work, you’ll need to go back and rework the plan.