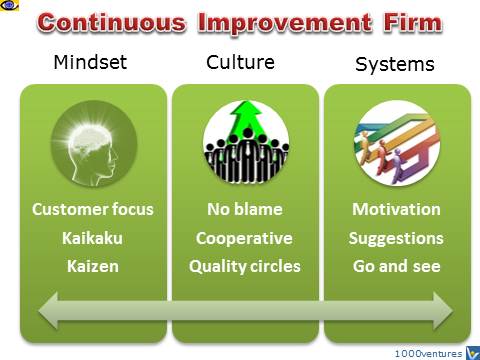
Visual management is the act of using visual signals to convey information. This process helps to increase efficiency and clarity, as information is instantly recognized. There are several kinds of visual control. Here are some examples. You can also learn about visual control in Lean Manufacturing. Continue reading for more information. This method is a great tool to get your business on track with lean production.
Lean manufacturing
Andon is a Japanese term for status-display visualization. It is one of many methods for visual management in lean manufacturing. This helps supervisors and workers to see the status of their work, process flow, and any other relevant information. Visual management allows for the easy labeling and marking of workspaces, materials or parts. It helps to identify inefficiencies and streamline processes. Below are some of the many benefits of visual control in lean manufacturing.
Lean methodology is incomplete without visible tools that allow for visual management. Supervisors and operators can use visual signals to identify waste, improve process flow and avoid errors. It can also reduce safety risks. By looking at floor markings or other visual indicators, forklift drivers can ensure they are in the right place. Visual management is a key component of lean manufacturing. Workers will be able to work more efficiently if they use visual management. In addition to reducing waste, visual management also minimizes safety risks.
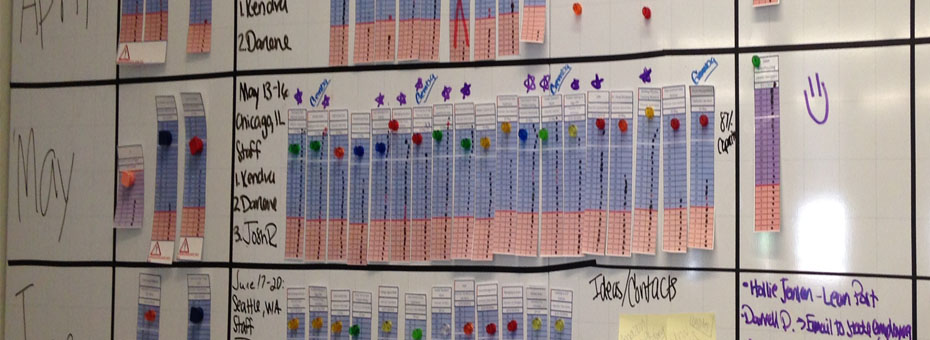
Process control charts
Process control charts can help you visualize performance metrics, establish a baseline and improve output. They help management, operators, and other stakeholders get on the same page by identifying common causes of variation and setting the correct path for improvement. Because they show unusual patterns, these charts are very helpful in processes that are outof control. Because they are very easy to make, process control charts can be used for visual management. They can also be used to show the status of any system or process.
The control chart serves the primary purpose of tracking process performance over time. These charts show the sequence of measurements or samples, which allows a manager to determine if the process has been stable. They can also be used to spot problems or propose solutions. An operator can use the centerline of the control charts to compare the process's performance against its baseline. The control limits typically have three standard deviations above or below the centerline.
FIFO lane
FIFO lanes are a way to increase system throughput and utilization. Consider a fast food restaurant or assembly line. It is likely that you have felt the frustration of having to wait in long lines for something. FiFo lane allows you to manage work flow and establish priority in lines by using visual management. You can mark these lanes with markings on roller conveyors and painted lines on the ground. The first job from Process A would move into the first FIFO lane. The next job will be moved to the next vacant position.
Time registration is one way to improve FIFO lane visual control. Employees can record the date and time when carts are loaded into a FIFO lane. Some employees use digital clocks to count the number of products immediately after putting them in the FIFO lane. To write times on carts, you can also use whiteboard stickers. These stickers can be used by downstream employees to write down times on carts.
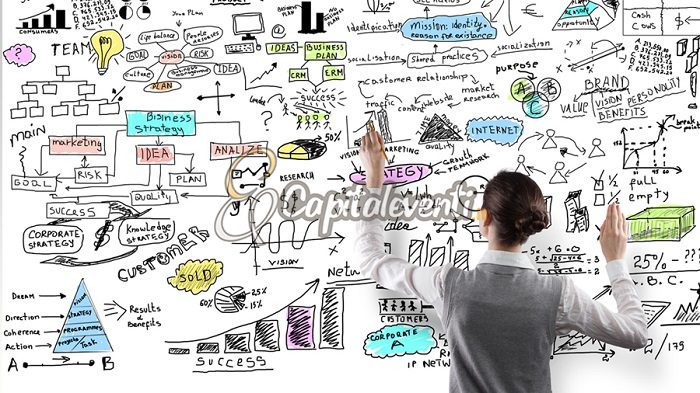
Lean daily management board
A multidisciplinary team was responsible for creating the Lean Daily Management Board. The board is based in part on five predetermined indicators: patient outcomes; documentation adherence; employee engagement and productivity. Each day, this team met to assess progress in each area. Each day, the team reviewed progress using a checklist. This included medication compliance and medication falls. To address any problems, they also used a problem-solving tool. The initial data collected in January 2014 noted a medication scan rate of 75% and a fall rate of 1.32/1000 patient days. However, these initial data were not specific to continuing education or patient care.
Daily management allows for a more visible view of the process and allows for managers to address problems as they arise. Poor performers will not accept more work. Poor performers will have to make their stretching work visible in order to take into account the extra effort and time it takes. Although daily management is not intended to be punitive it does point out inefficient and ineffective processes. People should be able to point out the failure of a process.
FAQ
What makes a production planner different from a project manger?
The difference between a product planner and project manager is that a planer is typically the one who organizes and plans the entire project. A production planner, however, is mostly involved in the planning stages.
What does warehouse refer to?
A warehouse, or storage facility, is where goods are stored prior to being sold. It can be indoors or out. It may also be an indoor space or an outdoor area.
What is the responsibility for a logistics manager
A logistics manager ensures that all goods are delivered on time and without damage. This is accomplished by using the experience and knowledge gained from working with company products. He/she should also ensure enough stock is available to meet demand.
How can manufacturing efficiency improved?
The first step is to identify the most important factors affecting production time. Next, we must find ways to improve those factors. If you don’t know how to start, look at which factors have the greatest impact upon production time. Once you identify them, look for solutions.
What are manufacturing & logistics?
Manufacturing refers the process of producing goods from raw materials through machines and processes. Logistics encompasses the management of all aspects associated with supply chain activities such as procurement, production planning, distribution and inventory control. It also includes customer service. Sometimes manufacturing and logistics are combined to refer to a wider term that includes both the process of creating products as well as their delivery to customers.
What does the term manufacturing industries mean?
Manufacturing Industries refers to businesses that manufacture products. Consumers are the people who purchase these products. These companies use a variety processes such as distribution, retailing and management to accomplish their purpose. They produce goods from raw materials by using machines and other machinery. This includes all types manufactured goods such as clothing, building materials, furniture, electronics, tools and machinery.
What are the jobs in logistics?
Logistics can offer many different jobs. Some examples are:
-
Warehouse workers - They load trucks and pallets.
-
Transportation drivers – These drivers drive trucks and wagons to transport goods and pick up the goods.
-
Freight handlers are people who sort and pack freight into warehouses.
-
Inventory managers – They manage the inventory in warehouses.
-
Sales reps are people who sell products to customers.
-
Logistics coordinators – They plan and coordinate logistics operations.
-
Purchasing agents are those who purchase goods and services for the company.
-
Customer service representatives are available to answer customer calls and emails.
-
Shipping clerks – They process shipping orders, and issue bills.
-
Order fillers – They fill orders based upon what was ordered and shipped.
-
Quality control inspectors (QCI) - They inspect all incoming and departing products for potential defects.
-
Others – There are many other types available in logistics. They include transport supervisors, cargo specialists and others.
Statistics
- In 2021, an estimated 12.1 million Americans work in the manufacturing sector.6 (investopedia.com)
- It's estimated that 10.8% of the U.S. GDP in 2020 was contributed to manufacturing. (investopedia.com)
- According to the United Nations Industrial Development Organization (UNIDO), China is the top manufacturer worldwide by 2019 output, producing 28.7% of the total global manufacturing output, followed by the United States, Japan, Germany, and India.[52][53] (en.wikipedia.org)
- You can multiply the result by 100 to get the total percent of monthly overhead. (investopedia.com)
- Many factories witnessed a 30% increase in output due to the shift to electric motors. (en.wikipedia.org)
External Links
How To
How to use lean manufacturing in the production of goods
Lean manufacturing refers to a method of managing that seeks to improve efficiency and decrease waste. It was developed in Japan between 1970 and 1980 by Taiichi Ohno. TPS founder Kanji Tyoda gave him the Toyota Production System, or TPS award. Michael L. Watkins published the book "The Machine That Changed the World", which was the first to be published about lean manufacturing.
Lean manufacturing is often described as a set if principles that help improve the quality and speed of products and services. It emphasizes the elimination of defects and waste throughout the value stream. Lean manufacturing can be described as just-in–time (JIT), total productive maintenance, zero defect (TPM), or even 5S. Lean manufacturing seeks to eliminate non-value added activities, such as inspection, work, waiting, and rework.
Lean manufacturing is a way for companies to achieve their goals faster, improve product quality, and lower costs. Lean Manufacturing is one of the most efficient ways to manage the entire value chains, including suppliers and customers as well distributors and retailers. Lean manufacturing practices are widespread in many industries. Toyota's philosophy has been a key driver of success in many industries, including automobiles and electronics.
Five principles are the basis of lean manufacturing:
-
Define Value: Identify the social value of your business and what sets you apart.
-
Reduce waste - Stop any activity that isn't adding value to the supply chains.
-
Create Flow - Ensure work moves smoothly through the process without interruption.
-
Standardize and simplify - Make your processes as consistent as possible.
-
Build Relationships - Establish personal relationships with both internal and external stakeholders.
Lean manufacturing is not a new concept, but it has been gaining popularity over the last few years due to a renewed interest in the economy following the global financial crisis of 2008. Many businesses are now using lean manufacturing to improve their competitiveness. According to some economists, lean manufacturing could be a significant factor in the economic recovery.
Lean manufacturing, which has many benefits, is now a standard practice in the automotive industry. These benefits include increased customer satisfaction, reduced inventory levels and lower operating costs.
It can be applied to any aspect of an organisation. However, it is particularly useful when applied to the production side of an organization because it ensures that all steps in the value chain are efficient and effective.
There are three types principally of lean manufacturing:
-
Just-in Time Manufacturing (JIT), also known as "pull system": This form of lean manufacturing is often referred to simply as "pull". JIT means that components are assembled at the time of use and not manufactured in advance. This approach reduces lead time, increases availability and reduces inventory.
-
Zero Defects Manufacturing, (ZDM): ZDM is focused on ensuring that no defective products leave the manufacturing facility. You should repair any part that needs to be repaired during an assembly line. This also applies to finished products that need minor repairs before being shipped.
-
Continuous Improvement (CI), also known as Continuous Improvement, aims at improving the efficiency of operations through continuous identification and improvement to minimize or eliminate waste. Continuous Improvement (CI) involves continuous improvement in processes, people, tools, and infrastructure.