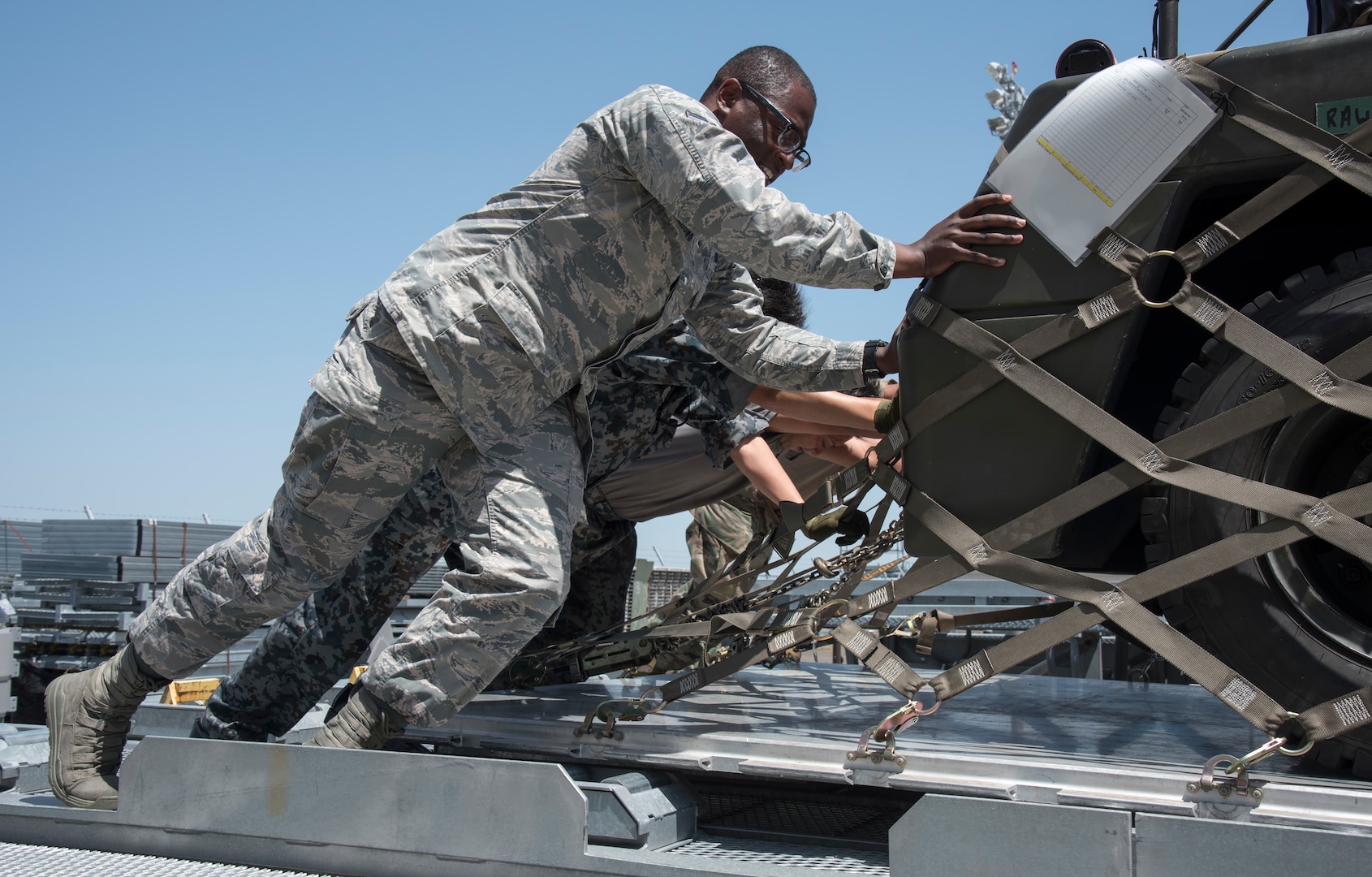
Oracle Supply Chain Management offers a comprehensive solution that enables organizations to respond quickly to changes, build resilient networks, improve forecast accuracy, and adapt quickly in the face of changing circumstances. Oracle SCM allows flexible supply chain planning. It provides end-to-end visibility across the entire supply chain. This improves collaboration while minimizing costs. Oracle Fusion CloudSCM allows you to improve your business processes while collaborating more effectively with your suppliers. Oracle SCM can help you achieve these goals, while reducing disruptions, reducing costs, and improving forecast accuracy.
Friendly interface
Many of the new features in Oracle SCM can be attributed to the improved user interface. This new release makes Oracle SCM more accessible and user-friendly. A product-based analysis script provides solutions, recommendations, and early warnings. An excellent example is the Oracle Inbound Transactions Analyzer. It is designed to detect inbound transactions issues and offer solutions. It is also highly customizable.
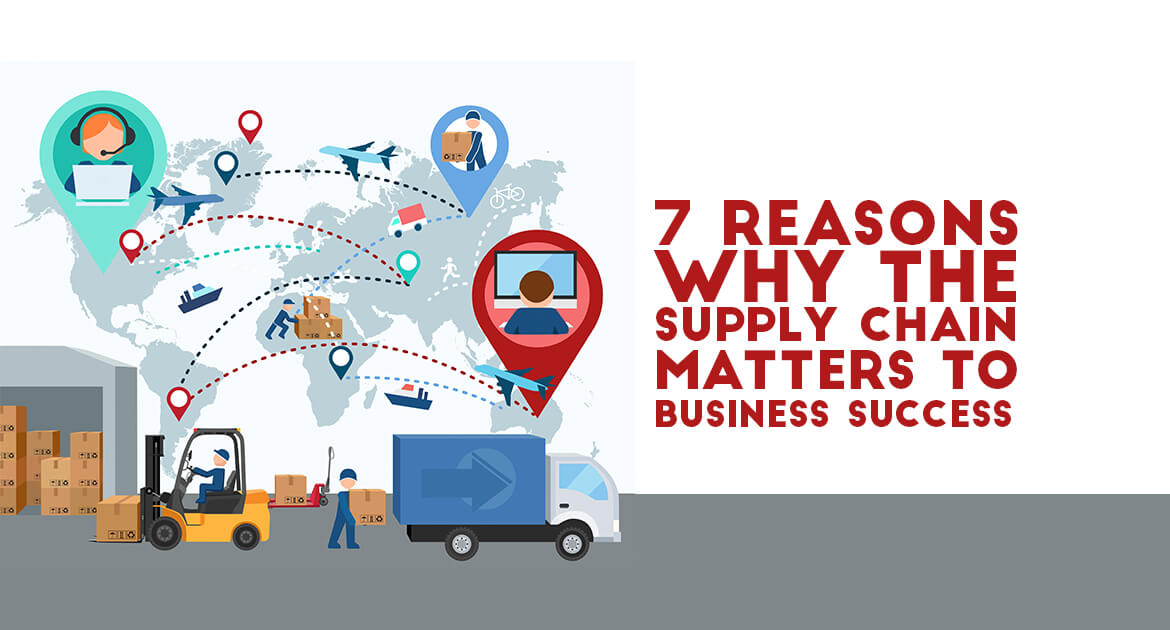
Cost Management
Oracle SCM allows you to set cost management policies for each item. Instead of relying upon a single costing method for all items, cost profiles are able to be customized by manufacturing process and product. For instance, manufactured items may be driven by a standard rolled up cost, while repair items will use the actual costing method. The software can also support multiple open and close periods. It also supports cost simulation and copying.
Support for decision making
Oracle SCM provides decision support. This is the use of advanced analysis to improve the performance and efficiency of management processes. Management can make the right decision based on information and data by using a range of business intelligence tool. Oracle Strategic Enterprise Management applications support many strategic management techniques. With this technology, executives can manage costs and measure their progress against a defined plan. They can also measure and pay employees based upon their performance. These integrated enterprise-wide applications complement Oracle's ERP systems.
Compliance with regulations
As regulatory compliance laws and regulations continue to increase, organizations need to find effective ways to manage them. Oracle has the answer. Oracle SCM regulatory compliance solutions allow organizations to more easily meet legal and regulatory compliance needs. The Oracle Cloud Platform offers flexible deployment options that can be used by organizations of any size. Oracle offers a range of configurable, customizable products that can be customized to meet regulatory compliance requirements.
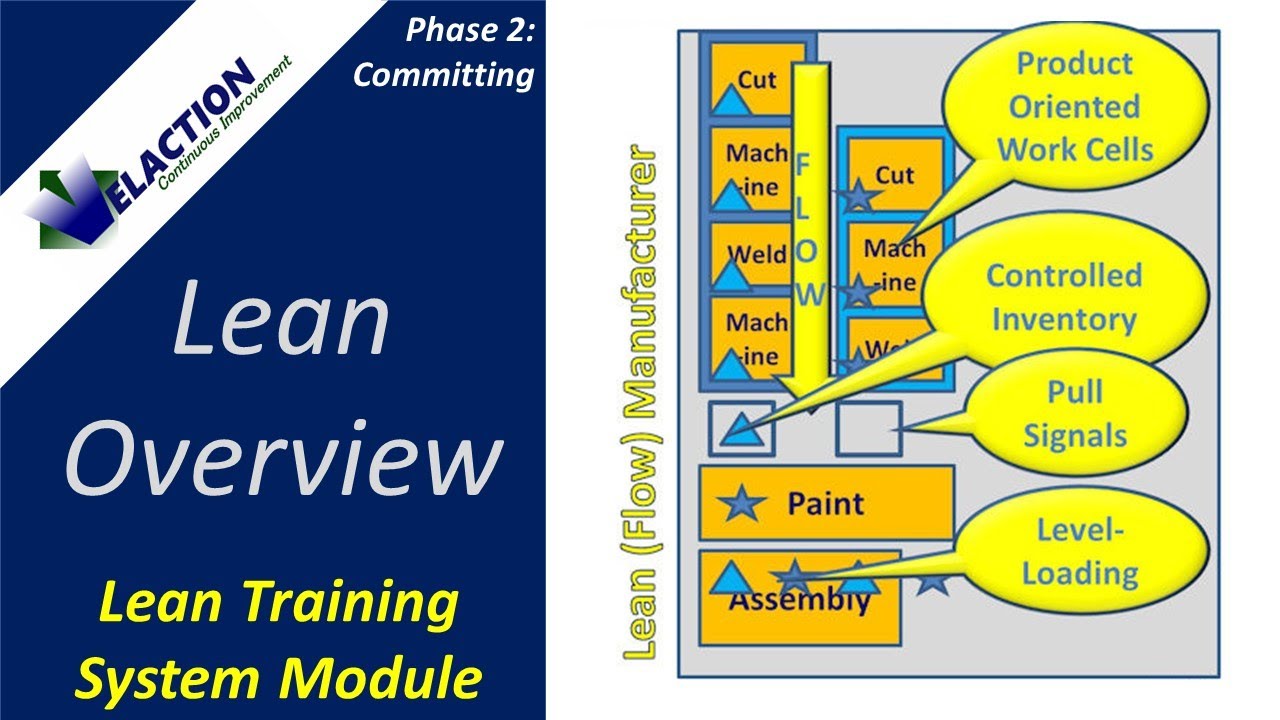
Flexible solution
Intellinum Inc., the world's leading supplier of supply chain mobility systems, created Flexi LogiPro. A flexible solution for Oracle SCM or Oracle WMSCloud, Flexi LogiPro is an innovative solution. The flexible mobile solution offers a barcode enabled, customizable user interface for mobile devices. It seamlessly integrates with Oracle SCM, WMS Cloud and Oracle SCM backend systems. It is available both for cloud and on-premise deployments. This allows companies to customize mobile apps for their unique needs.
FAQ
How can excess manufacturing production be reduced?
Better inventory management is key to reducing excess production. This would decrease the time that is spent on inefficient activities like purchasing, storing, or maintaining excess stock. We could use these resources to do other productive tasks.
A Kanban system is one way to achieve this. A Kanban board is a visual display used to track work in progress. Kanban systems are where work items travel through a series of states until reaching their final destination. Each state has a different priority level.
If work is moving from one stage to the other, then the current task can be completed and moved on to the next. But if a task remains in the beginning stages it will stay that way until it reaches its end.
This allows work to move forward and ensures that no work is missed. Managers can monitor the work being done by Kanban boards to see what is happening at any given time. This information allows them to adjust their workflow based on real-time data.
Lean manufacturing can also be used to reduce inventory levels. Lean manufacturing works to eliminate waste throughout every stage of the production chain. Waste includes anything that does not add value to the product. The following are examples of common waste types:
-
Overproduction
-
Inventory
-
Unnecessary packaging
-
Exceed materials
Manufacturers can reduce their costs and improve their efficiency by using these ideas.
What are the main products of logistics?
Logistics refers to all activities that involve moving goods from A to B.
They include all aspects associated with transport including packaging, loading transporting, unloading storage, warehousing inventory management customer service, distribution returns and recycling.
Logisticians ensure that the right product reaches the right place at the right time and under safe conditions. They provide information on demand forecasts as well stock levels, production schedules and availability of raw material.
They also keep track of shipments in transit, monitor quality standards, perform inventories and order replenishment, coordinate with suppliers and vendors, and provide support services for sales and marketing.
Is there anything we should know about Manufacturing Processes prior to learning about Logistics.
No. No. Understanding the manufacturing process will allow you to better understand logistics.
What does the term manufacturing industries mean?
Manufacturing Industries is a group of businesses that produce goods for sale. Consumers are those who purchase these products. These companies use a variety processes such as distribution, retailing and management to accomplish their purpose. These companies produce goods using raw materials and other equipment. This includes all types manufactured goods such as clothing, building materials, furniture, electronics, tools and machinery.
What are the responsibilities of a logistic manager?
A logistics manager ensures that all goods are delivered on time and without damage. This is done by using his/her experience and knowledge of the company's products. He/she should make sure that enough stock is on hand to meet the demands.
How can manufacturing efficiency be improved?
First, identify the factors that affect production time. We then need to figure out how to improve these variables. If you don’t know where to begin, consider which factors have the largest impact on production times. Once you've identified them all, find solutions to each one.
Statistics
- [54][55] These are the top 50 countries by the total value of manufacturing output in US dollars for its noted year according to World Bank.[56] (en.wikipedia.org)
- In the United States, for example, manufacturing makes up 15% of the economic output. (twi-global.com)
- In 2021, an estimated 12.1 million Americans work in the manufacturing sector.6 (investopedia.com)
- Job #1 is delivering the ordered product according to specifications: color, size, brand, and quantity. (netsuite.com)
- According to a Statista study, U.S. businesses spent $1.63 trillion on logistics in 2019, moving goods from origin to end user through various supply chain network segments. (netsuite.com)
External Links
How To
How to use the Just-In Time Method in Production
Just-in time (JIT), is a process that reduces costs and increases efficiency in business operations. This is where you have the right resources at the right time. This means that you only pay for what you actually use. The term was first coined by Frederick Taylor, who developed his theory while working as a foreman in the early 1900s. He noticed that workers were often paid overtime when they had to work late. He decided that workers would be more productive if they had enough time to complete their work before they started to work.
JIT is about planning ahead. You should have all the necessary resources ready to go so that you don’t waste money. It is important to look at your entire project from beginning to end and ensure that you have enough resources to handle any issues that may arise. You can anticipate problems and have enough equipment and people available to fix them. This way you won't be spending more on things that aren’t really needed.
There are many JIT methods.
-
Demand-driven JIT: You order the parts and materials you need for your project every other day. This will allow for you to track the material that you have left after using it. This will allow to you estimate the time it will take for more to be produced.
-
Inventory-based: This type allows you to stock the materials needed for your projects ahead of time. This allows for you to anticipate how much you can sell.
-
Project-driven: This is an approach where you set aside enough funds to cover the cost of your project. When you know how much you need, you'll purchase the appropriate amount of materials.
-
Resource-based JIT: This is the most popular form of JIT. You assign certain resources based off demand. You might assign more people to help with orders if there are many. If you don't have many orders, you'll assign fewer people to handle the workload.
-
Cost-based: This is the same as resource-based except that you don't care how many people there are but how much each one of them costs.
-
Price-based: This is a variant of cost-based. However, instead of focusing on the individual workers' costs, this looks at the total price of the company.
-
Material-based: This approach is similar to cost-based. However, instead of looking at the total cost for the company, you look at how much you spend on average on raw materials.
-
Time-based JIT is another form of resource-based JIT. Instead of focusing on how much each employee costs, you focus on how long it takes to complete the project.
-
Quality-based: This is yet another variation of resource-based JIT. Instead of thinking about the cost of each employee or the time it takes to produce something, you focus on how good your product quality.
-
Value-based JIT is the newest form of JIT. In this case, you're not concerned with how well the products perform or whether they meet customer expectations. Instead, your goal is to add value to the market.
-
Stock-based. This method is inventory-based and focuses only on the actual production at any given point. It is used when production goals are met while inventory is kept to a minimum.
-
Just-in-time planning (JIT): This is a combination JIT and supply-chain management. It is the process of scheduling components' delivery as soon as they have been ordered. It is essential because it reduces lead-times and increases throughput.