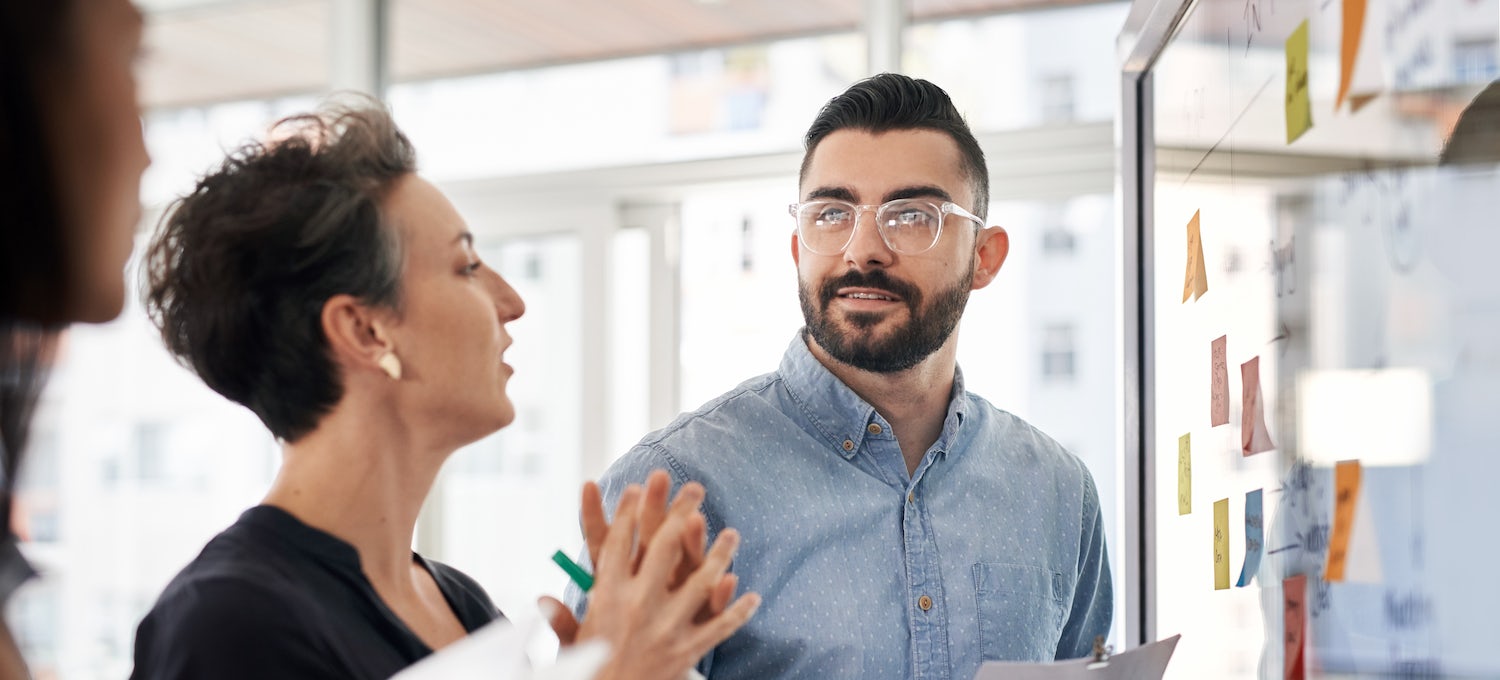
BLS Mechanical engineers are highly sought-after professionals who have extensive engineering knowledge and education. A BLS Mechanical Engineer is highly skilled and has a strong educational background. They are also highly qualified to serve as managers and team leaders. There are good job prospects for this career path in the next 10 year, with a 7% increase in available jobs by 2030. This will translate into an additional 20,900 new jobs. For this job, candidates need to have extensive knowledge and experience in simulation and computer-aided designing.
Your job duties
A mechanical engineer works to plan, design, or develop power-producing equipment. These professionals can also oversee the maintenance, installation, maintenance, and repair machines. They can work as independent consultants or in large engineering services firms. They may also design refrigeration systems for frozen foods or air-conditioning systems for buildings. Below are details about the salaries and employment of mechanical engineers.
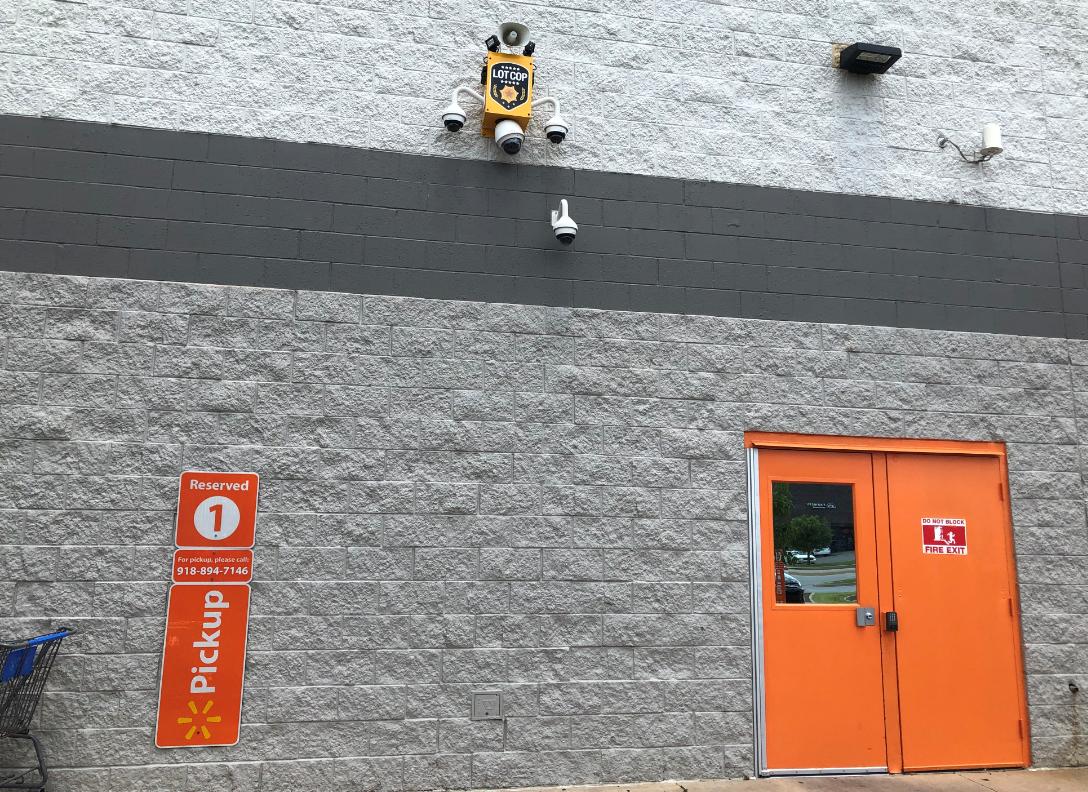
Entry-level mechanical engineers typically work in an office environment, but may also travel to the site of a construction project to work on an equipment problem. Basic business principles are required for entry-level positions. Additionally, mechanical engineers will use computers regularly, and therefore should have a strong grasp of computer science and IT. A strong technical skill set is important for analyzing designs and integrating sensors within machinery.
Education necessary
The Bachelor of Science Degree in Mechanical Engineering (BSME), is a great way for you to get into mechanical engineering. This degree typically lasts four years and covers the fundamentals of design, testing, manufacturing, and other aspects. Students learn how computer software can be used to create mechanical drawings or other designs. Whether you are interested in the design of airplanes, cars, or other machinery, a BSME will help you find a career in this exciting field.
This field is in good shape according to the BLS. BLS predicts that mechanical engineers will see a 4 percentage increase in employment between 2019-2029. Engineers will be able to work in management positions or as faculty members at higher education institutions. This job earns the average $84,190 salary. Additionally, the U.S. is expected to see a rise in employment for mechanical engineers over the next decade.
Salary
According to the U.S. Bureau of Labor Statistics (USBLS), the number of mechanical engineers is expected to grow by 5 percent between 2012-2022. This is a slower growth than the average of all occupations, but still very impressive. Those who stay on top of the latest technological advances will stand to benefit in a competitive job market. There are many factors which can impact the salary of an engineer in mechanical engineering.
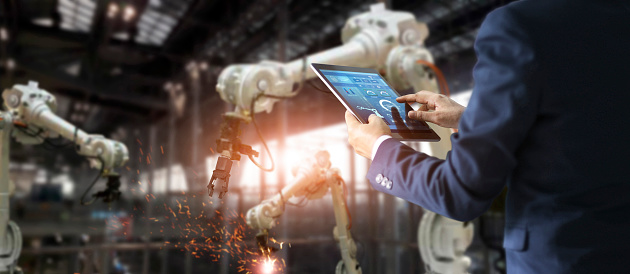
Although there are many factors that affect the amount of a salary, mechanical engineers usually make more than other types of engineers. In fact the top 10 per cent earned more money than $126,000.430 per year. Mechanical engineers can also expect to make a career in electronic product and computer manufacturing, along with higher salaries. California, New Mexico, Alaska and Alaska are the three states that pay the most for mechanical engineers. These states are ranked by their wage levels, which varies widely depending on experience and education.
FAQ
What is production planning?
Production Planning includes planning for all aspects related to production. It is important to have everything ready and planned before you start shooting. It should also provide information about how best to produce the best results while on set. This information includes locations, crew details and equipment requirements.
It is important to first outline the type of film you would like to make. You may have already decided where you would like to shoot, or maybe there are specific locations or sets that you want to use. Once you have determined your scenes and locations, it is time to start figuring out the elements that you will need for each scene. One example is if you are unsure of the exact model you want but decide that you require a car. This is where you can look up car models online and narrow down your options by choosing from different makes and models.
After you have chosen the right car, you will be able to begin thinking about accessories. Are you looking for people to sit in the front seats? Or maybe you just need someone to push the car around. Perhaps you would like to change the interior colour from black to white. These questions will help you determine the exact look and feel of your car. Another thing you can do is think about what type of shots are desired. Will you be filming close-ups or wide angles? Maybe the engine or steering wheel is what you are looking to film. These details will help identify the exact car you wish to film.
Once you have established all the details, you can create a schedule. You can use a schedule to determine when and where you need it to be shot. Each day will include the time when you need to arrive at the location, when you need to leave and when you need to return home. So everyone is clear about what they need to do. It is possible to make arrangements in advance for additional staff if you are looking to hire. It is not worth hiring someone who won’t show up because you didn’t tell him.
Also, consider how many days you will be filming your schedule. Some projects are quick and easy, while others take weeks. You should consider whether you will need more than one shot per week when creating your schedule. Multiple takes at the same place will result in higher costs and longer completion times. If you aren't sure whether you need multiple shots, it is best to take fewer photos than you would like.
Budgeting is another important aspect of production planning. As it will allow you and your team to work within your financial means, setting a realistic budget is crucial. Remember that you can always reduce the budget later on if you run into unforeseen problems. You shouldn't underestimate the amount you'll spend. If you underestimate how much something costs, you'll have less money to pay for other items.
Production planning can be a complex process. However, once you know how everything works together it will become easier to plan future projects.
What is the job of a production plan?
A production planner ensures all aspects of the project are delivered on time, within budget, and within scope. They ensure that the product or service is of high quality and meets client requirements.
What does "warehouse" mean?
A warehouse or storage facility is where goods are stored before they are sold. It can be an indoor space or an outdoor area. In some cases it could be both indoors and outdoors.
Statistics
- In 2021, an estimated 12.1 million Americans work in the manufacturing sector.6 (investopedia.com)
- In the United States, for example, manufacturing makes up 15% of the economic output. (twi-global.com)
- Many factories witnessed a 30% increase in output due to the shift to electric motors. (en.wikipedia.org)
- According to a Statista study, U.S. businesses spent $1.63 trillion on logistics in 2019, moving goods from origin to end user through various supply chain network segments. (netsuite.com)
- You can multiply the result by 100 to get the total percent of monthly overhead. (investopedia.com)
External Links
How To
How to Use the Just In Time Method in Production
Just-in-time is a way to cut costs and increase efficiency in business processes. It allows you to get the right amount resources at the right time. This means that only what you use is charged to your account. Frederick Taylor first coined this term while working in the early 1900s as a foreman. After observing how workers were paid overtime for late work, he realized that overtime was a common practice. He then concluded that if he could ensure that workers had enough time to do their job before starting to work, this would improve productivity.
JIT is a way to plan ahead and make sure you don't waste any money. It is important to look at your entire project from beginning to end and ensure that you have enough resources to handle any issues that may arise. You can anticipate problems and have enough equipment and people available to fix them. This will prevent you from spending extra money on unnecessary things.
There are many JIT methods.
-
Demand-driven: This JIT is where you place regular orders for the parts/materials that are needed for your project. This will allow for you to track the material that you have left after using it. This will allow you to calculate how long it will take to make more.
-
Inventory-based : You can stock the materials you need in advance. This allows you to predict how much you can expect to sell.
-
Project-driven : This is a method where you make sure that enough money is set aside to pay the project's cost. When you know how much you need, you'll purchase the appropriate amount of materials.
-
Resource-based JIT is the most widespread form. This is where you assign resources based upon demand. For example, if there is a lot of work coming in, you will have more people assigned to them. You'll have fewer orders if you have fewer.
-
Cost-based: This is similar to resource-based, except that here you're not just concerned about how many people you have but how much each person costs.
-
Price-based: This is a variant of cost-based. However, instead of focusing on the individual workers' costs, this looks at the total price of the company.
-
Material-based is an alternative to cost-based. Instead of looking at the total cost in the company, this method focuses on the average amount of raw materials that you consume.
-
Time-based: Another variation of resource-based JIT. Instead of focusing only on how much each employee is costing, you should focus on how long it takes to complete your project.
-
Quality-based JIT: Another variation on resource-based JIT. Instead of thinking about the cost of each employee or the time it takes to produce something, you focus on how good your product quality.
-
Value-based JIT: This is the latest form of JIT. In this scenario, you're not concerned about how products perform or whether customers expect them to meet their expectations. Instead, your focus is on the value you bring to the market.
-
Stock-based. This method is inventory-based and focuses only on the actual production at any given point. It is used when production goals are met while inventory is kept to a minimum.
-
Just-intime planning (JIT), is a combination JIT/sales chain management. This refers to the scheduling of the delivery of components as soon after they are ordered. It is essential because it reduces lead-times and increases throughput.