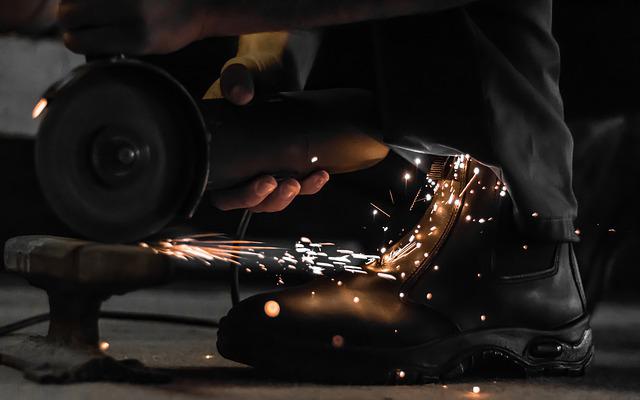
An industrial manager is an engineer who integrates different engineering processes to create an efficient management system. The industrial manager helps integrate all engineering processes into a single integrated management system. These are the basics of your job. Here are the requirements and benefits of becoming an industrial manager. This is the right career path for you if you have the necessary qualifications and are looking to take on a challenging, rewarding job. Continue reading for more information.
Job description
An industrial manager oversees the processes involved in the manufacturing and production of goods and services. The job can cover every aspect of the production process but will also be responsible for sourcing raw materials and implementing equipment. Industrial production managers should be computer-literate as computers are becoming increasingly important in the coordination of departments, suppliers, vendors, and clients. Industrial production managers should be knowledgeable about the latest management techniques and production technologies. Many managers participate in professional organizations, attend industry conferences and trade shows, and take courses to obtain certification in their field.
In addition to overseeing manufacturing processes, industrial managers coordinate the activities of various departments within a company. They make sure that production lines run smoothly and meet customer demands in terms of quality, time and delivery. They oversee staffing levels and alter production levels when necessary to reduce inventory. They may also oversee quality control programs and coordinate communication with suppliers and other departments. Most of this job involves managing people. This includes training, motivating, and identifying employees.
Education Required
It is not necessary to have a bachelor's in management, business, or engineering to become an industrial manager. Some employers prefer candidates with a background or education in these areas. Additionally, industrial managers need to be computer literate. Computers are an integral part of manufacturing. They coordinate production across departments, suppliers, customers, and even between clients. In order to succeed in this field, individuals interested should have the appropriate education and experience.
Many industrial production managers begin their careers as workers, and then move up to supervisory positions. Most professionals need to have a college degree or equivalent in business management to be able to move up to the position of industrial manager. However, some entry-level workers may be able to gain this education on the job, or they may choose to take classes sponsored by their companies. However, most managers are expected to have two to five years of relevant experience before becoming a manager.
Potential earnings
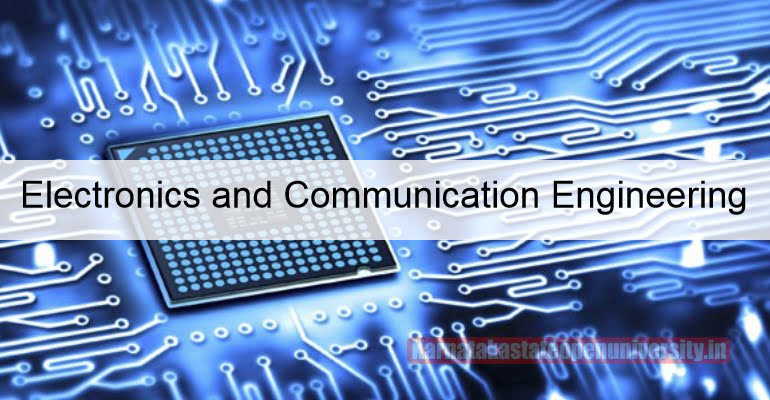
The industrial managers are responsible for overseeing the smooth running of manufacturing plants. They help to determine the best use of employees and equipment, establish production standards, and make strategic and tactical decisions. Their responsibilities include hiring, evaluating, and setting production times, and making sure safety procedures are adhered to. They oversee the day to day activities of a group of workers and analyze the production process continuously to ensure that it runs efficiently and at its peak efficiency.
The earnings potential of an industrial production manager depends on the employer and the experience of the employee. Although it is difficult to predict the future earnings, the average salary for industrial production managers was $103,380 in May 2016. The highest-paid industrial production managers earned $172,150 annually. High-skilled industrial production managers may earn more if they have been certified and received additional training. According to the U.S. Bureau of Labor Statistics, industrial production managers who have earned a bachelor's degree or higher may earn more.
Work environment
A manager of industrial production divides their time between the production floor or an office. Sometimes, they live in the same building. Industrial production managers must observe established health and safety practices and wear appropriate protective equipment when working in a production area. They often spend significant time in meetings and analysis of production data. Reports may be written by these managers. A manager of industrial production often works in a dynamic environment.
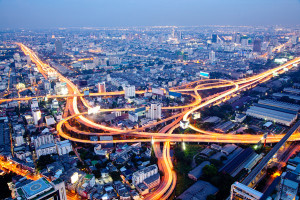
Industrial production managers play an important role in the management of a business. They coordinate the activities and improve productivity of different workers. A manager of industrial production is responsible for increasing productivity and safety. Due to corporate restructuring, many levels have been eliminated and support staff reduced. Production managers are now able to handle more of the work load. This is a serious challenge for any manager and can make the job of a production manager difficult.
FAQ
How can manufacturing excess production be decreased?
It is essential to find better ways to manage inventory to reduce overproduction. This would reduce time spent on activities such as purchasing, stocking, and maintaining excess stock. This would allow us to use our resources for more productive tasks.
Kanban systems are one way to achieve this. A Kanban Board is a visual display that tracks work progress. Work items are moved through various states to reach their destination in a Kanban system. Each state represents a different priority.
When work is completed, it can be transferred to the next stage. It is possible to keep a task in the beginning stages until it gets to the end.
This helps to keep work moving forward while ensuring that no work is left behind. Managers can monitor the work being done by Kanban boards to see what is happening at any given time. This data allows them adjust their workflow based upon real-time data.
Another way to control inventory levels is to implement lean manufacturing. Lean manufacturing emphasizes eliminating waste in all phases of production. Waste includes anything that does not add value to the product. These are some of the most common types.
-
Overproduction
-
Inventory
-
Packaging that is not necessary
-
Overstock materials
These ideas can help manufacturers improve efficiency and reduce costs.
What is the role of a logistics manager
A logistics manager ensures that all goods are delivered on time and without damage. This is accomplished by using the experience and knowledge gained from working with company products. He/she should ensure that sufficient stock is available in order to meet customer demand.
What is the role of a manager in manufacturing?
The manufacturing manager should ensure that every manufacturing process is efficient and effective. They must also be alert to any potential problems and take appropriate action.
They should also be able communicate with other departments, such as sales or marketing.
They should also be aware of the latest trends in their industry and be able to use this information to help improve productivity and efficiency.
Why should you automate your warehouse?
Modern warehousing has seen automation take center stage. E-commerce has brought increased demand for more efficient and quicker delivery times.
Warehouses have to be flexible to meet changing requirements. Technology is essential for warehouses to be able to adapt quickly to changing needs. Automating warehouses has many benefits. These are just a few reasons to invest in automation.
-
Increases throughput/productivity
-
Reduces errors
-
Increases accuracy
-
Safety Boosts
-
Eliminates bottlenecks
-
Allows companies scale more easily
-
Makes workers more efficient
-
The warehouse can be viewed from all angles.
-
Enhances customer experience
-
Improves employee satisfaction
-
Minimizes downtime and increases uptime
-
You can be sure that high-quality products will arrive on time
-
Removing human error
-
This helps to ensure compliance with regulations
How is a production manager different from a producer planner?
The primary difference between a producer planner and a manager of a project is that the manager usually plans and organizes the whole project, while a production planner is only involved in the planning stage.
Statistics
- It's estimated that 10.8% of the U.S. GDP in 2020 was contributed to manufacturing. (investopedia.com)
- According to a Statista study, U.S. businesses spent $1.63 trillion on logistics in 2019, moving goods from origin to end user through various supply chain network segments. (netsuite.com)
- Many factories witnessed a 30% increase in output due to the shift to electric motors. (en.wikipedia.org)
- [54][55] These are the top 50 countries by the total value of manufacturing output in US dollars for its noted year according to World Bank.[56] (en.wikipedia.org)
- You can multiply the result by 100 to get the total percent of monthly overhead. (investopedia.com)
External Links
How To
How to Use Lean Manufacturing for the Production of Goods
Lean manufacturing is a management style that aims to increase efficiency and reduce waste through continuous improvement. It was developed in Japan during the 1970s and 1980s by Taiichi Ohno, who received the Toyota Production System (TPS) award from TPS founder Kanji Toyoda. Michael L. Watkins published the "The Machine That Changed the World", the first book about lean manufacturing. It was published in 1990.
Lean manufacturing refers to a set of principles that improve the quality, speed and costs of products and services. It emphasizes the elimination of defects and waste throughout the value stream. Lean manufacturing is called just-in-time (JIT), zero defect, total productive maintenance (TPM), or 5S. Lean manufacturing emphasizes reducing non-value-added activities like inspection, rework and waiting.
Lean manufacturing can help companies improve their product quality and reduce costs. Additionally, it helps them achieve their goals more quickly and reduces employee turnover. Lean Manufacturing is one of the most efficient ways to manage the entire value chains, including suppliers and customers as well distributors and retailers. Many industries worldwide use lean manufacturing. For example, Toyota's philosophy underpins its success in automobiles, electronics, appliances, healthcare, chemical engineering, aerospace, paper, food, etc.
Lean manufacturing is based on five principles:
-
Define Value- Identify the added value your company brings to society. What makes you stand out from your competitors?
-
Reduce waste - Stop any activity that isn't adding value to the supply chains.
-
Create Flow. Ensure that your work is uninterrupted and flows seamlessly.
-
Standardize and Simplify – Make processes as consistent, repeatable, and as simple as possible.
-
Build Relationships - Establish personal relationships with both internal and external stakeholders.
Lean manufacturing, although not new, has seen renewed interest in the economic sector since 2008. To increase their competitiveness, many businesses have turned to lean manufacturing. Economists think that lean manufacturing is a crucial factor in economic recovery.
Lean manufacturing has many benefits in the automotive sector. These include improved customer satisfaction, reduced inventory levels, lower operating costs, increased productivity, and better overall safety.
Lean manufacturing can be applied to almost every aspect of an organization. Because it makes sure that all value chains are efficient and effectively managed, Lean Manufacturing is particularly helpful for organizations.
There are three main types of lean manufacturing:
-
Just-in-Time Manufacturing (JIT): This type of lean manufacturing is commonly referred to as "pull systems." JIT stands for a system where components are assembled on the spot rather than being made in advance. This approach aims to reduce lead times, increase the availability of parts, and reduce inventory.
-
Zero Defects Manufacturing (ZDM): ZDM focuses on ensuring that no defective units leave the manufacturing facility. You should repair any part that needs to be repaired during an assembly line. This also applies to finished products that need minor repairs before being shipped.
-
Continuous Improvement (CI): CI aims to improve the efficiency of operations by continuously identifying problems and making changes in order to eliminate or minimize waste. It involves continuous improvement of processes, people, and tools.