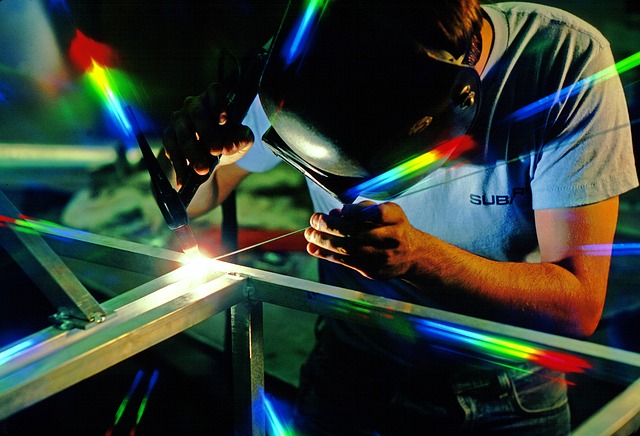
Supply chain risk management, regardless of how small or large your business is, is vital to maintaining a strong operation. There are many risks that can occur, from the seemingly mundane to the potentially disastrous. Your organization can be protected from losses with a well-planned plan and an effective implementation strategy.
Data sharing is an essential part of a supply chain continuity program. If you rely on one supplier, your organization is more vulnerable to supplier problems and vendor disputes. However, if your company is part of a multi-supplier consortium, you are more likely to avoid supply disruptions. You might also be able negotiate with an alternative supplier.
If your company has multiple contractors, there is a greater chance of vendor fraud, duplicate billing and improper related party billing. To help mitigate these risks, you can develop a risk assessment methodology, which can include a comprehensive assessment of your suppliers, partners, and other tier one components.
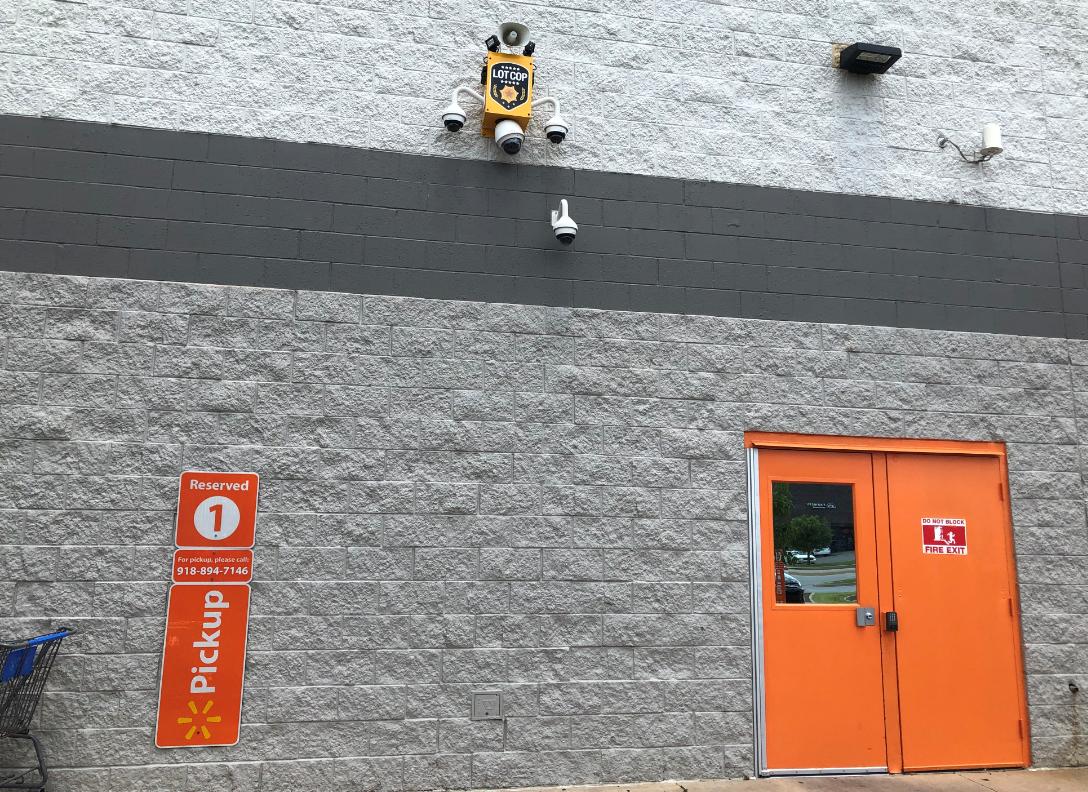
You must first identify the essential elements of a supply supply chain. After that, quantify them and create an action plan. These should include the above mentioned items as well as a few others. A proactive monitoring system is the most important component. A proactive monitoring system is one that gives executives accurate, real-time information about supply chain risks. If you can track supply risks in real-time, you will be better equipped to make informed decisions as well as to respond quickly.
As you begin assessing and quantifying your risks, it is essential to keep in mind that your supply chain's resilience is a function of governance. It is important to take into account the role of stakeholders. One example is the supplier bankruptcy in the pharmaceutical sector that could have been prevented if the company had properly managed its suppliers.
Having a well-conceived plan is the most basic step in the process of mitigating a supply chain crisis. But, it is not always simple to put in place the right contingency strategies. Many businesses fail to take the time to develop an appropriate number of contingency plans for each risk they are managing. These plans should be designed to have the highest possible impact.
The PPPR (preventive, preparedness and response) method is an internationally recognized standard in supply chain risk management. It is a solid approach that will improve your ability to react to supply-chain disruptions and can be used with other strategies to protect you organization from them. Using a PPPR can make the difference between surviving or thriving in today’s market.
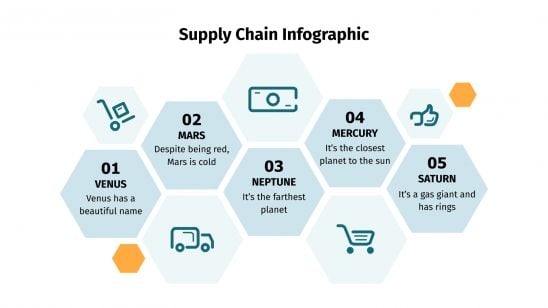
The right data can help you understand your suppliers' history and what they offer. This can assist you in making informed decisions whether you want to expand your sourcing efforts, or just improve your current processes. Having reliable data can help you provide your insurers with the right risk premiums.
FAQ
What kind of jobs are there in logistics?
Logistics can offer many different jobs. Some of them are:
-
Warehouse workers – They load, unload and transport pallets and trucks.
-
Transportation drivers - They drive trucks and trailers to deliver goods and carry out pick-ups.
-
Freight handlers are people who sort and pack freight into warehouses.
-
Inventory managers - These are responsible for overseeing the stock of goods in warehouses.
-
Sales representatives - They sell products to customers.
-
Logistics coordinators: They plan and manage logistics operations.
-
Purchasing agents - They buy goods and services that are necessary for company operations.
-
Customer service agents - They answer phone calls and respond to emails.
-
Ship clerks - They issue bills and process shipping orders.
-
Order fillers - They fill orders based on what is ordered and shipped.
-
Quality control inspectors are responsible for inspecting incoming and outgoing products looking for defects.
-
Other - Logistics has many other job opportunities, including transportation supervisors, logistics specialists, and cargo specialists.
What is the role of a logistics manager
Logistics managers make sure all goods are delivered on schedule and without damage. This is done using his/her knowledge of the company's products. He/she must also ensure sufficient stock to meet the demand.
What is it like to manage a logistics company?
It takes a lot of skills and knowledge to run a successful logistics business. Good communication skills are essential to effectively communicate with your suppliers and clients. You should be able analyse data and draw inferences. You must be able and able to handle stress situations and work under pressure. In order to innovate and create new ways to improve efficiency, creativity is essential. You need to have strong leadership qualities to motivate team members and direct them towards achieving organizational goals.
You must be organized to meet tight deadlines.
What are the responsibilities of a manufacturing manager
Manufacturing managers must ensure that manufacturing processes are efficient, effective, and cost-effective. They should also be aware of any problems within the company and act accordingly.
They should also be able and comfortable communicating with other departments like sales and marketing.
They must also keep up-to-date with the latest trends in their field and be able use this information to improve productivity and efficiency.
Statistics
- You can multiply the result by 100 to get the total percent of monthly overhead. (investopedia.com)
- Many factories witnessed a 30% increase in output due to the shift to electric motors. (en.wikipedia.org)
- [54][55] These are the top 50 countries by the total value of manufacturing output in US dollars for its noted year according to World Bank.[56] (en.wikipedia.org)
- It's estimated that 10.8% of the U.S. GDP in 2020 was contributed to manufacturing. (investopedia.com)
- According to a Statista study, U.S. businesses spent $1.63 trillion on logistics in 2019, moving goods from origin to end user through various supply chain network segments. (netsuite.com)
External Links
How To
How to Use Lean Manufacturing for the Production of Goods
Lean manufacturing (or lean manufacturing) is a style of management that aims to increase efficiency, reduce waste and improve performance through continuous improvement. It was created in Japan by Taiichi Ohno during the 1970s and 80s. He received the Toyota Production System award (TPS), from Kanji Toyoda, founder of TPS. Michael L. Watkins published the first book on lean manufacturing in 1990.
Lean manufacturing is often defined as a set of principles used to improve the quality, speed, and cost of products and services. It emphasizes reducing defects and eliminating waste throughout the value chain. Lean manufacturing can be described as just-in–time (JIT), total productive maintenance, zero defect (TPM), or even 5S. Lean manufacturing seeks to eliminate non-value added activities, such as inspection, work, waiting, and rework.
Lean manufacturing not only improves product quality but also reduces costs. Companies can also achieve their goals faster by reducing employee turnover. Lean manufacturing can be used to manage all aspects of the value chain. Customers, suppliers, distributors, retailers and employees are all included. Many industries worldwide use lean manufacturing. For example, Toyota's philosophy underpins its success in automobiles, electronics, appliances, healthcare, chemical engineering, aerospace, paper, food, etc.
Five fundamental principles underlie lean manufacturing.
-
Define value - Find out what your business contributes to society, and what makes it different from other competitors.
-
Reduce waste - Get rid of any activity that does not add value to the supply chain.
-
Create Flow – Ensure that work flows smoothly throughout the process.
-
Standardize and Simplify – Make processes as consistent, repeatable, and as simple as possible.
-
Building Relationships – Establish personal relationships with both external and internal stakeholders.
Lean manufacturing is not a new concept, but it has been gaining popularity over the last few years due to a renewed interest in the economy following the global financial crisis of 2008. Many businesses have adopted lean manufacturing techniques to help them become more competitive. Some economists even believe that lean manufacturing can be a key factor in economic recovery.
With many benefits, lean manufacturing is becoming more common in the automotive industry. These include better customer satisfaction and lower inventory levels. They also result in lower operating costs.
It can be applied to any aspect of an organisation. This is because it ensures efficiency and effectiveness in all stages of the value chain.
There are three main types of lean manufacturing:
-
Just-in Time Manufacturing (JIT), also known as "pull system": This form of lean manufacturing is often referred to simply as "pull". JIT refers to a system in which components are assembled at the point of use instead of being produced ahead of time. This strategy aims to decrease lead times, increase availability of parts and reduce inventory.
-
Zero Defects Manufacturing, (ZDM): ZDM is focused on ensuring that no defective products leave the manufacturing facility. You should repair any part that needs to be repaired during an assembly line. This applies to finished goods that may require minor repairs before shipment.
-
Continuous Improvement (CI), also known as Continuous Improvement, aims at improving the efficiency of operations through continuous identification and improvement to minimize or eliminate waste. Continuous Improvement involves continuous improvement of processes.