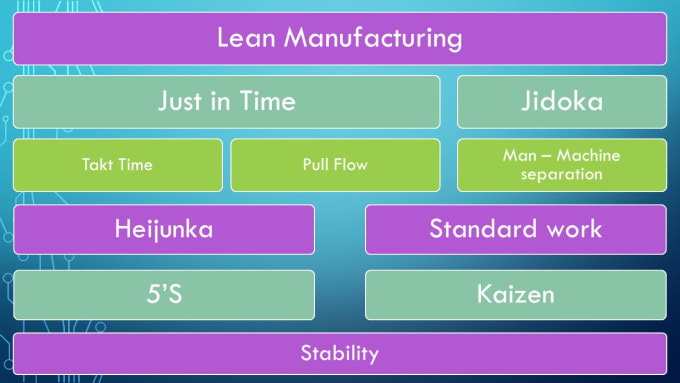
Industrial engineers work in the field of manufacturing technology, and are skilled professionals who help to improve production processes. They are responsible for the development and implementation of new methods, analysis of existing systems, and education workers about new policies. They are highly valued by engineering services, consulting firms, research and development companies, and engineering services because of their expertise.
Industrial engineers work in many different settings but their main focus is on reducing waste and improving production processes. They also reduce internal costs. These engineers are creative and use logic to design better processes. Some industrial engineers work with automated manufacturing processes.
The vast majority of industrial engineers have a solid background in mathematics, and other scientific principles. In addition, they must be skilled in problem-solving and critical thinking. They also need to have interpersonal skills and the ability to work well with others. Industrial engineers should be able to see the whole system and find weaknesses and strengths in alternative solutions.
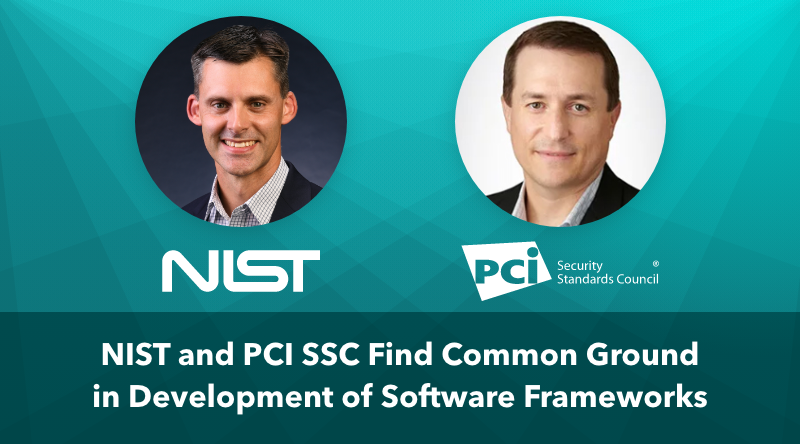
A bachelor's degree is required in order to pursue a career as an industrial engineer. You will also need at least four years experience. You can then apply for certification through the Society of Manufacturing Engineers. A master's degree allows you to specialize.
Industrial engineers are in high demand, and their job openings are expected to grow faster than the national average over the next ten years. This professional's employment is expected to rise by 10% during this period. While most of the work is full-time, hours can vary depending upon the project. The median salary for an industrial engineer in Nashville is $73,856. However, wage rates can differ from one employer to another depending on geographical location, employer, and individual qualifications.
You should highlight your professional and academic credentials when looking for a job as an industrial engineer in Nashville. You'll also need to make sure to take advantage of industry-specific certifications. A professional engineer license is required if you plan to work for a government agency.
Many companies hire interns to help them learn the ins and outs of industrial engineering. Interns learn about lean manufacturing, value stream mapping, and kaizen. Your skills and the company may allow you to progress your career to a managerial position.
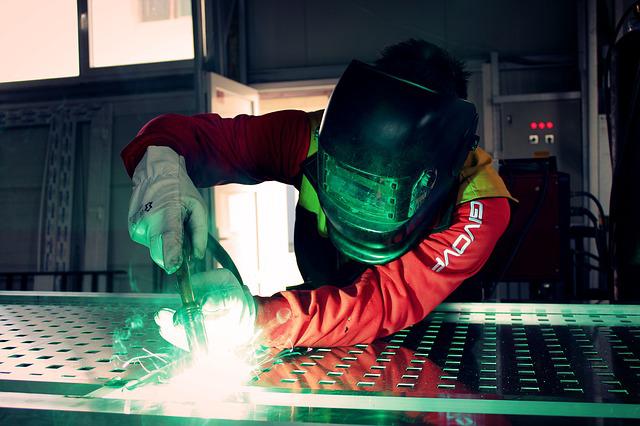
No matter whether you're in an office or lab, you need to learn interpersonal communication skills so you can communicate effectively with coworkers and managers. Other than communicating with colleagues, you must also be able communicate with customers and suppliers.
A variety of industries are looking for skilled industrial engineers. These include transport equipment manufacturers, electronic and computer manufacturers, and engineering services firms. Several colleges offer 5-year degree programs in industrial engineering. While many graduates are able to find entry-level positions in multiple industries, a few are more focused on certain specialty areas, such as automated manufacturing processes.
FAQ
What are the four types in manufacturing?
Manufacturing is the process by which raw materials are transformed into useful products through machines and processes. It involves many different activities such as designing, building, testing, packaging, shipping, selling, servicing, etc.
What is the job of a logistics manger?
A logistics manager ensures that all goods are delivered on time and without damage. This is achieved by using their knowledge and experience with the products of the company. He/she also needs to ensure adequate stock to meet demand.
What are the goods of logistics?
Logistics is the process of moving goods from one point to another.
They cover all aspects of transportation, such as packing, loading, transporting and unloading.
Logisticians ensure the product reaches its destination in the most efficient manner. They help companies manage their supply chain efficiency by providing information on demand forecasts, stock levels, production schedules, and availability of raw materials.
They can also track shipments in transit and monitor quality standards.
What are the jobs in logistics?
There are many types of jobs in logistics. Some examples are:
-
Warehouse workers – They load and unload pallets and trucks.
-
Transportation drivers – They drive trucks or trailers to transport goods and perform pick-ups.
-
Freight handlers – They sort and package freight at warehouses.
-
Inventory managers - They oversee the inventory of goods in warehouses.
-
Sales reps are people who sell products to customers.
-
Logistics coordinators are responsible for organizing and planning logistics operations.
-
Purchasing agents: They are responsible for purchasing goods and services to support company operations.
-
Customer service representatives - Answer calls and email from customers.
-
Shippers clerks - They process shipping order and issue bills.
-
Order fillers – They fill orders based upon what was ordered and shipped.
-
Quality control inspectors - They check incoming and outgoing products for defects.
-
Others – There are many other types available in logistics. They include transport supervisors, cargo specialists and others.
What is manufacturing and logistics?
Manufacturing is the production of goods using raw materials. Logistics includes all aspects related to supply chain management, such as procurement, distribution planning, inventory control and transportation. As a broad term, manufacturing and logistics often refer to both the creation and delivery of products.
What is the importance of logistics in manufacturing?
Logistics are an integral part any business. Logistics can help you achieve amazing results by helping to manage product flow from raw materials to finished products.
Logistics plays a significant role in reducing cost and increasing efficiency.
Statistics
- In 2021, an estimated 12.1 million Americans work in the manufacturing sector.6 (investopedia.com)
- (2:04) MTO is a production technique wherein products are customized according to customer specifications, and production only starts after an order is received. (oracle.com)
- According to the United Nations Industrial Development Organization (UNIDO), China is the top manufacturer worldwide by 2019 output, producing 28.7% of the total global manufacturing output, followed by the United States, Japan, Germany, and India.[52][53] (en.wikipedia.org)
- In the United States, for example, manufacturing makes up 15% of the economic output. (twi-global.com)
- Many factories witnessed a 30% increase in output due to the shift to electric motors. (en.wikipedia.org)
External Links
How To
How to Use Six Sigma in Manufacturing
Six Sigma is "the application statistical process control (SPC), techniques for continuous improvement." It was developed by Motorola's Quality Improvement Department at their plant in Tokyo, Japan, in 1986. The basic idea behind Six Sigma is to improve quality by improving processes through standardization and eliminating defects. Many companies have adopted this method in recent years. They believe there is no such thing a perfect product or service. Six Sigma aims to reduce variation in the production's mean value. This means that you can take a sample from your product and then compare its performance to the average to find out how often the process differs from the norm. If the deviation is excessive, it's likely that something needs to be fixed.
Understanding the nature of variability in your business is the first step to Six Sigma. Once you've understood that, you'll want to identify sources of variation. It is important to identify whether the variations are random or systemic. Random variations happen when people make errors; systematic variations are caused externally. You could consider random variations if some widgets fall off the assembly lines. If however, you notice that each time you assemble a widget it falls apart in exactly the same spot, that is a problem.
After identifying the problem areas, you will need to devise solutions. The solution could involve changing how you do things, or redesigning your entire process. You should then test the changes again after they have been implemented. If they didn't work, then you'll need to go back to the drawing board and come up with another plan.